Flash and JavaScript are required for this feature.
Download the video from iTunes U or the Internet Archive.
Topics covered: Design Process as it Relates to the Shuttle
Instructor: Prof. Cohen
Subtitles are provided through the generous support of Heather Wood.
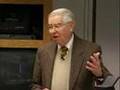
Lecture 19: Design Process ...
Related Resources
Prof. Cohen Bio (PDF)
This will be Professor Cohen's kind of last complete lecture, although, on the last day of classes the plan is we're going to take some of the time just to talk over what we've done and review things.
And it will be really oriented towards general aspects of systems engineering.
And, Aaron, I will turn it over to you.
Thank you.
Today, I'm going to lecture primarily on systems engineering but management as it relates to systems engineering.
I have several checks and balances.
And, of course, today I've got people from the Draper Laboratories and people from the predecessor to Draper Laboratories, MIT Instrumentation Laboratory are going to check me to see if I say the right thing.
First of all, I would like to say to you as a class that I read your last submission reports and really thought they were outstanding.
They show a great deal of interest, a great deal of understanding and a great deal of initiative.
And so, I really compliment you.
And I'm sure your final reports will be better, but they really were very, very, very good.
You've heard a lot of people talk previously, starting with, in my way of thinking, Dale Myers who was sort of the person who started the program in Washington at the time.
You didn't hear from another very important man, George Miller, who was really Dale's boss at the time.
But George is still alive, is still doing very well.
And you didn't hear from a lot of other people.
You did hear from Chris Kraft which sort of set the tone, you might say, for a very interesting and understanding man who really knows what he's doing and says what he thinks.
But there are several other people that I would like to talk about that had a great bearing on my career in terms of systems engineering.
There were two people, both who have passed away.
One is Joe Shea.
And Joe was a very remarkable engineer.
He was program manager of the Apollo Program at the Johnson Space Center, then left and became Vice President of Raytheon here and then became a professor at MIT in the Aero-Astro Department.
And I thought he maybe taught the forerunner to this course.
He taught systems engineering.
And Joe Shea was actually the best systems engineer I've ever met, so I am going to talk a little bit and give you some understanding of my interaction with Joe.
The best job I ever had, you might say, really, is I've had a lot of different jobs, but my first job was really working with the MIT Instrumentation Laboratory where I met a great number of people.
I'm not going to mention everybody because it would fill up the time.
They taught me systems engineering, but had it not been for the MIT Instrumentation Laboratory we wouldn't have gone to the Moon on the schedule we went on.
They really did a fantastic job, all these people.
I mean they were just you might say giants.
There were great people at Rockwell, at North American Aviation such as George Jeffs and great people at Grumman such as Joe Gavin and other places, but I have to say that the MIT Instrumentation Lab really carried the ball on understanding how to do guidance, navigation and control.
And if you read some of the comments by George Low, who is the other person I am going to talk about, George Low is another giant.
He says the most complicated system on the Apollo spacecraft was the guidance navigation system, if you read what he said.
And could you really hit a target 240,000 miles away and bring it back?
But let me get back to Joe Shea.
I said he was a great systems engineer.
And Joe Shea taught me a couple of things.
One, he taught me not to be afraid to make a decision.
He said the fact that you are in charge, the fact that you have looked at all the information, the fact that you know the details, you are the best one to make a decision.
And if you could make a timely decision and your battering average is a little over 60% you're doing very well.
But the fact you made it timely and the fact that you understand it, you can make a change.
You can change if you are wrong.
And that always stuck with me, not to be afraid to make a decision.
Because many times as you go through your role in systems engineering you're not going to have all the information to make a decision on a timely basis.
It is just not going to be there, especially if you do a program that pertains to advanced technology, advanced research and development.
That is one thing that is important.
Another thing that Joe Shea brought to the table.
During the Apollo Program, before we had Joe Shea, we would sit around a conference table in the early `60s trying to figure out what systems engineering was, but we couldn't really explain what we had to do.
We didn't know what we really had to do.
But when Joe Shea came, he brought with him the insight of what you needed to do to do systems engineering.
Now, this is the Apollo stack as you see in on the pad you might say.
The launch vehicles.
The launch vehicle.
The first stage, second stage.
Then you get to the lunar module, the command and service module, launch escape tower.
That is what it looks like on the pad.
Well, Joe Shea gave me probably the toughest job and one of the most important jobs that I had in my career.
He said, Aaron, you are going to be in charge of resolving all the ICDs, the interface control documents.
That is all the interfaces between all the stages, between the command and service module and the lunar module, between the command and service module, lunar module and the stack, between the command and service module, lunar module and the launch complex.
There were about a thousand ICDs involved in that.
And that was a formidable task because an interface control document you cannot design without the interfaces being defined, and you cannot define the interfaces without the design.
So it is really a chicken and the egg type of thing.
And it turns out that was a turning point in my career because we did do that.
In fact, a little sideline, a little interesting story.
He anointed me to do this job but didn't just leave me there.
He took me to the contractors, he took me to the MIT Instrumentation Lab, he took me to Rockwell, he took me to Grumman and he took me to the Marshall Space Flight Center and Kennedy Space Center.
And the funny part about it, he took me in to see von Braun, which I didn't know about.
I didn't know von Braun.
And he said, Wernher, this is Aaron Cohen.
We were in his big office at Marshall.
He said he is going to resolve all the ICDs, all the interface control documents.
And Wernher von Braun said that is wonderful.
What is an ICD?
So I knew I had a problem there right away that the head charge of Marshall didn't know what an ICD was.
But that was a little bit of a sideline on it.
I did have the job to actually resolve all the interface control documents.
And that turned out to be one of my most interesting, most challenging jobs as a young engineer.
It really taught me systems engineering, because one of the important parts of system engineering is understanding where the interfaces are and how you get the interfaces resolved.
And you could imagine trying to get Grumman at that time at North American Aviation and MIT Instrumental Labs to agree on an interface document.
I mean it wasn't the easiest thing in the world to do.
Yes. Did you have a question?
I was just wondering, aside from technically making sure that the interfaces are working and everything, what is involved in resolving an ICD?
That's a good question.
Well, first of all, I am going to talk a little bit more about ICDs in general.
ICDs you can define in several categories.
One is mechanical or physical ICDs, bolt hold patterns, just how things bolt together.
The other, you might say, is electrical ICDs, what kind of electrical signals are sent and electrical interfaces.
And the other are functional ICDs.
One of the big ICDs we had to resolve was a term called Guidance Reference Release.
Marshal had an inertial measurement unit in their instrument unit, and we had to have that synchronized with our system or with the system in the command and service module.
What is involved in it is you sit down and you talk.
You have a draft ICD.
And we had these big meetings.
We had them at the Kennedy Space Center.
I don't know if you've ever been to the Kennedy Space Center, but we actually fill the firing room with people.
And each group had a certain set of draft ICDs, and they would sit down in working groups and decide what had to be done to get the interface compatible in terms of the three phases Physical, electrical and functional.
And you just work out the details.
Aaron, probably now in the 21st century, we ought to add data ICDs.
Data ICDs, yeah.
Well, now things have changed probably a lot since I've been involved in it.
I mean remember Mars Polar Lander.
We had English units coming over.
Yeah, that's right.
And the people thought they were getting metric units.
So the data ICDs are also critical.
You know, and a lot of things are very simple and mundane.
I could tell you a story with the crew.
When we said you're going to have in-flight maintenance with the crew.
And we gave the crew to change out a component, but instead of taking the screw out very easily, we had actually put Loctite in the screw so we couldn't undo the screw.
There are very simple interfaces that have to be resolved.
Some are mundane, some are very sophisticated.
I don't know if that answers your question.
The problem is there is no F=ma.
There is no closed form solution that tells you exactly how to do it.
You just have to sit down and work it because the design hasn't been complete but you have ideas.
You float ideas, you negotiate, you arbitrate and then you come up with a decision.
The main thing is you've got to make a decision, and somebody has to be there to make a decision.
That was my job, to make a decision.
That was what Joe Shea left me with.
And people that know him will agree that he was an outstanding engineer but also probably one of the best systems engineers.
Larry, do you know what course Joe taught when he was here?
Yes, systems engineering.
He taught this course?
Yes.
I thought he taught this course because I know I came up and gave a lecture for him.
Until he was taken ill.
Let me talk about another person that was very prominent in informing my career.
His name was George Low.
After Joe retired, George Low became the Apollo Program Manager at the Johnson Space Center.
And George was very much a disciplinarian.
He always had time to see you.
But there were several criteria in seeing you.
You had to tell him what your subject was, how long he wanted and why you wanted to see him.
So when you met with him, if you asked for 15 minutes, you had 15 minutes.
And no matter how important the job was, if you didn't finish was you had to say in 15 minutes you were out the door.
