Flash and JavaScript are required for this feature.
Download the video from iTunes U or the Internet Archive.
Description: This session begins with a look at cork as a natural honeycomb structure, and covers properties of foams and some modeling.
Instructor: Lorna Gibson
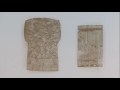
Lecture 7: Natural Honeycom...
The following content is provided under a Creative Commons license. Your support will help MIT OpenCourseWare continue to offer high quality educational resources for free. To make a donation or view additional materials from hundreds of MIT courses, visit MIT OpenCourseWare at ocw.mit.edu.
LORNA GIBSON: I wanted to talk a little bit about cork partly because cork is kind of interesting. Cork has a structure that's a little bit like one of those honeycomb things. What I'm going to do is I'm just going to talk and go through the slides. I'm not going to write the notes on the board. There's only a few pages of notes, and it's in the Stellar site. I'm not going to write notes for this because it's just really for fun.
This first slide starts off with historical uses of cork. Cork was used by the Romans. They used it for the soles of sandals, the same as we do. And they used it for stopping bottles of wine, the same as we do.
But they didn't realize that you could just use the cork. They would take the cork, put it in the wine bottle, and then they would use pitch which is a tarry stuff from a tree. They would use the pitch and seal the bottle with the pitch.
In the 1600s, there were some Benedictine monks that realized that you could just use the cork and not use the pitch. They were the ones who really perfected the use of corks in wine bottles for sealing it.
So what is cork? Cork is the bark of a tree called Quercus suber, the cork oak. Here's a piece of the cork bark. All trees have a layer of cork in them. But the thing that's different about Quercus suber is that it's very thick and the corks are obtained from this thick layer.
Quercus suber is a Mediterranean type of tree. It grows, Portugal is the main place that exports cork, but also places like Algeria, Spain. You can grow it in California.
The cork is kind of unusual because-- let me scoot onto the next slide-- it's kind of unusual. So here's a little picture. I went to Portugal when I was a graduate student doing this project. Here's the cork tree here. Here's the little mini we rented. Here's the cork being harvested here. Cork's unusual because you can remove the bark from a cork oak tree and it regrows.
So most trees if you did this, you would kill the tree. But cork doesn't get killed by doing this. What happens is they plant trees. You have to wait something like 10 or 15 years for the tree to get big enough to harvest the cork. And then the first harvest is poor quality and they don't use that. And then you have to wait another 10 years or so before you can actually harvest the cork.
So you can imagine if a cork orchard or forest gets chopped down to build a skyscraper, or apartment buildings, or something, it's not an economically feasible thing to plant cork trees these days. So when the trees are cut down, they don't tend to get replanted at this point. And there's a number of artificial substitutes for corks. You've probably seen wine bundles with foam plastic corks in them too.
OK. The reason it's called Quercus suber is that the cell walls in this particular type of cork oak are covered with a waxy substance called "suberine." That's where the Quercus suber-- "Quercus" is "oak." Every oak is Quercus something. "Quercus alba" is white oak. Quercus just means oak.
If we look at the structure of the cork, we can see that it's got these different views of the cork that are seen here. This is a drawing by Robert Hooke in the 1600s from his book Micrographia. He was the first person to really draw cork like this.
You can see he drew sort of boxy cells on this side. And then, the other perpendicular plane, the cells have this structure here, sort of more rounded. And here's a little sketch he's got of the cork tree.
Over here are SEM pictures. These two planes here correspond to this plane in Hooke's drawing. This plane here corresponds to this plane here. This over here is Hooke's actual microscope. I think the Royal Society still has that microscope that Hooke used in the 1600s.
Some of you know that Hooke wrote this book called Micrographia. He got one of the first microscopes. He looked at a lot of different materials, and he drew these beautiful drawings. He wrote a page or two about each of the drawings.
Harvard has a first edition of Micrographia, and I made a little video on it. So I thought I'd show you the video because the drawings are beautiful. But the url's on the slides, and so you can watch it yourself.
There's more on this and on how he came to be so good at making scientific apparatus, how he came to do the Micrographia book. At the end of it, there's a comparison of a number of his drawings with modern SEM images of the same thing.
