Flash and JavaScript are required for this feature.
Download the video from iTunes U or the Internet Archive.
Description: The structure of cellular materials, honeycombs and modeling honeycombs are explored in this session.
Instructor: Lorna Gibson
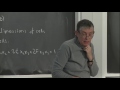
Lecture 3: Structure of Cel...
The following content is provided under a Creative Commons license. Your support will help MIT OpenCourseWare continue to offer high quality educational resources for free. To make a donation or view additional materials from hundreds of MIT courses, visit MIT OpenCourseWare at ocw.mit.edu.
LORNA GIBSON: All right, so I guess I should start. So I think last time we were talking about cell structure and cell geometry. And I got as far as putting this image here up. And I talked a little bit about how this works. And I was going to go over it again and then write the notes down today. So we'll start from there.
So we're going to do a little bit more on cell structure today. We're going to talk about some topological laws for cellular materials for polyhedral cells. And then we'll start talking about modeling honeycomb materials, and talk about how we look at the mechanical properties of honeycombs.
So I think where we left off last time was we started talking about mean intercept length. So the idea is that with-- hello, hello-- if you have a honeycomb, it's fairly easy to define the cell shape in terms of the ratio of the cell edge lengths, h over l, and the angle that the inclined cell wall is to the vertical one. But for a foam it's a little more difficult. And what people do is they measure this mean intercept length.
So last time I talked about it briefly. So the idea is you take an image of the structure you're interested in. You sort of draw out the outline of a planar surface. And then you put on that a test circle. And you superimpose on the test circle equidistant parallel lines.
So say we start off at theta equals 0. We then count how many times the cell walls intercept those lines. And we get a number of cells per unit length. And that gives us an intercept length for that orientation.
Then we rotate it around a little bit, say 5 degrees or something. And we measure a new intercept length for that orientation. And we keep doing it all the way around, 180 degrees. And then you get-- then what you do is you plot those points-- if I can find my little pointer-- we plot those points. And it will form an ellipse. And the major and minor axes of the ellipse correspond to the principal dimensions of the cells on that plane.
And then you can do the same for perpendicular planes and form an ellipsoid. And you can get the three principal dimensions. You can also get the orientation of the cells by getting the orientation of this ellipse, or the ellipsoid in three dimensions.
So let me just write down some notes that kind of summarize all of that. So I'm going to say that for foams, we characterize the cell shape and orientation by using these mean intercepts-- mean intercept lengths.
So we consider a circular test area on a plane section. So you want to use a circle and not say, a square or a rectangle. Because if you had a square, then you'd have different total lengths of line, depending on what orientation you took it. So you want to use a circular test section. And then you draw equidistant parallel lines.
So for example you might start at theta equals to 0. And then you count the number of intercepts of the cell walls with the lines.
So if we say that Nc is the number of cells per unit length of line, then we can get the intercept length for that orientation. Say for theta equals to 0, it works out to 1.5/Nc. So it's not just 1/Nc, because you may not be cutting the cell-- you know, you're cutting the cell-- say you've got a three dimensional cell like this. You're cutting it at different places along here. So people have worked out the stereology of that. And there's a constant that's 1.5 that fits into there.
So then you just repeat that process for different increments of theta. So you increment theta by some amount, something like say, 5 degrees. And then you repeat that whole process.
And then you plot a polar diagram of the intercept lengths versus theta. And you then fit an ellipse to the points. And if you did it in 3D, you'd have an ellipsoid. And then the principal axes of the ellipsoid are the principal dimensions of the cells. And the orientation of the ellipsoid is the orientation of the cells.
Hello.
And you can write the equation of the ellipsoid. So it would be something like Ax1 squared plus B x2 squared plus Cx3 squared plus 2Dx1x2 plus 2Ex1x3 plus 2Fx2x3. And that would all equal 1. And you can write those coefficients as a matrix. And if you do that, the first three, A, B, C, are the diagonals, and D, E, F are the off diagonals.
And you can also represent this is a tensor. And if you do, it's called the fabric tensor. So the fabric-- I think they use that term for other types of materials-- it says something about the orientation of the material.
And if you have this matrix here, if D, E, and F are all of 0, then A, B, and C are the principal dimensions of the cell. So if all non-diagonal elements are 0, then A, B, and C are the principal dimensions.