And you only did that once.
But you didn't ask for too much time either because you got penalized if you said you needed an hour and you only took 30 minutes.
So, he was very much a disciplinarian.
He actually, after he retired from NASA, after he retired from the Apollo Program became Deputy Administrator at NASA and was very instrumental in the Shuttle Program and then retired and became president of Rensselaer Polytechnic Institute.
So, George had a very illustrious career.
He passed away several years ago.
One incident might be of interest to you, and I recall it very vividly.
I don't know if everybody else does, but we were getting ready to go to the Moon on Apollo 11.
This is on Apollo.
And you monitor all the systems very carefully.
And we were monitoring the inertial measurement unit in the lunar module which is right here.
And for some reason or other the drift rate changed fairly drastically.
Now, it was still in spec.
The drift rate was still in spec but it changed.
And to get to the lunar module and change out an inertial measurement unit on the pad is pretty hard to do.
First of all, the lunar module has very little structure to it.
It is made out of Reynolds Wrap really.
I mean it doesn't have very much structure to it.
And so we reviewed it with all the people involved, reviewed the data and we concluded very clearly that there was nothing wrong with it.
And so we went to George Low and we told him a unified story, the MIT people, the MIT Instrumentation people, the Rockwell people, everybody, the JSC people.
And George Low listened very attentively and then said can you explain why it changed?
And we said no, we're going to change it out.
That is the thing that always stuck in my mind.
If there is something that you don't understand then you need to take some action to fix it.
And to me that was a very important part of my learning process.
And so, those were the people you might say that really had an effect on my systems engineering thought process.
The other thing I want to talk about with you today is you heard a lot of people talk that I would class as subsystem managers.
You heard Tom Moser talk about structures.
I don't know if I can recall them all.
Al Louviere talk about the mechanical systems.
You heard Bob Ried talk about aerothermodynamics, Bass Redd about aerodynamics, Henry Pohl about reaction control systems, auxiliary power units and hydraulics, Walt Guy about environmental control systems.
You heard of these people.
These people are what I call subsystem managers that actually, in some regards, work for me and, in some regards, didn't work for me.
And that is what you call a matrix management system.
Now, I'm going to talk about matrix management.
Matrix management was actually a very popular management system several years ago.
I don't know if it is used today or not, but matrix management is a type of management basically used by large organizations.
Primarily what it is are large projects organized with teams that work on a functional rather than a project basis.
In other words, these people I just talked about actually had two bosses.
They had a boss in their engineering organization, a very famous man named Max Faget.
And then they had another boss, which was so famous, me.
And I was their boss that controlled the project's cost schedule and performance.
And they actually reported to me on that.
But they actually had two bosses.
And so, you do that for several reasons.
You do that in order to conserve resources.
And many large companies do that.
The other way of doing it, actually, would be to put all that engineering talent in the project office.
And you could see the advantages and disadvantages.
I will show you more explicitly the advantages and disadvantages on that.
The advantages are that you have a dedicated organization.
The disadvantages are that when the project is over there is no place for these people to go.
And I don't know what you use.
You have a matrix at the Draper Labs today.
I'm not that close to industry.
Do most companies use matrix today?
Yes, most aerospace companies.
There are too many projects that change all the time and somebody has to be responsible for the people.
See, that's an interesting part.
We, at the Johnson Space Center, didn't have that many projects.
We only had really maybe one or two projects, but we still used matrix management because there is a check and balance on matrix management which you don't get on centralized or project management.
There is advantage to it.
There are some disadvantages to it.
His rotation lab was project-oriented at the time when we did Apollo.
You were project-oriented because you had one project and you were just project-oriented all NASA project.
So, there are advantages and disadvantages.
I had some dealings with Ford Motor Company, and I think Ford Motor Company actually uses matrix management.
I think most large companies use matrix management today.
Anyway, that's really the advantages and disadvantages of matrix management.
And a lot of things I have already said.
Under matrix management, all the people who do one type of work are in a pool.
For example, all the engineers in one engineering department report to an engineering manager.
That is what I said.
They all report to an engineering manager.
In this case, the name was Max Faget.
And if you do history in the Space Program, Max Faget becomes a very prominent name.
He was really, you might say, the original designer of the Mercury, Gemini and a lot to the Apollo spacecraft configuration.
So, you will run into his name time and time again.
But, the interesting part about it is that Max and I used to go at it tooth and nail.
I mean his people would want to do something like a Walt Guy.
Walt at that time was a very stubborn person.
And he would want to do something and I wouldn't want to do it.
Well, he would go to Max.
And then Max and I and Walt would have a meeting at the Summit with Chris Kraft.
It was a common point.
We all went to see Chris Kraft.
Sometimes I won and sometimes I lost, but I learned actually to love it.
Even though it frustrated me, I learned to love it because there was that check and balance on me that I could not do something that was going to actually be wrong.
Somebody else was going to catch me if I did something wrong.
Now, I honestly do not know today what NASA uses, whether they use matrix management on the Shuttle program or on the Space Station program or how they are going to do it.
Do you have any idea?
The Shuttle was certainly much more project-oriented.
We don't have the same, I mean there is an engineering division at JSC, but during the Shuttle that was -- It started out matrix management.
I think it really decreased, and there was no more Max Faget running things in that same way.
And so that, in my mind, at least in my way of thinking, is probably one reason why problems occurs, because you don't have that independent check and balance.
There is a very good reason why matrix management, I think, is important, even though you don't have a number of projects that would cause you to do matrix management.
Well, this says these same engineers may be assigned to different projects and report to a project manager while working on that project.
Therefore, each engineer may have to work under several managers to get his or her job done.
And that is what I was saying.
It just turns out that you do have that type of problem in doing that.
Proponents suggest there are two advantages to matrix management.
First, it allows team members to share information more readily across task boundaries.
Second, it allows for a specialization that can increase the depth of knowledge.
You can see how, if you have a matrix manager, you can call on more resources to go back to your home organization facilities in terms of testing.
I have worked under, and when I was in industry, total project organizations.
And it has a lot of advantages and disadvantages also.
The disadvantage of matrix management is that employees can be confused due to conflicting loyalties.
I mean was Walt Guy loyal to Max Faget or was he loyal to Aaron Cohen?
Now, Max actually gave him in raises but I controlled the dollars for the project.
But, you're right, that is what counts.
They call that pink ticket.
He was actually pink ticketed to Max and actually worked for me.
And I had to use all my persuasion to get him to do the type of job.
Properly management cooperative environment, however, can neutralize these disadvantages.
In Apollo there was one program.
Right.
[AUDIENCE QUESTION] For example, we had Air Force, Navy and NASA.
Right.
And we were doing accuracy evaluation for each one.
And we were developing the whole software from scratch for each one.
It was different language and different computers and you couldn't compare results.
Right.
And when you have one engineering organization that does the same at least you can compare.
You have the check and balance.
Right.
That's a very good point.
Yes, Jerry.
[AUDIENCE QUESTION] Whether you a project organization, you had your thumb on the people who had to produce.
In the matrix organization, off times the engineering manager would shuffle his man right out from under you to another project.
Oh, that's right.
That's what I had to contend with.
On the other hand, my strong personality and my good will kept it from going that way.
And there was a certain amount of esprit de corps that they wanted to get the job done.
In the end it is the people.
It's the people.
It doesn't matter what organization.
That's right.
If the people are wrong, no organization is going to work.
Well, that's absolutely right.
You have to have the right people.
Well, that's why I brought some of these people to talk to these students because these people were the people I worked with.
Even though we argued at times.
There was nobody that argued more than Henry Pohl and I did, but he is usually always right.
But you can learn to live with it.
Matrix management can put some difficult on the project managers because they must work closely with other managers and workers in order to complete the project.
The functional mangers may have different goals and objectives.
I was saying this as I present these charts, but I think you can visualize that.
And don't hesitate to ask questions because you've got a lot of people here in the room today that can help answer these questions.
Yes.
The point about checking and balance.
You have several managers.
Yes.
From my understanding, you have maybe a functional manager and then you have [OVERLAPPING VOICES].
Well, let me tell you what I mean by check and balance.
Let me give you a specific example.
Let's say Henry Pohl on the reaction control system wanted to do more testing or wanted to do more stability testing.
And I looked at my budget and I looked at where we stood in the schedule, and I said we just cannot afford that, we're just not going to do that.
I made an arbitrary decision.
Well, Henry would be very upset about that and he would go to Max, his functional manager.
And Max would say boy, you're right, Aaron is crazy.
He would then call a meeting with Chris Kraft between Henry, Max and myself to decide what we were going to do.
And then Chris was the final word, the man you met.
He's a pretty strong guy.
And if he agreed with Max, if Max had a convincing story, he would turn me around and then we would do the testing.