He had this very famous picture where he draws a flea. Don Galler, the person who runs the SEM for me, I had him put a flea in. And he has essentially the same kind of image. The thing that's spectacular is you can see how much of the detail that Hooke was able to capture in his drawings. There's some really beautiful drawings.
OK. So let's go back to cork. Hooke was the first person to use the word "cell" to describe biological cells, and he described the cell in cork. That's the structure looking at the SEM micrographs and his optical micrographs. These are just some more higher resolution, higher magnification, images.
One of the things that you can see is that the cork has these little corrugations on the cell walls. See those little wrinkles? All the cell walls have those little wrinkles. This plane here is the perpendicular plane. If you look down into the cells, you can see those blurry things. Those are the corrugations in the cell walls. That's the structure.
Here's a schematic. Here's the cork tree. The cork is the layer just beneath the bark. This is a picture of how the cells are oriented relative to their radial, and tangential, and axial directions. You can think of them as roughly hexagonal. They've got these little corrugations.
This is a schematic of an individual cell. We measured the dimensions of the cells, and these are some average dimensions here. Typically, the cells are tens of microns long, and the cell wall is about a micron thick. Something like that. OK? One of the things we're going to see is that corrugated structure gives rise to some of the interesting properties of cork.
If we load cork and just do mechanical tests on it-- this is just a uniaxial stress-strain curve. You can see the stress-strain curve looks like all these other curves we've seen for honeycombs. There's a linear elastic part here. There's a stress plateau here. And then there's a densification part here.
Typically, the relative density of cork is around 0.15. Something like that. It densifies at a strain of something less than 0.85. It's a stress-strain curve.
And when we did our little project on cork, we measured the properties in the three directions because in one direction, it's roughly hexagonal cells. That plane is isotropic. The e1,e2 plane is isotropic.
This compares the measured values of the properties versus what we calculated from the honeycomb model. And really, we just used the sorts of equations that we talked about in class over the last couple of lectures, apart from loading in the x3 direction because in the x3 direction, you've got those corrugated walls.
And you have to take those corrugations into account. So there's another complication that I'm not going to go into. But there's a sort of modification you can do to account for that.
But you can see there's actually pretty good agreement here between the elastic moduli that we measured and what we calculated. The compressive strengths down here are not quite so good. They're off by a factor of two, more or less. But they're in the right ballpark for the cork. So those are some of the structures, some of the properties.
One of the interesting things about cork is what it's used for. The uses of cork really exploit the mechanical properties. Obviously, it's used for stoppers for bottles. I brought a champagne cork along with me, and I brought a couple of other little pieces of cork here. I'll pass those around in a minute.
One of the things to look at is just the still wine cork, which is the one on the right, and the champagne cork, which is the one on the left. If you notice the still wine cork is just made of one piece of cork that's cored out from the bark. And if you notice these little channels. These little channels here are called "lenticels." On the still wine cork, they go this way. And on the champagne cork, they go that way. They're oriented perpendicular.
It turns out that they are normal to the isotropic plane in the cork. If you look at the champagne cork, this plane here is the isotropic plane. If you think of that being put into a bottle, I think part of the reason they orient it this way is because it gives you a uniform compression against the neck of the bottle and gives a nice seal. So that's one of the things about corks.
Another thing that's interesting is that cork has a Poisson's ratio equal to zero if you load it in that direction. Let's see. Did I not bring that picture? Maybe I didn't bring that picture. Hang on a sec. Nope. I guess I didn't. Sorry.
I thought I brought a picture where I had the deformation of the cells when you load it in that direction. When you load it-- so say the cells are corrugated this way on. When you load it that way on, it's like having a bellows and folding up a bellows, or unfolding a bellows. So when you load it that way on, there's no expansion or contraction this way on. And so you get zero Poisson's ratio.
And if you think of trying to get the cork into the bottle, it's rather convenient to have zero Poisson's ratio because you don't get as much expansion. As you're pushing it into the bottle, you don't get as much expansion that way out, pressing against it.
In fact, if you compare wine corks with rubber stoppers, this is a kind of typical rubber stopper. Wine corks are always just cylinders. In fact, even the champagne corks are cylinders when they start off. When they put it into the bottle, it's just a straight cylinder.
It gets deformed like that from being in the bottle for some time. They have straight sides and you can just squeeze them. There's these funnel things that wine makers have for putting the cork in the bottle.
