Flash and JavaScript are required for this feature.
Download the video from iTunes U or the Internet Archive.
Topics covered: Landing and Mechanical Systems
Instructor: Guest Lecturer - Al Louviere
Subtitles are provided through the generous support of Heather Wood.
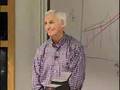
Lecture 8: Landing and Mech...
Allen Louviere started life as an airplane designer, went to Lamar University in Texas and then worked at General Dynamics in Fort Worth.
You told me about the YB-57.
I don't know what other planes you worked on up there, but -- Oh, B-58s, B-36s, F16s, F111s and B-57Fs.
Then they wanted to send him all around the world and had a young family.
And that was about the time that Johnson Space Center, which at that time was called the Manned Space Flight Center, was getting started in Houston in 1962.
So, Allen came to work.
And his specialty is mechanical systems.
We had a little discussion last night about some of the things that he has designed, but for me one of the most amazing is the landing gear on the Lunar Module.
I mean when you think that you can actually design the first piece of the hardware that touches down on another planet that's pretty exciting.
And, like most of the people who have been lecturing, he went onto work in similar systems for the Shuttle.
So, he also worked on the landing gear.
You can see a piece of tire here.
We'll talk about that landing gear, payload bay doors, and robotic arms.
And so he's going to share with us some of the experiences, both from the subsystem design point of view and then from the bigger systems engineering picture.
So, Allen, it is all yours.
Thank you.
The Lunar landing was sort of interesting.
The big problem was we didn't know what the lunar surface was like so you didn't know how to size the pad, which is always interesting.
The landing gear, we are going to talk about today, was much easier and it will do.
We're just going to talk about just mechanical systems.
It's not as romantic or ingratiating, but you've got to have them.
So, some of the avionics and other systems that you will see.
Actually, I should say one thing.
From the point of view of space engineering in general.
When you're building satellites or other space systems, the one thing that you try to avoid at all costs, I think this is far to say, is any mechanisms.
Because you send a mechanism into space and they fail.
They get too cold, they get too hot, they get vacuum welded.
Now, sometimes when you have people on a mission they can fix it.
I mean if you remember Apollo 16, the Lunar Rover, one of the fenders broke off.
And so they actually had to make another fender out of their checklist so that the dust didn't get all over them.
But basically that is the fear that all mechanical designers live in is that you're designing these things to work in an incredible environment.
And I'm sure you will talk about the landing gear.
That is one thing.
We know how to build landing gear for airplanes, but how do you keep them alive for two weeks in space in a rather unfriendly environment?
Well, the professor is right.
The problem you have is when you get these mechanical systems, if you have a lot of linkages, you're afraid they're going to weld themselves together.
And we've never had that happen but it certainly could.
The division I was in had all of these pieces.
The landing gear.
We had all the doors on Orbiter.
I think there were 25 or 35 doors on Orbiter that had to have mechanisms that had to open and close.
We built the repair tools.
We had a set of tools for these fellows to us.
And if that payload door didn't close that was really a bad day.
We put some tools onboard, a little wrench and a lot of cutting tools, and you will see some of that.
The manipulator, these are pretty well things that had been done before.
We had never done one of these before.
That's a whole different animal.
The separation system was for the separation system for the external tank.
There were three big separation systems.
It was not only a mechanical system but it was a pyro-system, it was an explosive-type
system. Believe or not, we had the ejection seats on about the first four or five flights.
We used the SR-71 Blackbird seats.
And we never had to use them, thank goodness.
We also had the docking system.
We had the Apollo system.
We had the Apollo-Soyuz.
And, if you look at the Orbiter, it is very close to Apollo-Soyuz with a little bit of modification to it.
That's the whole system.
But, fear not, we're not going to talk about all of those because that's just too many to talk about.
We're going to talk about two.
We're going to talk about the landing gear, wheels, brakes and tires.
And we've been building these for a long time.
It's more empirical design than I ever realized when we got into it.
We had never built a manipulator before.
And we started this as a technology study, and it ended up being the main cargo handling piece on the Orbiter.
Also, we did a lot of coordination and integration.
All mechanical systems depend a lot on other people.
He tells me that he wants to emphasize systems engineering, and I would like to second that because it's very important that you know that.
When you look at the systems engineering -- By the way, you don't have to be silent.
If you want to speak, now is the time.
I'm just here for a day.
I'm going to talk about this.
All engineers love the design part.
I did.
I found out that there was a little more to it than I first suspected.
If you look at requirements, schedules, cost and weight, most of the engineering work you think would be here in the requirements.
Once they are set, sometimes they're very difficult to change.
On Orbiter they were very difficult to change.
And we may have gotten some requirements that maybe we could have done a little better with had we changed them early.
And you will see the results of that, particularly on the landing gear.
That is probably the number one thing that we worry about at Johnson.
We like to keep these guys where they come back.
Now, these pieces right here are really engineering sort of things.
They relate to physics and maybe even Newtonian mechanics.
These don't.
Those are really estimates that somebody makes early.
And what they end being is a refinement process.
Most of these equations these fellows use from here are really empirically developed over many years.
They say here is the way this goes.
But all of these end up being estimates.
You think you're going to work there, but these three right here, schedule, cost and particularly for us in the aerospace weight turns out to be a big, big driver.
In fact, it will tell you what you're going to have to do in many cases.
Well, we're going to talk a lot about that.
We'll talk a little bit about test.
I presume you all, in your labs, do a little testing of some sort.
But we do a lot.
We do development testing early on.
For the manipulator, we did a little bit more than that.
We do qualification testing which is I'm going to go test this thing and see if it meets all the specifications that somebody has designed for it or the requirements.
And last but not least, after all of that is done, you do what is called a verification and certification test.
And it should be ready for flight.
I don't know what industries you're going to work on, but even in avionics, if all of your avionics people, there's a mechanical guy.
Even in avionics you'll have some sort of validation and certification test.
And these will drive you, too.
After all this is done, we did a flight test program.
And the initial test that came back from there made us do some changes on this.
And then you always get this.
Engineers are never satisfied with just making it good.
Better is what they want.
And program managers, where is Aaron?
He is not here today so I don't have to worry about him.
Program managers don't like that because what happens is this goes up and this goes up and that slows down, and that's not what they want to do so we have to go back and do that.
Enough of the intro.
These were essentially the first requirements that I could conjure up after all these years.
You've got to remember, this was 30 years ago.
Some of these may be a little off but they are about right.
It was going to be a freefall gear.
We're just going to get it started, open the doors and let the aerodynamics and just the weight of it drop that gear down and lock it in place.
The gear extension time was nominally ten seconds.
That was the max that we ever wanted it.
It would probably go down at about six or seven.
And we normally said the landing velocity, we don't want to drop that gear.
Once the gear is down, we don't want to go more than 225 knots.
Remember, this is in the early `70s and we're still trying to figure out what we're going to do.
But you've got to have some requirements to start with and these were the ones you started with.
We had a runway.
And we said the runway is going to be 12,500 feet.
We would like 15,000 feet, but because of the flight that the Orbiter took there were landing sites all over the world so we had to be sure that we'd get the landing sites with the 12,500 feet at least.
Cross-winds.
When you're coming in for a landing, if you have a cross-wind, 15 knots was about it.
We'll chat a little bit about that.
The deceleration, that was just for the brakes.
We had three hydraulic sources that we could use.
There were some auxiliary power units in the back that powered up the hydraulic system, and we had about three sources.
Most air craft just have two and a pneumonic system.
We did not have a pneumatic system.
But that worked very well, by the way.
The steering is nose gear steering.
And the hand controllers you could steer the front nose gear.
And it would go plus or minus nine degrees.
The turnover angle, if you just took two wheels and turned it over, the max that you could ever get out of that was about 63 degrees.
This set of requirements is about what we started with.
And, not to stop you, here are some more.
These turn out to be really pretty critical.
We will call them critical conditions that the Orbiter has to meet.
And this is landing weights.
And that is just how fast you're coming in when you hit the runway.
At 214,000 pounds, we were going to say we can take a sink rate of 9.6 feet per second, which is pretty fast.
And this is nominal.
If you go to Orbit and you come back and you make a nominal landing.
If it's 230,000 pounds, it's about six feet per second.
I came in yesterday on an 880.
I asked the pilot what he landed at, and it was 130 knots.
And I think the weight of that thing is about 150,000 to 170,000 pounds.
We're coming in with no engines so we're coming in pretty fast to be able to do that and set down.
This is an abort condition.
If we're on a mission and the controller is calling abort, you take off, turn around and come back and come back to the Cape.