And I would just have to find the money some place.
But if I could convince Chris that Max was overdoing it then I would win.
And normally I lost, but that is OK.
Do the engineers in any of these organizations out of matrix management feel that they have too many managers?
Well, it is frustrating to them a little bit.
Yes, they did.
It's frustrating because they had to feel that they were working for two different people.
And it is a little bit confusing to them.
I mean they had two loyalties.
That's what I pointed out.
They essentially had two different loyalties.
One to their functional manager who paid their salaries and the other to me who really had the money for the project and the schedule.
So, yes, it is a very tough thing to do.
But, as you could tell, by talking to these people that experienced it both in Apollo and in the early days of Shuttle, they were very satisfied with the results.
That is why it is very frustrating to some of us to see the way things are going because we carried over most of these people you talked to or are here in the room today worked on Apollo and then went and worked on Shuttle.
We had the same process.
We had the same Joe Shea, George Low process that we did.
Yes.
[AUDIENCE QUESTION] Well, that's absolutely true.
Your decision-making process in matrix management turns out to be a little bit more cumbersome than if you have direct control.
In other words, if you have your thumb on everybody you can get a decision pretty quickly.
On the other hand, you can violate some good checks and balances so you give up the process of a rapid decision-making process versus having some good checks and balances.
Does that answer your thoughts?
OK.
I am going to leave that subject, unless there are any other questions on it.
Can I just bring up something?
Sure.
And I welcome your opinion on this, Elliot.
And that is there has been a big change in NASA recently which is affecting management.
And that is because NASA has gone over to what they call full cost accounting which means that during all of this time the engineering organization maintained their engineers.
That's true.
They paid the salary and then they would be assigned to projects as required.
The system, as it's now working, is it's supposed to be much more like in industry where the time of every engineer has to be billed to a specific project.
And if you don't have a project to bill your time to, ultimately you become redundant.
And so, those of you who read Aviation Week and Space News, I hope all of you do, are aware that NASA is doing a lot of downsizing.
It puts a lot of constraint on management.
Now, in industry, obviously people have to be paid for.
But are there always enough projects to bill people to?
Well, there is never a situation that you have the exact number of people.
You're either short of many people, which is now the situtation at Draper, or you don't have enough money.
What you do, in a place like Draper, we have our own money.
It's called internal research.
And we use some money [NOISE OBSCURES] and we keep those people.
But those have to be people the company believes can be used in the future.
There is no point in keeping people that nobody wants.
Actually, the matrix system, and I talked about it with Jerry because we are doing the evaluation, that is why I have to leave, is really sorting the people out.
Because when it was a big project, it was a big family.
The guy owned them.
He knows them.
That's true.
Now, you work at the function organization and we send you to work, he wants the best people for his project.
He will say well, I don't want this guy.
Now, if it is a mediocre guy, we will say look, you cannot have the best.
But if it is somebody who is very weak we will say for one time, OK, maybe he didn't get along with the program so put him in another program.
But if we get the feedback, it doesn't work there, we know there is a problem.
In that way we weeded out a lot of people that, if you have the old system, probably will stay and make us less efficient.
NASA will be more efficient now, I think.
I think that is true.
On the other hand, it causes a lot of pain.
It is very difficult to let people go but that is part of management.
It's not just going to parties.
[UNINTELLIGIBLE PHRASE] That's right.
Yes, there is a question.
I guess another angle on the "very tough to let people go" I've noticed that it is extremely difficult from a bureaucratic standpoint to let somebody go in government.
And I'm just wondering with full cost accounting, OK, you've decided it is time for this person to go, but there is just a lot of politics and bureaucracy paperwork to go through to get somebody out of the organization.
There are civil service laws which have to be complied with.
It is difficult.
And, I have to say, I agree with Elliot.
In the long-run I think NASA will become more efficient.
Well, to answer your question, there are several ways to let people go.
One is if they've really done something bad.
You have a board and you go through it and you release them.
The other is if you NASA has a downsizing, which is called a RIF, reduce in force.
Then you can arbitrarily let people go.
I didn't mean to interrupt you, Jeff, but those are two ways.
I will just add the third way, which NASA is also doing, is you can offer what they call buyouts.
They offer up to $25,000 if you will take early retirement, so a lot of people do that.
And companies, not government, have a much easier time.
I don't know how Draper is, but companies have a much easier time letting people go than other places.
But that was about all I was going to say on management.
Now I'm going to get into, you might say, the interesting land of systems engineering and talk about systems engineering a little bit.
My charts are sort of yellow because they go way back.
It turns out systems engineering has been studied a long time a lot.
And there are many aspects of systems engineering that some people in the room may or may not agree with.
I've had time to reflect a little bit from my days at NASA in both Apollo and Shuttle and in Space Station.
And I was, as I say, Director of the Johnson Space Center, I was Deputy Administrator, Acting Deputy Administration under Goldin for a year, and then I taught at A&M.
And all that time I have had time to reflect and I have had time to do some, you might say, research of what I thought systems engineering was and how you explain it.
I want to try to do that today.
People in the room may or may not agree with it but it is my thought process.
And it turns out that much of this information was gathered from studies done by the military, mil specs on systems engineering.
They have spent an awful lot of money studying systems engineering.
And many of these charts are plagiarized, you might say, from those studies and they look sort of like they are yellow.
And they are.
But let's start off with systems engineering heritage.
Systems engineering, as we pointed out, is not new.
The pyramids, you know, that was a real systems engineering problem.
I don't know how they did it but it was a real systems engineering problem.
I don't know if even Jim Nevins could do that.
That was a tough job.
Broadcasting service and standards.
Now, most of the time when you talk to people about systems engineering, in fact, I've done a lot of research on that, they talk about systems engineering as operations research.
Well, I don't think that can be further from the truth of systems engineering.
I think it is a tool maybe used in systems engineering, but it is not really systems engineering.
The RAND Corporation developed the systems analysis.
The Bell Labs telephone systems.
That was, of course, where Joe Shea came from.
Joe Shea came from the Bell Labs at the time.
NASA military systems, and these are mil standards.
And the Army.
And then systems engineering management guide for Belvoir Defense Systems Management College.
There were a lot of studies done for systems engineering.
And we, in Apollo, were trying to do systems engineering in the 1960s for Apollo, is when we tried to start to do it.
By the way, these charts are not on the Web but I will give these to Jeff and they will be on the Web.
Trans-highlighting the need for increased systems engineering, there is a need to manage the total picture in the area of increasing system size and cost, but even a small project has systems engineering.
If you can think of how you design a bicycle, how you design an automobile, I mean these are very complex problems.
They are not simple.
They are really systems engineering problems.
But the increasing technological growth and specialization, increasing systems complexity, you know, the PC is a fantastic systems engineering problem.
And I guess Bill Gates saw the need for a true systems engineering job and made a lot of money on it in terms of what he did understanding systems engineering.
Increasing sensitivity to environmental factors and increasing costs of life cycle.
All those things make the trend in systems engineering important.
And, as I look at your reports, wherever you got it, I think you have a pretty good knowledge of what systems engineering is.
So, I am not sure this lecture is going to help you that much because I think you do look at it from a systems engineering standpoint.
By the way, my last topic is going to be cost analysis.
I'm sure you're waiting to hear that because cost analysis is very hard for you to come to grips with.
And I am going to talk a little bit about how you would go about doing a cost analysis which may not dot all the Is and cross all the Ts for you.
But I am going to try to do that.
We're going to take a break at about 11:00 and then I will have some time to go through cost analysis.
Well, what is systems engineering?
I don't know.
You may not agree with this, but systems engineering is the application of scientific and engineering to transfer an operational need into a description of system performance parameters and of systems configuration through an iterative process.
Now, let me give you a needs statement.
When President Kennedy said we are going to send men to the Moon and return them safety within a decade that is a perfect needs statement.
It doesn't tell you how to do it, he didn't put a cost constraint on it, he did put a time constraint on it, and he told you what you had to do but didn't tell you anything about how to do it.
That is a very good needs statement.
I don't know if he did that for that reason, but he gave the public and NASA a very good needs statement.
Now, our job was to transform an operational need into a description of system performance parameters and the system configuration through an iterative process.
And that is an exercise left to the student.
That is not easy to do, but that is really what you need to do.
Now, to integrate technical parameters and insure capability of all interfaces, that is what I talked about.
You talked about physical, functional and program interfaces.
They call them different things but basically interfaces become a very important part of the systems engineering process.
And the other factors into the total engineering are to meet cost, schedule and technical performance.
What is that?
I think Professor Hoffman talked about that.
That is the three-legged stool.
It is schedule, performance and cost.
It is a continuous tradeoff because you are going to have a criteria.
