Flash and JavaScript are required for this feature.
Download the video from iTunes U or the Internet Archive.
Topics covered: Test Flying the Space Shuttle
Instructor: Guest Lecturer ‑ Col. Gordon Fullerton
Subtitles are provided through the generous support of Heather Wood.
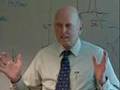
Lecture 22: Test Flying the...
Related Resources
Col. Gordon Fullerton Bio (PDF)
In that case, I will move on to introduce Colonel Gordon Fullerton who got is bachelor's and master's degree from Caltech in mechanical engineering, did ROTC and went on to the Air Force where, well, I guess he has flown, in the course of his career about 135 different types of airplanes. 16,000 flying hours. He flew F86 interceptors, B47 Bombers before going to Air Force test pilot school in the mid `60s. In '66, he was chosen by the Air Force for the Manned Orbiting Laboratory which was going to be the Air Force's Space Station. That program was cancelled in 1969 and the MOL, well, some of the MOL astronauts came over to NASA and became NASA astronauts. That was in the heyday of Apollo. And Gordon was support crew on the last four Apollo missions. Then went on to be the test pilot on three of the first five approach and landing tests. If you remember, that is when the Shuttle Enterprise, which was not designed for orbital flight but was designed to test basically the last 50,000 feet down to the ground, was dropped from the 747. Went onto pilot the third Shuttle flight, which was one of the orbital flight tests. That was the flight which landed in New Mexico. And then commanded STS-51F which was the first flight of the instrument pointing system. That was also the flight, I am trying to think, where you lost the engine, which we talked about. That was the one flight where we had an engine shutdown. And we went over that in some detail. I think they should hear about it from what it seemed like inside the cockpit, now that they have heard kind of the technical details. In any case, after leaving the Astronautic Office, Gordon has moved into pilot's heaven which is Edwards Air Force Base, the Dryden Test Flight Center where he basically spends all his time. Well, not all of his time because there is management stuff as well. Unfortunately, that is the price you pay. But basically he gets to fly airplanes for a living. And lots of different kinds, including the career aircraft and the B52 which launches various test aircraft and a whole bunch of other airplanes. If you remember in the whole systems engineering approach to things, we talk about the conceived design, manufacture, test and operation. So this is basically the final lecture and this is the test and operation of the Space Shuttle from a pilot's point of view. So, with that, I will give it to you, Gordon. Thanks. I was sitting at your place back in 1958 when I was a grad student at Caltech for a year before heading off to the Air Force. Wow, almost 50 years ago. But the real blessing of my life is to be able to do what I love to do for as long as I have done it, beyond all reason. Anyway, I hope to share some of that with you this morning. This is my first time through this pitch. Feel free to holler out any questions as we go and we will stumble through it together. I planned to talk about three different phases of the orbiter test program. The first were called ALT, the Approach and Landing Test, that consisted of really 13 flights, five captive inert flights where the enterprise was flown on top of the 747 but nobody in the cockpit. The controls were locked. That was to clear the envelope for the kind of unlikely looking combination of a 747 with an orbiter on top. And then there were three "captive active" flights where we were manned up in the orbiter with the systems running, the electronics, the hydraulics were active. The controls were free to move a little bit, not full throw. And we also determined how high the combination could get. Because altitude was not 50,000 feet, it was more like 28,000 feet max even with the 747 engines over boosted. Followed by three "free flights" were we actually pushed the button, munched off the top and glided to a landing. The orbital flight test, prior to the Shuttle Program, OFT consisted of four flights. STS 1 through 4 of varying durations. STS-1 was planned for just a couple days to get up and get down and have a look at how things looked after it flew. STS-2 was supposed to be five days. They had a fuel cell problem that cut their flight short, unfortunately for the crew. Then I was on STS-3. We were scheduled for seven days. And, because of a raging dust storm at the planned landing site, we got an extra day. A real blessing. With no tests to do, we had a free day on orbit. And ended up with eight days. STS-4 planned and flew seven days, landing on the fourth of July with President Reagan out there to watch. And then we got into operational flights of which there had been a lot. Something over a hundred. The last flight to fly, the return to flight was STS-114, but the number system went through a couple of phases. There have not been 114 flights. I don't know how many it has been, but there had been a bunch. I will talk about three, well, more than three flights, but the ALT flights. If you have to have a crew patch, that is a major hurdle that you have to overcome. When you are assigned to a crew, get the patch designed and then get it approved by upper management. Part of the OFT, STS-3 in 1982 and finally then an operational flight 51F in 1985. Prior to any of these flights, I worked into a dream job for really systems engineering, I guess, and for a pilot. I had been to test pilot school. I was intrigued with all the airplanes I flew with a cockpit design and was very aware of the flaws of cockpit design. It seems like sometimes engineers lie awake nights trying to make it hard to operate subsystems. I got in at the beginning of the orbiter crew interface and became, before it was over, sort of the Czar who was responsible to sign off all the drawings, lots of reviews. It was a great responsibility because I was immediately and early into subsystem design because you have to know what the subsystem does to make any intelligent choice of what the controls and displays should be. This is a view of, not the Enterprise, but probably, I don't know whether it is a simulator or the real airplane, they look alike, but one of the orbital capable shuttles. This is like the little old ladies always say when you're out on display for Armed Forces Day and look at all the things, how do you remember what they all do? Well, that really is a challenge to make things straightforward. And I became painfully aware, especially later on when we had a lot of experiments coming in, that engineers in their little ivory tower building a system in the lab are so totally, personally familiar with how their stuff works that it doesn't bother them that the switches are unlabeled or labeled illogically. And they bring that all in and want to put it in the orbiter. And when the crew says wait a minute, I have to remember, before I turn on switch A, switch C and D have got to be turned on in this order or the whole thing will blow up? And they say oh, yeah, that is the way it is. And they know it so well personally. And, yet, when you are overwhelmed with a whole lot of experiments, I am sure you ran into it on your flight, that all the stuff that is just totally familiar to the guy that invented it becomes a challenge when you are faced with a whole lot of them and a limited amount of time to learn it. And so, standardization of what the scheme, especially in the software. While there are a lot of gadgets, in fact, if you count all the switches, gauges, circuit breakers, upstairs, downstairs and the mid deck, there are about 2,100 total in the orbiter cockpit. But the real challenge is what shows up on the screens here. So the software was a bigger thing in making them all play together. Here is a higher view in the overhead panel above your head. And the forward cockpit has a lot of other switches. An example of what I am talking about, this array of switches right here controls the reaction control system valving and then the orbital maneuvering system. Back in Apollo, which I worked on when I first came to Johnson Space Center, I learned, while lying many hours in the Apollo crew simulator, that that had the worst cockpit every designed by man. As an example, it had a helium pressurization system to push the propellants for the reaction control jets out of the tanks and then the valves that went to the various arrays of thrusters all around the command module. And one would think logically, if you have something to turn on the helium, you label that helium on/off. And then the manifold, the next branch in the Christmas tree manifold would be system A versus system B or something like that. And, in fact, it had names like that. But they put the switches in a long room and labeled them A through H, right there on the panel. No clue as to what you were throwing, so every move you made in the cockpit, some of these things were critical, required you to either be a metal giant or open a checklist and say to pressurize system B, I have got to throw B on and then A next and then H last or something like that. Obviously, unacceptable. It became my career and mania to try to improve that. The first orbiter simulator built was called the OAS, Orbiter Aeroflight Simulator. It was on a moving based platform like the standard airline simulators you see today. This is Fred Hayes and I sitting in the cockpit. This one was built originally to be the Enterprise. And the Enterprise was OV-101 in the scheme of things, a numbering of orbiters as they were built. 