In that case, we have a payload onboard so the weight is going to be a little heavier.
Now, the pilot has to be a little better here because he's got to have a little lower sink rate because we don't want to take all that load in the gear.
In fact, the transatlantic landing, when was working, there were only two sites.
One was at Dakar across the Atlantic and the other was at Rota, Spain.
I think Newfoundland now is one for the high inclination ones.
And AOA was once around.
You'd go up to orbit and you'd come right back down the next time around so you'd get back to the Cape.
That was essentially what we had.
This particular one was a driver also because, in the early days, the Air Force wanted to have a mission like this where you'd go up once, you deploy a satellite and you come back around.
And they were only one single orbit and you'd come back around.
Now, getting those payload bay doors open and getting the satellite out was, to say the least, an interesting design problem to do that.
You don't have a lot of time.
Anyway, these were the other drivers that you had to do.
These were the ones that really drive you because they'll tell you what the loads are in the system.
And this just tells you that all NASA guys have these acronyms.
This is a set of circumstances that says we want fail operational, fail operation, fail safe.
So, if it fails first you can still operate it, if it fails again at least you're fail safe and you at least preserve the crew.
We usually use fail op, fail op, fail safe.
In this case, in the landing gear, we only had two.
But we had a whole lot of ways to get this gear down.
And I'll show you.
It's kind of complicated to take a look at but if you release the gear it starts to fall just by gravity, but then we have a little hydraulic assist and then we have a pyro backup.
Whether you want that pyro to fire or not, it's going to fire every time you drop the gear.
So when the gear comes out, it comes out backwards.
And the airflow is this way which drops the gear down and locks it into place.
That gear is not a light gear.
I mean it's pretty heavy.
You're talking about 400 or 500 pounds coming down.
And that's just the nose.
The main gears are larger.
And then the mains operate about the same way.
And I'll show you where all this stuff is.
I have a little drawing here that will get you going.
The professor and I talked a little bit about design.
Yes.
You only drop the landing gear a few seconds before landing.
If one fails you still have time to do all the others?
I'm sorry?
You only drop the landing gear a few seconds before touchdown.
Yeah.
If one method fails, did you still have enough time to try one of the others?
We decided that all three of these were going to be in play every time.
We made sure that we got that gear down.
That's truly a bad day if that gear is not down.
All you do from the cockpit is just put down the gear handle, and then everything works at once.
Everything works at once.
You don't have to decide has the gear gone down and, if not, do something else.
It just all works.
I think you'll find that we tend, at Johnson Space Center, to overdesign on the side of safety.
And it really didn't matter to us anyway.
We really want that gear to go down and lock in place, and that's what this is all about.
The other things that we worried about, and probably where the requirements on this particular vehicle were the weakest, we said we could turn this thing around in 30 to 60 days at the Cape after every flight.
Well, that really didn't work out that way.
When you have that many systems onboard and there is so much to take a look at after you've gone to a flight, just the post flight operations is a long time.
And I'm not sure we ever made 30 days ever.
We may have made 60 once, I think, but I'm not sure.
And the other thing was the pad stay time.
First flight, as I recall, was on the pad for about four to six months.
And now you've got to make all your systems work.
It's like having shelf-life on this thing.
You've got to make this thing work.
It's got to function.
That was the other one and that was a big problem for us, particularly from tires.
They leak.
You sure don't want to have those tires leaking in about four to six months.
We had no landing propulsion system.
Once those guys came in, it was all energy management from an altitude all the way.
And the landing velocities were rather high, the weights were rather high.
Probably some of you fly.
Let's see.
A 737 weighs about, I'd say, 160,000 to 170,000 pounds.
And they come in just right at about a maximum of 175 miles an hour, but we're coming in with no engines at about 200.
The runway touchdown point, I've got a little drawing of a runway and I'll show you what that is, that turned out to be a real key issue.
When we started out that 12,500 feet I showed you was actually 10,000.
And after a while we decided without engines and then without reverse thrusters we really couldn't do that.
While that not only affected the Cape design but it affected where in the world we could land this thing, I think Guam was the other place.
We could go to Anderson Air Force Base on Guam, right?
Yeah.
And here is what frightens all mechanical engineers, limited testing, where we're only going to have about three or four flights.
We were going to have five.
It worked so well that they decided to go with four.
And everybody gritted their teeth on that one because we really wanted one more flight.
These are some more requirements of sorts, but these were outside requirements that you have to take what you get.
And so, when you do design work or whatever field you're going to work in, you're going to find you're not always your own boss on this.
You have to go with what you've got.
And I think that's part of the system of engineering.
We were told that the idea of moving the Orbiter with the 747 wasn't brought up immediately and that it was going to tried to be move with like strap-on engines.
So this part about no end-flight retraction [OVERLAPPING VOICES]?
The first design of the Orbiter, actually, the early designs had jet engines, but the weight -- Remember we talked about the weight earlier?
The weight just drove that out.
We couldn't do that.
Plus, when you reentered with those engines, you've got another problem with all the heating.
And you probably have the fuel that you have to worry about so you've got a lot of problems.
[UNINTELLIGIBLE PHRASE] Would that have been a real big problem [UNINTELLIGIBLE PHRASE]?
Yeah, it would cost you money and weight.
Remember those two things I told you up there?
It would cost you money and weight.
Remember now, Congress is a finicky bunch.
You don't go back to them unless you really have to, to get the money.
If Aaron is here, he could probably give you a lecture on that.
He used to lecture me on that, as a matter of fact.
The Carrier Aircraft or ferry, one of the guys in our division, a gentleman who just passed away recently, named John Kyker had been a B-24 pilot.
Actually, he and another fellow named Owen Morris built a little model of the 747 and a model of the Orbiter.
And they actually flew it.
The wingspan was about like that.
And they actually flew it to see if it would be all right to put that Orbiter on top of that model.
And, by golly, surprise, it worked like a charm.
Also, when they flew that model, they found that they had, on entry, a different setting on their elevon than what was being projected.
And, low and behold, they went back and they found, yes, they did and they changed it.
We don't have any in-flight retraction for what you were talking about.
We would get the gear stored on the pad and ready to go.
And, as I said, we want to be sure it comes down when we tell it to come down.
Actually, in the hanger the Orbiter is up on jacks.
And one of the last things they do before they wheel in a carrier mechanism that will take the Orbiter out over to the vehicle assembly building, you have to push the gear up manually.
And, actually, the final stage because it has to actually go in and lock inside the locking mechanism, someone is up there basically with a big pole and just push it up until you get it to click into place.
And that's terrible.
There is no hydraulic system to reconnect it.
Well, we get a little bit of hydraulic help but it's not enough.
You have to get manual labor.
But it's all because of the weight and cost that we were talking about.
And weight was really one of the big issues.
When you go to work, you're going to find out that all of those empirical things, not the design problems, not the Newtonian physics, is what really gets you.
Did they have any sort of like emergency barricades at landing sites if a tire went?
Yes, they did.
At Dakar we put up a net at the end of it.
And I think Dakar was one of the shorter runways.
I think we were worried that when we came in at Dakar with the kind of peddles we were carrying that the Orbiter was going to be very heavy.
It would be this 256,000 pound thing.
And that's a big thing with no engines.
And we'll talk about the brakes here a little bit.
The brakes were not really qualified for a short stop on a heavy vehicle.
Remember, in the early days we had no drag shoot?
No drag shoot.
Well, we're going to talk about that, too.
I'm going to try to talk about all this stuff until you guys go to sleep or something.
[LAUGHTER] Well, enough of that.
One last thing.
You will see that I'm worrying you to death on requirements.
Whether you like it or not, when you go into engineering you're going to find that if you get the requirements right you'll probably get the design right.
If they are not right you're going to have lots of trouble.
We didn't get them all right.
We didn't get them all right but it was good engineering work.
The tire pressure, we had to start somewhere so we said here is what we're going to do.
We're going to do some sizing on these tires.
And, on the landing gear, we did this before we even had a contractor, our first pressure was about 340.
I think the tires on your car are around 35 psi or something like that, if you're lucky on a good day and they're not leaking.
And the upgrade now is about 380.
I think they want to go to 410.
The wheel is aluminum.
The axel is aluminum.
We've actually bent the axel before.
We've landed that thing.
The first axel we had, we bent the axel.
It deflected a little bit and took the brakes out.
That was another one of those things so we had to up that.
It was sealed with two O rings.
That was a good one.
That was good to start with.
The initial design, as a matter of fact, was great because that four months we had to stay on the pad for the first flight we got no leakage, which was good.
