Flash and JavaScript are required for this feature.
Download the video from iTunes U or the Internet Archive.
Topics covered: The Origins of the Space Shuttle
Instructor: Prof. Hoffman, Prof. Cohen, Guest Lecturer - Dale Myers
Subtitles are provided through the generous support of Heather Wood.
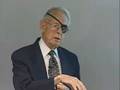
Lecture 1: The Origins of t...
HOFFMAN: Welcome everyone to 16.885.
And I guess this is ESD.35 as well.
I think.
I cannot keep track of the number.
Formally the title is Aircraft Systems Engineering.
I never thought I would actually be teaching a course with aircraft in the title of it since I am not an airplane person, I am a space person.
But, as you all know, we have decided to devote the course this year to a study of the Space Shuttle.
Very briefly, what the course has been historically, it was taught for quite a few years by Professors Murman and Hansman in the Aero-Astro Department.
It is a course in systems engineering devoted to aircraft systems.
And what they typically would do would be to have a series of lectures about principles of systems engineering, and also about various systems - general systems in aviation.
And then, as a class assignment, the students would work in teams and choose an aircraft and do a systems analysis study of that aircraft.
Well, a couple of years ago we were just sort of sitting down and chatting.
And someone brought up the idea that well, you know, the Space Shuttle kind of is like an airplane.
Maybe it would be interesting to devote the course one year to a special study of the Space Shuttle.
And that was actually the origin of what we are doing this year.
Following that, Professor Aaron Cohen, who is sitting over here, and I will introduce him in more detail in a minute, visited MIT, I think it was early last year, and gave a few lectures on systems engineering and the development of the Space Shuttle.
And we started talking about putting together a course on the shuttle.
And we were very fortunate now that this fall Professor Cohen is here as a visiting professor.
And he will be here at MIT roughly about half the time.
And he and I have put this course together.
And the way we are going to organize it is that we're going to emphasize two main areas.
First of all, to get to an understanding of the Space Shuttle as a flying machine, as a spacecraft, and also to study systems engineering as an engineering discipline.
We have put together a list of speakers, and I am going to pass out here copies of the syllabus.
If you will pass these around.
I have also established a stellar class website and, once you are all enrolled in the course, you will all have access to the website.
If any of you are here as listeners or for some other reason don't get formally registered to get course access, contact me independently and we can set you up for a special access so that you can look on the website.
If you look through here you will see that most of the class periods are devoted to guest lecturers.
And, thanks in large part to Professor Cohen, we have actually been able to invite people who played pivotal roles in the very early stages of the design of the Space Shuttle.
And also people who played pivotal roles in the testing and eventual operation of the
shuttle. So we have people who are active in the design and also some people who were critical in Mission Control and in the test flights of the shuttle.
It is, I think, a really unique collection of speakers.
And because I don't think there has ever been a time where this sort of a collection of people has actually come together to share their experiences on the shuttle.
And because we thought that it would have historical significance, and people would be interested in being able to look at that in the future, we are having the lecture series taped for eventual inclusion on MIT's OpenCourseWare.
So that is why you see the television camera in the back.
No need for all of you to dress up for it, but just so that you know.
The way we plan to run the course is as follows.
The lectures will run roughly about an hour, we will take a little break at the end of an hour, and then there will be an opportunity basically for close interaction between you in the class and the lecturer.
It is kind of free form because we have lots of different lectures.
Of course, there will be some variability in the way lecturers go about presenting the material.
Professor Cohen and I will attempt to make sure that, in each case, we do emphasize some of the basic systems engineering aspects of the presentation.
We want you to understand the principles of how some of the different subsystems were designed, basically how they were influenced by external requirements to make sure that we understand what the requirements were, how the systems were constructed and tested, and how they were operated.
What we will be asking from you in terms of your deliverables, first of all, we would like you to take notes on the lectures.
We will post the lecture notes on the website.
If you look through the schedule that I have given you here, you will see that I list the deliverables, and I am going to have to adjust the timing on that.
Two times in the course we will ask to see the lecture journals.
What we are looking for is to make sure that we are presenting and that you are getting out of this the basic systems engineering principles for each of the subsystems that are presented.
And we will talk a little bit about journal notes in the future.
The main deliverable from you will be a little bit different from in the normal Aircraft Systems Engineering course where groups of students basically chose and airplane and then looked at the design of that particular airplane.
We are only dealing with one vehicle, the shuttle, so what we will be asking you to do is choose one of the subsystems on the shuttle.
And, as you look through the notes, you see we will have information presented on a lot of the different subsystems.
I have a lot of material available, and I will go over that a little bit later, both in digital form and in books which we will have on reserve at the library which go into great detail on all the different subsystems.
So we have lots of information, as well as experts that you can talk with.
We will ask you to form up into teams, roughly four people on a team, more or less.
Choose a subsystem.
And then, basically, write a paper on how you would design that subsystem, if you were doing it today, using 21st century technology.
It gives you an opportunity to understand the subsystem, as it was designed for the shuttle, and then to take a look at current technology in that subsystem.
I know there are some people here from Engineering Systems, as well as from Aero-Astro.
People may have some other ideas.
If you have some ideas about writing about systems from a systems engineering and integration point of view or any other particular personal ideas of what you would like to do as a project which is slightly different from specifically working with a subsystem, come see me and we will talk about it.
The main thing is to make sure that you have a chance to explore some aspect of the systems engineering of the shuttle in greater depth.
That is all I am going to say right now.
Go to the website.
I will be posting more information because I want to give as much time as possible to our two speakers.
I, by the way, will be posting bios of all the speakers on the website so you will be able to look ahead of time and get an idea of who it is who will be speaking to us and what their roles were in the development or testing or operation of the shuttle.
So I would like to present now Professor Aaron Cohen who was born in Texas and has had a very distinguished career at NASA.
Just very briefly, he was the project manager, I guess first in Apollo, he was the Command and Service Module Project Manager.
And then he was the Project Manager for the Space Shuttle and eventually became the Center Director of the Johnson Space Center in Houston.
When he retired in the early `90s he took a teaching position at Texas A&M in the Mechanical Engineering Department where he is now Professor Emeritus.
And we are extremely fortunate to have him here co-teaching the course with me.
So, Aaron, I will turn it over.
COHEN: Thank you very much.
And it is a pleasure to be here with you.
I have a few things I would like to talk to you about very briefly and then I will turn it over to our guest speaker today.
I would like to let you know what you can expect for the next several lectures.
I am going to provide you with the overall shuttle, how the shuttle works, the requirements of the shuttle, the design and the development of the subsystems to a certain extent to give you an overall view of the shuttle so you will have a background of information when you later start to hear the detailed lectures of the subsystems in some degree.
As you listen to these various technical lectures, you should be prepared to figure out what system you are really interested in and what system you would like to move forward with in your future talks.
And so you will see that.
So that is what I will do in the next two lectures, Tuesday and Thursday.
In trying to figure out how we start the course, I went back in my memory to figure out a man who was there at the very beginning in Washington.
And this man, Mr.
Dale Myers, who is going to talk today, is what you might say is a true aerospace engineer.
He had a very distinguished career in both industry and government, in aircraft and space.
Dale, or Mr.
Myers, who was Deputy Administrator at NASA from October 1986 to 1989, and that was when President Regan called Dale Myers back to be Deputy Administrator after the Challenger accident.
Mr.
Myers was Corporate Vice President of Rockwell International, President of the North American Aircraft Group, where he was responsible for the B1 and various military and commercial aircraft.
In 1970 he has been an Associate with Rockwell International and Vice President and Manager for the Apollo Command and Service Module.
So he was Apollo and Shuttle.
The key thing that Mr.
