Flash and JavaScript are required for this feature.
Download the video from iTunes U or the Internet Archive.
Description: This session begins with a viewing of video on Hooke's Micrographia, then covers compressive strength and fracture toughness of foams.
Instructor: Lorna Gibson
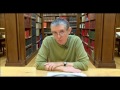
Lecture 8: Foams: Non-linea...
The following content is provided under a Creative Commons license. Your support will help MIT OpenCourseWare continue to offer high-quality educational resources for free. To make a donation or view additional materials from hundreds of MIT courses, visit MIT OpenCourseWare at ocw.mit.edu.
LORNA GIBSON: All right. And I really wanted to show you my little hook video and I downloaded it so I thought we'd start just by watching that and then I'll pick up about modeling phones. So this takes like nine or 10 minutes, but I just thought it was cute. And I made it and I want you to see it. So let's do that to start.
[VIDEO PLAYBACK]
We're here at the Harvard University Botany Library, looking at a first edition of Robert Hooke's Micrographia, published--
How do I get rid of the bar, Greg? Oh, there it is.
show the microscopic structure of materials. And it has a number of remarkable drawings in it. Here we see drawings of silk. These are two different silks. On the top here, we have a fine-waled silk. And in this more details drawing down here, you can see the patterned weaving of the silk. The bottom image here is a drawing of watered silk. And over here, there's another higher magnification image. And you can see the pattern here is more sharply angled. And it appears that this sharper angle here gives the different texture to the surface finish of the silk.
So here we see a drawing of charred wood. And one of the things I find interesting about this drawing is how similar it is to modern electron micrographs which we've seen before. And in this drawing, we can see two of the main features. We see these small cells, which are fibers that provide structural support to the tree. And we see these larger cells here, which are vessels which allow fluids to go up and down the tree.
And here we see a drawing of the surface of a rosemary leaf, with the unexpected, tiny, little bars. And this is something that you can only see with the microscope. You wouldn't expect to see those when you just feel the surface of the rosemary leaf. So it's kind of interesting that with the microscope, you can see these features that are invisible to the naked eye.
One of the main themes of material science is that the property of materials are related to their structure. And so being able to see the structure at a microscopic scale is very helpful. And today, we can even see the structure at the atomic scale.
Robert Hooke understood this idea. And in the description of the cork, Hooke states, "I no sooner discerned these-- which were the first microscopical pores I ever saw-- but methought that I had with the discovery of them, perfectly hinted to me the true and intelligible reason for all of the phenomena of cork." So what he's saying here is that by looking at the structure and looking at the cells here in the drawing, he thinks he can understand the properties of cork or the phenomena of cork.
What was it about Robert Hooke that allowed him to make this book? Why was it him and not somebody else? Well, Robert Hooke had kind of an interesting history.
He grew up on the Isle of Wight. And as a boy, he loved making drawings. And he got quite skilled at making drawings.
The other thing was, he loved making models of things. He made models of ships. He made a wooden clock that was a working clock when he was a kid.
And as a teenager, he moved to London. And he became an apprentice to Sir Peter Lilley, who was a famous painter of the time. So his drawing was good enough that he would be working with a very well-known painter.
After he did that, he went to the Westminister School. And he studied classics. He studied mathematics. But he also learned to use a lathe. And this was also very helpful in him making various sorts of apparatus.
And as a student at Oxford, he worked in the lab of Robert Boyle. And his job in that lab was to develop scientific apparatus. And he did things like he built pumps that allowed Robert Boyle to do the experiments that led to Boyle's Law.
When he returned to London after Oxford, he became the Curator of Experiments at the Royal Society. And one of the things he did was he got a microscope. He improved that microscope, increasing their magnification, which was what allowed him to make the beautiful drawings that we see today. And here in the preface of the book, we see that he even made a drawing of his microscope. So this thing down here-- this is Robert Hooke's microscope.
The development of new microscopes with higher and higher magnifications continues to this day. Scanning electron microscopes were invented in the 1960s. And today, we have transmission electron microscopes and atomic force microscopes with even higher magnifications.
At these higher magnifications, we can see details that Hooke was unable to see because of the limitations of the microscope that he had-- the optical microscope. But it's interesting to see today the images we see in a scanning electron microscope at a similar magnification to those that Hooke saw in his optical microscope. And it's remarkable to see how many of the features that we see in these much more fancy microscopes that he was able to capture in his drawings with his simple optical microscope.