You can just squeeze them into the bottle top. You can do that because the Poisson's ratio is zero and because the Young's modulus and the bulk modulus are both small.
But if you look at a rubber stopper, rubber stoppers always have these tapered sides to them. And that's because the Poisson's ratio of the rubber is 0.5. As you squeeze it in, it's trying to move out this way. You couldn't get the stopper in unless it had those tapered sides. So that's sort of an interesting thing about cork.
Let's see. Another application of cork is it's used for gaskets for the same sorts of reasons. It's relatively compliant. It takes up any slack between two pieces that you want to press together.
It's often used for musical instruments that come in pieces. Things like clarinets, there'll be a piece of cork-- you a clarinet player? Yeah? Yeah. One of the interesting things about the clarinet is that, if you can see here at the ends, there's a piece of cork there. And I think there's a piece of cork down there. And the other pieces mate up with that.
The cork provides a seal. And the way the cork is cut, it's cut in such a way that those lenticels go radially out like this, which means that the plane of isotropy and the direction that's got the zero Poisson's ratio is that radial direction.
When you're squeezing, say, the second part onto it, the cork does not expand circumferentially. So as you're squeezing it this way, it doesn't expand that way. It doesn't wrinkle or anything on your other part. They use the cork in a particular orientation for that reason, I think. So it's used for gaskets
It's also used because it's got a good friction property. It's got a property that is taken advantage of in things like flooring and shoes. Cork has a high friction even if it gets wet. Some sources of friction are from adhesion, from a surface effect. Then if, say, the floor gets wet, then you break that, and it could be slippery.
But the source of friction in cork is from an energy loss and dissipation as you're deforming it. Imagine you have a wheel here. The wheel is rotating on this cork floor. And here, a piece of cork is getting deformed as the wheel rolls over it.
As it gets deformed, there's some histeresis loop. Cork has quite a lot of damping in it. There's quite a lot of energy lost in that histeresis loop.
What that means is that's characteristic of the cork itself. It's not a surface effect. That means that if you use it for floors or for shoes, it doesn't lose that friction and damping when it gets wet.
Here's some measurements we did of the coefficient of friction for cork versus doing it dry and doing it with a liquid, soapy surface. You can see the soap doesn't make any difference.
Cork is seen as a very attractive material for things like flooring. It's actually not a cheap material to make your floors out of, but it's an attractive material for flooring. Part of the reason it's used for floors and for the soles of shoes is because of these friction properties.
Another feature of cork is that it's got very small cells compared to a lot of engineering polymers. The cells are on the order of tens of microns, whereas many polymer foams, the cells are hundreds of microns or millimeters.
We'll get into this later, but this plot here is really saying that the thermal conductivity of a cellular material depends, in part, on the cell size. The cell size for foam plastics is in here. And that for cork is down here.
Because it has a smaller cell size, it has a lower thermal conductivity. Cork was at one point used to some extent for thermal insulation. If you go to Portugal, where cork comes from, there's hermit caves. There were these old hermit, religious people who had holed up in a cave. And they would line the caves with cork to try to make it a little more insulated, a little more warm.
The other place you see this is if you look at cigarettes, you know cigarettes have that little brown tip on the part that touches your lips? That's meant to look like cork. And if you look, it has little dots on it. The little dots are the little lenticels. Apparently, they used cork originally in cigarettes as a sort of thermal insulation between the cigarette and your mouth. So it was used for that too.
And then, one final thing. Cork's also used, obviously, for bulletin boards. If you push a pin into cork, then you get this local deformation here. Here's our pin. And here's cells locally deformed. When you pull the pin out, you'll recover some of that deformation because the deformation is elastic. So the hole will partly close.
So that's my little spiel on cork. And that's just because it's interesting. There's no test on cork or anything like that. OK. So are we good with cork? Any questions? We're OK? OK. Let me scoot out of there. Then the next part of the course, I wanted to talk about foams.
Let me just park the cork thing. Let me pass these corks around. So you can play with those too. Oops. There's little bits of cork. There you go. There's the champagne cork, the rubber cork, some little cork layers.
OK. So the next part of the course, I wanted to talk about foams. And I want to talk about how we model the mechanical behavior of foams. If we look at the stress-strain curve for foams, these are some examples for foams made out of different materials with different characteristics.