The initial brake pads were beryllium.
Now, beryllium has one great feature that everybody liked.
The Langley Research Center had been working on brakes and they were using beryllium.
Goodrich had been working with the beryllium.
And it turns out that it has a great heat transfer capability, and we thought that was really going to be good.
And what do you say in your jargon?
Wrong.
It was wrong.
It did not work out right.
We had four rotors to start with.
We have five now.
If you're going to look at your brakes, I've got a picture up here, just like the front wheel brakes on your car, they have a caliper and you just put a pad on it.
But we have more pads than you do.
You will see some more about this.
This really got us.
A negative angle of attack, if you ever looked at the Orbiter when it was sitting on the runway, it sits nose down.
And when you come in and you drop that nose down it's going to load up that main gear.
And you will see what that does.
That might be all of the requirements that I have to start with.
Here is what the wheel looks like.
This particular drawing or graph is really what we started with.
And these are the summary things that we began with.
And this is the nose gear.
There are probably two or three things over here that are really important that we had to worry about.
One was a static load and the other was the weight for this thing.
This is all aluminum.
And we didn't want those going up.
At the time, inflation pressure for the nose was 300.
I think it's still a little more than that.
But the rest of this is just spec sort of things.
Now, when we did this, we had to start with something.
We did not have all this data.
What we did is we had a chart similar to this, in conjunction with Rockwell, and we worked back and forth.
That's another one of the interfaces that you had.
You always have a contractor.
And, of course, Rockwell had several contractors, I think, ten or twelve on this gear.
Getting this particular chart straight was very, very important to us.
Maybe some of the features, there is the inflation valve, the diameter here is about, I think this one was about 32 inches, 34.
And one of the design problems you get is how big a tire can I put in the wing or how big a tire can I put in the nose?
Now, the Orbiter wing is pretty good.
It's kind of deep.
The nose is not that roomy, but the nose gear is a smaller wheel.
It doesn't take the load.
That is low right now.
I think that's a little higher.
Here is the tire that goes with that.
The same sort of thing.
We start out with a sheet similar to this, not this neat and not this accurate, but now you'll notice that the tire weight is about 50 pounds.
Now we're about 100 pounds of tire just for one wheel and tire on the nose gear.
And there are two so now we're at 200 pounds.
I will tell you for sure, program managers will ask you what those weights are.
If Aaron were here he'd be fussing.
He'd say, yeah, you let that get away from you.
But that was the other one.
This is not terribly dramatic.
But I think the other thing is, see this thing, the design tire life was just for two landings.
I'm not sure we've ever done two landings on a nose gear.
I think after every flight we will take them off.
And, because of the way the runway is built, I will show you a little bit about the runway.
Here is a tire.
This is ALT-1 which is approach and landing test one.
If you can lift it.
I am going to pass it around for you.
This is ALT-1.
Here you will see that we've got 20 plies which is all this stuff here.
And that is what we used.
I think it is 28 now.
And you will see that at the top here is real rubber which is great, but synthetic rubber is better.
The tire we have now is synthetic rubber and is much better than what we have.
And you will see we have these beads in here.
Now, when you go back to the other piece here, we've got to realize that if you've ever tried to change a tire and you put the tire, all of you have bicycles.
Everybody in this town has got a bicycle, I think.
[LAUGHTER] Even him.
Anyway, when you try to change a tire, you can put one side in.
But getting this on would be really tough.
See, if you try to change this tire out it would be pretty hard.
You have to split the wheel so you can get that thing, and you put it in and then you put the wheel around the tire instead of putting the tire around the wheel.
And, when you see this thing, you will understand why.
I will pass this around for you and you can take a look.
It is heavy.
And those beads are really interesting.
They mean business.
They are tough.
They are steel.
Here is a nose gear.
This is STS-95.
Where you on 95?
Oh, I've got yours in here.
I've got yours.
Well, I'm going to let you tell it.
This hit pretty hard.
And if you take a look, you can barely see it right there, but a chunk of rubber came off.
And it's that good rubber that I was telling you about.
It's the natural rubber.
The ones we have now are better.
And when these tires hit, I think this particular one, they dropped the nose gear on rotation early.
And I think, when they did, they hit the tough part of the concrete at the Cape.
And you just get rubber everywhere.
Smoke and rubber and all kinds of stuff.
I think these are 32 or 34.
These are things that you really have to go and handle with care.
They are big.
You'll note there are no brakes on these front tires.
We will get that in a little bit.
Just to comment.
Last time we talked a little bit about what goes on when you actually land, but what Allen was saying is you flare out and then the pilot has to stay on the rear gear and hold the nose up for just the right amount of time.
If you hold it up for too long then you're going to lose the lift.
And, in the end, the nose gear is going to fall down too fast and you run the risk of busting your nose tire.
On the other hand, when you come down because of the negative angle, you actually, as Allen said, when you get down below horizontal, now you're putting more weight on the rear wheels.
And so, if you come down too early, now you run the risk of blowing your rear tires.
And so it's really a critical maneuver.
You have to hold it up just the right amount of time and then bring it down real slowly.
I think Lousma was a Marine, wasn't he?
Yeah.
Astronaut Lousma came in.
We didn't like him to fly too much because I think he did carrier landings or something.
I'm not sure what the guy did.
He'd come in and drop that gear down pretty hard and we'd all cringe thinking those tires were going to go.
Now, we saw the nose gear.
This is a repeat performance, except now we've got to make this wheel so we can put the brakes on it.
We've got to put the wheels on.
And now the same thing.
Now I'm going to tell you a little bit about integration with other people.
In the landing gear world, we were at the mercy of the structure's people.
You really wanted to be friends with them because they told you what the loads were.
And coordination with those people was really critical.
And I'm sure you're going to find that.
If you're in any kind of construction whatsoever, all the structures folks, you want to get them early on.
And the other people you want in there early are the operations people.
Those two people are the ones you want very, very early.
Here is the right load now.
If you just multiply that by four, you'd get about 250,000 pounds, 270,000 pounds that we could take.
And that is about what you're going to get on that back gear.
When you come down, you will get a little less than that.
We have about 20% to 30% margin empirically designed.
And we tested it at Wright-Patterson.
We tested this wheel.
This is a single O ring wheel.
The O ring is about right there.
And we tested this at Wright-Patterson with a side load on it, like on the flight he was on.
And I had to tell Aaron Cohen that every piece of the wheel came apart, which is not what you want to do with the program manager, but we had to start over.
So, we did.
And we beefed up the wheel, we beefed up the bolts.
We found that the two O rings we liked because they were good for leakage, but we also found that when you put them on that the wheel failed because of the O rings.
Also they failed because we were putting the wrong lubricant on those bolts, and that took a while.
And that particular failure, I just talked to you about, had both those problems.
How did the lubricant cause the wheel to come apart?
They couldn't get the right torque on the bolts.
I think they put too much torque on the bolts.
We never really found out, but we changed lubricants and that went away.
I told you now this is not Newtonian physics we're talking about here.
We're talking about empirical design.
And you had to go test this stuff.
And we did.
Let's see, what was the other point?
Here is where the axel fits in here.
I will show you where the brakes go here in just a minute.
I don't have a main gear tire cut like that one, but it's much larger.
It's about 40.
I think this one was 42 inches.
They tell me that they want to go to 44 inches for a little bigger wheel.
In the beginning, again, weight and cost stopped us from going any farther than that.
Mainly weight in that case.
Again, this was the critical wheel that we had to work with the structures people.
Our structures group worked it and Rockwell structures group worked it, so we had two structures groups that were working together and we had to wait until they gave us a load.
But when you have a design you cannot really wait until all the loads are in.
You have to start with something, so we started with a design that we thought was conservative.
It was not.
But we started with one that we thought was conservative and it did not do it.
You can see that the max load was 142,000 pounds per wheel which gave us a nice margin.
Of course, those are the aft wheels, the main gear.
And we liked that margin on there.
And the inflation pressure is about 370 on that.
This thing is like a stick of dynamite.
If it blows you have really got some problems.
I mean you have shrapnel everywhere.
But when you do the test it is always behind the cage or something where you can do it.
Again, safety was our problem.
When I saw that last orbiter come in, I thought for sure that something had happened to the wheel well and that the explosion was in the wheel well.
It terrified me.
Partially it was not the wheels that went.
They went eventually, but if you blow four of those wheels, two on each side, that's not a good day at all.
The Orbiter is about the same size as a 737.
Everybody flies a Boeing 737 about the same size, but they land a little softer and not quite as heavy.