Myers is going to talk to you about today, he was the NASA Associate Administrator for Manned Space Flight in 1970 when the Space Shuttle began.
And Mr.
Myers is going to talk to you about the beginning of the Space Shuttle and how the external environment helped create or generate requirements that really forced, you might say, the configuration of the shuttle.
And I think it is very important for you to understand that, because many times, when you get out and start to work, go to work, the requirements become generated by external environments.
So, without further ado, let me turn the speaker over to Dale Myers to give you his lecture.
MYERS: Well, thanks for the opportunity to talk to you guys about a very interesting historical element.
I was asked to talk about the origin of the shuttle.
And I was there in 1970.
And I think once we get this thing working where I can run the slides -- The joy of electronics.
When I first went to work for North American Aviation we used Marchant Calculators where you put in your numbers and pull a lever and actually move it to the next position.
And we did a lot of dynamic analysis.
And it took weeks to do a total dynamic flight analysis of an aircraft with a Marchant calculator.
Now we have the wonders of the computer.
The first airplane I worked on was a P51 Mustang, a fighter in World War II, and that had some interesting system engineering issues in it, too.
They used the inlet, it had a liquid cooled engine, and we had a radiator that was in a duct.
And the air came through the radiator, cooled the liquid and heated up the air that was then properly adjusted with a flap at the back of the radiator that gave it thrust out of the heat that was involved coming through the radiator.
That is the reason why the Mustang is about 15 miles an hour faster than the German's ME 109.
That is one of the prettiest pictures I have ever seen of the shuttle.
That is a picture of the additional photography that they brought into the system after the Columbia accident, and this was used on this last flight.
The first time I had ever seen the rearview of all the connections for the transfer of fuel from the tank into the shuttle, the connections to the tank, the forward bipod where the foam was that came off on the Columbia accident, just a terrific picture of all the tiles up under the wing that Aaron was so involved with.
But what I want to talk about, oh, here is another one that is really a first for me.
This is the mach 1 shock on the shuttle about 20,000 feet altitude, mach 1.1.
That big envelope of condensation, not as pretty as it looks on an F-18 or some really slick airplane, but it is there.
I am going to talk about what happened leading up to the shuttle.
And it is interesting because it involves the specific interests and personalities of the people who were involved.
Jim Webb was the administrator of NASA from 1961 to 1968, and he was a terrific interactor with the rest of the administration and with the President directly.
And did a great job of administrating NASA through the Apollo program up through 1968.
It turned out in 1968 things were kind of going sour for President Johnson.
Webb's big tie was with President Johnson, and he ended up leaving in 1968 after he suggested to President Johnson that he might want to leave some time soon.
I think he was thinking he was going to stay through the Lunar landing, but Johnson said why don't you leave now? And I don't really understand the interaction that was involved there, but Webb did not want to make future plans.
He really never paid much attention to the work that was being done inside the system on new ideas, new things beyond Apollo.
Of course, the Apollo was an immense program, 400,000 people.
Well, 300,000 on the Apollo, another 100,000 on other activities in NASA like the aeronautics program and the science programs.
But Webb didn't want to talk about things that were going to happen beyond that time period.
In the meantime, in the back rooms a lot of people were doing a lot of thinking about where does NASA go after the Apollo program? Apollo at that time, that Webb was there, had planned to go through Apollo 20, I think.
And so it was going to go on until 1973 or so.
And so I think Webb took the attitude that we don't need to think about the future yet.
Well, when he left in 1968, they brought in a fellow named Tom Paine who had been at General Electric Company doing advanced planning for General Electric, a very bright, very aggressively forward-thinking guy.
A guy that I always felt never saw a future plan he didn't like.
And NASA was doing a fantastic amount of future planning at that time because in the 1968 time period, we had just done the Apollo 7, gotten it back into flight again.
At the end of '68 we did the Apollo 8 which went around the moon, and NASA could do no wrong at that time.
They were just on a step.
And with Tom coming in, in early '69, all the work that was being done by NASA at that time, the idea was that the NASA programs were going to continue to grow and that you could really begin to do some expansive thinking about going out into space.
There had been work going on since 1964 on lifting bodies and on different configurations that people imagined could be used for traveling in space and returning to the ground in a more sophisticated manner than coming down on parachutes in the water.
Water landings were extremely expensive, having the whole Navy out there to support them, and so people were beginning to think about land landing.
And by 1969, enough pressure came on the administration that Nixon appointed his Vice President, Spiro Agnew, to run a program reviewing the future of NASA.
And he got a really good group of people together.
He got Bob Seamans, I am sure you all know.
Tom Paine, the Administrator of NASA, Lee DuBridge had been head of Caltech and was the Science Advisor to the President.
They had a guy that was the head of the Atomic Energy Commission and the Head of the Bureau of the Budget.
They did about a six month study supported by NASA.
And NASA's dreams were that there should be a space transportation system that would include the moon and finally Mars.
And it started with a 30 foot diameter, 12 man space station, two of them in earth orbit, possibly reaching 100 people in earth orbit.
Another space station the same size around the moon with 12 men.
A lunar base.
A nuclear stage to transfer resources from earth orbit space stations to the lunar orbit space station.
A two-stage fully recoverable shuttle with 100 to 150 flights a year because of this massive program that was being developed.
A SkyLab with five visits by the Command Module.
This, by the way, was a second SkyLab.
SkyLab was in our program, and a second SkyLab was under construction at that time in this time period.
And, of course, to do all this, we would continue the Saturn 1b and the Saturn V production.
Those were the big rockets involved in the Apollo program.
And space tug to go to higher than low earth orbit - to geosynchronous.
And, as I mentioned, the nuclear stage.
And a mars program by 1983.
That was all presented to this group, and they ended up setting up three different programs.
One was this massive all-inclusive program.
A second one was a program where the Space Shuttle would be built and the plans to go to Mars.
I never found the report so I don't know exactly how to describe that.
But, to go to mars, the NASA program said you have to have a space station to first develop medical information about man's long duration in space, in other words, how long a guy could last in space to go out to mars, and it became a fuel transfer operation, where low earth orbit rendezvous and docking and transfer of fuel would be made for a device to go onto mars.
So, that second case, the one of build the shuttle and go to mars was the one that Agnew and Paine recommended.
Paine, in his mind, said there has got to be a space station with that.
And so he left in place the studies that NASA had out with industry on building a space station.
And NASA then started a program on a fully recoverable two-stage shuttle.
There have been a lot of studies on how to do that, and we are going to get into some of the system dynamics that we were involved in that program as we go along here.
Meanwhile, the budget crashed.
NASA had a budget of about $6 billion in 1968.
And, by 1970, it was down to about $3.7 billion.
Actually, at the same time, the Manned Space Flight budget had gone from about $3 billion down to $1.7 billion.
So it got hit even harder than the rest of NASA during this time period.
And the reasons, well, we were in the middle of the Vietnam War, the budget deficit was going up dramatically, President Johnson who started The Great Society program for the poor in the country, and that was a big load on the budget.
And Nixon just wasn't a big supporter of the space program, and so the budget was going down.
The question was is there going to be a human space flight program at all? And that was a really big question because in a time period about a year after this period, one of the senators put a bill before the senate to cancel the shuttle.
The Shuttle Phase B program was underway by that time.
We did studies.
Phase A, a small amount of money to industry.
Phase B was enough to get a definition to where you could decide that you were ready to go into detailed design.
And Phase CD was actually the design and development and testing.
So we were into Phase B on the shuttle at that time.
He brought forward to the senate let's cancel the shuttle, and the vote was 50/50.
So the Vice President had to go in and vote to keep the Shuttle program going.
That is how close to cancellation it was.
