Flash and JavaScript are required for this feature.
Download the video from iTunes U or the Internet Archive.
Description: This session covers various ways of processing foams including metal, carbon, ceramics and glass foams, and the structure of cellular materials.
Instructor: Lorna Gibson
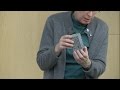
Lecture 2: Processing of Ce...
The following content is provided under a Creative Commons license. Your support will help MIT OpenCourseWare continue to offer high quality educational resources for free. To make a donation or view additional materials from hundreds of MIT courses, visit MIT OpenCourseWare at ocw.mit.edu.
LORNA GIBSON: I think, last time, we got as far as talking about processing of foams and we talked a bit about processing of polymer foams. And today, I want to pick up where we left off. And I was going to talk about processing metal foams. We'll talk a little bit about carbon foams, ceramic foams, and glass foams.
We'll finish this section on processing today and then we'll start talking about the structure of cellular materials. And hopefully-- we won't finish that today, but we'll finish it the start of tomorrow's lecture. And then, we'll start doing mechanics of honeycombs tomorrow. OK? So that's the scheme.
I thought what I'd do-- I have a whole series of slides that show, schematically, a variety of different processes for making metal foams. So I thought I would just go through the slides- and I think I did this really quickly last time-- but I would write down a little bit of notes on each of the slides so that you've got some notes on it, too. This is the first method here. And many of these methods were developed for aluminum foams. But you could, in principle, use them for other types of foams, as well.
This first method here-- let me see if I can get my little pointer. [INAUDIBLE] The idea here is that you take molten aluminum. Down in this bath here, you've got molten aluminum.
And they put, into the aluminum, silicon carbide particles. And the silicon carbide particles adjust the viscosity of the melt. They make it more viscous.
And then they just have a-- I've got this thing here-- they've got a tube here that they blow gas in with. And if you go to the bottom of the tube, there's an impeller, or a little paddle, that stirs the gas up. And so the gas just forms in the molten aluminum here. And then they have conveyors which pull off the molt-- or the metal foam, and then it cools.
The idea is that if you just had the aluminum, you couldn't really do this because the bubbles would collapse before they cooled down and became a solid. But adding the silicon carbide particles increases the viscosity of the melt. It helps prevent drainage of the foam. Normally, if you have a liquid foam, just from gravity, you're going to have some drainage. It's going to tend to-- some of the liquid is going to tend to sink, just from gravity.
By putting the silicon carbide particles in, you increase the viscosity. It helps prevent the drainage. And you can get the foam bubbles to be stable.
Let me just write one little note here. The first method here involves just bubbling gas into the molten aluminum. And that molten aluminum is stabilized by silicon carbide particles. Sometimes people use aluminum particles and the particles increase the viscosity of the melt. And that reduces the drainage and it stabilizes the foam.
That process was developed at Alcan in Canada and at Norsk Hydro in Norway. And this foam here is an example of the foam that they've made. And you can kind of see-- there's a density gradient in this foam. I'll pass it around. You can see it.
But the bubbles are smaller down here and there's fewer of them than there are up here. And that's partly from the drainage. The molten aluminum is draining down and you get more liquid at the bottom and then you get more solid at the bottom. So that's the Alcan foam.
OK. Another-- there's half a dozen of these processes for metal foams. Another version of the process involves taking metal powder and combining it with titanium hydride powder. And then you consolidate it and you heat it. So if I can show through the schematics here.
In the first step, you take the two powders, you mix them up. So the second thing down here is mixing the powders up. And then you press them together. There's a dye here that you press it, and then you get pieces. And then you can heat that up.
And the way that this works is that the titanium hydride decomposes at a temperature of about 300 degrees C. And if the other powder is something like aluminum-- aluminum melts at something like 660 degrees C-- the aluminum has become soft at 300 degrees C, but it's not molten. And the titanium hydride-- when it decomposes-- forms hydrogen gas. So the hydrogen gas forms the bubbles that you need to make the foam.
Are you riding your bicycle? You are tough. Very tough. I ride my bike, but I gave up a couple weeks ago. Well, three weeks ago, I guess. When it started snowing, I gave up.
The idea with this process is you can use titanium hydride powder with aluminum and the aluminum becomes soft at the temperature that the titanium hydro decomposes. And when it forms the hydrogen gas, that gives you the bubbles, and so you get the foam made by that process. And that was developed by a place called Fraunhofer. And I have one of their little foams here. This is an example of their foam made by that powder metallurgy process there.