But the geometry, a planned form looks about the same.
They don't have the payload bay that we have, but it is pretty close.
And here are the big guys.
Now you will see the hydraulic systems.
There are all the hydraulic systems that go in there.
And trying to move one of those tires by yourself is a chore.
It will get you in shape.
Rolling that thing around at the Cape will get you in shape.
And it's the same thing.
It's a split wheel that we have.
This one has the same problem.
You cannot see it but it is right there.
There is a big piece gone from right there.
And, again, it's the runway.
If you hit the runway on the high coarseness this is what you get.
I'm going to show you the runway here in just a minute, or a little sketch of it and you'll be able to see it, but you can see that that is a fairly big strut.
And we needed it.
How much travel does the strut have?
You mean after it's down and locked?
Oh, I would say probably six inches to a foot, just depending on which ones that Rockwell picked.
I'm not sure which one they have now.
We had a pretty stiff strut to start with.
I think they've done a little work on that.
That's a good question, by the way.
That does affect it a whole lot because you don't want to drop that gear too low because those doors are open.
If you drop that gear too low and that strut goes up, you're going to get those doors, and there goes that turnaround time we were talking about.
There goes the turnaround time.
I've got another one of my goodies here.
This is not the beryllium.
The beryllium had one big problem.
We thought that the heat transfer was great but the homogeneity of the heating was not good.
You would get spots.
Once you did that it would warp the brake.
When it warped the break then it would do all sorts of bad things.
When you look at this, here are the stators and here are the rotors.
This was a stator.
And what this is is they had two sets of stators on each of these.
And then, of course, the rotor went all the way around.
But here is a brake.
And you will see that it's only a piece of a brake.
And you are going to find out it is very, very heavy.
And there is really not much I could tell you about these, except that the one good thing we did was we insisted that Rockwell leave enough room in here for five stators and rotors.
We started with four and right now we have five.
And so we did it partially right anyway to start with.
Here is the axel, and this will fit on all of these.
And we thought we did about 25 stops with this thing, but I think we probably end up somewhere between four and ten.
Again, that's just money.
And, again, that's the turnaround time we were talking about.
So, all of the things we thought we could do, systems engineering things, did not work out quite right.
So the stators had to pass?
Yeah.
The caliber just pushes against it?
Just pushes, yeah.
It just shoves it.
There is the caliber so you just close that thing up and you just squeeze those guys together and you watch the smoke come out.
Did the caliber float at all like on a modern one?
We found that we had to do an orphus hydraulic system.
We found out the problem you're talking about, they had a funny name for it, but it was the one you're getting at.
And what was happening is that the brake was cycling because it was not orphused.
Once we orphused that thing it worked very, very smooth.
And, just like your front wheels, it just doesn't look much different than your front wheels, except they are a lot bigger.
And how would you like to have that pad on your car?
You would never have to have them replaced.
[LAUGHTER] Here you go.
This is a mechanical engineers' dream.
Here are more linkages than you could ever want.
You can have all sorts of fun with this kind of linkage.
This is the forward part of the Orbiter.
The nose comes around kind of like that.
And you can see that we've got that gear stuffed in there pretty good.
And some of the things that are on the door are sliced out, so when you look at the door in there you have just a whole lot of things in there.
And what happens is, remember I said the first thing is we have a little hydraulic actuator that starts this thing?
And, whether you want to or not, it opens those doors.
And we will fire this bungee right here.
This is a pyrotechnic thing.
And no matter what, we are going to fire that thing to be sure that if the hydraulic system isn't going to that, we are going to drop that thing with a pyro.
So, it opens the doors.
Once it opens and you start that gear down, remember, you've got about 200 something knots of wind that is going to drop.
So, this is going to help you.
It comes down, it folds down that way.
Our only comment to Rockwell was that we didn't like all this.
The leakages were even more than that when we started, and we had to reduce those down.
There is a little fitting right up here that you can get a little bit of help to get the thing back up.
But you do need the guys with their polls shoving it back up.
There is the wheel.
And once it's down, there is no brake on that one.
This is the forward one.
This will give you a little better idea.
This doesn't look too much different.
Forward is this way.
If you go that way, you see the gear has come down and is now locked into place.
In the other picture you couldn't see these little yokes, but when the strut comes up those yokes come up and grab it.
There is the extender strut.
Essentially, the drag shut, it's a solid piece.
I'm not sure what you could say other than the fact that that right there is the booster actuator that I was talking about, the pyro actuator.
And it is going to fire every time no matter what.
The same thing for the mains, except they are bigger.
One problem we had with this particular one was these doors.
Those are big doors.
They are bigger than probably two of these tables.
Maybe like that and wider so they are big.
And the problem is sealing them.
When you're coming in and you're going to re-enter, you've got to get a seal on there that is going to work.
Most of these were bolt seals.
You just put the Freon and they squeezed closed.
There is no seal sticking out.
Of course, it has got the re-entry material on it.
But, again, these were part of our problem.
And those seals were probably the trickiest things that we had.
And here professor is at extend/retract actuator, but it still won't do it all.
You could hook up a hydraulic system to get this gear back up.
Forward is that way.
But you need a lot of help.
Again, it was a weight problem.
I am going to show you this one, but I had to go to the Space Center Houston because I couldn't get a picture of the Orbiter.
So, this is a little mockup.
And here is the gear.
And what I really want to show you is, see that little guy right there, that's the pyro system that kicked that thing out.
They call it a bungee.
It's a Rockwell term, but it's not like a bungee.
It's really actually like a pyro.
And when that strut comes back up here are those yokes I was telling you about.
It just clamps around that strut and it hold it up.
That's probably the only thing you can see that is worthwhile on this picture.
Now we're going to talk a little bit about integration, an interesting problem.
Rockwell was our prime integrator.
They integrated everything.
We helped them, but they had all these people as contractors.
Not only did Rockwell have to deal with us.
Rockwell had to deal with all these contractors that they had.
The wheels were made by BF Goodrich.
Not Goodyear, Goodrich, which is now Michelin, I think.
And they flew it on the F-14 and C-5a which is a pretty big airplane.
We didn't have a four-wheel truck like the big aircraft did like a 747.
We thought that would be a great idea, but we didn't have the room in there to put the whole thing in.
The brakes were BF Goodrich, the same ones.
They were the ones that really wanted to go with a beryllium.
It turned out that they passed all of the initial tests for the beryllium, but the beryllium had no life, so we never really had a test failure.
But we had a test of things we really didn't like the way it was going so we changed.
They changed, I think, in 1990 or 1985 to the carbon brake that I was showing you just a minute ago.
The nose gear steering is a bi-steeror.
Nose gear steering is after you land and you get the nose gear down you can steer.
It turns out that the astronauts did not like to use the nose gear steering, so what they would do is get on the brakes.
They would do the brakes like this.
And they'd steer that way.
When you do that you heat those brakes up pretty good.
You heat the brakes up.
And, besides that, there was a single point failure in that nose gear steering.
If that thing failed, and it failed in a bad position, it might be nine degrees off, and so you're going to run the Orbiter off there.
I had to agree with the astronauts that probably the right thing to do was just get on those brakes and steer with those guys.
Menasco, they built struts for almost everybody.
HydroAir, they had all kinds of actuators.
And Rockwell did all the bar linkages that I was showing you about.
The antiskid system was another one of those important things.
What is it on your cars these days?
The ABS system.
This is our ABS system right here.
And we had one.
And we had nose gear steering.
We had all that good stuff.
You've got to remember now this is 30 years ago so it's a little different.
There we go.
I had to put that in there.
I like this picture.
There is nothing technical about it but I like it.
Isn't that neat?
Look at those little skinny wheels on that big vehicle.
Isn't that something?
[LAUGHTER] It looks like somebody made a mistake.
Anyway, it's coming in there.
You will note there are no drag shoots.
The initial design actually had a drag shoot.
One of the guys in our division decided that we didn't need a drag shoot so he put in an improvement which reduced the cost.
That was a mistake again, so we took the drag shoot off.
And I eventually had to put it back on anyway.
All engineers are not exactly right, but this thing flew well.
The gears really worked out real well.
We were tickled pink whenever we would see that thing fly.
I may have already told you.
I had to put that in there.
I like that picture.
This was a dilemma.
The tires never really failed to the spec that we gave them.
We didn't like it because we didn't think we would get the life that we wanted out of it.
And so we had running discussions.
Maybe not battles, but certainly running discussions with Goodrich on that tire.
We got excessive testing tire damage with a dynamometer test where you do all the testing and we put the side loads on.