So here we have a picture of cork. We have Hooke's drawings showing two perpendicular planes. We also have this nice, little drawing of a cork branch here. Cork is the bark from the cork oak tree.
And in Hooke's drawings of the microstructure, we can see these cells here are roughly box-like. They're more or less rectangular. And these cells here look more or less circular. So there's these two different perpendicular planes in the cork.
And when we look at these scanning electron micrographs, we can see very similar structure. There are some cells that are roughly boxlike, and others that are more or less hexagonal or roughly rounded. One feature that Hooke was not able to see, though, that you do see on the scanning electron micrographs, is the waviness in the cell walls.
And that was because the resolution of his microscope was insufficient to see that level of detail. And here in this illustration on the bottom here is a drawing of sponge. And when we look at the scanning electron micrograph, we see that the structure is remarkably similar to what Hooke has drawn.
So here we have Hooke's drawing of feathers. And we can see he's made several drawings at different length scales. And if we look at this one here, we see the barbule.
And you can see these little hooked regions there. And those hooks lock into the little feathers over on this side over here of the adjacent barbule. And in the higher magnification picture, you can see on one barbule, there's hooks on one side but not on the other.
And it's this hooking of the two sections together that allows the feathers to maintain a smooth surface for the wing when the bird is flying. And you can see the same sort of thing when you look at the electron micrograph. So you can see the little hooks on one side of the barbules. And you can see how they interconnect together with the next barb.
One of the most reproduced images from Hooke's book is that of the flea-- this image we see here. And you can see why. It's a gorgeous image.
And it shows details that people had never seen before. People were amazed to see that the little flea that they might have found on their dog or something was actually made up of this compound body, with all these little plates and little hairs here. And you can see these little tiny claws on the legs, and the legs have all these hairs.
Nobody had any idea that this is what a flea actually looked like. And so it was an amazing drawing. And it was something that people were just stunned by when Hooke's book came out.
And if we look at a modern electron micrograph, we can see it's remarkably similar if we look at the same magnification. So Hooke showed many of the same details, showed some of the same hairs on the legs, showed the same sorts of plates, showed the claws at the ends of the legs. And our modern image is probably from a different species of flea.
We don't know what species of flea that Hooke actually looked at. But you can see there's a tremendous similarity between the two images. And it's remarkable how many of the features that Hooke was able to capture in his drawing.
And here we have the compound eye of the fly. And this, again, was astonishing to people in Hooke's day. And even today, people look at this image, and they're pretty amazed at the detail in this drawing. And again, we can compare this with a modern electron micrograph. And again, you can see the similarities between what Hooke saw and what we see in a modern scanning electron microscope at a similar magnification.
In the 1980s, atomic force microscopes were invented, which have a resolution down to tens of nanometers. And today, there's transmission electron microscopes, which allow you to see the atomic structure. So for instance in a crystal lattice, you can see the individual atoms and the regular crystal structure.
Today, most experimental studies of materials include photographs of the microscopic structure of the material taken through some sort of microscope. And the remarkable thing is that all of these studies really trace back to this book here that we're looking at today-- to Robert Hooke's Micrographia.
[END PLAYBACK]
There you have it. So I just thought that was kind of cute. You might enjoy that. So that was that.
All right, let's get out of there. Stop. So let's go back to the foams. So I think last time, we got as far as talking about the linear elastic behavior of foams and modeling that.
But we didn't quite get to looking at the compressive strength of the foam. So I think we got as far as comparing the models with these equations here, and these plots of the data. And what I wanted to pick up with today was looking at the compressive strength. And we'll look at the fracture toughness as well in tension. So we're going to start with nonlinear elasticity and the elastic collapse stress.
So if we have an open-cell foam, the derivation for the elastic collapse stress is really pretty straightforward. We say the elastic collapse occurs when the cell walls buckles. So in this schematic here, you can see the vertical cell walls have buckled.
And so there's going to be some Euler load that's related to that buckling. And that's just the usual Euler load-- n squared, the n constraint factor, pi squared E. This is going to be E of the solid, I over l squared-- the length of the member.
And then the stress that corresponds to that is just going to be proportional to that buckling load over the area of the cell, which is just l squared, so just P critical over l squared. So that just goes as Es. I is going to go as t to the fourth, because we have that square sectioned member.
And now this is going to be l squared. And that's an l squared. So that's l to the fourth.
And so if I combine all of that together, I can say that the elastic buckling stress is going to be some constant-- and I think we're up to C4 now-- times the Young's modulus of the solid times the relative density of the foam squared. So that's our equation for the elastic buckling stress. And if you compare this with data, you can make an estimate of what C4 is. And we find that C4 is about 0.05.