OK. Let me just write a little note about that. So you can mix up titanium hydride powder with a metal powder and then heat that up.
When you do this, you need to have a metal powder that's going to be deforming by, say, high temperature creep at the temperature that the decomposition of the titanium hydride happens. And for aluminum, that works. So you need to have the metal material be able to deform fairly easily, in order to get these bubbles to form a nice foam. But that's another way you can do it, is by consolidating these two powders.
Here's another way to do it. You can also make use of this property of the titanium hydride-- that it'll decompose and form hydrogen gas-- by just putting it into molten aluminum. And in this example here, you've got an aluminum melt in here.
And this time, they've added 2% calcium to it. Again, to adjust the viscosity. And then they add the titanium hydride in this step here and they've got a little mixer thing here that's spinning around and will mix it. And then they'll put a lid on it to control the pressure and the titanium hydride will decompose, the hydrogen gas will evolve, and you'll get the foam made by that method, too. So you can stir titanium hide right into a molten metal, as well.
OK. So that's another method. And I think that was made by something called the Alporas process. And this is an example of one of their foams. I'm pretty sure that's an Alporas foam there. Yep.
AUDIENCE: [INAUDIBLE]
LORNA GIBSON: They can't really control it perfectly. In that first example that's going around-- maybe you might have missed it-- there's this drainage. The first one's made by a molten process and you get drainage.
And you get different sized bubbles. And you get different-- you get a density gradient in the thing, as well. So you can't control these things perfectly.
OK. Here's another method for the metal foams. This one here involves replication. In this method here, what you do is you start out with an open-cell polymer foam. In this step up here, there's an open-cell polymer foam. You fill that with sand. So you fill up all the open parts of the cells with sand.
Then you burn off the polymer. And so you've got a little channels where the polymer used to be. And then you infiltrate those channels with the molten metal that you want to use. So you replicate the polymer foam structure.
This is the infiltration process here. This little thing here is your furnace. And then you get rid of the sand and then you're left with a metal replica of the-- a replica of the original polymer foam. And this example here is one of these things that's made by this replication process. So that's an open-celled aluminum.
I think the-- if you look at the density of these things, they're fairly low. And so there's quite a large volume of pores and they're all interconnected. So it's not that hard to get the sand out.
This method would involve replication of the open-cell foam-- the polymer foam-- by casting. So you fill the open-cell polymer foam with sand. You burn off the polymer. And then you infiltrate the metal into that. And then you remove the sand. OK?
Then, another process involves just using vapor depositions. So you take an open-cell polymer foam again. Here-- let me use my little arrow. Here's the open-cell polymer foam up here. And you have a furnace here with a vapor deposition system. And they use a nickel CO4 system to do this.
You then burn out the polymer. You're left with a metal foam with hollow cell walls, where the polymer used to be. And then usually, what they do is they center it. They heat it up again to try to densify the walls.
The only teeny weeny problem with this process is that the gas they use this incredibly toxic. And so it's not cheap and it's got health hazards, as well, associated with it. But you can do it. That gives you a nickel foam when you're finished with that. And you could also use an electrodeposition technique that's similar.
OK. That's another method. Another method is shown here.
This is the entrapped gas expansion method. And what they do in this method is they have a can and the can has a metal powder in it. It's whatever metal you want to make the foam out of. In this example here-- it's probably too small for you to read in the seats-- but it's titanium. They've taken a titanium alloy.
They've got a powder of titanium alloy. They then evacuate the can. They take all the air out of it. And then they back fill it with argon gas. They put in an inert gas in there.
And then what they do is they pressurize and heat the thing up and so the gas is internally pressurized by doing that. And then, sometimes when they do this, they want to have a skin on the two faces. So in this next little image here, it's done where they roll the can and produce a panel that's got solid faces.
And then when you heat it up, the gas expands and you end up with a sandwich panel by doing this. So this bottom figure down here-- I'm not having much luck with the pointer. This bottom figure down here, they've heated it up. The gas expands and you've got this solid skin on the thing, which is from where the can use to be. So that's trapping of a gas.
OK? There's a couple more methods for the metal foams. One involves centering hollow metal spheres together. And the trick there is to make the hollow spheres.
And the way that can be done is by taking titanium hydride again, if you want to make titanium spheres. You put it in an organic binder-- in a solvent-- so you've got a slurry here. And you've got a tube that you blow gas through.
And as you do that, you get hollow titanium hydride bubbles. And then you can do the same thing where you heat that up. The hydrogen gas evolves off, and you're left with titanium.