The polyurethane and the polyethylene here are examples of elastomeric foams, really. This one here is an open-celled foam. This one's a closed-cell foam. Polymethacrylamide is a polymer that has a yield point. Mullite is a ceramic.
You can see the shapes of these curves resemble the shapes that we saw for the honeycombs. Right? They look exactly the same, in fact. And the mechanisms of deformation in the foams are very similar to the honeycombs.
Even though the foams have a much more complicated geometry, we can use some of the ideas from the honeycombs to understand how the foams behave. So that was part of the reason for doing the honeycomb analysis.
Let me back up. These curves here were all in compression. These curves here were all in tension. So again, these ones in tension also look like the curves for the honeycombs. Remember, in tension, we don't get any elastic buckling. So if the foam was made of an elastomer, we don't see any stress plateau.
If the foam is made of material with a yield stress, then we get a very short yield plateau because of a slight geometrical difference between pulling and compressing the foam. And if it's a brittle material, then we just get fracturing. There's going to be some fracture toughness that's going to characterize it.
We can look at the deformation and the failure in these foams and look at the mechanisms. And what we're going to do is model the mechanisms and not worry too much about the cell geometry. So we're going to use dimensional arguments here.
Here's a foam in compression. It was compressed from the top to the bottom. And you can see this strut that's circled in red. This is unloaded. And then, this is after some load. You can see this has bent somewhat.
And then, you can see this vertical strut here. As the load gets larger, you can see that strut's buckled. In an elastomeric foam, you get bending and buckling just the same as we did in the honeycomb.
Then here's a metal foam. You form plastic hinges in the metal foam. So here's a cell wall here. And it's a little bent to start with at zero load. But you can see it becomes more bent in this image over here. And here's a cell wall that's more or less vertical. And you can see that wall buckles. It's a plastic buckling in this case. There's a permanent deformation there.
Here's a brittle foam. And you can see cell walls in this foam fracture. So this region here is equivalent to this region here. That little glitch there is the same as that little glitch there. You can see there's a couple of cell walls here that are fractured. So we get fracture. The idea is is that the mechanisms of deformation in the foams parallel those in the honeycombs. OK?
All right. So let me write some of this stuff on the board. We're going to start off by talking about open-celled foams, so foams where there's just solid in the edges, but not in the faces of the polyhedral cells. Then we'll talk about close-cell foams where there's solid in the faces, as well. But the open-celled ones are easier. So we'll start with that.
In compression, we see the same three regimes as we did before for the honeycombs. There's a linear elastic regime that corresponds to bending of the cell walls. There's a stress plateau.
And for elastomeric foams, that corresponds to buckling. For metal foams, that corresponds to the formation of plastic hinges. And then, for ceramic or brittle foams, that corresponds to brittle crushing, so fracturing of the cell walls.
Then, if you load the foam up to higher strains and higher stresses, eventually you get to densification. And in tension, just like the honeycombs, for the elastomeric materials there is no buckling. We can get a stress plateau from plastic hinges if there's, say, a metal foam.
And for a brittle foam, we would get a fracture toughness and brittle fracture in tension. So the idea is the mechanisms of deformation and failure just parallel what we've seen in the honeycombs.
So we'll start off with the linear elastic behavior. And we'll start with open-cell foams. The initial linear elasticity is due to bending of the cell walls. And if the thickness of the cell edges relative to the length is small, the bending dominates the deformation. But as the thickness to length ratio increases, then axial deformations can become important too.
What we're going to do is we're going to consider dimensional arguments. We're going to set the dimensional arguments up so that we replicate the mechanisms of deformation and failure. But we don't worry too much about the cell geometry.
What I'm going to start with is considering a cubic cell. And I've arranged the cubic cell so that the cell edges are staggered. That's going to give me the bending. The edge length is going to be L. I'm going to say we have a square cross-section, t squared.
Here's our idealized model here with a cubic cell. All the members have a length, l. All of them have a square cross-section, t squared. That's an open-cell model. We've got just solid on the edges and nothing on the faces.
The idea is that if I bend that, or if I load that in compression, so I apply, say, a stress out here that puts forces on those members there, because I've staggered these cell walls with these ones here, we're going to get bending in this cell edge here. That bending is going to be what we model.