And we just didn't like what was happening.
Even though it passed this we went to, say, 20% over.
We were really getting failures that we really didn't like.
And we knew, from the very beginning after the test, that we were not going to get the five or six landings that we thought with every tire set.
On the mains you'd get one landing and that's it.
And you can see why you would get these big hunks.
I think they are better with the new runway or with the way they fix the runway.
I talked about the wheel.
The wheel cracked.
We had a wheel crack with a load.
The bolt lubricant did not work.
We couldn't get the right torque.
The two O rings caused a failure in the split wheel.
The bolts broke and we failed the 1,000 mile test.
That doesn't sound great, does it?
But it really was because this was an empirical design.
It worked fine because it met the spec that we had.
And what drives you, as engineers you might not like it, but program managers have their problems, too.
They have costs they have to worry about, they've got schedules they have got to worry about, and they get you to do things that will work every time.
And then later on you can make the improvements.
The beryllium brakes, we had cracked hot spots on the pad, we had thermal expansion and some melting.
Goodrich kept telling us that those cracks did not matter for flight, but we didn't like it and we fussed with them a lot.
And we fussed with Rockwell a lot.
And after maybe ten years they finally changed them.
The entry displacement was lower than expected.
We thought sure that the beryllium would be a great way to do it, and it didn't work out.
And I talked to you a little bit about the hydraulic system causing that wobble.
That was the test results on our outline.
Let's talk a little bit about the runway.
I have more goodies for you.
The runway was about 15,000 feet at the Cape.
Before the flight test, how do you actual simulate flight conditions, especially with the wings to simulate heat dissipation?
You mean dropping the gear?
Yeah.
I don't think we ever really did.
I don't think we ever had a wind load on it.
But we tested that gear.
One time we did it with a lower pressure just to see if the hydraulic pressure would work.
And that may give us a little bit of something, but that's all we ever did.
We had high confidence in that pyro.
If you ever heard it go off.
But you rely on the wing load to dissipate the heat, right?
One of the things, yeah.
And gravity, of course.
You're getting a gravity down, too, on the thing.
So, you're getting wind, you're getting gravity, you're getting pyro, you're getting hydraulic.
No, to dissipate the heat in the brakes.
Not the gear, but to dissipate the heat from the brakes you rely on the wing load.
Oh, sure.
But you couldn't test that on the ground?
I don't think we ever put it in a wind tunnel or anything.
If we did, I don't remember.
But we did check a lot to see what the heating was.
And we did it on a dynamometer which is like you do to your car tires.
No, I don't think we ever did.
That's a good question.
I wonder why we didn't do that.
I had to think about that one.
Here is the runway.
A lot of people in NASA have built runways and looked at them.
And what they did is they put these grooves in there to get the water off, just like they do on the highways now.
And you will see that is the grooved runways right there.
It sits in there about like that.
And I will pass this around and let you see it.
And you will see that it is really rough.
And you can see hitting that surface at those speeds is not really good.
What they have done, after I left by the way, which is a great thing to do, is they shortened the high friction part of the runway and they pinned it with like a ball pinned hammer.
They pinned it like they do highways.
That got our friction factor down.
We missed the friction factor, by the way.
And they put a thing called a corduroy on the front.
And here is the corduroy.
You want to take a look at that.
It's like that.
And so now the runway looks like this.
I think if we were going to fly the Orbiter some more that probably with this runway now at the Cape we would probably get a little better use out of the tires.
It turns out that trying to determine the friction factor here was not as easy as we thought.
And you will see when you see that the thing is not a smooth surface.
It's a pitted surface and it has little things that stick up.
And so if you pin it down like you do like a highway and get that it's much better.
We've gone through the requirements.
We've gone through some of the testing.
Now let's talk about operational findings that we found on this thing.
Remember, if you're going to be an engineer, which you are I hope, you're going to find out that all three of these things will be a problem for you.
You'll have to look at the requirements, you will have to look at the testing, and you will have to look at the operations of the thing.
If you work for a company they will put you way ahead if you tell them we ought to go find out how this thing is operating with our customers.
Here is what we found.
Our deployment velocity, when we dropped the gear on landing, was 312 knots operational.
Good.
We were right on.
Landing velocity was 225.
We actually came in once at 232 or a little higher than that.
And that was the Marine landing.
I'm not quite sure he was wanting to do those carrier landings.
The operational weight was higher.
We designed for 214 to 230.
We ended up with about 225 to 232 which is not bad because we had enough margin in those tires and wheels to take it.
The sink rates were not bad.
6.7 is about what they would always land at, which was really pretty good.
Now you can see that our design was not that far off.
The negative angle of attack I want to talk about here.
Let me show you it.
For some reason the initial design, which I guess we were all part of, had a negative angle of attack if you would take this route.
It was about four degrees down like that.
Now, if you take a look at this, when you come in here you will see that if you're going to get a load in your landing, so the elevons are going to be up a little bit, what you're going to do is all those loads are going to dump right straight into that back gear.
And that's really not what you want.
You ask yourself, well, why don't you just raise this gear?
And the answer is money [LAUGHTER] and weight.
But the initial thought was we ought to have it to look like that and do that and we will take the load off the brakes.
I'm not sure that was one of our better moves but that wasn't bad.
We talked a little bit about this [the negative angle of attack?].
The nose gear steering was never really used.
I'm not sure they do it now.
Oh, no, they fixed it.
Have they fixed it?
Yeah, they use it.
In fact, it was after our flight.
That is when they finally decided to fix it.
We're going to talk about his flight in just a minute here.
I went through great lengths to get his.
We had one tire failure on 51D.
And, after our operations, we did find that we could get John Young, who was chief astronaut at the time, to say, yes, we're going to change how we do these elevons on landing so we will take some of the load off that gear.
Let's review it.
We had the requirements, we had the design, we had the test results and now we've got the operational results.
The whole systems engineering scheme is to go from start to finish.
And this is what we did.
I may have made this sound more negative than it was.
It was great fun and it worked really well.
I mean it worked well.
As an example, and what the professor was talking about a minute ago, we did one of these.
This is loads here, but we did one for heating early on.
And we had a little computer, which was one of the few on the center at the time.
It was a Wang desktop.
They've never seen that.
I know that.
[LAUGHTER] It's a foreign word.
It's about this big.
And I think it had a max of about 256k and that was it.
We, to keep up with Rockwell, instead of loads, did heating because we were more worried about the brakes than we were the tires.
And, if you look at this curve, this one sets that nose gear down a little early.
You come in on the mains and you drop that nose gear down.
And then all of a sudden you get this spike.
Well, you can imagine if you get this spike here, the heating is going to be higher from there on.
If you keep that nose up, like he was talking about a minute ago, and you just wait a while and you get way down the runway or down the runway some place, you get a little lower load and it's a little easier on those tires and on the brakes.
It gives you a little longer rollout, but that's not bad because we've got plenty of room.
Now, some of these fellows had a problem with this one.
This is 51D.
This is the infamous flight for the professor.
See that tire right there?
It is blown.
It is the only tire that we blew in the whole of the flight test.
And what are we at 210 or 214 along flights, and it is the only tire.
I'm sorry, 114.
It's the only tire that we blew.
And I tried to ask him last night what they did.
I'll tell the story.
Well, I was going to tell you, he had a tremendous side load.
He had a tremendous 15 knot crosswind that they got.
And the gentleman who was flying was a fellow named Bobko.
He's kind of fun to talk to.
He did a good job getting that thing in.
And they got pretty far down the runway.
I think it was only 200 feet, our guys told me, before that tire blew.
And you were almost at a stop.
You were just going a little slow.
But the brakes were heating up because he was on those brakes fighting that side load.
More operational findings.
We shot-blasted the center strip at the runway.
We improved the groves, like I was showing you, and we put the corduroy in.
And that all happened after I was there, but I still deal with the guys out in the center and they helped me out to get this.
The design problem was the wing volume that we had.
We started 42.
They tell me they are going to go to 44.
I don't know if they have.
The tire pressure was 370.
We could go to 410.
I think the new tire will have 410.
We talked a little bit about lengthening the nose gear which would relieve some of that problem with the nose down.
It turned out the proposal was prepared.
It was presented.
And they decided that they really didn't want to do it because it would cost too much money and was too much weight.
The Orbiter, at one time, had a CG problem.
And I don't think they wanted to weight up there with that much of a moment arm on it, was one of the reasons.
The carbon brakes were added in 1990.
They worked great.
The new synthetic tire in 1992, which is different from that tire right there, worked very, very well.
The drag shoot.