101 had only the systems it needed to fly the approach and landing test. The plan was to retrofit it later to make it into orbit capable. But before the ALT program it had just what you needed and only that to fly in the atmosphere very short flights. But this is our first chance to look at what we had and what we were getting into as far as pilot concerns. Now, I guess you have had all the subsystems, right? You were all completely briefed and experts on subsystems by the people that had preceded me here in the course. I will give you, though, a quick review here, the avionics system. The Shuttle is build with inside the outer mole line as the pressure vessel that is roughly back to the forward bulkhead of the payload bay and is imbedded inside basically aluminum structure with a thermal protection system applied to the outside. And most of the avionics are in racks right up here, right in there with you in the cockpit on the middeck. The stowage lockers are aft of the racks full of black boxes and lots of wires. And the other place there were avionics is back here just after the aft bulkhead of the payload bay. And there are some areas where they put items like rate gyros and accelerometers. A lot way back. From a systems engineering standpoint, Fred Hayes and I were out at Palmdale where they built all the orbiters. It seems like the testing always happens after 2:00 AM, tests would run around the clock. And we were out there way after midnight in the cockpit participating in the first time they were going to close the loop between the rate gyros and the flight control system which is contained back up here in the nose and the general purpose computers. The whole orbiter was suspended on some big airfield bag so it had compliance to move. And the hydraulic system was on powered by a facility hydraulic source. The elevons were powered and the rudder speed brake was powered and the process let us down for the very first time that we were going to close the loop between the software up here and the rate gyros particularly and accelerometers mounted in the back. And it was a milestone. And we had people stationed around the back to see if anything spit out hydraulic fluid or whatever. Anyway, we went up to the glass shield and pushed the button to go into CSS, Control Stick Steering, which hooked the stick up now to the flight control system. I will never forget. We pushed the button and a rumble started. And the rumble built very rapidly to a violent rumble. I mean we were being bounced around the cockpit. This is 150,000 pounds of airplane dancing on these rubber bags. And it didn't take us long to say this doesn't feel good. We pulled the button that downloads back to direct control so there is no feedback. And the upshot of it was that these rate gyros are mounted on this flexible bulkhead. And that had been taken into account properly. And so there was a structural resonance that was just diversion. In spite of all the Grounds tests down at Downy and the Iron Bird mockups and everything, when we put it in the real airplane it tried to jump off the supports. And Fred and I were in the cockpit, our eyes were big, and we called the control room which were people back in an adjacent room. It seems like most spacecraft tests, traditionally, are done with engineers all locked up in windowless room, no view of the real hardware. Down at the Cape they are miles away when the spacecraft is either out on the pad or in the main checkout building. And so they said no, the procedure says this is OK and we want you to re-engage. We tried one more time. And this time the guy stationed in back that were watching said this doesn't look good. They started hollering on the loop so we pitched it off. And we went into a raging argument. We need to complete this test, the engineers were saying. And we were saying we don't want to break something. And they got people out of bed down in California, controls engineers. And so, it was a memorable night. The resolution was finally a redesign of the mounting area back there and reanalysis of the vibrational modes of the aft bulkhead sorted all out. Here is what we had for a crew interface. You saw in the earlier picture, upfront three CRTs, monochrome, green, it was either green or nothing on the screen, and we had two keyboards, three CRTs. There was always this little concern, when you are punching on a keyboard, you want to be sure it is selected to the CRT you think you are doing something on. Another marginal design, but that is what we ended up with. You notice we have a hexadecimal keyboard here. We have some strange keys called item and electric and ops which had to do with this truly unique way you cause things to happen through software. And lots of things were critical through software. And then this rather dim green screen. This was way before the days, I guess, Bill Gates was still here at MIT or maybe even hadn't registered yet. I don't know. It was way before Windows 1.0. And so it seems almost comical now when you compare it to even modern airliner crew interface with glass cockpits, but we were breaking new ground here. And it, even at the time, seemed antiquated because that is all they were willing to embrace in the way of computer control and design. And it was unique. And it causes lots of headaches and delays. The big thing about the orbiter with its data process system, the decision was made that everything is going to be done with these all powerful general purpose computers in which there were five in an array that worked together. Flight control, system management, navigation, inertial subsystem control of everything. And so, the result was the software loads, as they were built, had lots of flaws when they came down, yet we couldn't fix them. We had cases as dumb as a display that showed the Freon loop A pump on. And, when it got through the entire software belt, it was backwards. It would say off when it was really on. Seems like a simple fix, right? Go back to the programmer and rewrite the code. But we couldn't do it. We had to live with it for a long period of time through training until another whole load was built. Because the load that would fix this dumb little bi-level mistake was also the one that steered you during ascent. So everything was frozen and there was great fear of changing anything that would ricochet through to something truly critical. And so, even when we got to STS-3, we flew with a book about this thick of program notes that told you, line after line, what was wrong, what was backwards, what was a trap. And really a big challenge to the crew to embrace and live with because there just wasn't time in the program to build another load, check it out through all the different labs that had to certify it. That is load for modular software where you can change something here and be assured you are not bollixing up something else in the same machine. OMS, RCS. These are the two pods. On either side of the vertical tail are a couple big OMS, propellant tanks, oxidizer and fuel hypergolic. We didn't need any ignition system. As soon as these came together in a thruster you had thrust. And there were, I think, 44 main thrusters. Here are four yaw jets firing out to the side. S&B pitch jets. The same thing repeated on the other side. And up in the nose are the forward RCS. They had jets that fired up and out to the side and down. And I mentioned the controls in the cockpit, which we did. One of my great successes was getting the orbiter panels to be arranged in a plumbing layout so that you could see what you were pressurizing when you turned on the helium for a given let and that sort of thing. Helium tanks are what pressurized in a really cleaver system of OH control. That is when you are in zero G and you have propellant floating around randomly. And you turn on the helium to push it toward the outlet. If the outlet is uncovered, the helium is going to squirt right out. But they had an elaborate system of surface tension kind of baffles that kept and trapped fuel near the outlet of the tank so that when the thrust came on and all the propellant went down where it should, it sort of recharged this chamber at the bottom of the tanks to keep it flowing smoothly and not lose all the pressurization. I remember my first impression of what reaction control jets would be like was based on science fiction movies where you would see the spacecraft out there and there were little squirts of jets that nudge you around. And we went out to the Ground test facility at White Sands on a fieldtrip out there where they actually had the forward RCS setup, and they were going to do real firings of the main jets out there. And we were probably a couple hundred feet away from the test setup. We were out there waiting for this sequence of jet firing to start on a test. And the first firing of one of