Are we good with how this works? So it's kind of a crank and churn kind of thing. But it gives you a way of characterizing the cell shape and the orientation of the cells in the foams.
So the next thing I wanted to talk about was the connectivity of the cells. So imagine we have an array of cells. And if we have an array we have vertices that are connected by edges. And edges surround faces. And the faces enclose the cells.
And there's something called the edge connectivity, which is usually given the symbol Ze. And that's the number of edges that meet at a vertex. And there's a face connectivity, and that's the number of faces that meet at an edge.
And it's very common for honeycombs to be three connected. So Ze is 3. And it's common for foams to be four connected. And there's some topological laws that are kind of interesting. And so we'll get into those after this bit on connectivity.
So for the connectivity we have vertices, which are connected by edges, which surround faces, which enclose cells. So we're going to talk about the vertices, the edges, the faces, and the cells. So the edge connectivity, Ze, is the number of edges that meet at a vertex.
And for a honeycomb, say a hexagonal honeycomb, Ze is 3. So I have a little honeycomb here. If we look at the number of edges, there's three edges, connect at a vertex. So Ze is 3. And for a foam, Ze is typically four. So I'll just say typically here.
And if I go back, if you look at the sketches here of the rhombic dodecahedra and the tetrakaidecadedra, if you look at the tetrakaidecadedra, you can see the number of edges. So here's one edge. Here's another one here. There's another one here. And there's another one here. So that's the four edges that are meeting at that vertex there. So if you look at arrays of cells, you can convince yourself that Ze is typically 4 for a foam.
And then we also have the face connectivity, Zf. And that's the number of faces that meet at an edge. And that's typically three for foams.
And so again if you look at these pictures you can sort of see how the face connectivity is three. So if you look at this bottom one here, there's faces here. And then there's another face-- well, let's see if we can-- it's kind of hard to show.
If you look at this one here, there's this cell. There's that face there. And then there's another one coming out of the page, I think. OK. So that's connectivity.
And the next thing are some of these topological laws. So the first one I'm going to talk about is called Euler's law. If you remember Euler from buckling, same guy.
So Euler's law relates the number of vertices and faces and cells and edges for a large array of cells. So we can relate the total number of edges, so I'm going to call that E, vertices V, faces F, and cells C. That total number is related by Euler's law for a large aggregate of cells.
So in 2D Euler's law is that the total number of faces minus the number of edges plus the number of vertices is equal to 1. And in 3D, you just add a minus the number of cells in front. So minus the number of cells, plus the number of faces, minus the number of edges, plus the number of vertices is equal to 1.
So there's some interesting things you can figure out using Euler's law. And one of the things I wanted to look at was if we had an irregular honeycomb that was three connected. So say we have a honeycomb that's not just a regular hexagonal honeycomb, or not even one that's got repeating hexagonal cells. But say we had a honeycomb where some of the cells had 5 sides to them, some of them had 7, some of them had 6. You can ask, what's the average number of sides per face? And you can use Euler's law to figure that out.
So we're going to look at an irregular three connected honeycomb. Let's see, I can start that up here. So when I say irregular, I mean we've got cells with different numbers of sides.
So we have an irregular-- oops. You OK, Greg? --that is three connected. And what is the average number of sides per face? And I'm going to call that n bar.
So we're told that it's three connected. So that's saying that the edge connectivity is 3. So there's three edges coming to each vertex.
So imagine that you had just a regular hexagonal honeycomb, like this. Here's our vertex here. And there's our kind of three edges that come into it. And each vertex is going to have half of each edge, right? Because the next vertex-- each edge is shared between two vertices.
So if Ze is equal to 3, then the number of edges per vertex is 3/2. Because each edge is shared between two vertices.
And I'm also going to define something I'm going to call Fn. And Fn is going to be the number of faces with n sides. So I could have some number of the cells have six sides, some number have five sides, some number have seven sides. So these are-- Fn is the number of faces with some particular number of sides, n.
So if we have Fn is the number of faces with n sides, then if I sum up n times Fn and divide it by 2, that's the number of edges. So imagine I have all these faces. I take n times Fn.
So say we had four five-sided faces. That would be four of those. There's be 20 edges associated with that, 20 sides. Then I have some number of six-sided, some number of seven-sided. I add them all up. And I have to divide by 2 to get the number of edges, because each edge separates two faces.