We put the drag shoot back on.
And this is nothing more but a [UNINTELLIGIBLE] picture, but there is that drag shoot right there.
We have that drag shoot on now.
And they tell me that helps a lot.
If you put that drag shoot on, you save the brakes and you save those tires, too.
And it also tends to stabilize you to keep it going straight down the runway.
Even with the crosswind?
Even with the crosswind, yeah.
And you have to realize that this has to be designed not just for a landing at Kennedy Space Center or at Edwards where you have a three mile long runway.
Like Allen said, you've got contingency runways around the world where you might be landing with just two miles.
And that is when this stuff is really going to save your bacon.
We were proponents of the drag shoot for a long time mainly to save those tires and the brakes and get the cost back in there.
It was added in 1992.
And so with all of that.
After I told you all of that, I was a little bit negative, just to let you know, that everything doesn't go smooth.
If it does not go smoothly when you do engineering, I would suggest to you that you're probably going to have the same kind of situations.
Just concluding comments.
The tire design on development had margins to meet all the initial requirements, and they did fine.
It is still flying and flies well, a good vehicle.
We only had one tire failure, and the professor was a witness there, he was there.
We could have had a longer life on all that, but the clear issue was really weights and money.
Again, it is one of those systems engineering things where you have to trade that off.
The wheels performed a design.
Even better because we didn't have any leakage in six months on the pad which was great for us.
The beryllium brakes functioned but were sporadically marginal.
The KSC runway had friction and rough surfaces but that is fixed so everything is pretty good now.
The initial design of the requirements and improvements have continued, and I am sure that they will continue until the Orbiter doesn't fly anymore.
And I am going to stop right there.
You've had enough of me for a little bit.
Any questions on this stuff?
What did you think about that concrete?
Did you pass that stuff around?
Isn't that something?
It fools you, doesn't it?
I had never been to the Cape.
It is a lot rougher than you think.
And you see that stuff and say what were we thinking?
That's no good for a big tire like that.
OK, gang.
I will just finish the story of this 51D flight that Allen mentioned.
It was the sixteenth flight of the Shuttle.
It was my first flight.
And actually there were seven people onboard.
Six of us were rookies, so we had never been in space before.
And the commander had only been in space once and he was in charge.
And it was quite an exciting flight because we had a malfunctioning satellite, we had to do an unplanned spacewalk.
We did an unplanned rendezvous with a satellite.
And so lots of stuff had happened.
And then we came in re-entry.
And I just remember the deal was, as Allen said, the nose wheel steering was built in, but it was a single string system.
There was only one hydraulic loop in the nose gear.
And if that went hard over then you will leave the runway.
And so Gastros decided that until they made that redundant we weren't going to use the nose wheel steering.
In order to steer down the runway, you put even more or less pressure on the right or the left brake.
It turned out that we landed with the max crosswind.
We had a crosswind from the right side, I believe, and so wanted to blow the Orbiter over to the left side of the runway.
And so the commander had to put extra brakes on the right wheel.
And so that was what was heating up.
And I just remember, because I was sitting right behind him up on the flight deck, we touched down, everything went fine down the runway, the nose wheel came down and we could feel the deceleration.
I thought we were just about stopped.
And I remember thinking to myself it's all over, nothing can go wrong now.
Boom, the whole Orbiter shook.
I mean I really thought that one of the fuel tanks had blown up or something.
It was really impressive.
And, like Allen said, these things put out a lot of shrapnel.
In fact, after most flights, sometimes you will see the crew get out and walk around and kind of kick the tires and just sort of pat the Orbiter and say thank you for a nice flight and all that.
But they made everybody get out of there because the other tires, obviously, were overheated as well and they were worried that they were break.
But, as Yogi Bear said, it ain't over till it's over.
And it was exciting.
But after that they fixed the nose wheel steering, they got rid of the beryllium brakes and replaced them with carbon, they put in the drag shoot, and we really haven't had any problems since.
And I think it's a really good example of the whole engineering process where you build in margin.
And that is absolutely critical when you're designing a system.
And then going through the testing and then the operation and then closing the loop.
Once you find out how these systems really operate then, if you have the ability to make changes, you can go in and improve them.
Let's take our two-minute break, stand up, turn around and then we'll take up again with the manipulator systems.
Start up again with a different mechanical system.
In this case the manipulator system which is the space crane.
That's a good term for it.
It is a space crane.
This is a whole different way we did this.
When the Orbiter was built there were several sized payload bays.
One was 30 feet and one was 60 feet.
And it turned out that we did not really have a system to handle the payload where you were going to carry the payload, but we really didn't have them at the time.
Altitude and inclination varied.
Here was the significant capability we had to do.
We had to do 65,000 pounds, 15 foot in diameter and about 60 feet long.
That is about the size of a greyhound bus.
And we really did not have any system to handle it.
The thoughts were don't worry, we will spring it out, we'll throw it out, but we had no retrievalment methods.
Besides that, another systems engineering problem, most of the resources in the program were on the Orbiter, or just to get the shuttle flying.
And there was really not a lot of attention paid to the payloads in the early days.
In addition to that, when you look back, the ongoing programs were Skylab.
We had Skylab still going.
We had Apollo-Soyez just about ready to fly.
And then the prime objective, the Orbiter.
All these things contributed to the fact that it was a little later in getting this started than perhaps it should have been.
All the NASA centers had a concept.
Marshall had a concept.
We did not have a concept at Johnson at the time.
We were doing some off-line work on manipulators, but the initial part was not for the Shuttle.
We had some systems that were pretty good for deployment, but we had no system for retrieval at the time.
That was a problem.
The manipulator became a crane.
It essentially became a contender once we understood a little bit more about the requirements.
And the one that came up that said we have to go capture a satellite.
That is the one that was the real driver for the manipulator.
We had some studies going on.
I guess you guys call it robotics.
And we had found that we could get from General Electric some of the Atomic Energy Commission which they used to handle the very critical elements.
And we were just working on it.
And this was a side issue.
We were doing this technology.
It had nothing to do with the Orbiter at the time.
And we decided, after a while, that we liked the way it worked and what we would do is just make an extension of that, so we did.
And we decided that we would try to go to handling system.
And we did.
I'm not sure.
Is master slave a good term for robotics these days?
Let me tell you what a master slave is.
The hand controllers or whatever you're using looks just like the manipulator.
You have a little bitty one over here.
You've got a big one over here.
We were using a master slave kind of system.
And we found out right off that if you've made an arm that long and you try to put it in the crew cabin, it took up a lot of volume in the crew cabin.
And so we didn't have that much room to start with.
That became an issue right off.
The other issue was that we found out that when we were working with the AEC kind of things that dexterity and feedback was very important because they didn't want to drop this thing.
They wanted to be sure they could handle it.
But we really didn't need that.
We decided that we had to have a larger system than that.
And we also found that during these tests the fellow would hold his arms up and would get tired.
We decided if we got a barber he would be the guy that could operate this thing better than any of us.
[LAUGHTER] That's a 1G problem.
Even there, for training, he would get tired so easily.
But we never found a barber that could do it.
And we kept the master slave concept for future testing.
Just so we understand what a master slave is, let's take a quick look at this.
Here is the master.
You can go over and grab the hand controller right up here.
And, as you move that hand controller, this piece over here moves exactly like you move the hand controller and the arm.
Now, that is interesting because if this is one foot and that is 50 feet, you get a radio of about 1:50.
Instead of being able to move it like we wanted, you now have to ratchet the thing every time you did it.
It took more space.
So, we decided that really was not a good idea.
In addition to that, we found that the manipulator that we had was really too small for what we really wanted to do.
And the other problem was that the GE hydraulic manipulator was probably not what we were going to fly in space.
We did not want to fly a hydraulic system that would leak.
Now we had a problem between hydraulics and electrics, which now we had to do some modeling on.
Of all things, we had some money from the NASA Medical Group.
We told them what we wanted to do, they gave us some money and we went and bought a manipulator from GE.
They got it from Pittsburg Plate and Glass.
It was about 25 to 27 feet long and it had a suction end effector on it.
And what they would do is pick up these big pieces of glass and move them.
We bought their manipulator for about $50,000, I think, but it was medical money of all things.
And it had a master slave and it had a vacuum end detector.
We decided that there were several things that we had to analyze just to get this thing started.
One was the master slave, and we decided we wanted an alternate concept.
That one didn't even work.
The feedback versus fixed hand controllers was the other one.
A lot of people wanted feedback.
Do you do robotics with feedback, too?
Any of you in robotics?
I can tell you anything, can't it?