And you can also say that 0.05 really corresponds to the strain at which the buckling occurs. Because the Young's modulus goes as the constants 1 times Es times the relative density squared. So the strain's just going to be the stress over the modulus. So that does correspond to the strain.
So that's saying that buckling compressive stress occurs at a strain of about 5%. So that's open cells. And then if we look at closed cells, if you recall when we looked at the moduli we looked at a couple of extra terms.
One was associated with face stretching for the modulus. And the other was associated with the compression of the gas. For the buckling, the faces don't really contribute that much, because typically the faces are very thin relative to the struts.
And because they're so thin, they buckle at a much lower load, and they don't contribute too much. So we're not going to worry about that contribution. So I'm just going to say that the thickness of the face is often small compared to the edges.
And that really is from the surface tension in processing that draws material away from the face and into the edges.
There can be some contribution from the internal pressure. So if the internal pressure is greater than atmospheric pressure, then the cell walls are pre-tensioned, and you'd have to account for that. So the buckling would have to overcome that pressure as well.
So then you would have the buckling stress would just be what we have up there-- C4 times Es times the relative density squared. And then we just add on that factor P0 minus P atmospheric. The thing with the gas which tends to affect more than the buckling stress, though, is the post-collapse behavior.
So let me just show you a couple of things here. So here's some data for the elastic collapse stress. And you can see on the y-axis, we've got the stress normalized by the Young's modulus of the solid. And on the x-axis, we've got the relative density.
And that solid line there-- sort of solid, dark line-- is that equation there, which is the same as this one up here. And you can see the data lie fairly close to that. But what's interesting is if you look at the-- why is this not working? Maybe my batteries finally died.
If we look at the post-collapse behavior, you can see if these are the stress-strain curves, they're not flat here. They have some rise to them. And this is a closed-cell foam.
And you can imagine as you're compressing the closed-cell foam, you're reducing the volume of the cell. And as you doing that, you're increasing the pressure inside the cell from the gas. And you can calculate what that is. And I'll do that in a second.
And if you subtract off that gas pressure contribution, that works out to this line here. Then these lines will be more flat, like this. And we already really pretty much worked out that gas contribution.
So I'll just say for the post-collapse behavior, the stress rises due to the gas compression. And that's as long as the faces don't rupture. So if you have an elastomeric foam, typically they don't rupture.
And what we had worked out before was that that pressure-- we called it P prime-- it was P0 minus P atmospheric-- that was equal to P0 times the amount of strain, epsilon, times 1 minus 2 times the Poisson's ratio divided by 1 minus epsilon times 1 minus 2 nu minus the relative density. And once you get to the buckling stress, then the Poisson's ratio becomes 0.
So if you take a foam-- so I brought a little foam in so you can play around with this one-- so if you take a foam like this and you compress it, once you've buckled it like this, it's not getting any wider this way. And part of the reason for that is you've got all these pores in here. And the cells just collapse into the pores. They don't really need to move out sideways. So you can smush that yourself, and try to convince yourself that the Poisson's ratio is just 0. Yes, Matt.
AUDIENCE: [INAUDIBLE] I guess I want to measure [INAUDIBLE] the gas contribution?
LORNA GIBSON: Yes, so there is a strain rate effect with these things. But I wasn't going to get into that here. If you look in the book, it's described in the book.
So I think there's two things. One is that the solid itself can have a rate dependency. And then there could be something connected.
AUDIENCE: [INAUDIBLE].
LORNA GIBSON: Yeah, I mean, I'm not going to go into that here. But one could look at that. So let me just write down one more thing here, because if we let nu be 0, then this thing here becomes simpler.
So we could say the stress post collapse as a function of strain would be our buckling stress and then plus this factor here.
So that curve on the bottom over here-- if this is the stress-strain curve-- this little dashed line here-- that's the gas contribution. And that is this term here. So you can kind of see how the shape of the curves reflects that gas contribution. And when you subtract it out, you get pretty much a horizontal plateau over here. Are we happy? Yeah?
AUDIENCE: [INAUDIBLE]?
LORNA GIBSON: This is for the closed cell. Because the closed cell are the ones that are going to have the gas pressure. If it's open cells, the gas can just move out of the cells.
AUDIENCE: [INAUDIBLE]?
LORNA GIBSON: Oh, sorry, that was to show you that the Poisson's ratio was 0. And that's true for both of them.