the main jets, which are right up around 900 pounds thrust, was just this short pulse. And everybody went about three feet off the ground. I mean it was like you fired a howitzer. It was just stunning. Wham, wham, and it just blew you away. And the realization of we are going to be in the cockpit here, and these things are firing right outside the windshield. They did. In space, the ignition transient ricochets through the structure. You can hear this kind of bombing effect. But once they are on, if it is a long duration firing, it is silent. And the same way visually, you can see a flash when the fuel is led a little bit in front of the oxidizer to make sure you don't overheat something. And so, there is incomplete combustion at the ignition. You can see a flash go out there. But what is on during an OMS burn, for instance, when these OMS engines are firing and you are looking back at the aft, you see the flash and they are on and they are pushing and you can feel it. But otherwise invisible is the way I remember. On the other hand, there are vernier jets, little guys. I don't know if they are shown here. But there are little 25 pound thrusters or something used 98% of the time on orbit. You really are doing that kind of thing with the vernier jets. And you cannot hear those or see anything when they are going off. In fact, we got everybody quiet and kind of held onto the walls just trying to see if we could barely detect when a vernier jet fired physically in a cockpit. Interesting. The orbiter is one giant heat transfer machine. Lots of calories of heat energy pumped around from one end to the other. And so, there are water loops within the cabin that transfer the heat to Freon loops. The fluid is pumped through the radiators to reject heat. In spite of all these heat rejection systems then there are heaters everywhere, whole banks of heaters to keep stuff from freezing. Then for the landing and takeoff phases, there are flash evaporators that flash water and/or ammonia. When you are down in the atmosphere you use ammonia to cool the loops. And, of course, the payload bay doors are closed. And it turns out STS-3, a major test of it was test all these loops and how the structure responded to long durations of given attitudes with the sun shining on one side and cold space on the other side and how the structure would distort or hopefully not distort and how all that system would work. As it turned out, if you like lots of redundancy, this is probably the weak point I thought in the whole orbiter design, we've got three engines. We proved that you can get there with only two. But the Freon loops, there were two redundant through the radiators. And if one Freon loop pumped quick you are in a severe emergency. That means stop everything and power down severely. Turn off all the computers except one, get in a proper attitude and go into a panic reconfiguration to come back and land. Originally, the design had three Freon loops. It could use one and go on with no concern. But, as it turned out, the heat loads were so high and the weight criticality determined that all we had electrical power to run were two loops. And so we ended up with a single Freon loop which fortunately, as far as I know, never failed. But if it had it would have been a crash deorbit landing under severely powered down conditions. While it is kind of mundane and people don't think about it as a primary system, the thermal control really was critical. Payload bay doors, this is a busy chart but indicates these are really complicated. 60 feet long and something like 120 little motor driven latches to latch them closed. And you don't just go chunk close like the bomb bay on a B52 and it is closed. To close the payload bay doors you get them close and then the latches along the bulked, all in a zipper fashion, have to sequentially close. And then you go down the center section to latch the two left and right doors together. All software controlled. And there was a lot of concern that we address on STS-3 particularly about whether this is all going to work. If you have been floating around with these pointed to dark space, would they distort to where the zipper scheme would work? We worried about it enough that part of our emergency training, contingency training, a lot of time was spent underwater in the neutral buoyancy tank looking at a system going out EVA with a series of come-alongs, you know, the kind of things you use to pull the motor out a car, that kind of thing, that we could go down there and hookup and latch the doors shut to actually manually get them shut and then latch them shut with these. Fortunately, that has never been used. And this complex system has worked good, but it was scary the first time we flew it on STS-3. That was a big concern. What I have got here is hydraulic system. Hydraulics are hydrazine powered turbines that run at some ridiculous RPM, like 200,000 RPM to drive hydraulic pumps back here in the backend. And then they are crucial during launch because they have got to hold the elevons in position. But they also have to provide the muscle to gimbal the main engines and keep you steering straight during launch. During entry they are what you use to fly when you get into a dynamic pressure situation. Control the rudder speed brake and the body flap. The body flap is a big surface that sticks out underneath the main engine bells and is a slow moving trem device. The body flat is always moved. You go through this mach 25 to mach zero envelope. And the trem conditions necessary with these big elevons varies a lot. So, to desaturate the elevons and keep them basically faired with the wing, the body flap is your trim device. And it is like this row of tables long and this wide. I remember asking to see the motor. It is driven by a whole lot of mechanical advantage by a hydraulic motor. A guy took me around. I couldn't find the actuator for the body flap. He showed me. The motor was this big around and this long, a little hydraulic motor. So you can do anything with mechanical advantage. But it didn't have to move very fast. Finally, on the system pictures here, the RMS. Hopefully, you have heard about this. It was built by Spara up in Canada. The Canadians main contribution to the orbiter program. A pretty magical device. It can go on either side, but for our flights mounted on the left-hand side or the right if you're looking out the back windows at it. And it had joints logically called the shoulder joint, elbow, wrist joint. All electric motor driven. But the interesting thing was a control. You had hand controllers mounted in the aft part on the right console in the back where you looked out. And you could work in the mode where you actually drive in the end left, right, up, down, in, out without regard to whatever joint was done. That is all resolved by the software. And worked well. The end effector was a cleaver kind of a hallow cylindrical device. It would rotate inside and three cables that would be curved around the periphery inside this cavity when activated. I put this over a post on whatever you wanted to grab onto with a knob on the end. You go over the post and then rotate the inner barrel and the cables would wrap up and grab onto the post. And then they would retract in to rigidize. And that was the grabber on the RMS. And we flew this on STS-3. I will show you later. Anyway, that is the subsystem review. Let me show you how things went during approach and landing tests. Now, let's see. I have never figured out how to imbed video and PowerPoint so I am going to be doing it manually. Any questions while we are waiting on this to come up? Well, this is the desert around where I live and a Gila monster and a Joshua tree to set the scene. And here you have OV-101. The numbering system, as it turned out, is kind of interesting. They built OV-99 as the structural test article. It was strictly built to be in the lab and do all the structural testing on it. 101 then was the first orbiter build, the Enterprise, being hauled from Palmdale across the backgrounds and the desert roads to get over to Edwards in these scenes. And 101 was the ALT airplane. You can see kind of phony looking RCS. It has, as I mentioned, only the systems that you needed to fly atmospheric flight. This was a big thing getting it across the country. It had a Pitot boom on it. It has just simulated thermal protection. Styrofoam painted to look kind of like they thought the space vehicles would look but wasn't real. It was put in the mating and docking device which is at NASA Dryden where I work now. Hoisted it up. And then the 747 and 905, the first Shuttle carrier aircraft, was pulled under and they mated them up. I remember flying out to Edwards and seeing this unlikely combination. And the first time I saw the two together, I thought they cannot be serious. But then I realized I was going to be in it. There were 13 total flights. This is a taxi test. When you have an aerodynamic test you can sneak up, and so you do baby steps. This was just a high speed down the runway to see if it would rotate and if anything would shake alarmingly. And that will look good. Preparations proceeded for the first of the captive inert flights. This is Fitz Fulton and Tom McMurtry, both real good friends, and they were the crew