Now, a really important guy in all this was a guy named George Miller.
He had been head of the Manned Space Flight program.
He had been the stimulus within NASA for this broad systems study of going out to lunar bases and then to Mars.
And he left in late 1969.
He had done his job.
He got man to the moon and home safely, and he saw this cut in budgets going on.
I don't know whether that really influenced him to leave, but I think his general pattern had been that whatever he wanted to do, he wanted to complete it successfully and then he would move on.
And he did that with the Apollo program so he moved on.
George was a guy that really supported this tremendous set of future dreams for NASA.
Tom Paine left in late 1970.
And the reason he left was he kept pushing for a space station.
And the people in the administration had kind of seen the studies that had been done by this Space Task Group, where Agnew had said let's do the Shuttle and then let's go to Mars.
Paine, knowing in his few that you had to have a space station to be able to go to Mars, kept pushing the 12 man space station that would require a Saturn V for a launch so it was a big expense.
And it was a program that really called for NASA's budget to go up instead of down.
He accepted the idea that it had been pushed down to the $3.7 billion level, but he expected it to be $6 billion or $8 billion by 1974.
And nobody in the administration was buying that so he left in 1970.
And I think he was sort of asked to leave.
I don't know that for a fact, but all the evidence would seem to be that he wasn't really making it with the administration.
And I think this, by the way, turns out to be kind of an important part here because when Tom Paine left there was kind of a bad taste in the administration about NASA being too aggressive and wanting more and more big programs.
Paine left in 1970.
George Low became the acting administrator, and he became a very important part of the shuttle system background.
His background, by the way, started way early in NASA.
And he had been the program manager for the Command and Service Module for a period of time before he went up to NASA headquarters.
And I guess, Aaron, you became the program manager after George left.
And so I came in, in January of 1970.
I had been in charge of the Command and Service Module at Rockwell.
And George Low asked me to come back.
And I had worked so closely with George that I felt kind of a commitment to help in that area.
So I went back in 1970, Jim Fletcher came in, in April of 1971, and we saw where we stood as far as the budget was concerned.
So 1970, with this new cast of characters, we kind of accepted the idea that we were in trouble to the place where we could lose Manned Space Flight completely.
And our real strategy had to be to get something that would be important to the future of NASA with respect to the programs.
And our view was the most important part of the game was to build a shuttle that would reduce the cost of getting into orbit.
And that was the whole idea of the shuttle.
There was a general consensus that if you had a shuttle that would be recoverable and reusable it would reduce the cost of the operations.
As they used to say in those days, I think I have it on another chart, you wouldn't think of flying from San Diego to Boston on an airplane and then throwing away the airplane.
Which was, of course, what we were doing with the Ballistic systems.
But we thought if we could get a low-cost transportation system to a low earth orbit the rest of the systems would then follow naturally.
But, because of the budget picture and because of where we stood with the shuttle in Phase B recognizing it was going to be an expensive program, things started to fall out of the program.
They cancelled the Apollo 18 and 19.
I guess 20 had already been cancelled.
And they cancelled Saturn 1b and the Saturn V which were our big heavy lift capabilities.
Cancelled the second SkyLab that was already essentially complete.
That is the one that is in the Smithsonian Museum in Washington.
Cancelled the Command and Service Modules.
Cancelled the 30 foot diameter space stations.
And that was a big hit against the group because we were in phase B there getting ready to go into detailed design on a 30 foot diameter space station.
We didn't start the space tug, we didn't start the nuclear stage and we cancelled the Mars program.
No, excuse me, we deferred the Mars program.
Industry went down from 400,000 people working for all the NASA programs down to about 150,000.
I have seen numbers lower than that.
Now, concept for the shuttle, reusability equals low-cost.
That was fundamental.
Everybody believed that.
We had studies done by all sorts of outside groups.
IDA, the Aerospace Corporation and others did studies that essentially agreed with us that there would be a terrific reduction in the cost of getting stuff into orbit if we would build a recoverable vehicle.
Now, it was clear that since the R&D already T&E costs are higher, but you need a whole bunch of flights.
If you had a few flights, the extra R&D on the shuttle wouldn't pay off because you could build cheap Ballistic launch vehicles that would pay off before the shuttle.
So you need a lot of flights for a recoverable vehicle to be economical.
The lower the R&D the less flights needed to be better than the Ballistic launch vehicles.
And, if you got a lot of flights because the flight costs are so low, then a two-stage fully recoverable system would be the right way to go.
That was our concepts of what we were dealing with on the shuttle.
There has been a lot of technology.
I don't know how many of you know that the early lifting-body was done by a guy named Burnelli.
Not Bernoulli but Burnelli.
Burnelli was in Long Island and he built the first lifting-body.
That is an airfoil section and that is a broad piece of fuselage wide enough that the two engines could be involved in it.
Big windows for transport.
It was really quite an interesting beginning of a cargo airplane in 1921.
He built one of them and that was the end of that, but there were a lot of other things going on.
After Sputnik, the United States just kind of went wild with ideas for a while and then settled down on having NASA put in place, deciding that the military dinosaurs and mold programs wouldn't be done, that NASA would take over that kind of activity.
But we got some really interesting stuff going.
HL-10 lifting-body.
X-24A lifting-body.
X-15, although that was not considered a space device, by the time they put external tanks on it, it got up to mach 6 and 300,000 feet.
Really some terrific performance out of that airplane.
And then I added the Navaho, which I worked on for many years, because it had a parallel tank separation at mach 3.
The booster was under the vehicle.
The vehicle was a ramjet vehicle and it separated at mach 3 at about 40,000 feet.
It was a high dynamic pressure separation, but it showed us that parallel separation would work.
And that gets into this picture later.
Next step was in that '69 to '71 time period this guy named Max Faget who is really important, almost a genius in my mind in design that did the original Mercury and Gemini capsules, physically designed the shape of the Apollo Command Module and then came up with this first sort of practical view of a two-stage fully recoverable system.
It had straight wings like an X-15.
In fact, if you looked at the plan form, it looked quite a lot like an X-15.
But it had two of them.
It had pilots in each of the two stages.
It had internal fuel.
It had metal shingles, what I used to call unobtanium, but it was like molybdenum and Rene 41 and some really interesting materials which were really difficult to handle.
Stress, corrosion problems and all kinds of things that were tough to handle.
That is why I talked about unobtanium or some ablative.
And Max expected to have to use ablative on the leading edge of the wings.
And it had varying payloads.
The highest one I saw in any of the history was 20,000 pounds.
But 14,000, 20,000, that kind of thing.
A payload bay of about 12x40 and 400 miles max crossrange.
This gets important in requirements.
And, at that time, because we were going to have all these space stations and go to the moon and all that sort of stuff, we were going to have 100 to 150 flights a year.
And, if you have a lot of flights, it overcomes the base cost of the RDT&E.
And he was getting down into the $5 million a flight in his estimates.
But, meanwhile, because we had lost the space station, we had lost the lunar base, all this grand plan had disappeared, we needed more payloads.
We needed to get up to the 40 to 50 payloads a year to be able to make the shuttle look economic at the levels of cost-effectiveness that the Office of Management and Budget was demanding of us.
After this vote in the senate, George Low decided that we had to be responsive to the OMB so we had to get some more flights.
And this is where our requirements began to come into the picture.
We spent about a year working with the military where they finally agreed they would put all their payloads, and I mean all their payloads on the shuttle if we could meet the cost estimates that we had.
The commercial people were eager to get on the shuttle if our costs would be this low because they were beginning to see launch costs equal to or more than the cost of the satellites that we were putting up.
And the science people bought into the idea of space servicing.
This really got important because they agreed to design the Hubble Space Telescope so that it could be serviced in space.