So then we can look at the plastic collapse stress. Say we had a metal foam. And we do a calculation a little bit like the one we did for the honeycombs, too.
So we say the failure occurs when the applied moment equals the plastic moment. And the applied moment is proportional to the applied stress times the length cubed. So I'm going to call that applied stress-- our strength sigma star plastic times the length cubed.
So if you think of, say, the little schematic up here, the force is going to go with stress times the length squared. And the moment's going to force times the length. So it's the stress times the length cubed.
And then the plastic moment goes as the yield strength times the thickness cubed. And then if I just combine those, I get that the plastic collapse stress in compression is another constant-- I'm going to call it C5-- times the yield strength times the relative density to the 3/2 power. And if we look at data, we find that the constant is about equal to 0.3.
And if I go to the next slide, here's a plot of the yield strength or the plastic collapse strength of the foam divided by the yield strength of the solid, plotted against the relative density. And that dark, bold line is this equation here. And you can see the data lie pretty well on that line. There's one data set that's a little bit above the line. But you can see the slope of that data set is still about 3/2.
OK, and the same as in the honeycombs, we could say that we can get elastic collapse before the plastic collapse if we were at a low density. You can get the same thing in the foams. And you calculate out what the critical relative density is for that the same kind of way.
So we can say we can get elastic collapse precedes the plastic collapse if the elastic buckling stress is less than the plastic collapse stress. So all we do is make those two things equal to figure out the critical relative density where you get the transition from one to the other. So the relative density has to be less than 36 times the yield strength of the solid over the Young's modulus of the solid squared in order to get buckling before yielding.
And let's see, where can I put that? So for rigid polymers, that ratio of the strength of the solid over the modulus of the solid is about one over 30. And so the critical relative density for the transition is about 0.04. So you'd have to have a pretty low-density foam, but it's possible.
And for metals, that ratio is about 1/1,000. And then the critical transition density is less than 10 to the minus 5. So essentially, it never happens for the metal foams.
And then for the closed-cell foams, we could include the terms for face stretching and for the gas. But in practice, the faces don't really contribute very much. And typically for foams like say metal foams or a rigid polymer that had a yield point, the faces rupture.
And then if the faces rupture, then you don't get the gas compression term, either. So I'll just write the full thing down. But typically, you don't need to use it.
So the first term would be from the edges bending. And the second term would be from the faces stretching. And this would be from the gas. But in practice, the first term is really the only one that is significant.
So for closed-cell foam, this equation works pretty well, too-- the same one as for the open-cell foams.
OK, so if we had, say, a ceramic foam that was brittle, there'd be a brittle crushing strength. And then we get failure when the applied moment M is equal to the fracture moment Mf. And this works very similar to the plastic yield strength.
So we find the applied moment goes as the global stress times the length cubed. And the fracture moment goes into the cell wall strength times the cell wall thickness cubed. So the brittle crushing strength goes as another constant-- let's call it C6-- times the wall strength times the relative density to the 3/2 again.
And C6 is about equal to 0.2. And typically, ceramic foams have open cells. So I'm just going to leave it at the open-celled formula there.
So there's one last thing for the compressive behavior, and that's the densification strain. And we just have an empirical relationship for the densification strain.
So if you compress the foam and you get to very large strains, then the cell walls start to touch, and the stress starts to rise steeply. And there's some strain at which that occurs. And we call that the densification strain.
And in the limit, the modulus at that point would go to the modulus of the solid. If you could completely squeeze all the pores out, the stiffness of that would go to the modulus of the solid. And you might expect that that densification strain is just 1 minus the relative density, but it actually occurs at a slightly smaller strain. So in a large compressive stress, or strain, I guess we could say, cell walls touch, and we start to get this densification.
So the modulus in the limit would go to the modulus of the solid. And you might expect that the densification strain was just equal to 1 minus the relative density. But it occurs at a little bit less than that. So empirically, we find that it's just 1 minus 1.4 times the relative density.
And then I have this plot here, which is really just fitting a line to that data for densification strain. So those equations describe the compressive stress or the compressive behavior of the foam. So we've got the moduli, we've got the three compressive strengths, and we've got the densification strain.
So what we're going to do later on in the course is we'll use those models to look at how we can use foams and things like sandwich panels and looking at energy absorption. And we'll also look at these equations in terms of some biomedical materials-- looking at trabecular bone, and looking at tissue engineering scaffolds.