on the 747 for this first milestone flight. A lot of people were out watching and wondering if it would fly, which it did very well. And off it went. You notice a longer front attached structure there. And the orbiter is purposely on there at angle of attack to produce lift. I flew a 747 for ferry flights now and to haul orbiters back to the Cape when they land at Edwards, as the last one did. And the nose, that front bipod is much shorter so that the orbiter is down for less drag for the combination. But this setup here was so that we could get the orbiter off the top and not the tail. There is a rumble. The crew noticed a shaking. It is still the case when you fly. These vertical fins were added onto the horizontal stabs to increase directional stability because the orbiter blanks a lot of flow over the normal vertical. In fact, they overdid it a little bit. There is too much structural stability which has resulted in the weird situation. Your cross-wind limit, when you have an orbiter onboard, is greater than when it is not because you have so much directional stability and a crosswind. There is a strong weathervaning and you run out of normal rudder without an orbiter, so you are good only to 15 knots crosswind with the orbiter on. The limit is 20 knots. And it is a good limit. I have flown them both ways in cross winds. And, indeed, at those numbers you run out of rudder as you land and are rolling out. The strong weathervane intensity is leading you out this side of the runway. Anyway, that looked good. And so I came back and we had a big post-flight party. ALT was great for parties. We had 13 post-flight parties. And, at the same time we were doing the ALT flights, we are developing a Shuttle training aircraft. This is Gulfstream II with big side force generators on the belly. That is an airborne simulator. The left seat is set up with orbiter instruments. And the right seat was the standard gulfstream cockpit that had flown thousands of dives at the ground in the SGA preparing for the whole idea of first time for sure unpowered landing that you have to do right the first time. And back in the simulator here for lots more runs. And it was a great time because everything was brand new, very interesting. This is a camera and an actual model. This is before the days of computer generated video. It flew the little camera down to landing. And we learned a lot about [NOISE OBSCURES] characteristics. One that we really wondered about, when you made a lateral input to roll the orbiter in the simulator, it would bang you. It was this lateral lurch, we call it. It would jolt you sideways. And we thought this cannot be real. It doesn't make any sense. No airplane we ever flew does that. We squawked it. They came back and said the equations are all worked out so we live with it and thought it was just an artifact that snuck in there and didn't worry about it. Now, the captive-active started where we actually got in and cranked things up. On the second flight, I was chasing in a T-38. And Engle and Truly were in the cockpit. And I noticed a shiny look on the side. That big X on the CRT is what happens when the computer that is driving that CRT quits. That is sort of the panic symbol when the X shows up. Anyway, I noticed a leak, as it turned out to be. We had that severe hydrazine leak. Hydrazine is bad stuff to have leaking. And one of the APU supply tanks let go. Plus, they had an over temp. We found things that were wrong that made these captive flights worthwhile. If we had just gone and launched off on the first one, it could have been more exciting than it needed to be. We had five of those. And Fred Hayes and I got the odd numbered flights, one, three and five. Five more post-flight parties. And then we decided we were ready to go. Well, this is the last of the captive-active flights. The scheme by which we plan to get off of here and not take off the tail of the 747 was that the 747 would go as high as it could go. It could get up to around 27,000 feet with engines over-boosted. Pratt & Whitney said you could go this long with extra power. And then nose over and speed up to 240 knots. It was climbing maybe to 190, 200 knots. With a little downhill push, we got up to 240. At 240 the SEA pilots would go to idle power and air brakes up to put drag on the carrier. At that condition of 240 knots and the angle of attack of the orbiter, it was actually lifting more than its own weight. So the result is we really dropped the carrier, as it turns out. There is three-quarters of a G difference between the two. And so, we got a lot of use. For some reason Fred's left shoulder, he is in the left seat and he mashed the separation button after Fitz on the carrier aircraft hollered "carrier ready," that is they were back at idle with the speed brakes up, pushed the go button and bang, all seven explosive bolts would blow. Control Room was in Houston, strange enough. We are talking to people back in the old JSC Control Room when we are out at Edwards flying these flights. It was just like they were there. And we were coming up on a condition. And this was in August of '77. All the ALT flights happened in 1977. You notice there is a tail cone on here. The tail cone was flown on the first three flights. That makes a big difference. It smoothes the flow s that the buffet on the tail, the carrier aircraft was less, and it just about doubled the L/D of the orbiter. We are going to arm. And we had two chases, one off to the right and in trail separation. Just like the engineer said and the load cells that we had on there, testing exactly which was the thing tugging before we did it, said we could do straight up. This is slow motion. Nothing is leaking. The vortex is out at the wing tips causing condensation and away we went. And simultaneous with this bang that shutters through the airplane with all these explosive volts a big X on the CRT in front of me. We had cue cards and we had practiced this. My job, while Fred flew, he actually got a vertical clear from this chase pilot and then rolled into a bank and a lateral clear from the guy that was chasing from behind and knew that it was OK to push over. Because we are only now at 200 knots and we wanted to get to 300. And it took a considerable pushover to get up to speed. Meanwhile, I am pulling circuit breakers on rate gyros and turning off accelerometers at our preplanned procedure to accommodate flaws in the redundancy management. When you lose one computer you also take out part of the sensors in the flight control system. And, to be sure that a subsequent failure wouldn't put you in worse shape, it took about a minute's worth of manual reconfiguration on my part. And I kind of missed the whole first part of the flight. When I turned around I realized hey, this thing is flying good, it is smooth and is on speed. And Fred was flying. We flew a rectangular pattern out of a downwind leg here as we nosed over. And I got my chance to roll into a left 90 degree turn and fly base leg. And, as I put the stick over to roll, we got this big lateral arch just like the simulator said. It just stunned me. Son of a gun, they were right after all. It was just the nature of something flying at high alpha and rotating about a stability axis and the cockpit gets slid sideways. It has big elevons so it flies like a fighter. It really does. And you are doing it all with a little stick that doesn't move much. Anyway, we came down final at 290, I think it was, flared out. My job was to put the gear down, a critical function. And we are landing on lakebed 1-7 on the dry lake at Edwards which is something like ten miles long, so we have pretty good margins there. And Fred took the airplane back from ALT and I got to fly base leg. But we touched down at about 185, I think it was, nice and smooth. It was beautiful. The speed brake comes out to help cushion the de-rotation, nose gear down and he raised a little dust as he rolled to a stop. So it was a good day. Now, we had a really good post-flight party after this one. And see the rudder speed brake flared there and the elevons fold up. And so, now Fred truly did it again. A couple weeks later or thereabouts they got their turn and they did much the same flight, repeated it. Oh, one thing. You see the Pitot boom out there. The Pitot boom is strictly on the Enterprise, put out there to get good air data out in front of this big blivit of an airplane which is hard to get good measurements. Let me get the next one going here, if I can figure out how to get out of this. The excitement came later. On STS-1, I looked out there when were on final, I had to look out and look at the Pitot boom, and it is going through an arch of about three feet. It was built with the perfect resonance of everything else with the airplane, and it was just a blur out there going back and forth. And I really thought it was going to break off. Was that your only Pitot source or did you have the normal ones [OVERLAPPING VOICES]? Good question. Somehow we had at least inertially derived ones. Everything looked good. And, actually, it still put out good airspeed, even though it was a blur. And I think the beta averaged out. Anyway, it wasn't a problem we noticed other than visually it looked like it was going to break off. They changed and stiffened it up