You're left with titanium spheres down at the bottom here. And then you can pack those together and press those and form a cellular material that way. You can also center hollow metal spheres.
And the last method I've got for the metal foams is that you can use a fugitive phase. With the fugitive phase, you would take some material that you could get rid of at the end of the process. Say, something like salt, that you could leach out.
Here, we have our bed filled with salt. And then you would infiltrate that with a liquid metal, typically under pressure. And then, after the metals cooled, you leech out the salt. You get rid of that. You can pressure infiltrate a leachable bed of particles, and then leach the particles out.
OK. We have a whole variety of methods that have been developed to make metal foams. And most of these have been developed, probably, in the last 20 years. Something like that. Some of them are a little bit older than that. But there's been a lot of interest in this recently.
Those are all methods to make metal foams. I wanted to talk just a little bit about a few other types of foams. People make carbon foams. And they use the same kind of method as they do to make those bio carbon templates I told you about.
When you take wood and you heat it up in an inert atmosphere and it turns into a carbon template, you can do the same thing where you take a polymer foam, you heat it up in an inert atmosphere, and everything except the carbon is driven off. And you're left with a carbon foam. It's the same process they used to make carbon fibers. There's carbon foams.
There's also ceramic foams that you can make. I brought the little sample of ceramic foaming again. You can pass that around.
And those are typically made by taking an open-cell polymer foam and passing a ceramic slurry through the polymer foam so that you coat the cell walls. And then you fire it so that you bond the ceramic together and you burn the polymer off. And you're left with a foam that's got hollow cell walls. You can also make ceramic foams by doing a CVD process on the carbon foam that you could make by the previous process.
And people also make glass foams. And to make glass foams, they use some of the same kinds of processes as people use for polymer foams. I'll just say similar processes to polymer foams.
OK. That covers making the foams, and I think we talked about the honeycombs last time. I wanted to talk a little bit about making what are called 3D lattice materials, or 3D truss materials, as well.
Let me [? strip ?] that up there. Yeah?
AUDIENCE: [INAUDIBLE]
LORNA GIBSON: Chemical vapor deposition.
AUDIENCE: [INAUDIBLE] use this for metal foams?
LORNA GIBSON: Well, people were quite interested in using them for sandwich panels-- the cores of sandwich panels-- lightweight panels. There was interest in using them for energy absorption, say, car bumpers. The automotive industry was quite interested in this, in terms of trying to make components with sandwich structures that would be lighter weight, or energy absorption for bumpers. Or filling up-- if you take-- say you take a metal tube. If you think of a car chassis and it's made of tubes, if you fill those tubes with a foam-- especially if you fill them with a metal foam-- you can increase the energy absorption quite substantially.
So when you have a tube in a chassis, if it's loaded axially, it will fold up and you get all these wavelengths of buckling. And if you've put a foam in there, it changes the buckling wavelength and it increases the amount of energy you can absorb. So not only is the energy absorbed by the foam itself, it actually changes the buckling of the tube so you can absorb more energy. So there was a lot of interest in that.
There was an interest in using them for cooling devices for, say, electronic components. The idea was you would take, say, an aluminium open-cell foam and you would flow air through that. And say you have your device that's generating heat, you'd have a foam underneath it.
And the aluminum conducts the heat fairly well. And then you would blow air through it to try to cool it off. So there were a bunch of different applications people have had in mind for them.
AUDIENCE: What about glass?
LORNA GIBSON: Glass foams, I think, are largely used for insulation in buildings, believe it or not. I think, actually, one of the dorms at MIT-- maybe the Simmons dorm-- has a glass foam insulation.
AUDIENCE: [INAUDIBLE]
LORNA GIBSON: Well, I think because the foam-- because the cells are closed, the gas is trapped in the cell. Whereas with a fiberglass, gas could move through the fibers more easily. So I think that's partly how it works.
OK. Well, let me talk a little bit about the lattice materials, too, and how we make those. We're going to start talking about the modeling of honeycombs and foams. And when we do that, we're going to see that if we have a structure that deforms by bending, the properties vary with the amount of material, in a certain way. But if we have materials where the deformation is controlled by axial deformation, the stiffness and the strength are going to be higher at the same density.
People made these lattice-type materials to try to get something with a more regular structure, and especially a triangulated structure. You see how these things are like little trusses? Triangulated?