Whereas, President Kennedy didn't give us a cost, he did give us a schedule and, to a certain extent, performance.
But he didn't give us a cost.
Now, as it turns out, cost always becomes a factor.
It always becomes a factor.
But those were the things that really comprised, you might say, in simple-minded terms systems engineering.
I cannot emphasize those enough.
Now, I don't know if that is how you visualize systems engineering or how everybody in the room visualizes systems engineering but that and the design process is really what systems engineering and design is all about.
Now, whether we utilize that always in design of our projects I cannot say.
I think we could have done a better upfront job in systems engineering on the Shuttle.
I really think we could have.
I see things we could have done differently on the Shuttle today if we really practiced a true systems engineering process.
It is very difficult to do because you can stay in this systems engineering loop a long time and not get anything done.
There is an old adage, if you never get out of this loop, you could do something, do something and do something and never get anything done, so you've got to be very careful with that.
What is the role of systems engineering?
Technical customer interface requirements definition.
Requirements definition sound very, very simple, but requirements definition is probably one of the hardest things you have to do, is to find out what the true requirements are.
And, unfortunately, requirements do change as a function of time as you go through the phase of the program.
But requirements definition is very, very difficult to do and very important to come to grips with.
As JR Thompson talked to you, I don't know if you recall JR's review of the Shuttle main engine, SSME.
He said had they widened the throat a little bit they would have reduced the complexity of the design and development of the main engine.
Made it much more reliable but you would give up some performance.
Now, why didn't we do that?
Because there was a requirement to advance technology.
And I think JR made a very, very important point there that those are things you need to look at early in the program.
So, requirements definition are very important, extremely important.
And it is very difficult to get to the bottom of it.
Requirements definition is a task in itself.
And then, of course, there is a requirements management analysis and flow down audit.
And then, again, you get interface management.
Risk management is becoming a big item today.
You heard Bob Siemens talk, and I didn't mention Bob Siemens.
He is another very, very important man in this whole era of Apollo and down to Shuttle.
His role cannot be stated too highly.
He did a fantastic job.
His risk management was very interesting.
I heard him talk not too long ago.
And he said that the risk management in terms of cost and in terms of human life for the Apollo program was accepted, not only by the executive branch, the legislative branch but the public.
So, risk management needs to be accepted.
And that is one thing that is very, very important.
Understand what the risk management is in terms of life, in terms of cost and in terms of what it is going to do for you.
So, risk management is very important.
And it is the function of the systems engineer to bring that to bear.
Performance management, design process, so forth and so on.
Technology need identifier.
I had the reputation of not wanting to advance technology mainly because of budget constraints and I wanted to go with given technology.
Is that right?
I don't know if that is right or not, but the point being is that technology can drive a program.
The fact that you have to develop the technology can drive the program.
These are what the role of a systems engineering needs to do to figure out how they are going to handle technology, if they are going to advance technology or not.
What is a system?
A system is a complete solution to a defined need in its full environment over the prescribed life.
The system includes hardware, software, documentation, human resources, nonhuman resources, esoteric factors.
It includes almost everything you can think about.
Software turns out to be a big driver today.
Software in the system turns out to be one of the largest drivers.
Some of you asked me, and I hope it helped, what was the cost of the Shuttle Guidance and Navigation System.
I don't know who asked me for that.
Somebody asked me.
Was that helpful to you, the number we gave you?
The Shuttle.
They wanted to know the Shuttle.
But the fact is it didn't separate the cost of the software and the hardware.
And the hardware came on pretty much on cost but the software was a lot higher.
It was exponentially growing.
Software turns out to be, I don't know, Jerry, do you want to say a word on software?
Well, the problems of software were the issues of validation, verifying tests and retests.
And then every once in a while somebody would come along and say well, but we really ought to add this.
And adding on was a killer.
Well, as Bill Tenel used to say, it is sort of the garbage dump for things you couldn't do in the hardware.
The number that I remember is at some point, when you wanted to change one line of code, IBM wanted $1 million.
Each time for one line of code because they had to change the whole software, so that is why they have the software control mode [NOISE OBSCURES].
That's right.
I remember when I retired, Dave Leestma, who was head of the Astronaut Office at the time, said that he thought he could get a change through.
I forgot.
It was something to do with return to launch site.
I don't remember what it was but it was some kind of program he wanted to put in.
He talked to everybody and they all approved it, and it came to me and I turned it down.
And he said at my retirement party, now Aaron is leaving, maybe we can get it approved.
But software changes do increase the cost of the program.
A simple system example.
Space Shuttle.
Your house.
Electronic calculator.
Freeway.
The Golden Gate Bridge.
Rapid transit.
Computers.
A system really involves everything.
Almost everything you can think of is a system.
The other thing that is interesting is this chart right here.
You may have seen this charge before, you've seen it different ways, but the importance of systems engineering, the systems engineering is doing the right thing right.
As system increase in complexity and value, early system decisions become increasingly important.
It shows that actually in the impact of program funding, when 10% of the program funding is accomplished you have actually committed 90% of your dollars, systems engineering systems have actually committed 90% of your dollars, so that means early decision-making on systems engineering.
And whether you were going to make the engine throat wide or not actually impacts the program very heavily earlier.
That is why systems engineering is so important.
Systems engineering is requirements in solution management.
Understanding analysis, allocations, so forth and so on, which really affect performance, cost and schedule.
And there is the three-legged stool again.
This really says that if you remember certain parameters, the continued tradeoff between cost, schedule and performance is really one of the most important things you can understand that is really a systems engineering job.
One thing I would like to talk about is the attributes of a systems engineering.
Systems engineers are very hard to come by.
They really are very hard to come by, and it is almost hard to tell you how to become one.
I mean there are courses you can take, but one thing I would suggest you do, if you really want to be a systems engineer is you specialize in one technical area.
Whether it be structures, whether it be thermodynamics, heat transfer, guidance and control, control systems, specialize in one area.
That is the first step.
You need to be competent and show your competency in one area, but then you need to broaden out a little bit and look at how people actually operate.
Good judgment of technical competence in others.
Ability to build trust of team customer management.
And this is what this course is about, to work as a team and to have relationships with each other.
I don't know if it was true at MIT, but many years ago in universities it was very bad to work as a team because you tended to rely on each other.
And they wanted to have independent research, independent development, so students were not really encouraged to work as teams.
I don't know if that is true at MIT but it was certainly true at some universities I knew.
I don't know.
Was it true?
Well, we've gone through a major shift.
And I think the rest of the country is as well from individual to team effort.
Yeah, team effort.
Particularly in engineering.
That's right.
When I first went to A&M, they thought it was terrible.
Some of the professors thought it was terrible working as teams.
The difficult that all the top universities have is you guys are all admitted on the basis of your high school or I guess in graduate school your college grads, so those are individual efforts that got you here.
Now we're saying put the emphasis on team activity.
The Japanese have traditionally done that far better than we have.
That's right.
I just wanted to strengthen what you said because a lot of people think that a systems engineer should be a "Jack of all trades" and should know a little bit about everything.
Absolutely not true.
You have to be very good in one specific area, and that is your baseline.
That's right.
The most difficult thing in engineering as a manager is to make a decision when the guy who comes to you knows about the subject more than you because he is the expert.
And the only way you can do it is by knowing how an expert behaves.
And, in your area of expertise, you can make that judgment.
Some people are confused on this, but I think that I 100% agree with you.
You have to be an expert in one field, otherwise it won't work.
I should say there have been a lot of discussions among the faculty in the Aero-Astro Department and perhaps in other departments as well as to when systems engineering should be taught.
Should it be taught at the undergraduate level?
And right now the guiding philosophy in the Aero-Astro Department is to devote undergraduate time really to building up expertise in the individual subject matter, as Elliot said.
The idea being that wait until you really have a good grounding as an engineer in one or more specific subjects, and then, at the graduate level, that is time enough to actually look at systems engineering as a discipline so that you can draw on the expertise that you have built up.
That is not a universally held decision.
And there are people who make a good pedagogical case that you can actually start teaching principles of systems engineering right from the freshman level.
And, in the whole CDIO philosophy that our department tries to follow, we try to develop these principles which we think will then be useful as you get into more technical aspects of systems engineering levels.
We always try to balance the technical expertise with the systems level thinking.
Yes, Jerry.
I would like to point out that in the organizing teams, a key important feature of that is to have that systems engineer who is organizing the team and setting up the meetings to know why and who should be attending.
I attended a number of Space Station meetings when I had these product teams where every company in the world was there.
And you had 50 people sitting around and there were only four who were real contributors, and the others I could swear were falling asleep.
You fundamentally have to have good management in team setups.
Well, you're absolutely right.
Of course, one of the problems with Space Station, in all honesty, if you had tried to devise a management system that was complex the Space Station system would have won because it is probably the most complex management system.