[LAUGHTER] Well, we didn't think we need it.
The viewing, the line of site turned out to be another issue.
When you look at it, in the Orbiter, we had it at the aft station.
And looking back, at the time, there were no windows facing out.
What we did for the first time was put TVs on the Orbiter to use it.
So, the initial test was to see if we could do things with the TVs.
We decided that was an issue.
The end effector configuration was really never solved until about the end, and that's the thing that is the grabber that you have to grab this thing with.
And the power source we got fairly early.
We did not want to use hydraulics.
The other thing was the tip speed, and that is the speed at which the tip of the manipulator has to move so you can do things with it.
The problem we had is if we are going to capture a satellite and we had a relative velocity between the Orbiter and a satellite, since the guy was going to have to move this thing, but we didn't have a requirement so we had to go work on that.
Payload and cargo handling was the other.
We knew that we were going to handle 64,000 pounds.
And the manipulators we were working on weren't going to do it.
And, of course, the satellite capturing and retrieval was what I've already talked about.
We did a little modeling and converted some things at the center.
We decided that we had to have a high bay, a big room, so we got a room that was Building 13 and we built a plastic floor that was very smooth and put payloads on air bearings.
And then we mounted our manipulator right next to it.
Then what we would do is, on the air bearing floor, everybody would push this 5,000 or 6,000 pound payload across the floor.
And we had two strips where we could get the velocity of what was going.
And we decided that we would try to find out what the tip speed had to be to capture at certain velocities, so we did that.
And we just had very, very simple-minded effectors, but it worked fairly good.
We also worked on stationary.
These payloads right here, after using this floor for probably a year and a half, we came up with some requirements.
We couldn't use a master slave.
The feedback didn't really help us.
It was just too big.
Tell you what, if you ever look at the linemen these days that go up and fix these high lines, their manipulator, their system is similar to what we have.
We have a little bit more sophistication in the avionics, but it is very, very similar.
Mechanically they are very, very similar.
The line of site would be required.
We had an astronaut come over and use the manipulator.
We gave him a TV and then put what it is called an eye mark recorder on his head.
And what this eye mark record was is it looked into your eyes, and when you looked at something out here on a TV over here, you could see where he was looking.
Then we ran a test to see, while he was operating to capture these satellites, whether he was looking at the satellite -- I'm sorry, the TV, or while he was going line of sight.
It turned out, it was very interesting, it was 60% he was looking line of sight and 40% on the TV.
At the time, there was no aft window, so we went to Rockwell and they decided to put the aft windows.
Again, here is one of those problems.
The aft window is about that thick.
It pure quartz and is very, very heavy.
And nobody wanted to put them in.
I think we had some overhead windows in to start with.
I'm not real sure about that.
But we have overhead windows in there and aft windows.
So, we got those put in.
We also defined the end effector speed, the tip speed.
We found out that about foot per second was about all he needed.
Other than that, probably the satellite was moving so fast and it probably wasn't safe to do it so we settled on that.
We decided that we could capture satellites.
That was done.
And we again said we could not see using hydraulics on this system at all.
So, we moved to a bigger building.
Now we built a 60 x 80 foot floor and ran satellites across it, a very smooth floor.
The smoothness of the floor, we had a little hole in the middle that was 0.009 inches deep, and we shot the whole thing with a laser and got the floor built.
We also needed an Orbiter mockup so we built an Orbiter mockup to about where it would be on the Orbiter.
We got the floor built.
That should be 80.
The manipulator was now 50 feet long, so we had to make it 50 feet long.
But the problem was, since we were going to use the electrical system instead of the hydraulic system, now we had to make that hydraulic system think it was operating like an electrical system.
What we did was, on the electrical system, if you put the arm straight out and you lift it, we had a first cut at 100 pounds.
Now in orbit it is inertia that is going to get you, but on the ground we said we will hold this thing out at 100 pounds for the electrical system.
So, we modeled the hydraulic system to work just like that.
Also, we needed a lower scale payload.
We did not have any.
Remember what I was telling you a minute age?
60 feet by 15 feet is about the size of a greyhound bus.
Was what we were trying to work on.
And we also went to a fixed hand controller which drove us into the hydraulics business.
I'm sorry, into the avionics business.
Before we did that we had to figure out a way to handle payloads.
And so what we did was we had looked up some of these people who were loggers up in the Northeast, and they were using essentially a dirigible to take the logs down.
And they were big, about like what we wanted.
We got that company, Sheldahl, I think was the company, to build this thing and put helium in it.
And it turned out something this big has a tremendous inertia, which was great because that was what we wanted.
We didn't want it to be heavy but we wanted the inertia.
Plus, we got a little resistance from the air when we moved it around.
We had to take that one and show that we could grab it and put it in the payload bay.
And that took a while because when you get it all set around, when you start putting it down near the payload bay, say there is the aft station of the payload bay, you find out that you cannot see anything.
Now you really are on the TVs and you really have to get that manipulator where it knows where it is.
That was the other thing.
We found that once you started drop some of these payloads you will want to automate a whole bunch of this stuff.
In addition to that, when you look at the requirements, just putting it in the payload bay is kind of interesting, but once you get it in there you've got to hold it.
What we did is -- There is the trunnion right there.
You can see right there is where the trunnion goes in there.
This thing comes back, it opens up and it's like a big latch.
If you can drop that thing in there, you can just put it in there.
Now, that is not so easy so I will show you.
We built some guides.
But the other thing was none of the payloads were all the same size.
What we had to do is, this is the longeron right there.
There is that longeron in there.
And so we had these bridge fittings that you could move along and move all along the payload bay.
Now anybody that came along with any kind of size of payload we could now accommodate those fellows.
And it worked fairly well.
And we had done that.
The other part was once you got the trunnion latch you had to get this thing in there.
What we did was we tried a lot of schemes, but this was one that worked.
Let me start with this side.
There is the trunnion.
That is essentially these guys right here.
Those are the trunnions.
When you look at the trunnion it sticks out of there and it just drops down into the payload bay and it goes into that latch.
But getting it into that latch is not that easy because you really cannot see sometimes.
What we did was built a thing called a V Guide.
This is the V Guide right here.
And the V Guide over here is right there.
And then we have a scuff plate so that once you drop it in the V Guide this scuff plate kept the payload from hitting up against that latch.
And they are still using the same concept.
Here is what we really went with.
Not master slave anymore.
I'm sure in robotics labs or something you probably go to hand controllers like this.
We went out and looked at a lot of the cranes that people work with, and we found out that these three motors right here all were parallel, their rotation was parallel.
What we did was put sort of the auxiliary placement things outside those three things, just the way the linemen do out there now.
They do not have a hand controller.
They have a switch box or they have little handles that they use.
That is essentially the configuration that we started with on there.
And, if you look at it, this is a little more complex.
And about this time we had had enough work with the manipulator that we had that we had built in-house a 50 foot model that we could use and prove to the Program Office that we could handle the payloads.
We had the big inflatables, we had the air-bearing floor, and so the Shuttle Program Manager said we're going to go with it.
And the Air Force wants it so we're going to use it.
At about that time, the Canadians decided they wanted to be in the space and they are the ones who came and asked us could they build it.
And people in Washington said yes, so our division kind of backed off for a while and they formed a program office with the Canadians.
Actually, that is a Canadian arm called the Canada Arm.
Well, you know, you've got to have everything.
[LAUGHTER] This is the longeron in the Orbiter.
This right here is the longeron in the Orbiter.
And these are just little sort of wrists, and they will latch it in.
And you can see that we got the TVs here.
I think that probably this gives you a little better feel for the rotation.
We had one rotation that the first thing we had to do was, because when the payload bay doors closed, they closed on top of this thing so what you had to do was roll the manipulator out because we had to get it out of the way so there would be no interference with the payload bay doors.
There is a degree of freedom that is really just repositions the thing.
And then after that there is five degrees of freedom on there at least.
And if you start from the back here that first joint is a yaw.
And then all three of these center joints are translation.
And then there is a roll up here and there is a pitch up here.
We could go to any place with the end effector if we had the tip speed and we had enough joints.
The problem was that when we did this and we tried to build some gear trains and we found out that you didn't want to back drive this arm.
You caught something and it back drives.
We did that a lot with the inflatables.
If you use spur gears you would strip the gears out, so we went to roller gears or essentially the planetary type gears.
I think the Canadians now have all these interior angles or all those roller gears.
In the interest of time, since I am going on, here is the manipulator and this is the aft station.
And I have a little better one of that.
But about the time that we were just about to get this thing proven, we found out that people in the world were very interested in this.