Triangulated structures, when you load them-- say I load this like this-- there's just axial components-- axial forces in each of the members. And so, theoretically, this would be higher stiffness and strength for a given weight than, say, a foam would be. So people were interested in these lattice material. This one here is made of aluminum.
And I wanted to talk a little bit about how you can make these things. One way you can do it is by injection molding. And this here is just the centerpiece of something that would look like this.
So there would be a-- I didn't bring it, but there's a top face and a bottom face that fit onto this. And they would be injection molded as three different pieces, and then assembled together. So you can make a mold in this complicated geometry, and you can make a lattice material by injection molding.
We'll start with polymer lattices first. One way is injection molding. Another way to do it is by 3-D printing. You can generate a structure like that by 3-D printing. You can also make trusses in 2D and you can make them so that you can snap fit those together.
So you can make little 2D trusses. Here's a little truss here and here's a little piece of a truss here. And you can make a little snap fit joints.
Do you see how these ones have little divots in them? And you can make it so that these things will fit together. I think these guys-- can I do it? No. You'd have to take-- oops.
Wait a minute. No, it's not that way. There we go.
So you can snap them together like that. OK. I can't get it to-- there we go.
So you can do that. And you do that over and over again. And if you do it over and over again, you get something that looks like that. OK? You can make a snap fit thing.
Let me pass all these guys around and you can play with those. That's the injection molding one. This is the snap-fit one. Got that?
Let's see. I think I have a little picture here. This is an example of the snap fit truss here. It's the thing that's getting passed around.
And another clever way that was developed was by taking a monomer that's sensitive to light. You take a photo sensitive monomer. And you put a mask on top of it and the mask has holes in it.
And then you shine collimated light on it. You shine, say, a laser on it. And the light goes through the holes in the mask. And it starts to polymerize the polymer because it's photosensitive. And then, as the polymer-- as it polymerizes and becomes solid, it then acts as a waveguide and draws the light down deeper into the monomer.
And so the polymer acts as a wave guide. It brings the light down. And this is a schematic over here. This is a schematic showing the set up. And these are some examples of some 3D trusses that they've made using this technique.
And one of the nice things about this is you can get a very small size cell size. So this is-- I think that bar-- it says 1,500 microns. That's what? One and a half millimeters. So you can get a nice, small cell size if you want that. Let me write that down.
You take a photosensitive monomer and then you have it in a mold beneath a mask. And then you shine collimated light on it. And as the light shines on it, it polymerizes the monomer. So then it solidifies and then it guides the light deeper into the monomer.
OK. That's that. And then finally, there's metal lattices, as well.
And so this is, obviously, a metal lattice here. It's an aluminum alloy. And the metal lattice is made by taking that polymer lattice that was made by the injection molding technique. You coat that with a ceramic slurry. You burn off the polymer, and then you infiltrate the metal where the polymer used to be.
OK. That's the section on processing of the honeycombs and the foams and the lattices. So there's a variety of different techniques that people have developed for making these kinds of materials. And I thought it'd be useful to just describe some of the techniques.
As I think I said last time, this isn't comprehensive. This doesn't cover every technique. But it gives you a flavor of what techniques people have developed for making these kinds of materials. OK? Are we good? We're good. OK.
The next part, I want to do on the structure of cellular materials. And I have a little overview. I don't think we'll finish this today, but we'll finish it tomorrow. Yeah?
AUDIENCE: [INAUDIBLE]
LORNA GIBSON: Down here?
AUDIENCE: What happens to the ceramic?
LORNA GIBSON: They get rid of the ceramic. Typically, the ceramic is not very strong and it's just fired enough so they can infiltrate it with the metal. And then they-- yeah, I think with mechanical smushing around, you can get rid of the ceramic. And the ceramic's brittle, so if you break the ceramic, you're not going to break the metal.
AUDIENCE: I'm wondering if you could make a type of metal lattice [INAUDIBLE] with reducing [? the ?] oxides?
LORNA GIBSON: I guess you could, if you could-- but you'd have to then make the oxide in that shape, too. You've always got to make something in that shape.
AUDIENCE: [INAUDIBLE]
LORNA GIBSON: Yeah, maybe you could make a foam. But to make these lattices, you need this really regular kind of structure and be able to control the structure. OK. Let me scoot out of this set of slides and get the next set up. OK.
We want to talk about the structure of cellular solids. And we classify cellular materials into two main groups. One's called honeycombs. This thing down here is a honeycomb.