In fact, I tried to explain it to the Bob Gilruth one time, who is another man I should have mentioned.
He was the Director of the Johnson Space Center.
And he came to see me and his eyes just rolled back in his head.
He couldn't figure out what I was talking about.
So, you're right.
But, you know, the other person that agrees with you, Elliot, is Chris Kraft.
Chris Kraft feels very strongly about becoming an expert in one field before you tackle something.
Self-motivated.
Able to motivate others.
In matrix management, that becomes a good systems engineer, if you're able to motivate others.
Methodical.
Analytical.
Intuitive.
Questioning.
Open-minded.
I think that is one of the key points, being open-minded.
If you make a mistake be ready to accept the mistake and correct it and make a change to it.
That is very important in systems engineering, especially if you have to make some important decisions.
Confident.
A good communicator.
High level of integrity.
So, that is really some of my background on systems engineering.
Now, let's talk a little bit about more how you go about doing it.
Thank you, Elliot.
A system is generally considered a conglomeration of objects that perform a specific function.
And you can think of those.
I mean you can think of all those in the laptop computers you have, many things like that which we talked about.
And I mentioned this before.
This is what I say.
It is a postulate or whatever you want to call it.
What is important for the whole system is nearly identical to what would be the best in the long-run for each of its components.
However, what is best for each individual constituent may not be the best for the whole system.
And so that really is something you need to keep in mind.
That is really the postulate of systems engineering.
It may be the right thing for the system but it may not be the right thing for the total configuration.
And the systems engineering process is the customer/user need analysis, mission requirements, functional analysis, system concept, development, tradeoffs, design.
Now, this is systems engineering as it pertains to design.
Now, there is systems engineering as it pertains to operations, but this is systems engineering as it pertains to design.
Design optimization, requirements flow down, telecommunication, design insurance, verification audit and then you go through this iteration process.
In fact, this is what you do in your mind.
I am sure you do that.
When I taught this, when I spoke about this to several professors, my friends at Texas A&M, they say well, there is nothing in this.
They said it is all commonsense.
And, to a greater extent, it is commonsense.
But the problem is do you really practice it?
Do you really have a process in place and do you really practice it?
And we find that we don't really practice it too well.
And we say this over and over again.
But the three factors of systems engineering will be the cost, schedule and performance.
And that is the famous three-legged stool that we talked about many times.
But that really is the essence.
And, you as an engineer going to work and getting paid, that is what you're going to be paid for, getting a product out the door that essentially meets the cost schedule and performance.
You look quizzical.
Excuse me.
No, go ahead.
The statistic that you gave.
After 10% of the project funding then you have 90% of your requirements defined, do you think that function there might change today now that we have faster prototyping tools?
It could change, yes.
This was done some time ago.
Technology is changing.
Rapid prototype is changing.
CAD design.
A lot of things are changing.
It might be not quite as dramatic, you might say, but it is still going to be there.
A lot of your system engineering decisions are going to affect your end product very early in the game.
And one reason why that 90% gets locked in is because of the difficulty of making changes once you've got all the plans drawn.
That's right.
And so, to the extent that CAD systems make it easier to change drawings and propagate changes throughout the system, it may be that making certain changes are less expensive than they might have been.
As Jerry said about software, you start changing your software around, you've got to do re-verification and so on.
Certainly, to the degree that modern techniques might make things more flexible, that number might get pushed down a little bit.
But generally, once you've gone through preliminary design review, you have basically set the parameters of your project and things have a momentum and it really does get harder to change.
And, of course, once you've gotten to the critical design review -- That's right.
At that point you're starting to cut metal.
And then, once you've actually started to build something, the price of changes goes up astronomically.
When we did the Apollo Program we started in '61.
It is my guess that by '64, and not too far into '64, I remember June of '64 we had the implementation meetings with Apollo.
By that time all the hardware definition was in place.
That's right.
The program went on after that.
And the only thing that kept growing or changing was software, but the basic hardware picture was pretty much the nail was in, in 1964, three years into the program.
Well, as Jeff said, once you start cutting chips and start cutting hardware it is pretty hard to make changes.
If I could clarify.
What exactly is it that is being locked in?
Well, usually your requirements.
Primarily what your requirements are is the big driver.
And then, once your requirements are defined, you can actually start your iterative process of design.
Once you get your functional performance requirements defined, you then start your design iteration and you start locking into things and, pretty quick, you start cutting hardware and software.
Hopefully you have gotten a sense, from all of the lectures on the subsystems of the Shuttle, the degree to which they interact with one another.
That's a good point.
I mean imagine if halfway down the road there had been a major change to the thermal protection system which had bumped the weight up by, say, 20%.
Imagine the ripples that that would have affected.
Or, if somebody wanted to change the requirements for cross-range, after you had done the basic design of the system.
Let me give you a very real example in that.
We had the wing basically designed.
And you know that the landing gear comes up in the wing box.
Well, we came to the conclusion that if you blew one tire on touchdown you could blow all the tires.
And so, what they wanted to do is increase the number of tires that went into the wheel well.
And that was pretty late in the program.
I mean we had already decided, from the systems engineering point of view, we were going to have the number of wheels we had and go up into the wheel well.
But then came along a study that showed well, if you blew one tire you're liable to lose the vehicle on touchdown.
They wanted to go put more tires into that wheel well.
Well, can you imagine what that would do?
That would be redesigning the whole wing when the wing was built, so we lived with that.
We lived with that with some risk, but you didn't make the change to it.
That's the type of thing that gets into it.
And I'm sure there are a number of items I could talk about that would cause that problem to occur.
Sometimes if you come up with a problem that really would be fatal, you've got to change
it. You've got to stop, yeah.
And one of the examples being the O ring seal on the solid booster.
In retrospect, people have said we should have changed that at the beginning.
Now, who knows?
If on one of the Shuttle flights a tire had blown and we had lost the entire vehicle, there would have been an accident investigation board.
And they would have gone back and said we were flying with an untenable system.
And we should have made that change.
And that is where the engineer who has become a manager is really faced with a tough potentially life or death decision.
And there is always an element of risk, but if you try to take out all the elements of risk you will never fly.
Well, that's absolutely right.
And so how do you make that judgment?
As I said, that is why they pay you such a big salary.
Well, the interesting part about that is after the Challenger accident my deputy, who became a very good friend of yours, Paul Whites, who was an astronaut, a Navy fighter pilot.
And our job was to get the Shuttle flying again after the Challenger accident.
I thought I brought it with me.
We found this picture of a ship on a very ominous sea.
It said a ship in the harbor is safe, but that is not what ships are built for.
You could make it so safe that you could never fly or you could never fly cross-country or you could never take a train.
You've got to use some judgment.
And, of course, that risk today, that risk level today is not very well accepted.
A point I was trying to make is that during the Apollo Program it was accepted.
We knew we had to take risk.
Tell me when you want to break, Jeff.
Do you want to break now?
This is probably a good time.
OK.
We will take about a five minute break.
I want to get to cost, but I have got a few more things to say.
Let me talk about process.
We had a contract with Ford Motor Company, and I showed this to Ford Motor Company of a design process I would go through.
And they said that is very interesting, we studied for a long time and this is exactly what we use to understand the need.
And the need was not the Ford Edsel.
That was not a good needs statement.
But you need a need, you need a need analysis [OVERLAPPING VOICES].
Well, I tell you.
You need to talk to Henry Pohl.
Henry Pohl, who heard lecture, still has an Edsel.
Henry is probably one of the few people that still has an Edsel in his garage.
Henry has a lot of things like that, but Henry still has an Edsel.
But you need to do a need analysis, understand what the need means.
You need a function structure.
And, actually, in some of your reports I saw very good examples of all these.
Now, maybe not in all the reports, but I saw somebody talking about the needs, somebody talking about needs analysis, somebody talking about function structure requirements.
The hardest thing for engineers to do, especially young engineers to do, is to make some assumptions and constraints and do some preliminary calculations.
It is very difficult for them to do that.
They like to see F=ma.
And I once mentioned that to Joe Shea, and he said I am glad you were still on your formula when I talked about F=ma.
You need some calculations and then you need to do some conceptual designs.
And that really is, you might say, the design process.
And you can use various forms of it, but that is probably the best form of it you can think about.
Systems engineering.
Interdisciplinary activities.
Customer need.
Functional identification requirements.
Iterative design process with reviews at various stages.
Conceptual, preliminary and final designs.
And that is what Professor Hoffman was talking about.
As you go downstream very quickly on that it becomes harder and harder and harder to make changes.
Let me now stop with systems engineering, not that I couldn't go longer.
But let me stop with systems engineering and talk to you about a subject you're probably having more problems with than anything, and that is how you do a cost analysis.