And that turned out to be, of course, the key to the Hubble because of the mistake that was made in the mirror.
The re-servicing of the Hubble Space Telescope, is what - by bringing another optics in front of this distorted mirror - brought the Hubble back to the fantastic performance that it has today.
MAN: In your opinion, was the science community really anxious to have this servicing or was it something that was really forced upon them to increase the constituency? MYERS: I think originally they thought they were being forced.
But, as they thought it through, they could see that they could later change sensors and add additional stuff.
At least I know that the head of the science group, I cannot think of his name now, enthusiastically supported that and got the system out there to support that idea.
And they worked very closely with us on how to design it so that you could get access to the thing in space.
With all the difficulty we had with gloves and so on, they worked to help us understand how to remove and replace systems.
MAN: Was there at that time, if you recall, an opposition from the space science community to the size of the NASA budget that was being spent on the shuttle in the Manned program?
MYERS: Oh, absolutely.
Yeah, there was.
But, on the other hand, some of the committees like the town committee supported the shuttle because they could see other science opportunities that were involved.
So they didn't gang on us.
They were shooting arrows at us here and there.
And let me go on with the requirements.
Because of the military requirements, we had to change our specifications.
And this became another one of the elements that drove the final design.
The military wanted a 60 foot long payload bay.
It had been 40 in the designs that we had been doing so far.
They wanted 40,000 pounds Polar, and that made our due east payload up to about 65,000.
That was a big change from 20,000 to 65,000.
And they needed 1,500 crossrange.
They wanted to be able to go around the earth, while the earth turned, and land at the same spot.
So they had to have 1,500 miles of crossrange.
Now, you can do it a lot of different ways.
You could carry turbojets when you came back in and fly it back the 1,500 miles, or you could do it without turbojets which means you have to have aerodynamic crossrange while you are coming in.
Payload bay increased to 15x60.
15 was an increase by NASA because they saw that they didn't have a Saturn V anymore to do space station, so the best they could do was increase the diameter of the shuttle to where they have a 15 foot diameter to where they could carry the sections of the space station that we now have in the program.
We thought anything less than that was just too cramped for the guys.
We decided that we would find a non-ablative reusable thermal protection system.
Technology had moved far enough by that time that we were beginning to see these ceramic tiles develop to the place where they looked feasible.
They had been able to find a hardening for the surface that made them less penetratable than they had been.
And carbon-carbon came in that we could use for the leading edge, for 3,000 degree leading-edge temperatures.
We followed the tradition that said if it is fully recoverable it is going to be cheaper so let's go for a two-stage fully recoverable system.
And, of course, all the other things that we were developing at that time to reduce the cost of operations with automatic checkout and so on.
Well, that's a bad picture.
I am not an expert at this stuff so I wasn't able to get that slide down far enough to show where the Saturn V was, but Saturn V is only about 50% longer than that upper stage there.
So this thing had gotten big.
And the booster was larger than a 747.
It had to operate up to about mach 6.
The orbiter was about the size of an MD-80, MD-90, twin engine small transport.
And so they were big.
And these things had 12 big high-pressure engines in them.
And we in management, and I think the guys in design, were getting pretty worried about whether an airplane that large at that mach number was going to be a practical thing in terms of a system.
And that's not a system engineering approach.
That's sort of a gut feeling that you get after being in the airplane business for a lot of years and watching the development problems that were involved on the X-15, for example.
How long it took the X-15 to get to where it could go to mach 6.
But that was the direction we were going in.
By the way, one of the companies had the wings on the orbiter turned up.
I don't know why, but they had them turned up.
And by the way, the reason you see two different configurations here is in our phase B studies to the industry we said design us one that only has 400 miles crossrange and design us one that has 1,500 miles crossrange.
The upper ones have 1,500 miles crossrange.
And the delta wing will do that, the straight wings won't.
So, as we developed these requirements, it became clear that we were not going to go with a straight wing system.
These phase B studies that we had showed that we were going to have a development cost of some place between $12 billion and $15 billion for R&D.
And about that time Nixon had a meeting with Fletcher and said you can build any kind of shuttle you want, as long as it only costs $5 billion.
Well, that was a big shock to the system.
And, having heard that, OMB said make it cost-effective.
And that was a real tremendous driver in the system because we had never been asked to do that before.
And we had a whole new set of requirements to try to deal with.
So we had had this phase B program, it was almost complete, we had all these big, beautiful configuration studies and we had to look again.
So we went out and said let's get imaginative, guys.
Let's see if there is any way that we can reduce the cost.
There had been enough going on where one of the companies had been looking at the possibility of putting external tanks like drop tanks on the top of the wing on each side, two of them, one on each side of the orbiter.
And it made the orbiter itself, of course, much smaller.
Remember, we were carrying hydrogen and oxygen, and we were doing it inside the vehicles.
It is in those studies you saw in phase B.
And so it grew the outside dimensions tremendously.
And by going externally with the fuels, it really shrank down the system to where the diameter of a payload compartment was essentially the diameter of the orbiter.
And so people began to look at other ways to do it.
We had guys coming in talking about single-staged orbit.
And that was one that I rejected without study because I knew that the mass fractions required for that were just out of the world of reality.
There was a thing called a "trinese" where the theory was you had three vehicles.
They were deltas and fit together in a nice little teepee.
And two of them would be used for boosters going up and the third one would go on into orbit.
And that was kind of a dumb idea.
Because it turns out boosters and orbiters have entirely different requirements.
And so they might look the same on paper but they would not be the same when you build them.
Lockheed came in with an X-24b which had tanks mounted up forward of the delta wing.
And the idea would be that they would peel off after fuel was fed to the main engines in the orbiter itself.
And then we began to see these external orbiter tank studies.
And when the tanks began to look good externally then the question is do you boost from under the tank or do you boost with two boosters parallel to the tank itself? When the tanks went external, it finally ended up obvious that it would want one tank instead of two.
So the one tank went underneath the orbiter.
Then the question is do you boost through the tank or do you boost in parallel to the tank with two attached boosters?
So we had all these different studies.
And what was happening in the administration was they were kind of locked up with reducing Manned Space Flight budget down to like $1.5 to $1.7 billion.
And we needed to do this cost-effectiveness study for OMB.
We hired an outfit called Mathematica which had a senior well-known economist named Morgenstern and a bright young guy named Klaus Heiss who did a study for us on the cost-effectiveness of the shuttle.
And, to make a very long story short, the results were that the present configuration that we have for the shuttle today is the one that looked the best.
Present configuration being an orbiter with a tank under it with the hydrogen and oxygen in that tank fed separately into the orbiter and to the main engines which were so expensive that we wanted to recover them.
And boosters being solid rockets attached to the tank so that the total vehicle was a little shorter.
Oh, an important point.
At that time the solids were recoverable.
Their wall thickness was enough that you could use the solid rockets, drop them off by parachute into the ocean, pick them up, bring them back, clean them out and use them again.
And that was going to be a cost saving in the program.
And, by doing all this, we had liftoff thrust augmentation of the engines in the orbiter.
These engines, by the way, were 12,000 pounds per square inch internal pressure engines stage combustion.
The most advanced technology you could imagine.
And they were started a year before the shuttle was started to give them more time to develop.
They almost became the long pole of the tent, but I think maybe when it finally boiled down the thermal protection was the longest pole.
He was down there trying to fix them.
I think he was almost down there gluing them on.
Down at the Cape when we were getting ready to launch, we were still having trouble getting the thermal protection system working right.
Well, the result of all this, and there were a lot of other things that happened at the time, in 1971, I don't remember when, the Supersonic Transport was cancelled.
And that was a big technology blow to this country.