OK. And then I can use Euler's law. So I can say F minus E plus V is going to equal 1. And here I've got an F minus E plus-- I can put V here. V's going to be 2/3 of E. So I've got that.
So that's the same as F minus 1/3 of E is equal to 1, like that. And then for E I can substitute this thing here in. So that gives me F minus 1/3 of the sum of n times Fn over 2 is equal to 1. And then what I'm going to do is multiply everything by 6 so I can get rid of my denominator here.
So 6F minus sum of nFn is going to be 6. And then I'm going to divide that through by F. So that's 6 minus sum of nFn over F is equal to 6/F.
And then if I let F go to a large number-- so say I've got a large aggregate of cell. I've got lots of faces. I'm going to let F become large. So if F becomes large, then 6/F is going to tend to 0. Let me get the other rubber.
AUDIENCE: Professor?
LORNA GIBSON: Mhm?
AUDIENCE: That's-- F is like the total number of faces, not the total number of faces per cell.
LORNA GIBSON: F is the total number of faces. And Fn is the number of faces with n sides. We've got some number with 5 sides, some number with 6, some number with 7. So we're almost at the end here.
So 6/F goes to 0. And so that says that the sum of n times Fn over F is equal to 6. And that just is n bar. That is the average number of sides per face.
This is your-- kind of your total number of sides in the whole thing. And you're dividing by the total number of faces. So that is the average number of sides per face.
So what this is saying is if you have a three connected honeycomb, the average number of sides per face is always 6. So that if you introduce a cell with 5 sides, somewhere you have to introduce a cell with 7 sides, so that they compensate and you come back out to 6. And I have a little soap bubble picture here that kind of illustrates that.
So here we have a soap honeycomb. So you can make these just by putting two glass sheets close together with a soap bubble froth in between them. And you can kind of see in this picture here, they've numbered how many sides each cell or each face has. So here's one with 5, here's one with 7.
And I'm not going to add these up all together. But you can kind of see that the 5's and the 7's kind of compensate for each other, and that the average works out to about 6. And this is true for a large aggregate of cells. So if you only have a few, it's not going to work out perfectly. You need to have a large aggregate to have it work. Yeah?
AUDIENCE: And that 5, 7 balance doesn't have to be touching, right?
LORNA GIBSON: No, no, no, overall. Yeah, overall. And, you know, you could have one with 4 sides, and you'd need two 7's or one 8 or something. But you'd need to have that balance out and match up.
OK. So that's the Euler law. Now there's a couple more of these kinds of things. There's something called the Aboav-Weaire law. And so the Aboav-Weaire is sort of related to the Euler because it's looking at this idea that if you have a three connected honeycomb, if you introduce a 5-sided cell, you have to introduce a 7-sided cell to compensate.
And what Aboav noticed was that generally cells with more sides than average have neighbors with fewer sides than average. Let's see. So we'll say the introduction of a 5-sided cell requires the introduction of a 7-sided cell. And I'll just put-- this is all for a 3 connected net, a 3 connected honeycomb.
So that generally, cells with more sides than average have neighbors with fewer sides than average. And in 3D, you could say the same thing about the faces. The cells that have more faces than average have neighbors with fewer faces than average.
So Aboav made observations of this. And it was Dennis Weaire who made a proof of it. And the equation that they came up with relates the average number of sides in the cell surrounding a candidate cell. Let's see-- are we going to be able to put it in here? Maybe.
So say you have a candidate cell and say it has n sides. So you look at one particular cell and you say, count up, it's got n sides around it. And then you count up the number of sides of all the cells surrounding it. It has n neighbors because it has n sides, so then the average number of sides of the n neighbors is called m bar. It has n sides.
So then the average number of sides of its n neighbors is m bar. And m bar is equal to 5 plus 6 over n for a 2D honeycomb kind of cell structure. OK, so that's the Aboav-Weaire law.
And then there's one more of these things. The last one is called Lewis' rule. And Lewis looked at biological cells and 2D cell patterns, and he found that the area of the cell varied linearly with the number of the sides. And he found just an empirical relationship. It looks like this. We can say what everything is in a minute.