And, unfortunately, I am not going to give you a closed form solution for it.
There is none.
Not only that, I did the 90-day study when President Bush was president.
I stood on the steps of the Smithsonian.
Dick Truly appointed me to do it.
And that study was really paned by everything.
Because they said give us a cost analysis.
And I really thought they wanted to know what it was going to cost so I told them.
Well, they didn't like it.
And, in all honesty, I really wasn't that high because it was a 30-year project.
I gave them the cost for a 30-year project actually building launch vehicles, technology.
But, nevertheless, I had my day in the barrel on cost analysis.
Let me talk a little bit about cost estimation techniques.
It turns out some of you were trying to use it.
Here are the cost estimating techniques.
Expert interview.
You talk to an expert in the field, if you can find one.
Parametric analysis.
I am going to spend most of my time talking about parametric cost analysis because I think that is the one that pertains to an engineering design course.
Parametrics.
Because it is in terms that you understand, weight, performance, that type of thing.
I am going to talk about that.
Analogies.
And then the engineering which is really, you might say, the grassroots or the buildup of what it is going to cost for engineering hours, manufacturing hours and that type of thing, which is pretty hard to do.
I am going to go through those.
Now, some of you have tried to do some of these.
Some of you have tried to call contractors to find out what a particular thing was going to cost.
Some of you have tried to find out what the Shuttle Guidance and Navigation System cost.
You were trying to do it, but it's not easy to come by.
You call a vendor and he says well, he will quote you, but he wants to know what you're going to use it for.
It is hard to do.
I know it is very, very hard to do.
And they want to know how many hundred you are going to buy.
I don't minimize the job you have in trying to do a cost estimate, but you've got to recognize that, as an engineer and you go out and start to work, they are going to want to know what this thing is going to cost you and what allies you have to make.
Now, these are the cost estimating techniques over the project cycles.
You can see, as the project goes along, you have this so-called parametric method, analogies, judgments, system level CERs, cost estimate relationships.
And that is a very key thing, cost estimate relationships.
I am going to talk more about that, but let me tell you what a cost estimate relationship in a very simple-minded approach is.
Let's say you're going to go buy a house.
What is the first thing you want to know about buying a house?
How many square feet do you have, right?
You take how many square feet you're going to have and you usually know about what it cost per square foot in the area you want to buy a house in.
You multiply that and you get a rough estimate of the house.
Now, there is another factor that goes into that.
There is the culture.
Where you are going to build this house is going to affect the cost per square foot.
If you build it in a very expensive neighborhood -- I always give the relationship in Houston because I know Houston.
If you're going to build it in Clear Lake where NASA is, it is one culture.
If you build it in River Oaks where the very wealth oil people, it is another culture.
The cost per square foot in Clear Lake is much lower than the cost per square foot in Clear Lake.
You can get a rough estimate, but that is a very simple-minded CER.
It is a cost estimate relationship.
They become very, very complicated when you talk about past history, when you talk about weight of spacecraft and so forth and so on.
I will develop a little bit of that.
General subsystem CERs and calibrated system CERs.
But these are the parametric methods.
And you can see where they are used, analogies and judgment.
And they are used for a certain period of time.
Then, when you get to the phase B or CD, you talk about component buildup estimates, detailed estimates and vendor quotes.
That is sort of the schedule.
And this was provided by the cost technology over the project cycles by the Lunar and Mars Exploration Office.
That goes way back.
It has abolished and now restored again.
So, that is the cycle you go through.
And, of course, you're in really the phase A so it is going to be pretty hard for you to do the direct methods.
Even though you might try, it is going to be pretty hard for you to do that.
You almost have to use some type of a parametrics.
And I am going to talk about how you do a parametric.
I am going to talk to you about how you do both of them.
And this can get you into more trouble.
Cost estimates get you in a lot of trouble.
How many in here are familiar with what we call a work breakdown structure?
OK, good.
Work breakdown structure is really the management tool that is needed in doing a project.
Whenever you get a project you form a work breakdown structure which is a hierarchical breakdown, the work necessary to complete a project.
Work breakdown structure elements should be identified by title, by numbering system that performs the following functions.
It identifies the level of the breakdown structure element, it identifies the higher level to which the breakdown structure would be integrated and shows the cost.
That is the key thing.
It shows the cost account number of the element and how much it costs, how much labor hours is going to take.
That is a very, very important tool.
In fact, when you go out and work in industry, actually, if you become a member of a work breakdown structure, you're graded on how well you perform under this work breakdown structure.
That is the tool they grade you on.
We will put these charts on the Internet.
Roll of the work breakdown structure.
Project and technical planning and scheduling.
Cost estimating and budget formulation.
Project status reporting and plans such as specifications and drawings.
Now, those that raised their hands, where did you learn to do work breakdown structure?
Can anybody answer me?
Where did you learn to do that, those that said you were familiar with it?
Yes, sir.
I learned it here at MIT.
Did you?
Very good.
They taught you.
That's very good.
What course was it?
It is not a course.
It is my research.
Oh, your research.
Did you find it hard to do?
I found it initially difficult, but once I realized how to work it, I definitely saw the benefits of that approach.
Very good. Well, it is an important tool that you need to do.
And that is why it is probably a little hard for you to do cost estimation because you are not used to some of these things you need to do to get the cost done.
Well, some of the basic elements of cost estimation is understand the product, develop a detailed work breakdown structure.
Did you do that for this project?
No.
That is OK.
I didn't mean to put you under the gun.
Understand the development of the culture.
Understand the culture.
It turns out the NASA culture is pretty high level because it does involve risk.
And I will give you a little story about.
Somebody asked von Braun one time why NASA had to gold plate everything.
He said because you made it out of pure gold it would cost too much.
It is not that they gold plate everything, but it is that you really have a life concern in a very hostile environment.
You have to understand the development culture.
Gather data from close analogs, develop the cost estimate relationships.
There are textbooks that show you how to develop CERs.
There is a large society called parametric cost analysis.
And in that you can get how to develop CERs.
I am not suggesting you necessarily do that because it is very, very time consuming, but just know that they do exist.
There are, by the way, very sophisticated computer programs, which I want to talk about, that develop the CERs for you based on inputs you give them.
These programs are very expensive.
One is called PRICE.
I will show you what the other one is.
And it was actually developed by RCA.
It now is owned by the Martin Company.
Or was owned by the Martin Company.
Group CERs according to the work breakdown structure.
And you need to quantify the risk and the method.
Estimate the cost, spread the cost and do a reality check.
Those are some of the things you need to do.
Now, understanding the costing and the analysis process, as I said, you need to understand the project, participate in the design team activities.
Scoping, inheritance and complexity.
Identification of content, schedule and goals.
Collecting cost, estimating inputs by weight statements, technical characteristics, preparing the estimates, CERs, translating labor hours and dollar hours.
And this is a lot of details that you are not going to have time to do, but you do need to understand the complexity that doing cost analysis entails.
It is very, very difficult and very hard to do.
And you have groups set up to do that.
But, on the other hand, engineers working on a project are going to be called upon to do it because you are the best source of information that they have to do it.
Here is the basic building block of the parametric cost estimating, is the relationship of the cost estimating relationship.
And the dependent value variable is cost.
The independent variable is something that you can understand.
It is weight, power, ISP and so forth.
They are specific engineering terms.
And there is some relationship between weight, certainly for structures, there is certainly a value based on historical data points of weight of the structure, the type of materials and so forth on the CER, the cost relationship.
So, that is how it is developed.
A lot of students had a very difficult time using this program because they didn't know how the CERs were developed.
It frustrated them because here was this magic program that calculated the CERs for them.
Right, Josh?
Josh is one of my students.
And they had a very difficult time trying to understand how to use the program because they couldn't understand how to do the CERs.
But there is a methodology in it.
And there are many books that explain it.
The other thing that is important, as I pointed out, is the cultural variable.
The cultural variable is this.
See, this is one, unit dry weight.
And it can show us the total cost, but it can show that for aircraft you're on one culture plane, on an unmanned spacecraft you're on another cultural plane, on manned spacecraft you're on another cultural plane and on a planetary spacecraft you're on another cultural plane.
That is a very big issue.
One of the issues with NASA they say, to get the cost down for NASA, is you need to change the cultural plane.
Of course, if you change the cultural plane you probably have to give up something.
You probably would give up some risk in terms of safety or margin.
So, you have got to recognize that the cultural variable is a very strong indicator.
Are you happy to note that the aircraft is so low and everybody flies on an airplane, but that is the cultural variable that it shows.
For a structure, you can see how the structure varies based on the cultural plane.
When you were talking about like using square footage as a rough estimate for a house, and in the space business we do use weight as kind of a substitute.
You can translate from weight into cost.
And yet people always point out, well, yeah, but a kilogram of aluminum structure costs a lot less than a kilogram of computer chips.