So there's one last property I wanted to go over, and that's the fracture toughness. So if we were pulling the foam in tension, and we had a crack in the foam, we'd want to know what the fracture toughness would be for a brittle foam. And this follows the same sort of argument as we had for the honeycomb.
So all of these equations really are just following the same kinds of arguments. But you can kind of see how having the honeycomb calculations makes it easier to do the foam ones. So we'll do the fracture toughness calculation, and then I want to talk a little bit about material selection and selection charts for foams. So that's less equation-y.
OK, and we're just going to look at open cells here. So imagine we have a crack of length 2a. And we have some remote stress applied, so remote tensile stress, so I'm going to call that sigma infinity-- the far-away stress.
And then we have a local stress on the cell walls. I'm going to call that signal local. So I have a little schematic that kind of shows what we're doing.
So we're pulling on it. There's some crack. The crack length is large compared to the cell size. And we want to know what the fracture toughness is.
So we can say from fracture mechanics the local stress is going to be equal to some constant times the faraway stress times the square root of pi a over the square root of 2 pi r. And that's at a distance r from the head of the crack tip.
And if we look at our little schematic here, we could say it's hard to say exactly where the crack tip is, but it would be somewhere in here. And we'd say this next unbroken cell wall is a distance r ahead of the crack tip. And that r is going to be related to l. It's going to be some function of l.
So I can say the next unbroken wall ahead of the crack tip at some distance r is going to be related to l. And that's subject to a force, which is going to be the local stress times l squared. So that force is going to go as local stress times l squared. And the local stress-- I can substitute this thing here in-- that's going to be proportional to the faraway stress.
And I'm going to get rid of the pi's. And I'm going to substitute for r. I'm going to put in l.
So it's going to be proportional to the faraway stress times the root of a over l and times l squared there. And then we're going to say, again, the edges are going to fail when the applied moment equals the fracture moment.
And the fracture moment is going to go as the modulus of rupture of the cell walls times t cubed. And the applied moment is going to go as f times l. And I've got f from up there, so that goes as the faraway stress, sigma infinite, times the root of a over l. And now I've got l cubed, because there's an l squared there and there's an l down here. And then if I just equate those, then this is going to go as sigma fs times t cubed, like that.
So then I can say the fracture strength is equal to my faraway stress. That's going to go as my modulus of rupture times the root of l for a times t over l cubed. And then my fracture toughness is going to be this tensile stress times the root of pi a.
So there's going to be some other constant here, which I'm going to call that C8. We've got the modulus of rupture of the solid. I've got the square root of l, and I'm going to multiply it by pi so it's like other fraction mechanics kinds of equations.
And then we multiply that times the relative density to the 3/2 power. And here, if we look at data, we find that that constant is about equal to 0.65.
And here's another one of these plots. So here I've normalized the fracture toughness of the foams by the modulus of rupture of the cell walls times the root of pi l. So I've taken the cell size into account here, and I've plotted against the relative density.
And that equation there is the same as this equation I've got down on the board. And this is the only one of the properties that we've looked at that depends on the cell size. There's a cell size dependence here.
All right, so I think that's all the modeling of the foams. Are we good? I gave you a lot of equations. We're good? All right.
So I want to talk about how we might design foams to improve their properties. And then I want to talk about how we might select foams for certain applications and look at selection charts. So when we've been talking about the foams, especially the open-cell foams, we've been saying their deformation is largely by bending of the cell edges. And if we could do something to increase the stiffness of the edges or the strength of the edges, then that would increase the overall properties of the foam.
And there's a couple of ways to think about doing that. So the foam properties-- if the foam is controlled by bending of the edges, and the edges have some flexural rigidity, EI, if we could increase that EI of the edges, we would increase the properties of the foam.
And one way to do that is by making the edges hollow. So if we had hollow edges, and you had a tube, then that would increase the EI. And we can work out how much it's going to increase them.
And I have a little example here of-- a natural example of hollow foam struts. So this is a grass. I don't know what kind of grass it is. I just saw this grass.
And we picked some different grasses, and we took some SEM pictures. And it has a really kind of common structure for grasses. It's very common for grass stems to have sort of a solid outer part and then a foam-like inner part. It's so common that botanists have a name for it. They call it the core-rind structure.
And if you take one of these grass stems, and you look at the sort of foamy bit in the middle, and you do a SEM picture of that, you can see that the little cell walls are actually little hollow tubes. So one of these things-- it's a little hollow tube. So what I wanted to do is work out how much the modulus of the foam would increase if you could make all the edges into little hollow tubes.