And honeycombs have polygonal cells that fill a plane and then they're prismatic in the third direction. So you can think of them as just being a prismatic-- and they can be hexagons, they can be squares, they can be triangles-- but you can think of them as prismatic cells. And the cells are just in a 2D plane.
And then we also have foams. All of these ones over here are foamed materials. And they're made up of polyhedral cells. The cells themselves are three-dimensional polyhedra. And this slide here shows a number of different types of foams.
These ones are polymers up here. These are two metals. These are two ceramics. This is a glass foam down here. And this is another polymer foam down here. OK?
AUDIENCE: [INAUDIBLE]
LORNA GIBSON: No. I just know that.
AUDIENCE: OK.
LORNA GIBSON: I took those pictures so I know that. No, you can't tell by looking at them. In fact, that's one of the things about how we model the cellular materials. The fact that their structure is so similar is what gives them similar properties. And they behave in similar ways because they've got similar structures.
OK. We've got 2D honeycombs, where we have polygonal cells that pack to fill a plane. And then they're prismatic in the third direction. And then we have what we call 3D cellular materials, which are foams, which have polyhedral cells. And then they pack to fill space.
The properties of all of these materials depend, essentially, on three things. They're going to depend on the solid that you make it from. If you make the material from a rubber or from an aluminum, you're going to get different properties. So they depend on the properties of the solid.
And some of the properties that we're going to use that are important for this type of modeling are a density of the solid-- which I'm going to call rho s-- a Young's modulus of the solid-- which I'm going to call es-- and some sort of strength of the solid-- which I'm going to call sigma ys for now. And you could think of other things. There could be a fractured toughness of the solid. There could be other kinds of things.
One thing that the properties of the cellular material depend on is the properties of the solid. Another is the relative density of the cellular material. And that's the density of the cellular thing divided by the density of the solid. And that's equivalent to the volume fraction of solids.
So it makes sense that the more solid you've got, the stiffer and stronger the material's going to be. So it's going to depend on how much material you've got. And it also depends-- the properties also depend on the cell geometry.
The cell shape can control things like whether or not the honeycomb or the foam is isotropic or anisotropic. You can imagine, if you have a foam, and you've got equiaxed cells, you might expect to have the same properties in all directions. But if you had cells that were elongated in some way, you might expect you'd have different properties in the direction that they're elongated relative to the other plane. So cell shape can lead to anisotropy.
For the foams, you can also have what we call open-cell and closed-cell foams. If you look at this slide here, and we look at this top right images-- these two up here-- the one on the left in the top is an open-celled foam. There's just material in the edges. There's no faces. And so a gas can flow between one cell and another.
And then if you look at the one on the right, this is a closed-celled foam. There's faces. If you think of the polyhedra, you've got solid faces covering the faces of the polyhedra.
For an open-cell foam, you've only got solid in the edges of the polyhedra. And the voids are continuous, so they're connected together. And for a closed-cell foam, you've got solid in the edges and the faces. And then the voids are separated off from each other. So we'll say, the cells are closed off from one another.
Another feature of the cell geometry is the cell size. And the cell size can be important for things like the thermal properties of foams. It's important for things like the surface area per unit volume. But typically, for the mechanical properties, it's not that important. And we'll see why that is when we do the modeling.
OK. Yes?
AUDIENCE: For the closed-cell foams-- because we can't really see it without cutting it, is it that all of the faces are closed? Or is it like some fraction of the faces are closed?
LORNA GIBSON: If you look at this one on the top right here, they're pretty much all closed. But the reason we have this little picture down here is some of them are closed and some of them are open. So you can get ones that are in between. But typically-- this is kind of unusual. Usually, they're either all open or all closed.
If we look at the mechanical properties of cellular materials, typically the cell geometry doesn't have that much of an effect. The relative density is much more important. The relative density, we define as the density of the cellular solid.
And when I use a parameter like rho or e or something, if it's got a star, it's for the cellular thing and if it's got an s, it's for the solid. So rho star is going to be the density of the cellular material. And rho s is going to be the density of the solid it's made from. And so the relative density is just rho star over rho s. And I just wanted to show you how this is the volume fraction of solids.
So rho star is going to be the mass of solid over the total volume. Imagine you've got a honeycomb or a foam and you've got, say, a unit cube of it, the sum total volume of the whole thing-- the density of the cellular material is going to the mass of the solid over the whole volume. The density of the solid is going to be the mass of the solid over the volume of the solid. This is really just equivalent to the volume fraction of solids, how much solids you've got. And that's also n equal to 1 minus the porosity.