In other words, there was a major program that would have absorbed a lot of the high-tech engineers that were involved in the Apollo program.
And, I think, some of the administration thought the Supersonic Transport is a better place to have our technology capability than would be a shuttle.
But Supersonic Transport was cancelled by Boeing.
And I think that probably helped the atmosphere that was involved.
But the other thing that happened is that Congress and the administration finally got the idea that we really weren't going to build a space station immediately.
That we were just interested in getting the shuttle started.
And so we didn't have this massive budget increase that Tom Paine kept wanting.
And Fletcher kept working on trying to get budgets spread so that it wouldn't be a major peak in budgets close in.
And he did that by starting the main engine early, starting the tanks late, starting with solids late and putting an obvious emphasis on the orbiter itself.
So that spread the budget out and helped a lot in giving the administration the feeling that we weren't going to kill them with budget requirements.
So Nixon started the program January of 1972.
George Low and Jim Fletcher went over and had about a 40 minute talk with President Nixon, and he announced the same day we were going to start building the shuttle.
It was going to be a reusable orbiter, the engines in the orbiter, reusable solid cases, an extendable fuel tank, 40 to 50 flights a year, $10 million to $15 million a flight.
Our internal calculations were more like $10 million but we wanted to have some pad in it.
And $5.2 billion, plus a 20% reserve for the administrator for what we call unk-unks, unknown unknowns, things you get into trouble during a development program where you need some more money to do some more testing.
And Nixon agreed to that.
The Bureau of the Budget was in the meeting with him.
And, as soon as Nixon left office, the Office of Management Budget forgot the 20%.
So then it was now $5.2 billion of 1970 dollars.
To make it worse, the NASA Comptroller pressed, I'm sure by OMB, didn't agree that we would use 1970 as the base.
He took the $5.2 billion in 1972.
We lost two years of inflation.
Well, it may not sound like a lot to you but, boy, it sounded like a lot to the guys working on the program because it was clear that we were going to have a tough time meeting that budget.
Here I am explaining to the press, I think it was about two days after Nixon's announcement, one of the studies was to use the first stage of the Saturn V, the S1C.
This one apparently, I think this is the winged version, because all the engines at their back center gradually all the way back here some place.
And we were using, in this design, using the first stage of Saturn V boosting directly into the tank which was attached to the orbiter.
This one was parallel.
I guess that was liquids.
They look like they have bigger diameter.
And I didn't talk about that, but a lot of people were pushing a pressure-fed liquid engine so that you'd be sure you had the capability to cut them off.
And the idea was that because they were pressure-fed that the thickness of the walls was enough that they, too, could be recovered in the ocean and brought back.
And the final decision by the people that were in the propulsion business in NASA was that the technology looked tough.
It was new.
We didn't have a background of pressure-fed boosters.
And the solids, as we will get to later, looked like they were a better deal.
So the design issues, as I saw them as the head of Manned Space Flight, were that the delta wing was required for crossrange.
External tanks were much lighter, the system got to be about half the weight because of all the reduction in external configuration when you took all the fuel out and put it separately in the tank.
Thermal insulation, we bought off on the ceramic tile, the carbon-carbon and fiber blankets, the same as we have today, solid or liquid boosters.
The solids looked more reliable at that time.
There had been a history of solids on many of the large military boosters, and they looked better.
And, at that time, I thought we were going to have a way to terminate the thrust of the solids.
Engine location and type started on the ground for safer, better performance and the stage combustion for better performance.
We had, under our study, retractable turbojets.
Once you got into the atmosphere, you would pop these turbojets out and flew home.
And we decided we couldn't handle it.
Thank God we had had all this lifting body experience where the guys that landed these very low elevatory devices.
Actually, the orbiter had a little better elevatory than some of the HL-10s and X-24s, so we dropped the turbojets out of the system.
Series versus parallel boosters, series was heavier and had less performance with a lot more bending loads in the system.
When we go up, we go max Q.
And with crosswinds we get big loads on that wing.
And so this turned out to be a heavier way to do it.
Well, a little more on solids versus liquids.
I always like to tell this story about solids could be shipped by rail.
I can say it another way.
The diameter of the solids was set by rail shipment.
And there is a story which I am sure some of you have heard that the rails of the American rails were set first by the British who brought the British rail system to the United States.
The British rail system was set by the width of the wheels on the carts that they used to have.
And the cart's width was set by the Roman chariots that used to be on the roads because they made grooves in the tiles.
So that set the diameter of the shuttle.
And the Roman chariot's wheel width was set by two horses in front of them.
So there are some who say that the diameter of the shuttle rocket engines was designed by two horses' asses.
Those were the guys that wanted to use liquid.
They can be shipped by rail.
They had a better reliability record at the time.
Solids could be recovered.
Industry studied pressure fed to recover them, too, but we didn't buy that.
The designers thought they could turn off the solids but later found out they couldn't turn them off uniformly and that the thrust variance that would be involved between the two would be totally beyond the capability of the vehicle to sustain it.
So we dropped it.
Thermal insulation, we talked about it.
They were all new developments that had been experimentally tested, they looked like they were going to work, but we had a lot of work to do.
And the ceramic tiles really turned out to be one of the toughest new technologies that we got into.
High-pressure stage combustion engine, we knew that was a big new development.
And so, as I said, that was started early.
And design crew escape, well, the idea was we were going to be able to terminate the thrust on the rocket engines.
And we looked at these rockets to pull away the cabin, we looked at all that stuff, and none of them had a broad application.
You had the question of safety.
If you took it off at the launch site, if you took the whole front end off the vehicle at the launch site, it had big questions of the reliability of the system.
We went through a lot of studies to try to find a way to capture the crew in case of a problem and never found a system that fit into the program.
So we ended up with crew escape only with a complete structure.
And that, of course, was the problem in Challenger.
We ended up wrecking the structure to where we did not have a recovery capability, but we put in a system where if the vehicle were complete and structurally sound and was gliding the guys could get out.
But that was the only escape system that we had.
I wanted to touch operation costs a little bit.
We had built enormous confidence from the Apollo program.
In spite of the Apollo 13 problem, the rest of the vehicles had worked beautifully.
I used to say that every flight always had man in the loop some place during the flight that was important to the success of the program.
Many times it was a minor thing.
Like when Apollo 12 got struck by lightning when it was launched, the guys were able to reconfigure switches to get the power back on, get everything back to normal and had a nice flight to the moon and hit a few golf balls.
Every flight had man involved, but every flight was a tremendous success, except Apollo 13.
And, at the time, we were dealing here in the 1970 time period.
Well, April of 1970 was when we launched Apollo 13.
Anyway, we had tremendous confidence.
And we thought we had tremendous support from the industry and we thought we had tremendous support from the public, but we still were concerned about the operational costs so we hired American Airlines, for one, to work with us on what the costs would be and how would you design the system to give you the least operational costs? The military, because they were committing to put their payloads on the shuttle, had studies done by the Aerospace Corporation about the operation costs.
There was a study done by IDA, Institute of Defense Analysis.
All three of them agreed that we were going to have tremendous reductions in the cost of operations.
They didn't quite come down to the same levels that NASA had estimated but they were close.
It was kind of interesting that we all thought it could be done.
We all thought there could be be enormous reductions in the cost of operations with the shuttle.
We thought we had enough space-based hardware that we could do quick turnarounds and handle it more like an airplane.
But NASA and these groups didn't really properly account for the costs associated with post-flight maintenance, the rocket engine.
When IDA and Aerospace did the studies, we told them the rocket engine was going to be reusable for at least 20 flights.
Well, it turned out it wasn't.
And it was such an enormous new development that in the early flights of the shuttle it took a lot of time and a lot of effort to replace engines and refurbish engines.