But, nevertheless, when you put everything down when you're designing a planetary spacecraft, they do have these estimated relationships.
If you're going to have a project which lands 150 kilograms on Mars compared to a ton on Mars, we do have these relationships.
Because, in general, we figure that the ratio of hardware and software and computer chips to aluminum and all that is roughly similar.
But if you are going to try to build something that is fundamentally new, which involves a lot of new technology, then of course you can go way off of these rough estimates.
To get a good understanding, you might say a very quick understanding, you might go to the NASA website and get parametric cost analysis.
It will give you a very good understanding of what you can get.
And you can get some of these programs off the Internet today.
They are not very sophisticated but they do have some CER relationships, as Jeff was talking about.
It might be a little bit more difficult for some of the items.
Structures would be an easy item to do but, unfortunately, I don't think anybody is doing
that. But it would even be good for the avionics system, I think, in life support.
Yes.
Are these software packages basically just a large database?
They are basically a large database that you put in the data.
In fact, they are so sophisticated now, you can put in the software, the type of software you are using, the number of lines of code and, based on the CER for that particular subject, it can tell you how much it is going to cost per line of code.
It is very, very sophisticated.
And NASA uses it quite a bit.
Yes?
With this software, you must have to update it very, very frequently because of technology changes.
They update it very frequently.
That's right.
And that is why they are so expensive.
They are very expensive, but they update them.
For example, I started using it at A&M, and they didn't have even a software package in there for composites.
Now they have one for composites.
And there are a lot of these which are proprietary and you cannot even get access to them.
I mean the Aerospace Corporation has compiled a huge database of costs of a lot of components historical to how much it was estimated, how much it actually cost.
And so NASA and the DOD often go to Aerospace to do cost analysis for them.
And, of course, Aerospace charges.
And they don't release their database because it is proprietary.
Knowledge is power and money in this situation.
They put a lot of work into putting the database together.
Yes.
[AUDIENCE QUESTION] Were you able to try to use it?
Did you try to check it out?
[AUDIENCE QUESTION] And, of course, it may not have the update as this gentleman was talking about, but it has a certain amount.
You could do a pretty quick analysis.
I would suggest you try to do that because I know that I had looked at it, and there are ways to do it.
Now, you've got to be careful of the results because sometimes the results become pretty high.
But you've got to be careful of the results and look at it pretty carefully.
This is another development of cost scaling law.
This happens to be weight versus -- You can see the two different cultural planes, known cost and weight, unknown cost from a given weight.
This is basically how they generate the CERs.
It is a process.
It isn't an analytical process, but there also is a lot of empirical data that goes with it.
And, as Jeff said, it is based on a large database.
Now, cost estimation, I am telling you hard it is to do and you probably already know it.
But, for a cost estimation, now, this is after you get over the errors of parametric cost analysis.
Now we're talking about how you do a cost analysis when you're really trying to figure how you go forward to ask for a budget.
You need fairly detailed information.
It is unrealistic for designers to give cost information for conceptualist designs, but designers must be able to make rough cost estimates.
That is what I am saying, that you do need to be able to make rough cost estimates.
Now, if you are trying to make a detailed cost estimate, and that goes back to the work breakdown structure, you need the number of labor hours and number of people on the project.
I mean people is probably going to be the most expensive.
You need the number of labor hours, the number of people on the project.
During the Shuttle Program, Orbiter Project Manager, I used to call my counterpart at Rockwell every Saturday morning.
And we would go through how many people we had on each work breakdown structure for each contractor.
We would talk about it to be sure we had the budget to cover it.
And then, of course, we had to be sure we got the product out the door.
But the number of labor hours, the number of people on the project, the length of time these people are going to be on it, the overhead rates, office space, computer, benefits, cost per hour of a person basically is what you are looking for, that is how you really do a cost estimate.
And, of course, it is going to vary, depending on the locale of the contractor.
What are the cost drivers?
Now, here is where the cost comes out, some of the things that Dr.
Hoffman was talking about.
The errors in the design.
Change in requirements.
Core interface definition.
Technology development.
Poor communication.
Poor teamwork.
These are all elements of systems engineering that have gone awry, that have not gone in the right direction.
But this is what caused the cost to go up.
In my experience, the biggest problem in cost estimates have been the changes in requirements.
That is really the thing that has caused most of the problems.
That is why you need really good definition requirements and not change it.
Technology development, that can cost you a lot of money and sometimes you have to go forward with it.
Now, this is old data.
This is 1993 data, but I got this from a contractor a long time ago.
First of all what you need to do, and of course it is a lot different, I don't know if it is higher or lower today with CAD systems, this was before they really used CAD systems, but this the average cost of an engineering drawing.
And it goes through how you do it.
It is probably the labor rates are higher today.
The average hours per drawing are probably lower.
But this says in 1993, the rate is an estimate for 1993 government year of about $3,000 in average drawing, so you have to figure out how many drawings you need.
I mean that is a good way to understand the cost estimate of what it is going to be.
You need to know how many drawings you need and you need an understanding of the cost
settlement. The elements of cost during manufacturing then are the number and complexity of the drawings, cost of a drawing, number and complexity of machine and fabricated parts and what the parts are made out of.
Aluminum, steel, titanium, nickel, inconel and so forth, because some are more complicated to machine than others.
But some are used in the Space Program, some are not.
Titanium was becoming more and more important.
Other things of manufacturing are tolerance of parts.
It turns out engineers tend to, you might say, put extra tolerances on parts that they don't need.
And that can cause parts to be very, very expensive.
The finish of parts, the quality of parts, assembly, complexity and time qualification of checking a test.
I remember my first day at work, when I worked for RCA, I was designing a microwave tube, magnetron.
I was a terrible draftsman, as a matter of fact.
That was a long time ago.
I would probably be better with CAD systems.
But I sent out this part to the shop.
And this guy coming in showing this stogy out in the machine shop.
At that time we sat in these big bullpens, each person at a desk, and I had my name on my desk.
He comes in this big room and says where the hell is Cohen?
That is me.
He said this is the dumbest drawing I have ever seen in my life.
How do you expect anybody to make this part?
So, you have to be sure you understand what you are doing.
It turns out I learned to work with that guy and became good friends.
That never happened again, but he wanted to know where the hell was this Cohen who put out this dumb drawing?
He said there is no way I can make this part.
And that was a small part, but you need to understand the complexity of the part and what you're putting out to the shop.
But today they have checks and balances.
And, with the CAD systems, I am not even sure this is accurate anymore.
This about brings me to the close of what I wanted to talk to you about, but let me just give you one final chart.
And then I would like you to ask some questions about anything I talked about or anything anybody else covered that you heard about.
I would stress that for you today in your course is to try to use parametric cost analysis.
That is what I would think you should do.
At least that is what I think you ought to do.
And I think you can get information off the Internet that will allow you to do something.
Now, it may not pertain to all projects.
I am not saying you have to do it, but it might be the thing to do.
It is going to be very difficult.
Doing the right thing by creating a work breakdown structure in trying to do that, it is going to be very difficult for you to do it in this course.
But the parametric approach to cost, hardware costs are not produced from parts less than labor tables, so you don't need that.
They are produced from general measures of the impact of such items costs and in preparing inexpensive and more realistic and manageable costs based on cost estimating relationships.
You might want to do some reading on cost estimating relationships, and there are a lot of references to that, just to be sure you understand what I am talking about and what they are so it is not a complete mystery to you so you get a better feel for what it is.
A lot of textbooks have cost estimating relationships.
CERs make use of characteristics that can be readily quantifiable such as weight, size and to estimate variables that are difficult to quantify such as cost and production schedules.
As I said, parametric models can range from a simple arithmetical relationship to a sophisticated computerized model so they can be very, very complicated or very simple.
And I suggest you try to do that.
Let me just show you what the programs are, not that you will be able to get them, but when you get out of industry, if I can find them here.
Well, it may not happen.
There is certainly a lot of information.
Here is the price model.
That is price H.
And you can actually do structural weight material types, tolerances.
You can actually do electronics, digital, analog technology.
So, you do have quite a bit of latitude of what you do.
Now, you're probably not going to get that program here because it is pretty expensive and pretty hard to do.
But when you go out in industry or government there is a very high probability you will be using some of these programs.
And Johnson Space Center uses this one and the Marshall Space Flight Center uses this one, CRH.
There are two programs that are used by NASA, I know, and they are becoming more and more important as we go ahead.
Aaron, one thing you haven't discussed in all this discussion of cost is margin.
And, as a manager, you have to deal with that, so maybe you can make a few comments on that.
Sure.
Well, let me start off this way.
What Professor Hoffman is alluding to is that when you create a budget you want to have some type of reserve or margin over and above your cost estimate.