Typical values for cellular materials-- I think last time I passed around one of those collagen scaffolds-- those tissue enineering scaffolds. It was in a little plastic bag. That collagen scaffold has a relative density of 0.005, so its 0.5% solid and 99.5% air. And if we look at typical polymer foams, the relative density is typically between about 2% and 20%.
And if we look at something like softwoods-- wood is a cellular material. And we look at softwoods, the relative density is usually between about 15% and about 40%. Something like that. OK? As the relative density increases, you get more material on the cell edges, and if it's closed-cell foam, on the cell faces. And the pore volume decreases.
And you can think of some limit. If you keep increasing the relative density more and more and more, eventually you've got-- it's not really a cellular material anymore. It's more like a solid with little isolated pores in it.
And so there's two bounds. And the density has to be less than a certain amount for you to consider it a cellular material in the models that we're going to derive to be valid. And if the relevant density is more than a certain amount, people model it as a solid with isolated holes.
If I have a unit square of material, if it's a cellular material, you might expect that you've got pores that would look like this. And you've got relatively thin cell walls, relative to the length of the material. And for a cellular material, typically, the relative density is less than about 0.3.
And when we come to the modeling for the honeycombs and the foams, we're going to see that the cell walls deform, in many cases, by bending. And that you can model the deformation by modeling the bending. And that the bending dominates the behavior if the density is less than about that.
And at the other extreme, you can imagine if you had just little teeny pores. I have a little pore here and one here and one there and one there. That's not really a cellular material. It's just got a teeny weeny little bit of pores. And that could be modeled as isolated pores in a solid. Each one is acting independently.
And people have found that that is appropriate if the relative density is greater than about 0.8. And then, in between, there's a transition in behavior between the cellular solid and the isolated pores in the solid. OK? Are we OK?
The next thing I wanted to talk about was unit cells. Especially for honeycombs, people often use unit cells. A hexagonal cell is an obvious one to use to model this kind of behavior.
For honeycomb materials, you can have unit cells and you can have different ones. On the left here, we've got triangles, in the middle, I've got squares. On the right-hand side, I've got hexagons.
And you can see, even if you have a certain unit cell, there's also different ways to stack it. So the number of edges that meet at a vertex is different for, say, this example on the top left and this example on the bottom left. Here, we've got six members coming into each vertex, and here, we've got four. And again, this stacking for the two square cells is also different. So you can have different numbers of edges per vertex.
Another thing to note that's kind of interesting-- if you look at the honeycomb cells here, this one on the top left-- this equilateral triangle one with the stacking-- and this one on the top right-- the regular hexagonal cells-- those two are isotropic for linear elastic behavior, whereas all the other ones are not. So we have 2D honeycomb unit cells. We can have triangles, squares, and hexagons. They can be stacked in more than one way. And that gives different numbers of edges per vertex.
And in that figure, a and e are isotropic, for linear elasticity.
OK. When we come to modeling the honeycombs, we're going to focus on the hexagonal cells. We'll talk a little bit about the square and triangular cells, as well. And then, for foams, when you look at the structure of a foam, it's obviously not a unit cell that repeats over and over again. But people started off trying to model the mechanical behavior of foams by looking at periodic repeating polyhedral cells.
And there's three cells here that are prismatic. We're not really going to talk about those beyond this. So they're not really physically realistic or interesting.
But people would use these two cells here in initial attempts to model foams. And this one here is called the rhombic dodecahedra. Rhombic because each of the faces has four sides and dodecahedra because each polyhedra has 12 faces.
I forget if I've bored you with my Latin already. Hedron means face in-- oh, this is Greek, I think. Hedron means face. Do is two, deca is 10. So dodeca is two plus 10. It's got 12 faces. OK?
So that's the rhombic dodecahedra over here. And then this bottom one down here is a tetrakaidecahedra. It's a similar thing. Tetra's four, kai mean and. Four and 10-- tetra kai deca-- it's got 14 faces.
OK? And those two pack to fill space. I think those are the only uniform polyhedra that pack to fill space.
Here is the 3D foams. We have the rhombic dodecahedron and the tetrakaidecahedron. And the tetrakaidecahedron packs in a bcc packing.
Initial models for foams-- they took these two unit cells. And what they would do is have an infinite array of them to make up the whole material. And then they would isolate a unit cell.