so it wasn't a problem on subsequent flights. Now, you can see here we are at free flight four now which was the other crew's turn. The tail cone is off and our final pressure glide slope with the tail cone on was 11 degrees. With tail cone off it was 23 degrees, halves your L/D. So you really are in a steep dive. Normal ILS into Logan out here would be 2.5 degrees so you are coming down gangbusters. And it is even worse in ALT than it was in the orbital missions which were coming down with the same configuration but much heavier. Heavier you've got more gravity working for you and you can fly shallower. It doesn't seem to figure, but that is the way it is. So 19 degrees is a normal return from orbit. Final pressure glide slope we were up in the 20s. Kind of catching up a little. One of our jobs on the flight preceding this was to try the braking. We just let it roll out on the first couple flights. They wanted to do brake tests. And Fred jumped on the brakes after we touched down and another resonance problem, interaction between the structure and the anti-skid, and I thought it was going to break the airplane. It was just violent shuttering, shaking, everything rattling in the cockpit. And I hollered to Fred, get off the brakes, we are going to brake something. He said no, the card says we have got to do max braking. I was pleading with him to get off the brakes, which he did. Easy fix. When they flew the next flight here they did hard braking, and it was smooth. They went in to change the resister and the feedback electrons, and that did it. I mean it was instant fix. So there still is reason to do flight tests because surprises happen. Now free flight five, it turns out there was a little brake here. We are back at Houston and Prince Charles, who wasn't married yet at that time, came by on a visit. And we gave him a ride in the simulator. He had some flying time. And he got into a horrendous PIO. I mean he was out of control and crashed in the simulator. And felt bad. And we said that is because you're not used to the stick and everything. And that was his tour. Now, for this flight, he was actually out along the runway. They had him out there so he could watch. The objective here was to land on the concrete runway, put it right on the line, there is a white line 5,000 feet down, and Fred was really working at it, putting in a lot of inputs. Look at the elevons going there. You see them? And he is making roll commands. And so we logged a couple landings. And down and rolled to a stop. Afterwards, we called out and he came up to say hello. He said oh, you made me feel good. You guys did as bad as I did. There he is right there with his binoculars. Well, that scared everybody to death. It looked worse from outside than it did in the cockpit. And the flight control flaw that we found, though, was serious. You've got elevons that do both pitch and roll. So, in the software, when you are asking for both pitch and roll at the same time, it has got to decide which one do I move? This is just a supposition of what would come. The software had to give priority. And they decided to give priority to pitch. And roll was taken second priority when you had to limit the commands to the elevons to within the capability of the hydraulic system. The result was a lag in roll response when you are working pitch hard. And the lag was up around two-tenths to three-tenths of a second. You may be aware if you studied flight control systems. Any kind of system that has a quarter second delay between input and response is asking for a PIO, Pilot Induced Oscillation. And we had a big time in roll. Fred was clanking back and forth to stop and roll trying to level the wings out there that first skip. I heard the controller banging over there. And I suggested if you get off maybe it will damp. We're doing this and, sure enough, that is what he did. He stopped the inputs, the airplane damped right away and then it went OK. But it was something we had to fix, obviously. Here is a picture just a micro-second after liftoff on one of the last two. Well, there was a decision with a lot of debate about do we go back and fix the flight control and fly some more ALT? But this is a huge production and it was costing time and we weren't getting into orbit. A decision was made now we will do it in simulators and in-flight simulators and fix the problem, but press on. That was the end of ALT, at the end of which, when you do flight tests, you talk about opening the envelope of an airplane. Well, the envelope of the Space Shuttle is 400 nautical miles altitude and mach 25. And in ALT we got the four miles and 0.3 mach. It is really down in the lower left corner, but worth doing. Test results. I mentioned as we went we had that APU fuel leak. Fixed it. Didn't come back. The buffet lifter drag was right on what we expected, no surprises there. Handling qualities were good, even with the lurch. It was not a problem. I mentioned the Pitot boom, the anti-skid. SCA did the job, although it struggled to get up. With the tail coming off, it could only get to about 18,000 feet. So this was not a good program to build up your flying time. It was about a total, in three flights, of about 12 minutes of flying time. And the biggie I mentioned was the handling qualities and the PIO tendency that we fixed with lots of studies later and changes in the way the control equations were written. And, as a final thing, they did some more flights with the nose lowered down and determine what the ferry flight performance of the combination is. I, later after flying in space, checked out on the 747 and still fly it on the ferry flights. And it does the job. It burns lots of gas. I figured out that the combination across the country, the mileage is about 300 feet per gallon, so a football field per gallon of fuel. 40,000 pounds an hour is the field flow. It goes about 1.5 times its own length when we get on the gas, but it gets there. I don't have to buy the fuel. A lot of people said wasn't this scary, ALT? Actually, from a risk standpoint, we had ejection seats. If anything had gone wrong, anywhere along the line, we could have pulled the handle and jumped out. The scariest part of it was when we got in, and during the captive flights, we would just walk up a stairway and crawl through the hatch. And the same way getting out. But after the captive active flights, we would land still on the orbiter. And they had this cherry picker to get us out. Now, the situation here is it's a round hatch hedged at the bottom. They only wanted on person at a time on the end of this thing. You open a round hatch and then they bring this up, the guy on the ground. And he doesn't want to get too close and ding so he leaves about this much of a gap from this round hatch which is 60 feet above the ground that you have got to crawl out on your knees, then stand up and then make the leap across the thing onto this wobbly cage up there. That is how our captive actives went. Where you wearing flight suits for all these tests? Yeah, we were wearing flight suits and helmets like you would in a 518 or any fighter. Not pressure suits. We didn't have a severe cabin pressure risk at 25,000 feet. Let me get into the full screen mode here. I put in some thoughts about what is different when you test an aircraft versus a spacecraft. With an airplane you can do little baby steps, incremental tests. You can do static runs of the propulsion up to the full power in the airplane itself. Then you taxi it slow and then faster and faster down the runway. You can rotate the nose a little bit. The first flight you will fly slow and leave the gear down and then land it soon and check everything. And you could hold off for a perfect day to do it. And then you go faster and faster to expand the envelope. If anything goes wrong you can peel off and get back on the ground quick. And, as I mentioned, you can always pull the handle and bail out if things go really bad. When you have a spacecraft it is all or nothing. You have got to use the propulsion at its full power. All the critical systems and subsystems have got to work. You cannot make a quick abort. Long delays like days are sometimes required to get back to the conditions where you can make an appropriate landing. And the weather could turn sour at the time. When you are going to flight test the spacecraft you have got to have a lot of redundancy in the design to allow for the bad day that has to carry it through in a considerable amount of time. You necessarily have got to test everything to the limit, wind tunnels, CVD, thermal vacuum because the environment is lots more stressful. You have got to have a lot of instrumentation so that you can tell what did go wrong or be sure that everything went right. You are talking about an army of controllers in a control room to pull it off with a complex system like the Shuttle. And lots of simulation to get everybody trained. A biggie is to verify the software. I mentioned the software is guaranteed to be wrong on the first release and several subsequent. It is just the nature of building software. And so getting that checked out is a major one. Procedures. When we flew the orbital flight, the stack of checklists just laid on top of each other was about this high, for 51F, and it weighed 210 pounds. It was called the Flight Data File. And then lots of time and expense getting everybody really ready to go. And being sure that when you're going into an unknown part of the envelope that the margins on the flight control are adequate. So the surprises and the aeroderivatives that hit you can be accommodating. I have rambled on a long time here. We can take the five-minute break, I can answer questions, however you want to do it. Maybe it's time for a stretch. Let's do a two-minute break. These people are tough. All right. Break is over. The next assignment for me was being put on an orbital flight test, and specifically STS-3. A two man crew, Jack Lousma, a Marine, and myself from the Air Force, we were in pressure suits, you will notice there, and on ejection seats in the Columbia. This is OV-102. 