Assuring the safety of flight in a hostile environment, and space is hostile, and we are dealing here with what amounts to a short amount of R&D development testing when you get into these flights.
Difficult cutting-edge technologies.
The engine in the thermal program, the tiles worked but they often got chips outs of the tiles so we had to replace tiles between flights.
And this is fail operation, fail operation, fail safe.
The airplanes have fail operation, fail safe.
They took the attitude that if you had three computers that was plenty, and if one went bad during a checkout you launched anyway.
You don't know that but that is what is happening to you on commercial airplanes today.
We went one more.
We went fail operation, fail operation, fail safe.
We have four computers in the shuttle, but we cannot fly without all four in perfect condition.
So those things add cost when you do that.
And then cost tradeoffs between R&D and operations, people have argued with me many times that our decision to put the tank externally was a bad deal.
It turns out that it was certainly a bad deal on Columbia.
The foam on that tank came off and hit the carbon-carbon leading-edge of the wing and broke a hole in it and caused thermal excesses in the re-entry.
So you could argue, yeah, we should have had a two-stage fully recoverable system.
But those were the cost tradeoffs that were involved in getting a system that would be accepted and bought off on by the administration.
I want to talk a little bit about operation costs.
That has been the big miss that we made in this program.
As I said, cost of operations never got down to what it should have been.
Well, it never got down there for a couple of reasons.
We were never able to get up to a flight rate that would favor a reusable vehicle.
I think we got up to 26 flights in one year, but most of them were down around eight or ten.
And so we weren't up far enough to offset the cost of the research and development costs to get the operational costs down low.
But I have an interesting little summary.
It is not an exact thing at all but it gives you a little feeling for what I have seen out in this program.
In 1970, the $10 million flight price was based on the same accounting system that we used for the Apollo.
Now, when you go down to Cape Canaveral we had a lot of other things going on besides Apollo.
And so we had the common support activities like the medical department and the mail system and all that sort of stuff as a common separate accounting.
And all the costs for the Apollo were those that we called hands-on, things associated with buying parts, bringing in spares, putting on spares, checking out the vehicle and launching it.
So we had two different pieces of money involved in the Apollo program, and one of them never even was charged to the Apollo program.
So we used that same system, it seemed logical to go ahead with the same accounting system for the shuttle as we did for the Apollo.
Well, it turned out that these separate items were a pretty big chunk of money.
And I have assumed that it was about $400 million a year.
I am not sure that is right, but I wanted to do it just to give you an idea of what happens with inflation.
Remember we said we would do this job using 1970 dollars and we said that the costs would be $10 million of 1970 dollars? With $400 million in overhead and inflation, according to the Consumer's Price Index, which I looked up on Google, by the way, they have a nice little calculator for inflation, 40 flights a year, no overhead, in other words, like Apollo, a $10 million price in 1970 would be $23 million by first flight and would be $50 million now.
Same 40 flights but including overhead would make the flight cost $20 million in 1970, $45 million in 1981 and $101 million per flight for 40 flights in 2005.
A huge increased price because of the inflation that occurred in the 1980 to 1982 time period.
Eight flights per year, including overhead, runs it up to $60 million in 1970 dollars.
And eight flights per year is sort of what we have been running here recently.
$135 million at time of first flight and $302 million a flight in 2005.
Now, the cost per flight on the shuttle, I don't know.
I know that it is up in that $400 million or $500 million price.
I use this only to give you kind of a rough feeling that, although we missed operational costs badly, we didn't really just be totally out of the ballpark on them.
Shuttle performance is great.
The shuttle has done everything it was designed to do, and probably a few more things we didn't think of at the time.
It has put military devices in orbit, commercial devices in orbit, scientific payloads all to LEO with solids we brought along, and it has taken stuff to GEO, geosynchronous orbits.
It has retrieved and replaced satellites.
It has retrieved satellites and brought them down to the ground and repaired them and brought them back into orbit.
It has repaired satellites in orbit and it has launched elements to the space station.
In the 1980s, the shuttle had only 4% of all the launches in the country but carried 41% of the mass launched.
Shuttle R&D was well within what Nixon and Fletcher agreed to, $5.2 billion plus 20% in 1970 dollars.
And I mean quite a lot of it.
Probably the 20%, only about 5% to 10% of that was actually used.
In that sense, they overran what the OMB said we were to develop it for where they didn't give us the 20% reserve.
We overran it by 5% or 10%.
Missed two key design issues.
Call them system engineering issues.
Cold O rings in the Challenger.
We had O rings in that vehicle which when they were cold they lost their flexibility.
And when they were cold in a design that was opened a little bit when the pressure came on internally, that was a disaster waiting to happen.
So that was a bad design of the way the O rings were designed into the vehicle.
The second one is the foam shedding.
We knew that we were going to have ice and/or foam on that tank, and we really pressed the industry to make sure that that foam was going to stay on.
We had foam enough that we didn't get a lot of icing, but we had foam that had to stay on.
Because we know that as it shed, we didn't think so much of the carbon-carbon as the tiles, these brittle tiles that we had on the bottom of the shuttle.
So foam shedding was known to be a problem all the way through this arm of the development but just has not been able to solved.
And after the Columbia accident, the Martin company, I assume, worked for two years trying to make that foam stick better.
And it did stick better but pieces still came off.
So the fleet has been grounded and they got to get that fixed.
And, of course, we missed the operational cost.
Two-stage reusable vehicle would have missed worse, I am sure of that, because of the size of that first-stage booster and the mach numbers it had to go to.
I guess I have concluded that spacecraft are not like airplanes.
Every flight is a structural dive demonstration.
You know, you develop an airplane and you fly it many times before you fly it to the corner of a VG diagram.
And I can only think of one exception.
A guy named Weese Welch, one of the greatest test pilots North America every had flew the first flight of the F-86 which is the fancy new jet that we brought in just before the Korean War.
And, on his first flight, it flew so well that he took it into a little dive and the mach meter went up to one.
And, actually, the ground data showed that he probably went to 1.04.
Some say they heard a sonic boom.
I am not sure of that.
But that was about a month before the X1 went supersonic.
In those days, test pilots were kind of innovative and they did things that they were told not to do.
And he did it.
But every flight is a structural dive demonstration.
We go right up to max Q every time we fly.
We go through wind shears and take it up to high Gs.
We go to high Gs on the way up, we go to high Gs on the way down, we go max thermal every flight.
So we are dealing with a tough set of activities when we do this.
No reusable space system ever gets the millions of hours of stressed operation that airplanes get.
Once an airplane gets through development, it starts getting millions of hours of test data or information where if you have a problem you fix it.
And you just don't get that in these systems.
The space system has decades of evolutionary model development.
In other words, the airplane business has been so dramatically economical that you could build new airplanes every ten years or so.
And each new airplane took advantage of all the things known from the past airplane and designed into it.
As I said, every reusable system is exposed to enormous environmental variations every time.
Thermal, vibration, pressure, mach number, all these things happen every time.
And so I look at the shuttle as being an amazing piece of machinery which is done extremely well in what I consider a continuing R&D environment.
We just don't have yet an operational system.
So my view of the next program, keep it simple.
It has sort of been a prime view that I have had of design every since I have been in the airplane business.
Don't stretch the technology.
Use really good margins of safety because we are dealing here with, as I said, maximum conditions on every flight.
You better play it safe.
Keep it small.
Carry as few passengers as possible.
Carry people or cargo but not both.
Keep the requirements to a minimum.
Use as many past components and systems as have been proven to be reliable.
Design for operations, very important.
Easy access.
One man can replace a black box.
You don't have to run a big pickup machine to take something out of it.