So we're going to start by saying the foam behavior is dominated by cell bending, so edge bending. And the foam properties can be increased by increasing the EI of the cell wall. So there's a couple of ways we could do that.
So the first one is looking at hollow walls. So imagine I have a thin-walled tube-- just a circular, thin-walled tube. There's my little wall there. It has some radius little r, and a wall thickness t.
And then imagine I have the same amount of mass, but now I have a solid circular section. And I'm going to say the radius of that is big R. So for our thin-walled tube, the moment of inertia is pi r cubed times the thickness, t, if it's thin.
And for our solid circular section, I is going to be pi big R to the 4th over 4. And if I say I want to set this up so that the masses are equal, then the areas of the cross-sections have to be equal-- say it's from the same material. So the masses are going to be equal if pi R squared is equal to 2 pi r t.
So I'm going to solve here for R. So the pi's are going to cancel out. So the masses are equal if R is equal to the square root of 2 times r times t.
And then what we're going to do is see how the big is the moment of inertia of the tube relative to the solid. And the tube is pi little r cubed t. And the solid was pi R to the 4th, divided by 4. And I'm going to get rid of the R here, and get rid of the pi's there.
So R to the 4th is going to be 4r squared t squared. So the 4s are going to go. And this boils down to r over t.
So if I had a thin-walled tube, the moment of inertia is going to be r over t bigger than if I had the same mass in a solid circular section. So you can see for the little plant here, by making a thin-walled tube, you're increasing the stiffness of the foam with the same amount of material. That's the idea. And you can do a similar kind of analysis for other properties.
So that's if we have hollow tubes. So another option is we could have cell walls that are sandwich structures. So imagine if the cell walls themselves were little, tiny sandwich structures.
So when you have a sandwich beam, what you have is too stiff, strong faces that are separated by some sort of porous core, like a honeycomb or a foam or balsa wood. And the idea with the sandwich structure-- if I draw a little sketch of the sandwich, here's my faces. So imagine those are solid.
So they might be aluminum sheets, or they might be fiber reinforced composites. And then we have some sort of cellular thing here as the core. And the idea is, that's analogous to an I-beam.
So in the sandwich beam, we have two, stiff, strong faces separated by a lightweight core. So the core is typically a honeycomb, or a foam, or balsa wood. And the idea is, you increase the moment of inertia of the cross-section with little increase in weight.
And if you think of an I-beam, an I-beam has a large moment of inertia, because you're separating the flanges by the web. And the sandwich beam works in the same way. You're separating the faces by the core. But the core doesn't weigh very much, because it's a cellular thing.
So the faces of the sandwich are like the flanges in the I-beam. And then the core is like the web. So the idea is to make something called a micro-sandwich foam. So what you want to do is make the cell walls into sandwiches. And one way to do that is to disperse a large volume fraction of thin-walled spheres into the foam.
And you have to get the geometry right to make it work. So let me draw a little kind of sketch here of how it works. So here's our thin-walled spheres.
And then you're going to distribute those in a foam. Here's another sphere over here. The spheres are not perfect. Let's say there's another one in here. And then the idea is this stuff in here would be the foam.
So these guys are hollow spheres. And say the spheres have a diameter D. And say they have a wall thickness here of t.
And say that the separation of the spheres I'm going to call c. You can see that there. And then the cell size of the foam I'm going to call e. So there's a bunch of parameters you have to kind of play with to get this to work.
So you have to have thin-walled spheres so the faces are thin. The sandwich panels work best when the faces are thin. So you need the thickness of the sphere to be much less than D.
You need the faces to be stiff relative to the foam. So you need the modulus of the sphere material to be greater than the modulus of the foam. And you need the volume fraction of the spheres to be relatively high to get the spheres close enough together for this to work. So you want that volume fraction to be something like 50% to 60%.
And for the foam, you need to have the foam cell size less than the separation between the spheres. You need to have a number of-- you can't just have one pore in here. That's not really like a foam. It won't behave like a foam as a continuum.
So you need to have a number of different cell sizes in between each sphere. And so you need the cell size of the foam to be a lot less than the separation of the spheres there, c. But if you can control this geometry, you can get the sandwich effect.
And you can get improved properties by doing that. So there's ways you can play around with the structure of the foams to improve their properties. So that was one thing I wanted to say.
Another way to improve the properties of a foam-like material is to use one of those lattice materials. So we've been talking about ways to improve the bending stiffness. But if you could get rid of the bending altogether and have axial deformation in the cell walls, that would be much stiffer.