I'm going to set this up so that one thing is proportional to something else. These relationships are going to be true regardless of the cell geometry. So I could have picked a tetrakaidecahedra if I wanted to, and I would have had these same relationships. I'm just picking a cubic thing because it's easier to think about.
So first of all, we look at the relative density. Remember, the relative density is the volume fraction of solid. So it's the volume of the solid over the total volume. And that's going to go as t squared l over l cubed, or just t over l all squared.
You remember for the honeycomb, the relative density went linearly with t over l. For the open-celled foam, it goes as t over l squared. The moment of inertia in this case is going to go as t to the fourth.
Remember, we have a square section, t squared. So if it's bh cubed over 12, b is t, h is t. It's going as t to the fourth.
Then what I'm going to say is the stress is going to go as F over an area length squared. OK? So if I look at my little square thing here, I look at having my force here. Here we have a force f. And it's acting over an area that's somehow related to l squared. Right? I don't know exactly what that constant is, and I'm going to not try to calculate that. But it goes as F over l squared.
Similarly, I can write that the strain is going to go as delta over l. So the strain is going to go as this bending deflection here, that delta divided by the height of the cell. And that's also l. Then I also know from structural mechanics that delta is going to go as Fl cubed over E of the solid and I.
Then I'm just going to put all these things together to get the modulus. The modulus of the foam is going to go as the stress over the strain. If I plug in what I have for the stress, it's F over l squared. If I plug in what I have for the strain, it's delta over l.
So this is F over l and delta. I'm going to replace delta by Fl cubed over Es. I'm going to use, instead of I, I'm going to use t to the fourth. Then the F's are going to cancel out. I've got that the modulus goes as the modulus of the solid times t over l to the fourth power. Then I can put that in terms of the relative density. It's going to go as the relative density squared.
So I can summarize all of this by saying that the Young's modulus of the foam is some constant C1, I'm going to call it, times the modulus of the solid times the relative density squared.
OK. So this has the same kind of form as those equations we had for the honeycombs. Right? There's a solid-cell wall property. The solid module's here. For the honeycombs, I put it in terms of t over l. But the t over l was related to the relative density.
How much solid you've got is reflected in the relative density. And then, this constant C1 wraps up all the geometrical constants that I've said, one thing's proportional to another, and something else is proportional to another. C1 just wraps up all of those. OK?
I'm just going to say here C1 includes all the geometrical constants. We have to get C1 by looking at data. If we look at data for the Young's modulus, we find that C1 is just about equal to one.
People have also done more sophisticated analyses than this. There's a group of people who looked at doing a full-scale, structural analysis of an open-celled tetrakaidecahedral cell. Remember, I said they pack to fill space.
So you can look at a unit cell. They also made their cells such that the thickness along the length of the cell was not constant. The thickness varied as something called a "plateau border."
If you have a foam that's made by surface tension, the edges will tend to have these plateau borders. And the thickness will vary along the length of the edge. So when they did all this whole, complicated thing, they could calculate a value for C1. They calculated 0.98. So it's very close to 1.
I'll say analysis of open-cell tetrakaidecahedron cells with these plateau borders give C1 equal to 0.98. OK. So that's the Young's modulus.
We can also look at the shear modulus. The shear modulus is also going to be controlled by bending of the cell walls. And so the shear modulus is just going to be some other constant times Es times the relative density squared, so a similar kind of relationship. It's just a different constant.
And if the foam's isotropic, and if the Poisson's ratio is a third, then C2 is equal to 3/8. Remember, if we have isotropy, then the shear modulus is equal to E over 2 1 plus nu. And so you can get the C2 from that if you say nu is a third.
Then we can also get Poisson's ratio for the foam. If the foam is isotropic, so we'll say for an isotropic foam here, nu is equal to E over 2G minus 1. That's just rearranging this expression here.
And because E and G both depend on the relative density squared, they both depend on Es squared, that's all going to cancel out. So this is going to be equal to C1 over 2 C2 minus 1. So that's going to equal to a constant.
That constant's going to be independent of whatever material the foam is made from and the relative density. The constant just depends on the cell geometry.
Remember, in honeycombs we found the same thing. The Poisson's ratio for the honeycombs only depended on the cell geometry. It didn't depend on the solid properties. It didn't depend on the relative density. So this is an exactly parallel thing here for the foams.
Yeah?