So he found that the area of a cell with n sides, that's A n, was linearly related to the number of sides, so this n over here, and naught's just a constant and A n bar is the area of the cell with the average number of sides. So here, A n is the area of cells with n sides and A n bar. And then n naught is just a constant. And he found that for 2D cells n naught was equal to 2.
And if you look at voronoi honeycombs-- remember last time we talked about those voronoi honeycombs-- you can show that this holds for voronoi honeycombs. And then you could write a 3D version of this as well. And in 3D, it's the volume and faces instead of the areas and the number of sides. So you can say that the volume of the cells with f faces relative to the volumes of the cells with the average number of faces, they vary linearly with the number of faces. So there's sort of an exactly analogous expression here.
And here, this f naught is another constant. And in 3D it's about equal to 3. So these are all just kind of interesting topological rules that are nice to know about. OK. Yeah?
AUDIENCE: Basic question. In two dimensions, what is a face? Like what does that refer to?
LORNA GIBSON: So-- and let me put my little slides again. So say we have some honeycombs like this, then say we look at this guy. So that's a vertex there, that's an edge, and this thing in the middle here is the face. So in 2D, the face and the cell is kind of the same thing. All right? And then--
AUDIENCE: [INAUDIBLE] sides, what's different with the edge?
LORNA GIBSON: It's not quite. Like if I count up the number of edges, I say one, two, three, four, five, and I count those up like that. But if I say sides of the face-- see that's a face or it's a cell-- I would say that had six sides. Right?
So typically when people say it has-- a cell or a face has so many sides, they count up how many all around it. But because each side is-- or each edge is-- shared between two faces, the number of edges is actually half that. Right? Because there's one edge, but if I count up the number of sides for this face and I count up the number of sides for that face, I'm counting that twice.
So it's a little bit-- so I try to see edges when I'm talking about adding them all up and I try to say sides when I'm talking about, here's a face, how many sides does it have. OK? It's a little bit confusing. Anybody else?
AUDIENCE: [INAUDIBLE] what is n bar naught?
LORNA GIBSON: n bar naught, did I put an n bar naught? Oh, that's where I didn't erase this enough. There you go. It's just n naught. OK.
So we've been talking about the structure of the honeycombs in the foams. And what we ultimately want to do is be able to model the mechanical behavior or the thermal behavior, some sort of behavior of the cellular material. And for looking at mechanical behavior, there's three main approaches that people take. So you have to model the structure somehow. So there's three main approaches.
And the first one is to use the unit cell. So say, for example, for the honeycombs, if you have a hexagonal honeycomb you'd just use that unit hexagonal cell. And that's what we're going to do probably starting later on today. So for the hexagonal honeycomb, it's kind of obvious. You would use a unit cell, the thing's periodic, you figure out how that unit cell behaves, you're all set.
For a foam, it was not so obvious a unit cell to use. But the thing-- people use different things, but one of the common ones they use is a tetrakaidecahedron. So the nice thing about the tetrakaidecahedron is that it packs to fill space. So it's a repeating single cell. Packs to fill space.
But, in fact, real foams aren't tetrakaidecahedrons, so this is a bit of an idealization. So we'll just say foam cells are not tetrakaidecahedrons. OK, so that's one approach.
And then a second approach is to use something called dimensional analysis. So in dimensional analysis, what you want to do here, with this technique, is model the mechanisms of deformation and failure in the structure. But you don't necessarily represent the cell geometry exactly. And so what you do is, you say one thing is proportional to another and there's some constant of proportionality, and you just wrap all of those constants of proportionality up at the end.
So for instance, when people look at foams, the geometry of the foams is kind of complicated. There's cells with different number of faces, there's different sizes of cells, it's kind of a mess. So we could just say the geometry is complex and it's difficult to model.
And with dimensional analysis, instead what we do is we model the deformation mechanisms and failure mechanisms. And you can get quite a bit out of just modeling those. So when we look at modeling foams, we're going to do this, and you'll see how it works.
And then the third method is to use finite element analysis. So this is a numerical technique and it's a very standard numerical technique. And one of the nice things about this is you can apply it to random structures. So for example, those voronoi structures we saw, if you want to try to see-- say you had a certain amount of material and you had a honeycomb that was a regular hexagonal honeycomb. You had the same amount of material and you put it in a voronoi honeycomb, and you want to know how does having a random material affect the properties relative to the uniform material? You could figure that out using finite element analysis.