And keep the design reserved while you are designing it so that when operational issues come up you can design for the operational issue and keep reducing the cost of operations.
I don't know what all that means.
I think it means that if we had it to do over again it would have been great to be able to contain the requirements within NASA, probably build a much smaller system that you could get many more test flights at lower cost, but we didn't have that opportunity, as you now know.
So we have the shuttle disappearing into the distance.
Decision has been made that the shuttle be phased out in 2010.
And it is going to be a tough issue because now the shuttle is down in between flights because we lost foam on the last flight.
They grounded the fleet until we can figure out what to do about that foam problem.
And then Hurricane Katrina knocked off the top of the VAB, which isn't a big deal, but it really messed up some of the tank facilities and tank access.
And people's lives have been affected with losses of homes.
So there is a whole bunch of new issues involved in the shuttle that I read in the paper this morning which may mean another delay in the next launch of the shuttle.
And that means a compression of the time between now and 2010 when they are trying to use the shuttle to meet the commitments that we have with the Europeans and the Japanese about putting pieces of the space station up into space.
An interesting new problem for the shuttle.
OK? [APPLAUSE] HOFFMAN: Let's take a one-minute stretch break.
Stand up if you'd like, turn around in a few circles, and then we will have a half an hour for some questions, answers and general comments.
The external environment, the background, what went into the design of the shuttle.
And I think what Dale alluded to at the end is very much to the point, and we will be talking about this with the people when they talk about the individual systems.
In terms of the actual performance, which we have gotten out of the shuttle, despite the fact that we have had two catastrophic accidents which, by the way, involved not only the design of the shuttle but the way we operated the shuttle.
And that is an important thing that we will spend time talking about.
Had we not made the decision to launch Challenger on that cold day, who knows what would have happened? And, similarly, we accepted the fact that foam was continually falling off of the tank, even though that was incompatible with the design specifications on the thermal insulation for the shuttle.
So we had basically two parts of the shuttle system and we had design incompatibilities, but we chose to keep on flying.
But, as a whole, the shuttle has been remarkably successful from a technical point of view in terms of what we have been able to do in near earth space, has been I think, compared to what you could do working out of an Apollo capsule, was absolutely phenomenal.
And, in fact, I think in terms of near earth operations, the shuttle will be sorely missed when we retire it and there will be a lot of capabilities that we will be giving up.
But, on the other hand, where we really got it wrong, by orders of magnitude, was in the cost and reusability of the shuttle.
Now, perhaps that goes back to the requirements because, again, we were trying to do an awful lot of things for the very first time and, yet, we were being told by the Office of Management and Budget that you said it had to be cost-effective.
I mean, in a sense, NASA was being asked to operate the shuttle almost as a commercial enterprise and to make money on it.
This is like you build a test vehicle for the first time and you are being asked, at the same time, to operate it at a profit.
And, as you know, one of the systems engineering principles is you have this triangle.
I am sure you have all seen this.
Performance, cost, schedule, you have all seen the triangle, right? And you cannot specify all three.
They are not all independent parameters.
If you specify the performance and then you're limiting the cost, you cannot control the schedule.
Anyway, all three of those we, in a sense, got specified when we accepted the requirements to build the shuttle.
And something has to give.
And, in the end, it was the schedule and the cost.
And we will have more to say about this in the next couple of lectures, but now let's take advantage of the last 20 minutes and give you a chance to ask some questions about the content of the lecture.
And Dale can try to answer them.
I will say, by the way, in terms of the schedule of the class, when this was given as an aircraft systems course, there were two lectures of an hour and a half and then there was a laboratory period scheduled on Wednesdays.
And the idea, I think, was that by scheduling a lab everybody would have one period of time at the same time so that it would make it easier for you to work as teams on your project.
Because we have so many people coming from out of town, I thought that it would be better to make sure that they have full time to interact with you.
And so we didn't schedule a laboratory period for this course.
Instead, we have two two-hour lectures.
And I am assuming that all of you, once you form teams, will be able to work out some times when you can get together.
The only other thing I will mention, if you look ahead for Tuesday, September the 20th, that is the first deliverable regarding your term project.
And all we want you to do there is just to think about what subsystem you might be interested in studying and write a paragraph about what you think you might want to do with it.
And what we will do is we will be taking a spiral approach to this project.
So, if you look ahead, you will see there are various times when we ask for preliminary results.
And then we will work with you, give you guidance in how to deepen that so that then you can go back.
And the next time you hand something in it will be at a deeper level until the end when you're finished with the project.
OK, let's move into the question and answer period.
And there has been a lot of material presented.
And this is your chance to ask the guy who was here when it all happened.
Dale, why don't you take center stage now? MAN: Thanks so much for coming.
I was kind of intrigued by your talking about the different phases of development.
You called it phase A, phase B and C/D.
And I was kind of wondering when, in those phases, you kind of developed the high-level requirements, when you developed kind of low-level requirements, how much industry was involved in different levels? What percent was industry engineers and what percent was NASA engineers in those studies? And I was just wondering if you could expand on that.
MYERS: Yeah.
Good question.
The theory is that you do phase A as conceptual activity and, when you have gotten your requirements nailed down, you then do a phase B.
And that's what we thought we had done.
It turned out that military requirements came in after phase B had been started, so we actually had to change the contracts with the industry to take into consideration those military requirements.
And they were a big change to the requirements.
So, in that sense, we had some inefficiency in phase B.
And it was after we began to get the results of phase B that we realized we didn't have a system that was going to meet the requirements.
So, instead of canceling phase B, we finished the phase B because we needed that basic understanding of all of the systems and all of the elements that made up the system.
We finished phase B but we started some additional phase As, conceptual activities to try to find a solution.
And I don't remember how we worked from the recognition of the new configuration back into the phase B guys.
Oh, we had a phase B extension to bring that new configuration.
NASA's decision that we would go to an external tank.
We modified the phase B studies again with an extension that allowed the industry then to catch up with what was going on.
And, by the time we finished that phase B extension, we all the requirements in place, we had all of the design understood well enough to start phase C/D.
I think it is pretty amazing that a device that was going to do what we wanted to do with the shuttle, go into orbit, come back in and land, the configuration really stayed the same from that point on.
It is just amazing that we did that well, I think, in definition so that when we really started the C and D phase, which is the detailed design, things stayed in place.
And that meant all the aerodynamic work that had been done which was, by the way, the most aerodynamic work, most wind tunnel testing ever done on a new system, I think, logically because we were working through the mach number range.
And all of the other elemental testing that had gone on all allowed us to keep the configuration identical from that point.
MAN: I know there has been a lot of talk, but it seems obvious now in hindsight that the capsule, or the orbiter or what have you should be on the top of the launcher to clear it from the debris from the fuel tank or what else.
What I'm wondering is at the time in the early stages, was there ever any talk about safety issues in putting the orbiter so low on the hull on the side? MYERS: Yeah, there was a lot of talk with Martin about foam shedding at that time.
And, during the initial decision process for putting it on the side, we had done studies of stacking it in series.
And it was a weight problem.
It was literally an issue of the structural weight of the orbiter mounted vertically because of the terrific loads that you get separately on that system.
And so we recognized that the side mounted tank was going to be a much more economical system.
So we had to worry about ice and foam.
And so we had a lot of discussion with Martin Company at that time.
I think we did a lot of work down at Marshall, too.
COHEN: That's a very good question.
In fact, I will try to develop some of that thought process as we go along.
The key point to make is the following.
Should we have challenged the requirements? Making the orbiter so big with the payload base so big, it was very difficult to put that on top.
If you made it smaller you could.