And you can get axial deformation by having those 3D truss kind of materials. So I have a picture of this. There we go, so there's one of those 3D truss materials. So another alternative is to sort of get rid of the bending altogether, and to try to make a truss-type material.
So there's various ways to make these. I think that we talked about a few of them earlier on. And you can analyze them as truss-type structures.
And I can just run through a sort of little dimensional argument to get the modulus. So the modulus is going to go as the stress over the strain. The stress is going to go as a force over a length squared. The strain's going to go as a deformation over l.
So this is just like what we had before for the foams. But in this case, the deformation is going to go with the force times the length over the area of the cross-section divided by Es, because we're pulling it or pushing it axially. So that goes as Fl over t squared Es.
And if I just put that back in the equation here for the modulus, I get that we've got F over l. And I've got delta here, so that's F l t squared Es. And you just get the modulus goes as the modulus of the solid times t over l squared. And that goes as the modulus of the solid times the relative density.
So for the open-celled foams, the modulus went as the relative density squared. So if it was 10% solid, the modulus would be 0.01. And this is saying if it's 10% solid, the modulus is 0.1. So it's much bigger.
So this is all sort of well and good. The only difficulty is that when you look at the modulus, you can do reasonably well. But when you look at the strength, some of the members are going to be inevitably in compression. When you have these truss materials, some members are going to be in tension. Some members are going to be in compression.
And the compression members tend to buckle. And once the compression members buckle, then you're back to the same kind of strength relationship that you have for the foam. So that's one of the difficulties of this.
So let me say that the strength-- so if the strength was controlled by uni-axial yield, it would go linearly with relative density. But if it goes with buckling, it goes as the square.
So I'll just say the compression members can buckle.
And say you had a metal lattice. Then there's some interaction between the plastic behavior and the buckling. And you use what's called the tangent modulus instead of just the Young's modulus.
And the tangent modulus is lower. And there's also what's called knock-down factors that can be large, too. So the knock-down factor can be like 50%.
So the measured strength can be half of what you thought it was going to be. This should be a squared over here. Sorry.
So even though the stiffness of these 3D trusses can be quite good, the strength often isn't quite as good as one might hope. So that's one of the issues with them. All right.
So do you see the idea, though, with all these different micro structures, is that you can control the structure in a way to try to increase the bending stiffness or get rid of the bending stiffness and increase the axial stiffness? So there's things you can do to play around with that.
And I wanted to talk a bit today about material selection charts for foams. So when we talked about woods, we started talking about this. Remember, I derived a little performance index.
We said if we had a material and we wanted to have a given stiffness, and we wanted to minimize the mass, we had that performance index that was E to the 1/2 over rho. And we had a chart of modulus versus density. And we saw that wood was really good.
You can do that for other sorts of properties, not just modulus. So you can make-- depending on what the mechanical requirement is, you can work out different performance indices. So I want to go into that in a little bit more detail. So the question is, how do we select the best material for some mechanical requirement?
So in the wood section, we looked at the minimum mass of a beam of a given stiffness. And we saw that the performance index was E to the 1/2 over rho. So let me do another one of these little examples, and then I'll show you some more of them.
So another example would be what material-- minimize the mass of a beam of a given strength or a given failure load.
So we'll call the failure load Pf. And we can see the maximum stress in the beam is going to be the moment in the beam times the distance from the neutral axis y, and divided by the moment of inertia. So here, M is the maximum moment in the beam. And y is the maximum distance from the neutral axis.
And I is the moment of inertia. And I'm going to say i goes as t to the 4. And I'm going to define a failure stress of the material sigma f.
So sigma max is going to go as my failure load times the length. That would be the moment. The distance from the neutral axis is going to go as t. And the moment of inertia is going to go as t to the 4th. And that's going to be the failure strength there.
So I can solve this for t. And then I'm going to write the mass in terms of t, and put that in there. So here t goes as Pf l divided by sigma f. And that's going to be to the 1/3 power. I guess I can scoot over here.
Then we can say that the mass M goes as the density of times t squared times l. So the mass M is going to go as rho times l times t squared. So that whole thing goes to the 2/3 power.
So if we look at the material properties, the mass goes as the density times the failure stress raised to the 2/3 power. So if we want to minimize the mass, we want to minimize rho over sigma f to the 2/3, or we want to maximize sigma F to the 2/3 over rho. So that's the performance index for that case.