So you can apply it to random structures. And another thing you can do with finite element analysis-- and people in the orthopedics end of the world often do this-- if you're interested in trabecular bone, that porous type of bone I showed you the first day, people can take micro-computed tomography images of trabecular bone and they get a file which basically says, every voxel, says if it's solid or it's void. And you can use those files as input to a finite element analysis. And so you can analyze exactly how a piece of a trabecular bone would deform. So it's nice for that.
So one of the things we're going to talk about later is we'll look at the structure of trabecular bone and the sort of mechanics of trabecular bone, and I'll show you some results that a former student of mine did, where we look at-- say you have a sort of intact structure of a certain density and then you reduce the density by fitting the cell walls or you reduce the density by removing cell walls-- because in osteoporosis sometimes the walls resorb all together-- and you can see what residual strength you would have for some given amount of density loss. So it's good for looking at that kind of a thing.
You can also use it for looking at local effects. So you can look at defects, for instance. So if you think of the trabecular bone as having missing trabeculae, that would be a defect in the structure. You can look at that.
You can look at size effects. So when we were studying some of those metal foams, some of them have very large cells, and if you have a small sample relative to the cell size, you may only have four or five cells across the dimension. Where you've cut the cells, you've got edges that are less constrained than in the bulk of the material because at the outer edge you've cut them. They're not connected to anything else. And so you can look at edge effects that relate to the size effects in foams as well.
So these are basically the three approaches that people use for modeling cellular materials. And what we're going to do is we're going to start with looking at honeycombs and we're going to look at these hexagonal kind of honeycombs like this. And one reason to start with them is that they have this unit cell structure. And if you can analyze how that unit cell deforms and fails, you can say something about the whole structure.
And it turns out that the honeycombs, they deform and fail by the same mechanisms as the foams. So if you can understand through this simple structure, it gives you a lot of insight into how the foams behave. So if I deform this a little bit, the cell walls bend. And you can show that if you deform this guy a little bit, the cell walls bend. And so you can learn a lot by looking at the honeycombs and then sort of applying that to the foams.
So we're going to start off-- so that's the end of the section on sort of the structure of the cellular materials-- and now we're going to look at modeling the mechanical properties and we're going to start with the honeycombs and then we're going to do foams. So when we talk about the honeycombs, we've got this hexagonal structure here and we're going to call properties in this plane the in-plane property. So if I load it this way on or that way on, those are in-plane, and if I load it that way on, those are out of plane. So think of the cells are in the plane and the prismatic direction is the out of plane. And clearly, the honeycombs are going to have similar properties this way and that way, but they are going to have very different properties that way.
So we're going to start with the in-plane behavior. So the honeycombs have these prismatic cells and they're widely available in different materials, polymers, metals, ceramics. And they're used in a variety of applications. So one of the most common is to use them in sandwich panels. So I brought a couple of sandwich panels with me today.
So here's a couple of sandwich panels that have honeycomb cores. This one's an aircraft flooring panel. It's got carbon fiber faces and a Nomex core, honeycomb core. And this is an aluminum honeycomb. It's got aluminum honeycomb core and then aluminum faces, and it's kind of amazing how stiff that little panel is. And each of the pieces is really not that stiff at all, but the thing put together is quite stiff, and we'll talk more about that when we get to sandwich panels.
So it's used in sandwich panels. They're used for energy absorption. So sometimes you'll see there's some natural disaster area and they fly in helicopters and they drop big crates of supplies, and they will have it like a pallet with a big crate thing. Often they have a honeycomb, like a metal honeycomb, that is kind of oriented this way. So the pallet would be like this and the honeycomb's like that. And the idea is that when they drop it-- they sort of bring it down as close as they can-- and then the honeycomb absorbs some of the energy from the impact.
And they're also used, I think, sometimes in car bumpers. So they're used for energy absorption. And they're used as carriers for catalysts.
So the catalytic converter in your car looks like this, this is kind of the material that's used in the catalytic converter in your car. And the way that works is, the cell walls here are actually porous and they're coated in the platinum, which is the catalyst, and half of the cells are blocked off on this end. So every other cell on this end is blocked off and then every other cell over here, the opposite ones, are blocked off. And so the gas is forced down a channel but then through the wall and then out the next channel. And that's where the reaction actually occurs, is in the cell wall.