The real question, I think, and I was going to ask Dale this question which is a follow-up to yours, should NASA, once OMB and the White House gave a cost constraint and once we had the change in the Air Force requirements, should NASA had said no, we don't want to do it? And that is really a very fundamental issue in terms of understanding your requirements, because the requirements drove the 14-day turnaround time, the fact that you wanted large payloads, you wanted to get to the payloads, put the orbiter where it was.
The fact that you needed a high-performance engine and a lot of payload in orbit said that you needed a liquid oxygen liquid hydrogen engine to get the highest specific impulse to get the engine at highest performance.
All that added together, the thermal protection system was basically a glass house which was incompatible with material coming off the tank.
So there was some, you might say, incompatibilities and requirements.
And the question is should we have challenged those requirements more strongly? That's really the fundamental question.
I don't think we should of.
But let me ask Dale because it would say what you would have done with the orbiter.
MYERS: I did.
I challenged the requirements inside NASA.
I never challenged it with the military, but I challenged it inside NASA with George Low and with Jim Fletcher.
And their conclusion was that we would not have a Manned Space Flight program if we challenged the military requirements.
And then the rest of it followed.
HOFFMAN: But your question is a very, very pertinent question.
MYERS: Yeah, it sure is.
HOFFMAN: It is a very key question in today's environment.
Of course, you are infinitely smarter after it happens, but your point is very well taken.
MAN: Do we have better systems engineering tools now than we did in the `70s? And so, if you used today's tools to design the shuttle then it would be better? MYERS: I think.
Well, of course.
MAN: Would you have avoided cost overrun and so on? MYERS: System engineering is better, yes.
Cost estimation, I'm not so sure.
We had the best guys in the country doing cost estimations on the shuttle, but we missed it probably as much as anything else by just not having those people understand the complexities of operating in space.
And I think a lot more is known generally now about the cost of operating in space.
I think that the next try at a reduction in cost for getting into space will be a much more significant activity, but I consider cost estimation a part of system engineering.
A lot of it is much better, some of it is not, I think.
COHEN: Well, just to follow-up a little bit.
When we designed the orbiter, we didn't have CAD/CAM systems.
If you look in the aft end of the orbiter, it is sort of like the hardest thing you have ever seen because we didn't have a computer-aided design.
If we had had that, we probably would have done a much easier job in the aft end of the orbiter and in the mid fuselage and in the cockpit.
That is systems engineering.
You today have much more valuable tools than we had during the Apollo program and during the Shuttle program, but there still is a lot of education you need in systems engineering.
And I think Dr.
Hoffman explained the famous triangle, cost, schedule and performance.
And that is a continued work in systems engineering.
MYERS: And I always think of systems engineering as the people who work across the system with everybody in a real communication system.
And it is that kind of communication that does good system engineering.
Tools are not.
OK? Anything else? MAN: Could you talk a little bit about the Astronaut Office and what they thought during these conversations? Were they in favor of the recoverable fully piloted booster and what were their input on the risk conversations? MYERS: Yeah.
They were aware of it.
We kept in touch all the way through the development program, including the decisions not to have a launch abort system.
And they all recognized there was risk in the program, no question about it.
Aaron, you were there.
What about it? HOFFMAN: Well, you said it right.
I think that's right.
They were part of the design and development team and the requirements team, so they were very much in favor of it.
Of course the big issue, which we will talk more about, is escape systems.
And we will go into that a little bit.
Why don't we have an escape system? And I'm sure when Chris Kraft comes you can ask him a lot of questions about that.
I'm sure he will have a lot to say about it, but a lot of us will talk about that.
I think the astronauts were very much a part of the design, the development, the requirements in this phase of the program.
So they were very much a part of it.
MYERS: They weren't too much in favor of an automatic landing system.
HOFFMAN: That's right.
MAN: That was my next question.
MAN: [UNINTELLIGIBLE PHRASE] When does it appear clearly that the Space Shuttle was not a low-cost access to space, or was it already too late to change the program or requirements? MYERS: I think the problem was that we never got up to flight rate.
There were payloads waiting for us but we never got to flight rate.
And, if we had gotten to a higher flight rate, operational costs would have been lower.
Not enough lower because, no matter what we would do, we never would have met our original estimates on operational costs.
But, as you saw by that inflation story that I had, costs today would be enormously higher than that $10 million estimate that we had in 1970 just because of inflation.
But we never got flight rate so we didn't ever get to the lower cost.
And, in the early days, I wasn't there, but it appears to me there was a lot of pressure to get that flight rate up so that the cost per flight would come down.
And that pressure got to be instilled into the people at NASA and the industry to where the decision made on that cold day in January, or whatever it was, on the Challenger.
Even though there was evidence that those O links had leaked in previous flights, the decision was made to launch.
Now, that is a management policy issue associated with trying to reduce the cost of flight.
And so that was a bad decision.
Anything else? HOFFMAN: I will say one other thing on cost per flight.
You have to realize when you're dealing with a reusable system it is hard to specify exactly what you even mean by the cost of the flight.
You can take the total amount of money you spend on the shuttle program every year and divide that by the number of flights.
Well, this year we only had one flight which came to a pretty high cost.
And last year the cost was infinite.
On the other hand, you can look at what is the cost of flying six flights a year versus what is the cost of flying seven flights a year.
And that is what you would call in economics the incremental cost of a flight.
Also, you have to realize that in the cost of the flight there are an awful lot of things that are wrapped up.
Not just the cost of the shuttle itself but all of the mission operations, the flight planning that has to be carried out.
There was one flight, a space lab flight I think back in the `80s where they launched the space lab mission, it was supposed to be a two-week mission, but they had fuel cell problem so they had to come back after four days.
And, in order to give the scientists the opportunity to get their flight data, they rescheduled the flight for a few months later.
So they had the same crew, they had the same flight plan so they didn't have all of the expenses, the paperwork expenses, the training, all of the re-planning and the experiments were the same.
It was the least expensive flight that we possibly could have run.
And, at the time, the estimates were that that actually cost NASA probably about $120 million.
That was kind of the barebones estimate of the incremental cost of a shuttle flight.
And then it can go from there all the way up to billions of dollars if you just take one flight a year like we have this year.
COHEN: Well, the other thought, too, I remember going up to see Dale Myers when he was Associate Administrator for Manned Space Flight and I was the Orbiter Project Manager.
As he pointed out, we had four computers.
The original thought is if one computer went out on the ground we would lift off with three computers.
And that's what we talked about.
Well, of course, that never happened.
I mean, not only that, we have five computers now.
We actually have a fifth computer which is a backup computer.
So things change, environments change, and we were going to do very routine payloads.
We were going to take it up, launch a payload and come back down, just very routine payloads.
Almost every payload today is different.
And it does take that large amount of infrastructure to get that.
MYERS: One of the cost elements in our cost-effectiveness study was a reduction in the cost of scientific payloads because we were going to have sort of a boilerplate bus.
A heavy, rugged bus that had power and communications.
And the scientists would bring their experiments to this bus, put it on this standard vehicle, take it into orbit, launch or keep it, depending on what the experiment was, then bring it back.
And we were going to have this standard bus that was going to be one of the big improvements in cost of the science payloads.
So we showed a reduction in the cost of scientific activity in our cost-effectiveness studies.
That never happened.
The science guys never could accept the idea of an independent bus.
HOFFMAN: We could go on talking for a long time, but it is the end of the class.
Let's thank Dale Myers again.
[APPLAUSE] MYERS: Thank you.
I enjoyed it.
HOFFMAN: So send me your bios and have a good weekend and see you next Tuesday.
Free Downloads
Video
- iTunes U (MP4 - 244MB)
- Internet Archive (MP4 - 436MB)
Subtitle
- English - US (SRT)