And they would apply loads-- some say compressive stress, for example. And then they would figure out what the load, or force, was in every single member, and how much that member deformed. And they would figure out the component of the deformation in the same direction that they were putting the load on. And they would figure out things like a Young's modulus, or they would figure out when there was some failure of one of these struts, and they would figure out a strength for the foam.
But you can kind of imagine, geometrically, not that easy to keep straight. A little bit complicated. So one way to model foams is by using these unit cells. But we're going to talk about a different way to do it, as well. OK. So those are unit cells.
When they make foams, as we just talked about, one way to make a foam is by blowing a gas into a liquid. And if you blow a gas into a liquid, then the surface tension is going to have an effect on the cell geometry and on the shape of the cells. And if the surface tension is isotropic-- if it's the same in all directions-- then the structure that you get is one that minimizes the surface area per unit volume.
And so people were interested in what sort of cell shape minimizes the surface area per unit volume. And Lord Kelvin, in the 1800s, was the person who worked this out. And this is called the Kelvin tetrakaidecahedron.
And it's not just a straight tetrakaidecahedron. There's a slight curvature to the cells here, to the faces. And you can kind of see it in some of the edges here. Like if we-- let me get my little pointer.
If you look at that edge, it's not straight. This edge here is not straight. It's got a little bit of a curvature to it. But this minimizes the surface area per unit volume.
And then more recently, in the 1990's, there were two people-- Dennis Weaire and Robert Phelan-- discovered that this structure here-- which isn't a single polyhedron, but it's made up of a few polyhedra. That has a slightly smaller surface area per unit volume. Smaller by 0.3%. So, a tiny bit smaller.
OK. Let's see. What I'll say here is that foams are often made by blowing a gas into a liquid. And if the surface tension controls and it's isotropic, then the structure will minimize the surface area per unit volume.
OK. That's relevant if the foam is made by blowing a gas into a liquid and surface tension is the controlling factor. Sometimes foams are made by supersaturating a liquid with a gas, and then you nucleate bubbles, and then the bubbles grow. So there's a nucleation and growth process. So that's a little bit different.
And if you have a nucleation and growth process, you get a structure that is similar to something called a Voronoi structure. In an idealized case, imagine that you have random points that are nucleation points and that you start to grow bubbles at those nucleation points. So you start off with these random points.
And the bubbles all start to grow at the same time and they all grow at the same linear rate. If you have that situation, then you end up with this Voronoi kind of structure. And I've shown a 2D version of it here just because it's easier to see in 2D, but you can imagine a 3D system.
And in order to make one of these Voronoi honeycombs, you can imagine-- if you have random points-- here, say that little point there is one of the nucleation points, and here's another point here-- you form the structure by drawing the perpendicular bisectors between each pair of points. This is the bisector between these two points. Here's a bisector between those two points. And then you form the envelope of those lines around each nucleation point. And that, then, gives you that structure.
And you can see, this structure here is kind of angular. It doesn't look that representative of something like a foam. But if you have an exclusion distance, where you say that you're not going to allow the nucleation points to be closer than some given distance-- your exclusion distance-- then you get this structure here.
And this starts to look a lot more like a foamy kind of structure. So these Voronoi structures are representative of structures that are related to nucleation and growth of the bubbles, or nucleation and growth processes. Let me write down something about Voronoi things.
And these Voronoi structures were first developed to look at grain growth in metals. They weren't developed for cellular materials. But you can use them to model cellular materials, as well, as long as it's a nucleation and growth process.
We'll say that foams are sometimes made by supersaturating a liquid with a gas, and then reducing the pressure so that the bubbles nucleate and grow. So initially, the bubbles are going to form spheres. But as the spheres grow, they start to intersect with each other and form polyhedral cells.
And you get the Voronoi structure by thinking about an idealized case in which you randomly nucleate the-- you have nucleation points at a randomly distributed space. They start to grow at the same time and they grow at the same linear rate.
OK. The Voronoi honeycomb, or the foam-- you can form that by drawing the perpendicular bisectors between the random points. So each cell contains the points that are closer to the nucleation point than any other point-- or any other nucleation point.
And if we just do this process as I've described here, you end up with a Voronoi structure, where the cells appear kind of angular. And if you specify an exclusion distance, where you say the nucleation points can't be closer than a certain distance, then the cells become less angular, and of more similar size.
OK. So are we good with the Voronoi honeycomb nucleation and growth idea? Alrighty.