101 was the Enterprise. 102 was the Columbia. And our countdown went smoothly. This was in March of '82. And this is a signature moment in your life when the SRBs light. I mean it looks smooth and nice as we are flying through a cloud here on launch, logging weather time I might add, but it is rough and noisy and rattley. And the acceleration is right away, and it builds up to 3Gs. When the main engines are throttled back, the whole 3Gs. And so, it is no doubt you are on your way somewhere really fast wherever the solids want to go. Everything worked good right up to MECO. And the external tank, as you saw, drifted away. And then here come the first order of business, opening the payload bay doors so we can start rejecting heat with the radiators that are mounted on the inside. We are tailed down. And as you watch here, we are going right over Los Angeles at the time. This is just north of LA. You can see LA. Sorry, this is Santa Monica, LAX and Palos Verdes right there. Anyway, the first thing we had to do is get out of Theodolite, that is a sighting device that surveyors use, and take a daunting number of readings on little targets that were pasted around inside the payload bay and on the doors to measure where they were. And we did that through the flight all the way along. It wasn't fast enough. Out in front of the nose there were some dark patches. That is where tile were, white tile, and fell off during launch. They actually found some washed up on the beach. Fortunately, none of the black tile on the bottom fell off but we did lose some on the top. Zero G is really one of the delights. There are two really good things about flying in orbit, weightlessness and the view out the window. And that is like nothing that you experience, even flying high-performance airplanes. We had the RMS cranked up. That was my job as RMS operator. And we had a package in the back, the plasma diagnostic package to grab and move out there. There are some things that show you the housekeeping area. In the corner there is the john. And long duration spaceflight exercise is important. It is really not a big deal on a seven-day flight. Jack is a Marine, as I mentioned. He has got to have his daily ration of pushups, so here we go. How about a one-handed pushup, Jack? How about a no-handed pushup? This is a quick summary. We went our seven days. And the lakebed at Edwards, they had a really wet spring, was unusable, so we went to White Sands, New Mexico. The first day, right as we are about to light the OMS engines to start deorbit, they said hold off because this terrible dust storm is going on. And then we waited a delightful day with nothing in the flight plane much to enjoy ourselves, and then came down the next day. Now we find another gotcha in handling quantities here. Right here Jack thought the nose might be coming down too fast and tried to stop it, and ended up doing a little wheelie. Subsequent analysis showed that the whole response of the vehicle changes when you are down on the main gear only. And nobody thought of that. It would seem like, well, they are worried about pitch in the air but not while you are rolling on the main gear trying to de-rotate. So it resulted in more software changes. Another thing we learned, they were pushing for auto-land. We flew the whole turn onto final and down final hands off in auto-land. The program wanted to take this out of the hands of the crew, so here on the third flight they had us sitting there watching the airplane fly down to pre-flare. And then the first chance Jack got to grab the stick was at the last minute to do the flare and landing. And that was dumb when you look back, really dumb. And so, now all flight commanders, if it has been auto down to 40,000 feet where you go subsonic, we will fly manually all the way down to get a feel for the airplane. It makes a lot more sense. That is the way flights are done now. Here is where we started from orbit. This is how Cape Canaveral looks. Right here is the shuttle landing strip that is down there. You can see it. And the launch pads are these two dots. And so, that is where usually a shuttle flight starts and ends. Here is a picture of our payload bay on STS-3. And we did have a payload. Previous crews had pretty much empty payload bay, but we had an environmental measurement thing, a lot of instrumentation. Then this PDP, Plasma Diagnostic Package that we actually had something to grab with the manipulator arm, as you see here. I looked around and found, I don't know if you can recognize this, but that is Cape Cod back there. A picture of MIT. Not a good picture. There have got to be lots of better ones. And here is where we ended up, the White Sands area near Alamogordo, New Mexico. What we learned, this is a pretty cryptic summary. Training was a real problem. The first two crews that flew STS-1 and STS-2 had all the attention of the training people in the simulators. They had priority, properly so. We, on the third flight, had low priority and really struggled. And what we found, when we got in the simulators, is when they didn't work right nobody could explain why. Many times we try on ascent and crash and burn. And you always were scratching your head is this real? Is this the way the orbiter flies or is it some flaw in the simulator? Early on you are developing not only the orbiter but the training facilities. And the people didn't understand the system. We had more exposure from ALT to subsystems than the people that were supposed to be the experts. It was a group learning process and a long way from what happens now when crews go in. And they get the straight word right from the beginning on how things are. The tiles fell off. Not good. They changed the bonding scheme, improved the quality control and, fortunately for the program, no critical tiles fell off. But that was alarming. We looked out there, we reported it, took pictures of it looking at these gaps in the system right out in front of the windshield. But Ground said don't worry, that is a cool area during entry. Entry is at 40 degrees angle of attack so it is cool on top. They were right. Everything was fine. Another tile thing was after the flight, actually, delay that. It was really more after the next flight. I mentioned how the ride is. The first two minutes were rough and exciting. The next six or seven are unbelievably smooth when you get on the main engines, and then more vibration that you are getting sitting in the chairs now. And it is just a steady relentless push. It is just a spectacular right. But you are back in the seat. Had an APU oil overheat during that 3G part. Actually, about two minutes before MECO, Ground called and said we needed to shut down one APU. We were up past the point where we could live without all three APUs running. I had a chance to test what I worked on years previously with the cockpit design. You are concerned about visibility when you are squashed in the seat at 3Gs and access. And the APU switches, we had to put them down here. And, I remember worrying specifically, if we have got to get to the APU switches, the guy on the right seat under 3Gs, can he lift the helmet and look over there and find the correct switch? And you do not want to shut down the wrong one, one of the good ones. And it turned out, I guess with the adrenaline lifting this heavy helmet at 3Gs, I did it without even thinking about it and went right to the switch. So it worked. General habitability was good in the orbiter. The first time anybody lived there for eight days. A good way to think about living in the orbiter, think of it as a camping trip. You go on a camping trip you don't worry about hot water, showers and all the niceties of home. You get in that frame of mind and it is fine. The food is adequate, the facilities are OK, although in our case the toilet ground to a halt. It is a drum that rotates to centrifugally sling all fecal material out and contain it. And it ground to a halt. We were in a real camping trip for a while on that, although it worked out. The arm worked great, RMS. The main jets I mentioned earlier. Of course, you don't use the main jets much. It would be hard to sleep with them booming away, but you use the Verniers most of the time. Verniers are critical to smooth operation over long periods of time. We spent a lot of time, for instance, tail sun. For like three days we put the tail right at the sun and stayed in that inertial attitude. And so it cooked the backend while the front end