So we can obtain these performance indices for different loading configurations and different mechanical requirements. And I don't want to go through a whole lot of them, but I'm going to put this up with the notes. So this is from Mike Ashby's book on Material Selection in Mechanical Design.
And this is a whole series of these performance indices for different situations, for things loaded in torsion, for columns and buckling, for panels and bending. So these ones are all for stiffness. And they all involve a modulus raised to some power divided by a density.
So a tie in tension, c over rho, the beam in bending is E to the 1/2 over rho. A plate in bending is E to 1/3 over rho. So you don't need to memorize those. But you can see you can derive these for different situations.
And here's another one for strength-limited design. So the shaft is, depending on what the specifications are, it's the strength raised to the 2/3 power over rho. The beam loaded in bending-- the top one there-- sigma f to the 2/3 over rho. That's what we just did.
So there's all these different kind of performance indices. So depending on what your situation is, you would pick one of these indices. And then what you can do is use these material selection charts, which plot one property against another on log-log scales.
And because all of these performance indices involve a power, they always end up being a straight line on your log-log plot. And here this one, I think, is the same as what I showed you for the wood. This one's the modulus here plotted against density.
So foams are down here. And other engineering materials are over here. And these guidelines here are the different performance indices.
So this one's E over rho. This one's E to the 1/2 over rho. This one's E to the 1/3 over rho.
And for this case here, as you move the lines up to the top left-hand corner, E is getting bigger. Rho is getting smaller. And so the actual value of the performance index is getting bigger. So you can use this to select a material.
So we've made these charts for foams as well. So here's a couple of charts for foams. And I think what I'm going to do is just go through them quickly.
And there aren't really that many notes, so I'll just put the notes on the website. And you can come and write all the notes down. And then we can finish this today.
So this one here is the Young's modulus versus density. And these are all sorts of different foams. So the low modulus ones tend to be flexible. The higher modulus ones tend to be more rigid.
And you could use this to select foams, if you wanted. You can also see what the range of values is. So the values of the modulus here goes from a little less than a 100-- because this is two orders of magnitude here, I think, each one of these-- down to about 10 to the minus 4 or a little less than that.
So there's a huge range. There's almost a range of a factor of a million in those moduli. And the same with the strengths here. The strengths go from 10 to the minus 3 mega-pascals up to about maybe 30 mega-pascals, something like that.
And you can see for the modulus and the strength, things like the metal foams are good. The balsa's good. Here's the balsa up here. Metal foam's up there.
So you can kind of see the range of properties that you could get. And then you could also-- need a drink, hang on. You can also plot the specific property.
So here's the compressive strength divided by the density plotted against the Young's modulus divided by the density. And here you want to be up at this end. So you would have a high strength and a high stiffness. So the balsa and the metal foams are good up here.
This next plot-- this is the compressive stress at 25% strain. And this is the densification strain. And if you think of having your stress-strain curve looks like this, something like that, so you could say that's a strain of 0.25 and that's the stress that corresponds to that. So that stress times the densification strain, which is out here someplace, is an estimate of the energy underneath the stress-strain curve.
So you can think of this right-hand plot here-- those dashed lines-- these lines like this and this and this-- each one of those corresponds to how much energy you would absorb under the stress-strain curve. So points that lie on here would have an energy of 0.001 megajoules per cubic meter. And over here, we're at 10 joules per cubic meter. So again, the balsa and the metal foams are good over here.
So you can use these plots to try to identify foams for particular applications. And I think there's a couple more. It doesn't have to be mechanical properties.
Here is thermal conductivity versus compressive strength. So you can imagine if you wanted some insulation, you wanted to have a certain thermal conductivity value, you probably also need at least some minimal compressive strength. You could also have something like a maximum service temperature, that maybe the foam is going to melt at some temperature. You can't go beyond that.
So there's some property there. And I think there's one more here. You can look at things like the density in terms of the buoyancy of a foam, if you have some buoyancy application.
And you can look at cell size on this one here. And cell size can be important for things like filtration and catalysis. So the amount of surface area goes as 1 over the cell size-- the surface area per unit volume. And so the cell size can be important for those sorts of applications.
So the idea is, you can make these material selection charts for foam. And you can put data on there. And you can compare foams. And you can use these performance indices.
So I'm going to leave it at that. There is a little bit more notes. But I'll just put them on the website, and you can get them from there. So I think we're good for today.
Free Downloads
Video
- iTunes U (MP4 - 155MB)
- Internet Archive (MP4 - 155MB)
Subtitle
- English - US (SRT)