All right. If we think about cell shape-- if we start with honeycombs and we just think about it hexagonal honeycombs, if I have a regular hexagonal honeycomb so that all the edges are the same length and this angle here is 30 degrees, then that is an isotropic material in the plane in the linear elastic regime. One of the things we're going to do is calculate-- if I loan it this way on, what's the Young's modulus? If I load it that way on, what's the Young's modulus?
And we're going to find they're the same, in fact, no matter which way on I loaded it. It would be the same. But if I now have my honeycomb, and imagine that I stretched it out-- and I'm kind of exaggerating how much we might stretch it out. But if we did something like that, it wouldn't be too surprising to think that the properties are going to be different if I loaded it this way on and that way on.
And in terms of the cell geometry, I'm going to call that vertical cell edge length h. And I'm going to call this one-- the inclined one-- of length l. I'm going to say that angle is the angle theta. And the cell shape can be defined by the ratio of h over l and that angle theta.
OK. When we derive equations for the mechanical properties of the honeycombs, we're going to find that they depend on some solid properties. Say, the modulus of the honeycombs can depend on the modulus of the solid. It's going to depend on the relative density raised to some power.
And we're going to figure out what that is. And then it's going to depend, also, on some function of h over l and theta. And that function really represents the contribution of the cell geometry to the mechanical properties.
OK. That's the honeycombs. It's fairly straightforward to characterize the shell shape for the honeycombs. It's a little more involved to do it for the foams.
And the technique that's used is called the mean intercept length. At least, that's one technique that's used. Let me wait until you've finished writing because I want you to see the picture as I talk about it. OK?
OK. Here's-- whoops. My pointer keeps disappearing. This top left picture here shows an SEM image of a foam. And you can see, you've got some big cells and little cells and there's no obvious way to characterize the cell shape.
And what people do to calculate this mean intercept length is they would take an image. They would then sketch out just the cell edges that touch a plane's surface. So all these black lines are just the-- if you took your-- if you put ink on your foam and you just put it on a pad and put it on a piece of paper, you would get this outline of the edges of the cells, where they intersect that plane.
And then what people do is they draw test circles. Here's the test circle here. And they draw parallel equiaxed, or equidistant lines. So the lines here are parallel. They're all at, say, zero degrees. And they're all the same distance apart.
And then they count the number of intercepts. They count-- say we went out here. The cell wall intercepts here. There's one that intercepts here. And then, it'd go up here. Here's another intercept. Here's another intercept.
So they count the number of intercepts of the cell wall with the lines. And then they get a mean intercept length, which is characteristic of the cell dimension. And then what they do-- because this is just in one orientation-- you would then rotate those parallel lines by, say, 5 degrees and do it all over again. And get another length at 5 degrees and one at 10 degrees one at 15. And so you get different lengths for the intercepts as you rotate your parallel lines around.
And then you make a polar plot, and that's what the thing is down at the bottom here. And so you plot your mean intercept length as a function of the angle that you measured it at. And you can fit it to an ellipse.
And if you do it in three dimensions, you fit it to an ellipsoid. And the major and minor axes of that ellipse, or ellipsoid, are characteristic of how elongated the cell is in the different directions. And the orientation of that ellipsoid is characteristic of the orientation of the cells.
Those of you who took 303, too, you remember Mohr's circles? Is this beginning to look familiar? It's the same kind of idea as Mohr's circles. Same way we have principal stresses and orientation of principal stresses, now we have principal dimensions and the orientation of the principal dimensions. So it's the same kind of idea. OK?
Let's see. I feel like I'm getting to the end here. Maybe I'll stop there for today.
But next time, I'll write down the whole technique about how we get these mean intercepts and get this ellipsoid. And I'm going to write the mean intercepts down as a matrix. But you could also write it as a tensor. And there's something called the fabric tensor, which characterizes the shape of the cells.
And as you might imagine, the same is with the honeycomb. If you have equiaxed cells in the foams, you might expect you would get isotropic properties. If you have cells that are stretched out in some way-- so you've got different principal dimensions for them-- then you've got anisotropic material. And you can relate how much anisotropy to the shape of the cells.
OK. I'm going to stop there for today. I'll see you tomorrow. Seems very sudden. I'll see you tomorrow.
I'll pick up and I'll finish this section on the structure. We've got a bit more to do. And then we'll start looking at honeycombs and modeling honeycombs.
The honeycombs are simpler to model just because they have this nice simple unit cell. So we'll start with that, and then we'll move from there to the foams. OK?
Free Downloads
Video
- iTunes U (MP4 - 168MB)
- Internet Archive (MP4 - 168MB)
Subtitle
- English - US (SRT)