And that takes care of several things.
It takes care of changes, it takes care of I forgots and it takes care of inefficiencies.
Studies have found that in a high technology program for the first time you are about 30% inefficient, so you are only about 70% efficient.
Now, this was data that was taken some time ago.
You are 70% efficient, so you need to allow some type of margin in that for your inefficiencies.
If you do that and you talk about changes and you talk about I forgots, your reserve becomes very high.
And normally your boss, the guy that is over you is not going to let you have that much money.
One of the investigations we had on me during the Shuttle Program, because my cost was growing, a very famous man came in to be head of the program named General Abrahamson.
Many of you may have heard of General Abrahamson.
While he did the investigation, he said, Aaron, you need a large reserve.
He didn't know he was going to become manager of the program.
When he became manager of the program, I had this large reserve in there, he was reviewing and said you cannot have that much reserve so he wacked it down.
But you do need a reserve because you're not going to make it without a reserve.
And, I don't know if you noticed or not but in the papers I gave you on the cost of the Shuttle system, it had about a 30% reserve in there.
When I did the study for the 90-day study, I had a 50% reserve in there because I felt that was a pretty far out program and you needed a reserve.
You need to fight for your reserve, but I guaranty you're not going to get everything you think you need.
Yes, sir.
For something like aerospace, every time you do a cost estimate, they talk about it, look at it and say, well, let's increase that by 50% or double it.
And often, even once you've done that, you still don't come under budget.
I mean look at the ISS or the Airbus 380 that is going out.
Why?
Well, again, it is really because -- First of all, it is primarily for the inefficiencies.
You just cannot do a high-tech program.
Look at what it cost to do the Big Dig, to drive it home.
It is very difficult to do a good cost estimate, but that is the problem that Congress sees with government programs today, both the Department of Defense and NASA, that they cannot do a good cost estimate.
The current program says they are going to do the CEVing and go to the Moon for $104 billion, which is 55% of what it cost to do the Apollo Program in current year dollars.
And that is going to be interesting to see if they can do it.
It is tough to do.
But really I think the biggest problem is your inefficiencies.
Of course there are changes and I forgots.
Interesting enough, though, you may or may not believe this, and you probably won't but I will say it anyway, it turns out that the studies done for the Shuttle Program, for the Orbiter actually, in real year dollars, met the cost if we would have gotten the inflation rate.
We lost the inflation for two years, which Dale Myers fought for vigorously with OMB.
If we would have gotten the inflation for those two years, we would have met cost for the development cost.
Not for the operational cost, but for the development cost we would have come pretty close to it.
We didn't really miss it that far.
In Apollo, I'm not sure, you would need to ask Dr.
Siemens, but the story goes is that NASA came in with an estimate.
And at that time the administrator, Webb, looked at it and said that is fine and he doubled it, and so Apollo did very well.
I think Bob Siemens has told that.
The story we heard was it was on their way over to the White House that he said our final estimate, we've put all the factors and everything in, is $10 billion.
And Webb said, OK, we will tell the President $20 billion.
I am sure Bob Siemens would know.
Yes, sir.
Aaron, I wanted to ask you about the location of the reserves.
Not just dollar reserves, but my experience as a payload [NOISE OBSCURES].
The model I have been faced with is that the mission manager has a reserve for crew time or for weight of something but, down on the project level, you would really like to go and have your own.
And so there was a tendency for everybody but the lowest level, from the individual experiment up to say, well, I am going to put in a little bit of pad rather than count on the fact that I can go up to the mission manager and ask him for some reserve later.
Well, that is the danger with that.
You are absolutely right.
Everybody would like to put their own reserve in.
Of course, being a project manager, I thought the reserve ought to be at my level.
But actually, John Yardley was my boss in Washington, and he thought he should handle the reserve.
And the subsystems managers wanted their reserve, right?
Wanted their reserve.
And John Yardley was another person I should have mentioned.
John actually basically pulled the reserve up and handled it in Washington.
There is a certain efficiency, I assume, in having all the reserves centralized so that there is not a lot of waste down to lower levels, but you have to have the confidence that you are going to be able to draw on it.
Right.
And with that John would partial out some.
What he would do is be sure that you weren't double reserving him or triple reserving him.
And then he would allocate it to me.
I know he had a rule of thumb.
When JR Thompson went up, you heard JR talk, he always asked for more than he needed, so John would give him less.
When I went up, I always asked for less than I needed, so he would give me more.
He had a good feel for his managers.
That is what he told JR one day.
Normally, you wind up handling it.
If you have a good program manager at the top you normally wind up handling it there and he parcels it out based on the fact there is no double bookkeeping.
Yes.
My experience at Draper is typically there are two different ways of estimating.
One was called top down and the other was bottoms up.
And traditionally bottoms up would always stick their reserve in some way and top down would always say I want to know what your reserves are because I want to bring it up to the top.
And that was a constant argument.
Then when you got to submitting your proposal often the customer didn't want to know about this extra money and then you would have to shove it back in and hide it, in a sense, by padding things.
Handling costing in reserves is, to some extent, at least in my experience, a psychological thing dealing with customers and your management.
And it has always been one where you shuffle that reserve around.
But this gentleman asked the question about why does it appear that NASA never can stay on their budget?
That is really a tough question to answer.
I don't know.
I mean I have a personal feeling on it, but I think the basic problem you have is that it is a high technology program.
It is one of a kind and it is a lot of inefficiencies.
When you come to work every day, you don't know exactly what you are going to do.
You have a technology development that costs.
You have I forgots.
You have changing requirements.
Changing requirements are something that systems engineering ought to be able to control.
I forgots are something systems engineering ought to be able to control.
Inefficiencies, to a certain extent, systems engineering ought to be able to control.
That is one of the purposes, in all honesty, that are concentrating on system engineering at such places at MIT and other schools to allow the future generation of designers and developers in working that they can have a budget and then stay on the budget.
Maybe in your generation you will be smarter and able to control it, but it is not going to be an easy job.
That is one thing I would say.
Let me just make one other comment.
We cannot estimate too much.
That you've got to always keep in mind this triangle of cost, performance, schedule.
If you are working on a project where the schedule is fixed like Apollo then that better ring the bells to say that I need more reserves.
And maybe that is what was going on in Jim Webb's mind when he said if we really have to get this done by the end of the decade, I better make sure that I am not going to be constrained by cost and so I will double it.
The other thing that you have to take into account with the performance is how much new technology is this program going to require?
Because the new technology, that is the hardest thing to estimate the cost.
That's right.
And so, if you have a new technology program then your margins better be big enough to accommodate that.
That is why, for the CEV, they are really going out of their way to saying, to the maximum extent possible, we don't want to develop new technology for the CEV.
We want to use Shuttle parts wherever we can, Apollo heritage.
We want to build it out of things that we know and we understand so that we hopefully can keep the cost as low as possible.
And we will see how it all works out.
Yes, sir.
It seems to me that you often times have the pressure to give a cost estimate on the low end of what you believe it to actual be just so the project might be more appealing [NOISE OBSCURES].
That is certainly another part of the whole political thing.
And not just from the political point of view of presenting your estimate when NASA presents the estimate to Congress, but then you have the contractors who want to get the contract from NASA.
And you have certainly had experience with this.
How do you deal with the contractor who low-balls and then assumes that they will be able to make it up later on?
Low-balling really should not be tolerated.
And they try to do that, not tolerating it, but you are absolutely right.
When I did this 90-day study, I really felt they wanted to know what it was going to cost, so I had a 55% reserve in there because I really felt that there were so many unknowns with it.
And, of course, that didn't go over very well.
They said my study actually killed the projects.
But I told them what it was going to cost.
And then this is a subject for another lecture entirely, which I am not sure that we are going to do in this course, but there are many different ways to let out contracts, fixed price contracts, cost plus contracts, award contracts.
And all of those can have an impact on the ultimate cost of your project.
And they all have their utility depending on how well the technology is known and what is the time pressure.
Again, cost, performance, schedule.
And you asked about Airbus.
I don't know the specifics of Airbus contracting, but I am familiar with ESA.
And, because of some of the peculiarities of the European system, they tend to use fixed price contracts a lot more than we do here.
And sometimes it works but sometimes you get really burned on it because contractors are not going to go into bankruptcy because they cannot deliver on their fixed price contracts.
You try to go fixed price on the CEV and it would cost you a fortune.
Those are very good questions.
Unfortunately, we don't give you very firm answers on cost.
But at least you are thinking and I appreciate your thought process.
It is very encouraging to hear you ask those types of questions.
Have a good weekend.
We will see you on Tuesday.
Free Downloads
Video
- iTunes U (MP4 - 243MB)
- Internet Archive (MP4 - 396MB)
Subtitle
- English - US (SRT)