of the orbiter is cold. We took all the Theodolite measurements, opened and closed the doors. All of that worked fine. The systems handled it. A lot of it was ground analysis. And how the temperatures were, were extensively instrumented. And we did notice a strange thing. Not strange but it became apparent. When you are in orbit, when you are on the sunny side of the earth, as soon as the sun comes up it is high noon bright, but there is no atmosphere around to diffuse the light. When we were at tail sun, it is hidden behind perfectly eclipsed by the aft structure. And so, there is no sun ball to be seen anywhere, even though it is bright sunny from just the reflections of the structure you can see out the window. I noticed, looking at the radiators, which are very, very smooth concave surfaces out there and shiny silver colored. It looked like there were bright diamonds all along the surface when we were tail sun. And I finally figured out it was just little specks of dust on the radiators, which you wouldn't even notice normally. But exactly tail sun, the sun's rays are coming right down exactly tangent to that surface. And the least little thing on it would flare. And interesting effect which took me a while to figure out what all these bright spots on the radiators are. Entry on STS-3 was done to an about 1:00 in the morning landing at White Sands, New Mexico. We started the entry. Halfway around the world it is dark, and most of the entry was in the dark. The plasma light show that happens, as you get down in the atmosphere, the ionization that happens produces a spectacular scene out the windshield. I mean it also had us thinking about the missing tiles that are going. But a night entry is really a show. The next flight was a day entry which was not nearly as spectacular. I mentioned about grabbing the stick too late, unfair to Jack, and then the de-rotation. Now onto part three. How am I doing? I might make it yet. STS-51F was a whole different situation than the earlier test flights. One big difference is there were seven people instead of two. With seven we had to add a little bit on the patch to put the extra two names. This is the ninth flight. There are nineteen stars. Primary experiments. This was a science flight. It was a space lab but without the laboratory. All equipment in the payload bay full stem to stern with telescopes mostly. And all the telescopes mounted on the pointing system we had were solar telescopes. So we had the sun in the accurate part of the sky. Here is Orion and Leo, the backwards question mark. Nineteen stars. A lot of symbology here. A short entertaining video. We had seven people, including three mission specialists, which Dr. Hoffman was when he was down in Houston. And we had two payload specialists, guys who were not full time astronauts. They were solar physicists. And they were the experts on the solar telescopes that we had and went along to fly. First try here at main engine ignition ended three seconds after ignition. We felt the spacecraft rock around, the noise and then nothing. And we had a pad shutdown because the left engine, the automatic system detected a failure, a slow-acting valve and it shut us off. So we are there wondering if we are on fire and whether we ought to race out and so forth. It was tense for a while but there wasn't a fire, just this automatic shutdown. We crawled out. We were told there would be a two-week delay, so we took the kids to Disneyland and had a good time, went back home and started the whole training cycle again. And came back two weeks later and got a good start this time. But not after lying on our back on the pads strapped in for five hours because of some software glitches that had to be fixed and computers reloaded and tested. And one of our reports was five hours is the limit. I mean you are lying on your back with your feet up in a pressure suit strapped in. That is more than is reasonable to ask prior to launch. On the way up, well, I will mention that later. Here is the instrument system. This baby was built in Germany. It is this gimbal device that held these four solar telescopes and the star trackers. Here is a physics experiment. The OMS engines are lit and produces one-sixteenth of a G. The thrust of the orbital maneuvering engines. If you are trying to sleep, that is what happens when the OMS engines come on. And you saw the water going across. It is déjà vu. We had the same old PDP package on this, but with a difference this time. We took it out of the payload bay and brought it up here. That is my right ear you are looking at in profile out the window. It is crowded up there with seven people up on the flight deck all trying to get a view here, but we let go of it. And it had a momentum wheel in there to cause it to spin up slowly. And we backed away from it and flew a couple of very challenging loops around it. Here is a sequel to the hairbrush. This is not me. It is Story Musgrave who has the same hairdo as I do. And he is getting spiffed up for the TV show. That is all we did is horse around for seven days. It got extended a day to eight days again. And this landing was back at Edwards, runway 23 on August 6th when it was 105 degrees, lots of heat waves. This landing was by far the most forward CG because we still had all that equipment in the payload bay. And we were almost the heaviest orbiter landing, so getting the nose down before it fell down, crashed and broke the nose gear was one of my primary concerns on this one. More about the actual launch itself. There is the customary view. They put a camera right in close and got this really close-up view, but it was about 5.5 minutes after this picture. We had delayed five hours. It is late afternoon so very quickly heading out over the Atlantic we were in darkness. And then, bang. Remember the left engine got us on the pad abort? Well, the center engine shut down. We were at 3Gs and all of a sudden we are at 2Gs or something like that. Instant square wave cutoff and acceleration. Looking there and confirming the center engine shut down. What happened was there are a number of sensors on the main engines. The particular one that got us was the fuel high pressure turbo pump. A piece of machinery running at 75,000 RPM high pressures. The high-tech gear that makes the main engine so efficient, IISP, but really run at the limits of metallurgy and technology. The sensor that senses the output temperature was a series of four platinum wires in the cavity in the output of that turbo pump. They had some tendency for the wires to burn through. When they burn through, they showed over-temp was the electrical result of a burn through, one of these sensors. Well, we had two burn throughs. And the software said that must mean there are two sensors that say you are too hot, I will shut the motor off. And it did. With no reaction we just kept going straight and smooth, but it now put us into what is called an abort. Well, here is the crew. There are seven of us. I need to practice this more. But, anyway, it was a two shift operation. We were going to work around the clock, so we had a red team and a blue team. And I was the commander so I had a striped shirt. Abort to orbit. We had to call from the ground, confirm what we knew already, which means turning that rotary knob to ATO, abort to orbit, kind of an oxymoron in a way. It is not really an abort. It is pressing on and pushing the button behind it. It loads the software in to do a couple of things, lower the insertion target. We had tried to get as high orbit as performance would permit, but now we are going lower. Engine down costs you total performance. And we also started dumping OMS fuel. We had to turn on the OMS engines, and we ended up dumping 4500 pounds of OMS fuel, a little bit of extra thrust but a significant loss of weight to allow the remaining performance to get us to an acceptable orbit. And, interestingly, the last sim we did in training in Houston, before we went to the Cape to fly about two days before, was an integrated sim where we are tied into all the controllers and everybody is working as a team. And the very last run we had was an ATO, abort to orbit. And, son of a gun, that is what we did. We always had trouble starting a watch. And you try to do everything internally on the crew so that if you lose communication with the ground you can complete the emergency properly on your own. On ATOs before, we had to start a stopwatch at the time we started the OMS dump. And we had a chart to go in to find out how many minutes of OMS dump we needed to do given at what velocity we lost the engine. And Story's job was to do the watch. In the excitement of all the other stuff we had to do to get the OMS on, we would always forget the watch. But this time he got the watch going so we actually did it right. And we knew that when we got to where we burned out all the available fuel, which we did, we went to a fuel depletion cutoff, that we would be really close to having to do right away another OMS burn to get an acceptable orbit. We are right on the boundary, as it turned out. We dumped the right amount of OMS, every last drop of main propellant gone, we were just on the boundary of not having to do the first OMS burn and we could relax 45 minutes later halfway around the world