AUDIENCE: I have a silly kind of question. What is the difference between foam and the honeycombs?
LORNA GIBSON: Oh. The honeycombs have cells in a plane, and they're prismatic in the third direction. And the foams have polyhedral cells. You know what a tetrakaidecahedron, a 3D, polyhedral cell. OK? The honeycombs are prismatic. And the foams have polyhedral cells. OK? Are we good? OK.
So there's a couple more interesting things about Poisson's ratio. The same way we can make honeycombs with negative Poisson's ratios, we can also make foams with negative Poisson's ratios.
They do it the same way as for the honeycombs, really. The honeycombs had negative Poisson's ratios if the cell walls looked like this, this sort of arrangement. So that sort of a thing. We said that theta was negative for the honeycombs. And if you invert the cell walls on a foam, you also get negative Poisson's ratios.
And the way they do that is they take a thermoplastic foam, and then, they load it hydrostatically. So they compress it in all three directions. And they smush the cells in on each other.
And then, they heat it up to a temperature above the glass transition temperature while it's still smushed. And then, they cool it down. So they end up with that structure frozen in. And if they do that, they get a negative Poisson's ratio.
I'll just say they invert the cell angles analogous to the honeycomb. They load the foam hydrostatically and heat to a temperature above Tg. And then, they cool and release it.
I have a photograph here of a foam with a negative Poisson's ratio. You can see how the cells have been smushed in. It's the equivalent of the way it's done for the honeycomb. OK? Are we good? OK.
That's the linear elastic moduli for open-celled foams. The next thing I wanted to do was closed-cell foams. If we look at a closed-cell foam, we can idealize it in this kind of a way here. I've set it up so that the edge thickness is different from the face thickness.
That's really representing the fact that in foams, many foams are made using a liquid, and the foaming is controlled by surface tension. Often, the surface tension draws material into the edges and away from the faces. So the faces tend to be thinner than the edges.
When we have deformation of the closed-cell foam, we've got bending of the edges the same as we did for the open-celled foam. But the faces can stretch. So they can have an axial stretching. You can think of that as a cell membrane stretching here. So imagine if I either pull on the foam or I compress it, there's going to be some axial load in the faces.
So when we analyze them, we have to account for both bending of the edges and axial deformation in the faces. I'll just say we have edge bending as in open-cell foams. And we also get a face stretching.
Another thing that can happen in the closed-cell foams is we can get compression of the gas. In an open-cell foam, the gas can move from one cell to the next. But in a closed-cell foam, the gas is trapped. And as the volume of the cell changes, the gas gets compressed. So we have another effect here.
So we'll say for polymer foams, surface tension tends to draw material to the edges during processing.
We define two thicknesses, one for the edge and one for the face. And then we apply a force to this cubic structure. And we can do an analysis a little bit like what we did for the open-cell foam. Let me rub all this off.
OK. I'm going to set this up a little bit differently than for the open-celled foam. We're going to do a work argument. We're going to look at the external work done by the force F going through a deformation, delta. And that's going to have to equal the internal work done by the edges bending and by the faces stretching.
So let me set that up. We're going to say the external work done, that's going to be proportional to F times delta. So delta is how much the whole thing is going to deform. Then, I've got internal work from bending of the edges.
That internal work is going to be proportional to F over delta times delta squared. I'm going to end up with an expression where everything's in delta squared. So I want to keep the delta squared there for now. And F over delta is the stiffness. That's going to go as E of the solid times I over l cubed. I is going to go is Te to the fourth here because it's I of the edges.
I've also got internal work from stretching of the faces. That internal work is going to be-- I'm going to run into my other equations here. Let me put it down a little. That's going to go as the stress on the face times the strain in the face times the volume of the face.
Or I could write that, instead of stress of the face, I can put it in terms of Hooke's law and say it's E of the solid times the strain in the face squared times the volume of the face. And I can replace the strain in the face by delta over l. So it's delta over l squared. And then, the volume of the face is going to be t of the face times l squared.
Then I want to balance the internal work and the external work. I can say F times delta is going to equal some constant I'm going to call "alpha" times E of the solid times t of the edge to the fourth, that's this guy up here, over l cubed times delta squared plus some other constant I'm going to call "beta" times E of the solid times delta over l squared tf l squared.