So they're used as carriers there. And some natural materials also have a cellular structure, have a honeycomb structure. So for example, things like woods and cork have a honeycomb structure, too. So I said the mechanisms of deformation and failure in the hexagonal honeycombs parallel those in foams. So we can learn a lot about foams by understanding the honeycombs.
And then, similarly, the mechanisms of deformation and failure in triangulated honeycombs parallel those in the lattice materials. Remember I brought those lattice materials in? The sort of trust type materials. The triangular honeycombs have a behavior similar to those lattice materials.
OK. So let me scoot over here. OK. So let me scoot out of this one. OK.
So here is our kind of hexagonal geometry. This is kind of an idealized geometry here. And, as we talked about in this section on the structure, we're going to call these vertical walls, we're going to say they have a length h, the inclined walls have a length l, the wall thickness is t, and there's going to be an angle between the horizontal and that inclined wall of theta. And I'm going to define three axes here, an x1, an x2, and an x3 axis. So the x1, x2 plane is the in-plane and x3 is out of plane. OK?
So if we load our honeycomb up, we get stress strain curves that look like this. So the ones on the left here, over here these three are all in compression, and the ones on the right, these three are all in tension. OK, so let's talk about the compression ones first. And let's start at the top.
This is in elastomeric material, so like one of these rubber honeycombs. This would be a material that yields plastically, so like an aluminum honeycomb. And this would be a honeycomb that fails in a brittle manner, like one of those ceramic honeycombs. OK?
So if we go up to the elastomeric one, up here, if I compress it I get a linear elastic part first, and then at some point, I get a stress plateau where the stress is almost constant for strains that are quite large. And then finally, the stress starts to rise quite sharply at the end here. So the strain here goes from 0 to 1. So that's a strain of 100%. You've completely flattened the thing there.
So that's a large strain. So initially, when we're loading it up to smaller strains like this, we've got linear elastic behavior and these cell walls bend. And you can relate the modulus here-- let's see where'd my little arrow go-- you can relate this Young's modulus here to the bending of those cell walls. And we're going to-- I don't know if we'll finished that today-- but we'll start that today.
Then-- oops, lost my arrow, where'd my arrow go-- then at the stress plateau here, that plateau is related to collapse of the cells. So if I have my little rubber honeycomb and I load it, at some point, the cell walls buckle. So you see how they've buckled there? And that stress plateau, I can smush that to quite large strains that are roughly constant stress. OK?
So what's happening here is that we're buckling the cells. And as we go along here, the buckling deformation gets bigger and bigger. And then if I smush it and I've got it kind of like that, at some point it becomes much harder to press it together again because the cell walls are now touching each other and they're pressing against themselves, and to get a certain amount of strain, it gets much more difficult to do that. And the stress required to do that gets much bigger. And that's what leads to this last piece of the stress strain curve here, which is called densification because you've almost eliminated the pores. It's hard to eliminate them entirely but the porosity has gone way down by the time you're up there.
So this type of stress strain curve where you've got linear elasticity and then a stress plateau and then the densification is classic for compressive behavior of cellular materials. So elastomeric ones will have a plateau that's related to elastic buckling. I lost my arrow again. There we go.
If we had a metal honeycomb, we'd again have linear elasticity related to cell wall bending. This plateau here would be related to yielding of the cell walls. So say we had aluminum honeycomb, the aluminum could yield, and that would again cause this stress plateau. And then we get densification.
If I had a brittle honeycomb like the ceramic one, we'd have initial linear elasticity. Then you've got a stress plateau that's kind of a lot of up and down here. And the serrated nature is related to the fracture of individual cell walls. So it goes up and down because when you break a cell wall, the stress drops off, and then the other cell walls will try to pick the stress up again. And so each one of those little up and downs corresponds to breaking a cell wall.
But if you kind of took an average of that, you can see there's a stress plateau and then there's the densification region. So in compression, the shape of the curves is very similar and the mechanism of the plateau varies a little bit. So let's see if I can write some of that down.
So in compression, we can say we have three regimes of behavior. So we've got the linear elastic regime initially and we're going to see that's related to cell wall bending. Oh, thanks. And then we've got a stress plateau. And for elastomeric materials, that's caused by buckling of the walls. For metals, it would be caused by yielding. And for ceramics, it would be caused by a brittle crushing.