We had a Russian general want to come see us, so we said OK and we entertained the Russian general.
We wanted to show him that even though the arm was about 40 feet long that we were very dexterous so we were going to pour him a glass of water.
And we did, except when we got the general there and I walked in, they had the glass, but the water wasn't in what I thought it was in.
It was in a vodka bottle.
[LAUGHTER] And there is no liquor allowed on a federal installation.
And I'm sitting there and the guide is looking at me and I'm saying there goes that job.
[LAUGHTER] I told the general, his interpreter, hold your glass there so that you got the bottle.
Real nice.
The guy was really good at the manipulator.
He poured it in there.
Fortunately it was water.
[LAUGHTER] But we actually poured a glass of water out of vodka bottle for the general.
But I thought my time at NASA had come to an end.
You guys wouldn't do that, would you?
No. It would have been vodka.
[LAUGHTER] Yeah, they'd use the vodka.
Nowadays, they might use the vodka.
I hadn't thought about that.
Well, let me go on here.
I was going to point out one thing here that the TVs turn out to be a very important part of this whole thing.
Once you get a payload and you sort of are blind, now you have lots of TVs you can use.
There are four on Orbiter.
There are two up front, two on the back bulked and there is one on the end effector so that you can sort of see where you're going for the last engagement.
And you can see here there is the aft station, there are the windows.
Now, he's got a pretty good line of site if there is nothing in there.
If there is a docking tunnel in there that makes it a little more difficult.
Did you have a docketing tunnel?
You just had a place where you could set it.
My favorite thing, for this gentleman, is that fixing the Hubble to me was the greatest thing that we have ever done.
And I hope they do it again some time.
And the manipulator always plays a part in that.
The only other thing that we did that was interesting, early on we built an end effector where the astronaut could stand on it.
Our first cut at this was to do it like the guys that do the high lines, and we put all the controls out on the end effector.
The Canadians did not like that.
It complicated things.
Remember, we only had about 120 kilobytes total for the computer for this thing and that was it.
They didn't want to waste any more and they didn't want all the weight.
I guess the astronauts or someone said we'll go with just a foot stand and then we will control it from the aft station here.
And I think that's the way you do it now, isn't it?
Yeah.
It was a tough battle, but weight and cost won out again.
It's tough to beat them.
These aren't really that great, but you can see that this thing takes up a lot of control panel in the aft station of the Orbiter.
It really does.
And here are the windows right there.
And there is an overhead window.
We thought at one time that what we would have to do, the arm is here, this aft, there was a payload that wanted the arm to come back this way.
If it did that you had to have that window.
A very strange thing happened, because when you turn your arm back that way, right is left and left is right.
We had to practice the reverse of everything or get a mirror or something.
We tried a lot of it.
The Program Office wisely decided that was not a good idea so they were going to handle that payload another way.
I wish I could remember exactly what it was.
There are two hand controller here, and here they are right here.
This was a lot more fun than wheels, brakes and tires.
This was a fun project.
And this is the translation controller.
You've operated this one.
And there is the rotational hand controller.
This one on the left essentially operates the three center joints where it goes like that.
And then all the others are done with this hand controller.
I think those are pretty normal flight controllers, aren't they?
Those are the ones you used.
At least we thought it was.
The biggest argument we had with the Canadians was this, the end effector.
That is the hand, the thing that grabs it.
We wanted one that was more dextrose.
They argued, and rightfully so, that what we really wanted was one that would make a good sturdy latch.
And this one does.
The way this works is that there are three little wires in here, three cables that come in, so once this end effector is placed over this grapple pin here these wires close.
And, as they close, they also move back and they grab on the end of that pin right there and pull this end effector into this shoulder right here.
Now, in the meantime, there is a docking target that he looks at that he can see.
Now, once it sits on this shoulder that really is a good structural latch.
You've got a great structural latch.
And if this indexes you can also make an electrical connection across there, which some payload is willing to do.
Now you make a capture latch which is essentially the way you do docking a lot of times.
You make a capture latch with these wires that actually just close around this thing.
Then it pulls it back, sets it on these shoulders and now you have a nice sturdy thing.
And the Canadians did a good job there.
I have to tell them that.
The problem with that is the one we had on the nose of your steering.
We had ten single point failures in there which makes you nervous, particularly if you're hauling a big payload or an expensive payload.
However, they did a good job.
Reliability has never failed that I know of, so that was a good thing that they did.
This was a lot more fun than the wheels, brakes and tires guys.
Then the only other thing is we had a backup mode.
We were afraid.
At the time we weren't that enthused with computers so we wanted a backup mode.
So, we got everybody to go to a single joint mode.
What we did was hardwired all the joints and put a box on the control panel so you could move each joint singularly.
And that was the backup mode.
You can do it with a single joint or you can do it computer supported.
You can do it either way.
And we also had to have a jettison mode.
If this thing stuck out there, you would have to throw it overboard because you couldn't close the doors.
We had to get rid of it.
The Canadians thought that was not a good idea.
OK, last bit.
This was a different project from the other one I was talking to you about.
This one did not start with any history at all.
We really had to start this one from scratch.
It is probably one of those things that came along just at the right time.
And we were studying some technology.
And we had enough sense to convert, but it essentially is just a big crane.
I think that the thing that surprised us the most was this one right here.
The crew took to this very, very easily.
It took very little for them to do it.
As a matter of fact, our simulator in Building 9A became a trainer forum.
We were still doing development work.
And they said, no, we're going to make this a trainer.
And those guys were pretty good.
They came in, in very, very little time.
We had to do this.
This was that inflatable testing.
Remember on our other project I said you've got to do the testing, you've got to prove the requirements?
Here was one where we did a little bit of innovation with that big inflatable to show that we could meet the requirements.
And we did.
And surprisingly and happily working with the Canadians was great fun.
It was the first time I had ever worked with any of the internationals, but it was great fun.
And they did a great job on this thing.
They are still upgrading it.
It is still flying.
And I'm taking up all your time I'm going to take up.
Just one or two things in finishing up.
Allen talked a lot about the importance of testing.
And this was a challenge with the arm because, remember, all the stuff that we did with the inflatables, that was all done with a hydraulic arm.
The actual arm with the electric motors was incapable of lifting its own weight in the earth's gravity.
I remember going once up to the factory in Canada, and the only testing that they could really do, they had a big air bearing floor up there.
And they could use the electrical arm, but only in two-dimensions.
And so it didn't get its full three-dimensional testing until STS-3, the third orbital flight test where they had the arm on.
And that was the first real use where they could put it through all the paces.
But it really has worked well.
And, in fact, you've all seen the picture of the astronaut Bruce McCandless and the manned maneuvering unit flying off by himself.
That has become like an icon.
The reason that was originally built and fielded was because people didn't think that the manipulator arm would actually have the capability of grabbing onto a moving or rotating satellite.
And so the idea was that the astronauts would have to go and catch it and then fly it or stabilize it so that you could come pick it up with the manipulator.
But, on the solar maximum repair, actually, it turned out that they couldn't catch it with the manipulator because there was a configuration problem and they couldn't latch it.
And so they actually had to go after it with the manipulator arm, while it was spinning, and they were able to get it.
And, in fact, a lot of work that we did in simulators showed that the manipulator had a lot better capability than we originally thought it would.
That was Joe Allen, right?
Well, it was Terry Hart who actually caught it.
Terry Hart. There was Pinky Nelson who went out.
Joe and Dale went out to get [OVERLAPPING VOICES].
These were not big astronauts.
They were a couple of the smaller guys.
Anyway, just to end, the moral of this is there is a lot of discussion often about humans and robots and who should be doing what.
And I think a lot of people don't realize that, from the very beginning, we have actually had a human robotic interaction on the Shuttle.
And particularly for EVA activities it has allowed -- And I will be talking about this later in the term.
We get humans and robotic systems working together.
Now, granted these are teleoperated robotic systems.
The real hardcore roboticists don't call it robotics unless it's autonomous.
But, nevertheless, it is a telerobotic system that we use in combination with humans.
And it has given us very great capabilities.
OK, we will see you on Thursday.
Let's see.
Oh, there is a lot of stuff.
OMS, RCS, fuel cells, auxiliary power unit and hydraulic systems.
And also we will be looking for the outline, the first cut on your reports.
Henry will reveal you with all of that.
And let's thank Allen.
[APPLAUSE] Thank you.
Free Downloads
Video
- iTunes U (MP4 - 255MB)
- Internet Archive (MP4 - 404MB)
Subtitle
- English - US (SRT)