So far, I've got this in terms of the force I'm applying. But I want to get a modulus of the foam out of this. I want to relate this force here to the modulus of the foam. I can say the modulus of the foam is going to be related to F over l squared, that's the stress, divided by the strain, delta over l.
I can write the force is proportional to the modulus times the deflection, delta, and times the member length, l. And then, I'm going to plug that guy into this expression up here. And I'm going to get a delta squared on the left. And I'm going to get delta squareds in each of the right-hand terms. And so I'm going to cancel out the deltas.
If I put all that together, I have the modulus in the foam times delta squared times l. There's a delta here, and there's a delta there. That gives me delta squared. And that's going to equal alpha Es Te to the fourth over l cubed times delta squared plus beta times Es times delta squared tf, if I cancel out one of those l squareds.
So here I can get rid of the delta squareds in all these terms. And if I just divide by l, I'm going to have the modulus of the foam. I get a term here that it goes as alpha E of the solid times t of the edge over l to the fourth power plus beta times E of the solid times tf over l. Are we good?
OK. And what I'd like to do is instead of putting it in terms of te and tf, I'd like to put it in terms of the relative density. I'm going to look at two limits. I'm going to say if we just had open cells, if there were no faces on the membranes, if we just had open cells, and we had a uniform t, then the relative density would go as t over l squared.
If I just had closed cells, and I had a uniform t, then the relative density just goes linearly with t over l. The relative density is the volume fraction of solids. It's the volume of the solid over the total volume. For a closed-cell foam with a uniform t, the volume of the solid is going to be t times l squared. And then, the volume total is l cubed. So it's t over l.
Now, I'm going to define one more thing. If I say that phi is equal to the volume fraction of the solid in the edges, then I can say te over l is some constant times phi to the 1/2 times the relative density to the 1/2. And I can say tf over l is equal to some other constant, c prime, I'll call it, times 1 minus phi, that's how much is in the faces, times the relative density.
Then I could combine all of this. Can I put it in here? Maybe I'll just stick it down here. Hang on. OK. Put it up here. This is my final expression here. And this term here arises from the edge bending. This term here arises from the face stretching. So I think I should wait a bit for you to catch up.
The idea is the edges are bending. The faces are stretching. We're looking at the work done by deforming the edges and the faces and equating that to the work done by the externally applied load, f. OK?
That gives us two terms, one that accounts for the edge bending, and one that accounts for the face stretching. To be comprehensive, we want to take into account the compression of the gas, as well. So there's one more term I'm going to add on to that.
Typically the gas effect is only significant for elastomeric foams. If you had a metal foam or a ceramic foam that was closed-cell, it wouldn't really contribute much. But just to be complete, we'll go through this.
The idea here is we say we've got a cubic element of the foam. Initially, it has a volume, v0. If we apply a stress, a uniaxial stress, there's some change in the volume of the foam. So there's some volume, v, after we compress it by some strain, epsilon.
If we can figure out what the volume is relative to the initial volume, we can figure out how the change of the amount of gas goes from the initial state to the compressed state. Then we can use Boyle's law.
The idea is P1V1 equals to P2V2. Then we can figure out, using Boyle's law, what the pressure must be. And then, that pressure is what's contributing to the modulus.
When I do this, I'm going to write down some equations that just have the main results. There's a whole bunch of algebra just to get from one to the other. And I'm not going to write them all down. When I write the equations, don't panic if it's not obvious how you get from one to the other. In the notes that I'm going to put online, there's all the details of how you get from one to the other.
The idea is that we start with a cubic element of foam. Initially, before it's loaded, it has a volume V0. Then we apply a uniaxial stress. And we say the axial strain in the direction of the stress, I'm going to call epsilon.
Just from the geometry, you can calculate the deformed volume. So after you load it, the volume is V. And that volume on loading, V, divided by the initial volume, V0, you can show. It's fairly straightforward. It's 1 minus epsilon times 1 minus 2 times the Poisson's ratio of the foam.
Here, I'm taking compressive strain as positive. And if you do this whole volume thing, you'll get terms in epsilon squared and epsilon cubed. But because if it's linear elastic, epsilon is going to be small. I'm going to ignore the epsilon squared and the epsilon cubed terms.
That's the total volume of the foam after and before the compression. And then, what I want is the volume of the gas. And the volume of the gas is just going to be the volume minus the volume of the solid.