And then we've got densification. And that's related to the cell walls touching. And if we increase the ratio of the thickness of the cell walls relative to their length, we're going to increase the stiffness, so the Young's modulus of the honeycomb. The stress plateau I'm going to call sigma star. And we decrease the strain at which that densification occurs, which I'm going to call epsilon D.
So you see over on the right hand side of these plots here, that strain there is the densification strain, epsilon D. So that's in compression. And these materials are very often loaded in compression.
In tension, we still get linear elasticity initially. And that's going to, again, be related to the bending of the cell walls. But if we look at the stress plateau, if you look at these three curves here on the right, the stress plateau only exists if the material has a yield point and you get some plastic yielding there. If you have an elastomer, if I pull on this-- you don't get buckling in tension, so you're not going to get a stress plateau in tension. And for a brittle material like one of those brittle honeycombs, if you pull that in tension, you would just get a crack propagate and the thing would break into two pieces and so you don't get a stress plateau there.
So the stress plateau in tension only exists if the material yields. So you don't get any buckling in tension. And for a brittle honeycomb, you would just get fracture. OK?
These inclined walls are going to bend. We're going to see that in more gory detail in one minute. If you can wait one minute. OK. So are we good with a stress strain curves yet?
AUDIENCE: More of an abstract question, but is it possible [INAUDIBLE] to get collapse this way before the plateau?
LORNA GIBSON: I haven't seen that. But maybe it it's possible, I don't know. I don't think so, but maybe. Anybody else? OK.
OK, so here's some photographs of honeycombs. So these ones are white but these ones are just the same. So most of them are just a regular hexagonal honeycomb and one of them is this funny shaped honeycomb here. These two guys at the top, these two here, are unloaded. And then the rest of them have some loading.
So if you look at this one down here-- so here I'm taking the honeycomb and I'm loading it. This is the x1 direction, that way on. And if you look very carefully, you can see what happens is these vertical walls just move sideways and that is going to zoot, with the sound effects. And then the-- I can't help making sound effects-- and then these guys here bend. OK, so this guy here-- it's maybe a little hard to see it on the image but it's actually a little bit bent there. So that's loading it this way on.
And then similarly, if I take it and I load it that way on, that's the x2 direction. And now these guys here, the vertical guys, are just going to compress a little. But these guys here, the incline guys, are still going to bend a little bit. And I've got some schematics that's going to show that a little bit better.
And then if I shear it, if I took it like this and I-- I can't do it because my hands aren't glued to the rubber-- but if I could sort of shear it this way on, then you would get this kind of deformation here and that also involves bending. You can imagine these guys here would bend if I do that to them.
And then the buckling deformation looks like this. If I scooch that like that, it should look kind of like that picture there. OK? So that's kind of what the deformation looks like for these sorts of honeycombs. So these were elastomer rubbers.
These are just some images from an aluminum honeycomb. So here's, the top one's the undeformed honeycomb, the middle one's loading it in the one direction from left to right, and the bottom one's loading it in the two direction from top and bottom like that. OK?
So you can imagine that you've got little cell walls. If you load it up high enough, those walls are going to yield and we're going to see that the yielding in the walls causes the formation of something called plastic hinges and the walls can rotate and they can produce these kind of shapes. OK.
So then this is sort of a schematic stress strain curve here. And this is showing what happens if you increase the thickness of the walls relative to the length, or you increase the relative density, you increase the volume per action of solids. And this kind of shows the different regimes.
So over here-- well let's, first of all, start with the different relative density. So this one here is the lowest relative density, then this is higher, and higher, and higher. And not too surprisingly, the more you increase the density, the more material you've got, the stiffer it is, the stronger it's going to be. And the more material you've got, the sooner it's going to densify. If you've got more solid in here, you're going to reach that densification strain at a smaller number.
OK, so the shape of the curves looks like this. And you can define these three kind of regimes. So everything in here is linear elastic, everything in this big sort of envelope here is the plateau region, and everything up here is this densification region. So this is just a bigger picture kind of plot. OK, so let me skip through all of that.
All right. OK, where are we? Chalk? Here we go.