to do the final circularization. So it worked out good, except we were in a lot lower orbit than we had planned. And everything about this space lab flight depended on the orbit, so we were into a giant re-plan. Here is a nice picture of the IPS. Gordon, I also explain the situation of the inhibit switch on and off. I don't know how much you were aware of what was going on there in the cockpit. There is a switch in the cockpit. You have a lot of parameters that are monitored in the software on the main engines which, if they go out of tolerance, will shut the engine off. In fact, that is exactly why we lost the center engine. But, right after that engine shutdown, we were in a state where we really don't want to lose another engine. Because if, with only one left, we did not have the performance to get to orbit, we would have had to have gone to Zaragoza, Spain and land in the middle of the night where it was a 10,000 foot overcast and raining. I mean if we pulled that off we would have deserved some kind of metal. And so, as a preplanned procedure, when you lose one engine before, the point where you can stagger into orbit on one remaining engine you inhibit the limits. You throw a switch that says you're telling the engines to keep running regardless of over-temps or anything because you take the chance, which is a big one if something let go, to not be susceptible that got us for the first engine, that is a sensor failure. And so we did that. We inhibited the limits until we got to a point in the energy profile where we were "press to MECO." That is the call. Press to MECO means that you are now at a velocity where you can make it into acceptable low orbit on one engine if you should lose another one. Press to MECO then the plan was we will re-enable the limits so we are not hanging it out on a possible second engine failure. And we would accept a second engine failure because we knew we could make it on one engine. So we did that, the call came up, we went to enable. And then, before we got there, we got another call from the ground that said go back to inhibit. Well, it wasn't time to get a full explanation. We dutifully did it. What they saw on the ground is more failures on the right engine. Remember the left got us on the pad abort? The center engine shut down on the way up. And, to make everything equal, the right engine, the same sensors they can see on the ground, it is not visible in the cockpit, each of those four platinum wires they saw starting to go. Clearly a design problem here. And they could tell those were going to go and get us that second engine, so that is why we went back to inhibit for the rest of the way. It made a good war story, but we got there. We started operating the IPS. A platform built in Germany with all the telescopes. These are start trackers to align where it is. And this baby could point. The spec was one arch second of accuracy. An arch second is the size of a dime. If you are standing at the capital and looking at dime at the Lincoln Memorial, that is how much. But, when we cranked it up, it didn't work worth a hoot. They just couldn't get it to stabilize or point where it was supposed to. And, for three days, the payload specialists and the MSs were in constant communication with the ground. And they patched the software in a major way and kept sending up new software loads to get this thing to work. And viola, on the third day they finally got it right, then it worked well and got a lot of good solar science. Just an aside, when you are looking at pictures from space, you tend to think you walk around out here and the atmosphere is this big ocean of air above you, right? Lots of air way up there. This little bitty blue line right there, barely perceptible, there always appears on any sunlit picture showing the limb of the earth, that is the same blue as the scattering that causes the sky to be blue. And that is how thick it is. It is just this little thin shell of atmosphere around. At 18,000 feet three miles up you have lost half the atmospheric pressure. And that is laying on an 8,000 mile diameter globe. And so that is where all of human history has happened, in that little shell over there laying around the globe. A philosophical point for you engineers. What is flying on orbit like? Well, it is one of the 215 pounds of checklist. Here I am checking propellant usage against what we've got and where we are because we dumped 4,500 pounds of crucial fuel that we needed to make the planned most maneuvers that ever been done in the orbit on our mission. We didn't want an extra blip out of an RCS thruster, and it worked very well. We got through seven days and even had enough to have another day of science on the eighth day. Flying is mostly watching the clock. Everything happens according to time. And, since you have 16 sunrises and sunsets every 24 hours, you never know what time it is without looking at a watch. And you are looking at a crew activity plan with everything laid out. And we even had an alarm system you could set in the CRT to make a tone to wake you up. It is a lot of clock watching to pull off a complex mission like this. It is just the way life is on orbit. Now, here is one of our really serious high-level scientific objectives. This was the official name, the Carbonated Beverage Test. I don't know if it was an MIT guy or not. He was a real serious academic type. An Indian I think. Anyway, he built a Coke can that had a lot of pressure regulators in there and laminar flow annular things. So many that this Coke can only held four ounces of Coke. But he talked to the White House. Reagan was president. And somebody on the staff approved we are going to fly these Coke cans and see if they had a system to provide pop in orbit with the regular kind of carbonation and dispense OK. We got the briefing and we had the four stowed in a locker. And I got them out at the start of the test. But 30 days before launch, all of a sudden this big thing came down. Pepsi got wind of this experiment and went to the White House staff and they got Pepsi put on. Pepsi went into a crash program to fly more cans of Pepsi. Here is Carl trying the Pepsi. You notice that looks a lot like a shaving cream can. Well, that's how the Pepsi came out, just like shaving cream, this frothy ball of stuff. I mean theirs was the last minute deal. It didn't have any pressure regulators in it. It just went out there. Now we worried about having to make a judgment, which tasted better. Well, the problem was we didn't have any kind of refrigerator so they are both warm. Warm pop is not my favorite. And so, they were not anything anybody fought over, either kind. If you let the Pepsi float around it would coalesce a little CO2 in random fashion, but the physics of it, Carl found by blowing very carefully on the edge you could get it spinning up. And spinning Pepsi would have the froth at the poles and the liquid around the equator. And we always had a tall guy standing by in case it drifted into something. This is the end of the experiment here. He got it into his mouth without touching any of it. We had the same PDP but, as I mentioned and as you saw in the movie, we let go of it. We actually maneuvered all around the orbit and looked at the wake through the plasma, let go of it. The proximity ops were very extensive and challenging and many, many maneuvers. That is in the Caribbean. The tongue of the ocean. A spectacular coral reef around very deep water. Here is the Gibraltar. The rock, I believe, is out on the point. The Mediterranean here and the Atlantic here. You've heard you cannot see borders in space. Not true. This is Israel this way and Egypt this way and the Gaza strip along here, which has been in the news as of late. And in the same area the Dead Sea, the Sea of Galilee. Here is most of Israel in one picture. A little closer to home. This is most of New Jersey. Long Island. There is Manhattan. Hudson River and East River. There are about 10,000 copies of this picture. This is Southern California. This is San Diego right here. Los Angeles. And, in high rise print, you can see water here which is San Francisco Bay. And the center of it all is the Antelope Valley right here where I live and where Edwards is right here. This is the San Andreas Fault right through here. Closer up of LA which, at the end of 51F, we came right by Catalina Island, right up the Harbor Freeway into Edwards. And we went by Harbor Freeway at about mach 3. And closer up of the dry lake at Edwards. And the landing. Flight test results most of which I have mentioned already. And, to finish up, I have reports on a memory stick here, the pilot reports we wrote as crews which you can take at your leisure. If you are interested, copy it off. They are available. Not great works of art, but the specific things that we learned on doing the flight test. And these are just thoughts of transitioning into operation from test mode, which I got to see the whole gamut from beginning to full operational. I apologize for running over. I don't think anybody minded. As you see, everybody is listening very intently. Thank you very much for taking the time. [APPLAUSE]
Free Downloads
Video
- iTunes U (MP4 - 251MB)
- Internet Archive (MP4 - 405MB)
- Internet Archive (MP4 - 19MB)
Subtitle
- English - US (SRT)