And I can get that by just subtracting off the relative density. So Vg over Vg0. Again, Vg0 is the volume of the gas initially. Vg is the volume of the gas when I'm compressing it. Remember, the relative density is the volume fraction of solids. So I'm essentially subtracting out the amount of solid to get the amount of gas.
Then we can use Boyle's law. Here, p is going to be the pressure after the strain and p0 is going to be the initial pressure.
The building seems rather making unhappy noises for some reason. I'm not sure what that's all about.
There'll be some initial pressure in the gas even before the strain, or before the stress is applied. That's p0. So the pressure we need to overcome is p minus p0. Again, I'm missing out a bunch of steps. But using that expression and this expression and this expression, you could find that p prime is equal to p0 times epsilon times 1 minus 2 nu divided by 1 minus epsilon 1 minus 2 nu minus the relative density.
Then the contribution of the gas to the modulus you can get by just taking the derivative of that pressure with respect to the strain. So remember, modulus is stress over strain. It's the same kind of idea.
So I'm going to call it E star g for the contribution from the gas. So that's going to dp prime d epsilon. And that's going to equal p0 times 1 minus 2 nu over 1 minus the relative density. OK? As I said, I'll scan the pages that have the details and put it online.
The final expression we get combines all of these things. The modulus of the foam relative to the solid is phi squared rho over rho s squared plus 1 minus phi, that's the amount of material in the faces, times the relative density and then plus this gas compression term.
Like I said, for most foams, the gas compression is negligible. So if p0 is equal to the atmospheric pressure, so about 0.1 megapascal, then the gas term's negligible, except for elastomeric foams. So that's the Young's modulus.
Then we can do a similar thing for the shear modulus. And the thing to notice in shear is that when you shear something, there's no volume change. So if you shear it and there's no volume change, there's no gas compression. There's no pressure built up because there's no change in the volume. So for the shear modulus, you just have the first two terms.
And if the foam is isotropic and you use a third, then this constant here is going to be 3/8. And then, Poisson's ratio is just going to be a function of the cell geometry, again. And roughly, we could say it's going to be around a third.
OK. Are we good? Let me wait a little bit.
So the idea is we're looking at the deformation of the bending in the cell edges, and the stretching in the cell faces, and the gas compression. And we're accounting for those different terms.
The next thing is to compare these model equations with some data. And here's data for Young's modulus. Here, we're plotting the relative Young's modulus, so the modulus of the foam divided by the solid against the relative density. Again, these are log-log scales.
On this plot, everything with open symbols is an open-cell foam, and everything with filled symbols is a closed-cell foam. Here's our equation for the open-celled foams, the simplest thing that goes with density squared.
And that's that thick line there. And you can see these are all open-cell foams. There's some more up here. So that gives a reasonable description of that data.
And then, these are two lines for closed-cell foams for different values of phi, so different values of the amount of solid in the edges. And you can see all the filled symbols are the closed-cell foams. And they're in between this line here and this line here, basically.
So that gives a fairly good description for the modulus of the foams considering how crude this model is. We're not trying to account for the cell geometry. We're just modeling the mechanisms of deformation and failure.
And then, here's a similar plot for the shear modulus. Here's for open-cells, 3/8 times the relative density squared. These are open-celled foams down here. These are closed-cell foams up here. If the amount of material in the faces is small, then you would just get the shear modulus varying with the relative density squared.
Then here's data for Poisson's ratio. We don't really know what the constant is because we don't know what all these geometrical parameters are. But here's a value of a third. And you can see there's a lot of scatter here. This is like less than 0.2. This is more than 0.5.
And the scatter really represents differences in the cell geometry. If the foams were, say, anisotropic, and the cells were stretched in one direction, then you would get different values of the Poisson's ratios. So that's the Poisson's ratios there.
I'm thinking I'm going to stop there because that seems like enough equations for today. And then, next time we'll start doing the stress plateau and we'll figure out the elastic collapse stress from buckling and a plastic collapse stress from yielding, and so on, and so on.
We'll finish doing the modeling next time. And we'll probably start doing a little bit of other stuff on foams next time.
Free Downloads
Video
- iTunes U (MP4 - 148MB)
- Internet Archive (MP4 - 148MB)
Subtitle
- English - US (SRT)