OK, so I think I mentioned this before, but let me just go over it again. So there's three types of things that affect the properties, the mechanical properties, of the honeycombs. And probably the most important thing is the relative density of the honeycomb. So remember, we said this was the same as the volume fraction of solids, and for a hexagonal honeycomb, you can show that's equal to the thickness to length ratio times h over l plus 2 divided by 2 cos theta times h over l plus sin theta.
And if you have regular hexagons, so h over l is equal to 1, all the sides are of equal length, theta is equal to 30 degrees, the relevant density is 2 over 3 times t over l. So it just goes linearly with t over l. The thickness to length ratio of the walls.
So it depends on how much solid you've got. Depends on the solid properties. So the Young's modulus of the solid, yield strength if it's a metal, some sort of fracture strength if it's brittle. It also depends on the cell geometry, which we can describe with h over l and theta.
So if we think of a cell here-- that's our edge length h, that's our edge length l, that's our angle theta, here's the cell wall thickness t, and then we've got some set of solid properties here. OK? So that's kind of the set up. And we're going to define x1, x2 axes like that.
And we're going to make a few assumptions just to make life a little bit simpler. So we're going to assume that t over l is small, so that also means the relative density is small. And what that means is that we're going to be able to neglect axial and shear deformations. So you can imagine, if I have a thin wall and I'm applying loads that produce moments and produce bending, if the wall is very thin then the axial and the shear deformations are going to be small.
I'm also going to assume the deformations are small. And what that means is that I'm going to neglect any changes in the geometry of the cell during the deformation. And I'm going to assume that the cell wall is linear, elastic, and isotropic.
And we're going to start off with looking at in-plane behavior, and we're going to start with the elastic moduli. And if we look at the elastic moduli, we're going to be talking about Hooke's law. And Hooke's law and the elastic behavior of the material can be described by a set of elastic constants. And if you recall, the number of independent elastic constants, how many constants you need to describe the material, depends on its symmetry. And these materials are orthotropic.
So the regular hexagonal honeycomb is actually transversely isotropic, but imagine that h was not equal to l, then it would be orthotropic. So remember, orthotropic means that you can rotate the structure 180 degrees about three mutually perpendicular axes and the structure looks the same. So if I take this and I do that, it looks the same, and if I do that, it looks the same, if I-- no matter how I rotate this, about three mutually perpendicular axes, the structure remains unchanged. So it's orthotropic.
So I'm going to write down Hooke's law for our orthotropic material, and then we'll talk about the constants that we're going to work out. OK, so this is Hooke's law for our orthotropic material. And let me just remind you what our notation is here.
So epsilon 1 is epsilon 1 1. Epsilon 2 is epsilon 2 2. Epsilon 3 is epsilon 3 3. Epsilon 4 is gamma 2 3. Epsilon 5 is gamma 1 3. And epsilon 6 is gamma 1 2.
So these are the normal strains here, epsilon 1, 2, and 3, and these are the shear strains here, epsilon 4, 5, and 6. And you remember this convention where the subscripts add up to 9. So 4 plus 2 plus 3 is 9, 5 plus 1 plus 3 is 9, 6 plus 1 plus 2 is 9.
And then the stresses are a similar thing. So sigma 1, sigma 2, and sigma 3 are the normal stresses. And then sigma 4, sigma 5, and sigma 6 are the shear stresses.
And for the in-plane moduli, so we're dealing with the x1, x2 plane, there's four independent elastic constants. So we could think of it as E1, E2, a Poisson's ratio 1 2 and a shear modulus in the 1 2 plane. OK?
And the compliance matrix is symmetric, so there's the reciprocal relationship between the moduli and the Poisson's ratios. And then the notation I'm going to use for Poisson's ratio, I'm going to say that mu i j is minus the ratio of the strain in the j direction divided by the strain in the i direction. OK.
So what we're going to do next is we're going to calculate some of the elastic moduli. I'm going to show you the derivation for E1 star and mu 1 2 star, and you can get the other two in a similar way. So I'm not going to do all of them but next time we'll do the derivations for the Young's modulus in the Poisson's ratio. OK?
And then we're going to talk about the out of plane direction later and we'll get the moduli for the out of plane direction as well. OK? So I think I'm going to stop there for today. And then we'll start doing the derivations next time.
Free Downloads
Video
- iTunes U (MP4 - 168MB)
- Internet Archive (MP4 - 168MB)
Subtitle
- English - US (SRT)