Flash and JavaScript are required for this feature.
Download the video from iTunes U or the Internet Archive.
Topics: Formulation of finite element matrices
- Summary of principle of virtual work equations in total and updated Lagrangian formulations
- Deformation-independent and deformation-dependent loading
- Materially-nonlinear-only analysis
- Dynamic analysis, implicit and explicit time integrations
- Derivations of finite element matrices for total and updated Lagrangian formulations, materially-nonlinear-only analysis
- Displacement and strain-displacement interpolation matrices
- Stress matrices
- Numerical integration and application of Gauss and Newton-Cotes formulas
- Example analysis: Elasto-plastic beam in bending
- Example analysis: A numerical experiment to test for correct element rigid body behavior
Instructor: Klaus-Jürgen Bathe
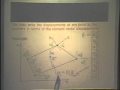
Lecture 6: Formulation of F...
The following content is provided under a Creative Commons license. Your support will help MIT OpenCourseWare continue to offer high quality educational resources for free. To make a donation or view additional materials from hundreds of MIT courses, visit MIT OpenCourseWare at ocw.mit.edu.
PROFESSOR: Ladies and gentlemen, welcome to this lecture on nonlinear finite element analysis of solids and structures. In the previous lectures, we talked about the general incremental continuum mechanics equations that we're using in nonlinear finite element analysis.
In this lecture, I would like, now, to talk about the finite element matrices that we're using, actually, in static and dynamic analysis. You want to talk about these in quite general terms. In the next lecture then, we will talk more about the details of these matrices. You want to formulate these finite element matrices. And we want to talk about the numerical integration that we use to actually evaluate the matrices.
I've prepared some view graphs regarding this material. And I'd like to share the information on these view graphs now with you.
The derivation of the finite element matrices, of course, is based on the continuum mechanics equations that we have developed earlier. And you have seen this equation earlier when we talked about the total Lagrangian formulation, the T.L. formulation. We talked about the terms in this equation. We talked about their meaning, what they stand for. And we have derived certain terms here because they have been obtained by linearization process.
This was the governing equation for the total Lagrangian formulation. The governing continuum mechanics equation for the updated Lagrangian formulation is shown here. Once again, we talked about each of these terms. We talked about what their meaning is. And, of course, we arrived at this equation by linearization process.
For the total Lagrangian and the updated Lagrangian formulation, we recognized because of the linearization process that was involved, we need to iterate to obtain an accurate solution to the actual problem of interest. And here on this view graph, I've summarized the iterative equations that are used in the total Lagrangian formulation.
We, once again, have seen this equation before. We should recognize, now, these terms. The iteration count, of course, being k, as shown here on the left-hand side of the equation. And k minus one on the right-hand side of the equation.
We also recognize this equation here, now. Namely, the equation where we update the displacements from the k minus first iteration to the k iteration. For this iteration, of course, we need initial conditions. And those initial conditions we also talked about earlier.
A similar equation is used in the updated Lagrangian formulation. These are the terms that we talked about earlier. And, of course, once again, we are iterating with iteration count of k on the left-hand side, iteration count of k minus one on the right-hand side of the equation.
The displacements are updated, as shown here in this equation. And for this iteration, of course, we need initial conditions, which are given here. And all of these terms, really, we discussed in some detail in the earlier lectures.
Well, assuming that loading is deformation-independent, we also recognize that this here is the expression for the external virtual work. t plus theta tR, the script R that I talked about earlier already. And these are the terms that we already defined earlier. Particularly the body force term, the surface force term. Notice that, so far, we really talked about static analysis. And I'd like to now, of course, also introduce the term that we use in dynamic analysis.
This, of course, is the inertia term. And in dynamic analysis, this is the term that is really contained in this term here as an effect of fV. Of the volume forces, the forces per unit volume.
Notice that this is really here an integral over the volume at time t plus theta t of the mass density at time t plus theta t times the accelerations at time t plus theta t, the virtual displacements, and, of course, the integrating over the volume at time t plus [? theta, ?] t plus theta t, as I said already.
This is, of course, an "inconvenient" interval. Inconvenient in quotes because we don't know this volume. So we cannot really directly evaluate this integral. Instead we'd rather like to work with the original volume like we do in the total Lagrangian formulation. And transformation of this integral to an integral over the original volume is achieved by this equation here, by this term here.
Notice that, of course, 0 rho times 0 dV for a particular set of mass particles must be equal to t plus theta t rho times t plus theta tdV. And this is the reason why we can directly write down this equation here.
However, considering this transformation for finite element analysis, it is important to realize that we assume here that the possibilities of the motion, of the material particles as contained in the finite element interpolations are the same in this volume as in that volume. This fortunately, is true in isoparametric finite element analysis. And therefore, this transformation from the volume t plus theta t to the volume V 0 is a very convenient transformation to perform for the evaluation of this term. We use that abundantly in isoparametric finite element analysis.
If the external loads are deformation-dependent, then we have to recognize that these forces here are deformation-dependent, and therefore, we have to evaluate them in the iteration. And that is being shown here in this equation. That we are always evaluating this term new, depending on the iteration k minus 1, we integrate this product here over the volume at time t plus theta t in iteration k minus 1.
Similarly, we update, also, the surface forces. Since the surface area changes of the body during the last information process, we evaluate this part here as shown here. Of course, there is an approximation involved. But if we keep on it iterating t plus theta tVk minus one, we'll take on the volume t plus theta tV. And of course then, we really include here the term that we want to include, namely that one in the analysis.
Similarly here. The surface area, in iteration k minus 1, as k goes larger and larger. If we converge, we'll actually be equal to that surface area, meaning that this expression is equal to that expression, which of course we want to include. It's this expression that we want to include in the force vector.
We, in one of the very early lectures, talked about the materially-nonlinear-only analysis. And the equation that is used, the continuum mechanics equation that is used in the materially-nonlinear-only analysis is given here. Notice, here we have a stress strain law tensor, an incremental strain tensor, the virtual strain.
The incremental strain tensor is the real strain tensor here. All the components of that tensor have a superscript k. The external virtual work. And here, we have the stress tensor, components of the stress tensor. At time t plus theta t in iteration k minus 1. And the virtual strains again.
Notice here now, we do not have anymore subscripts, 0 or t, on these components because in materially-nonlinear-only analysis, we assume that the deformations are very small. The displacements are infinitesimal. And the stress, the second Piola-Kirchhoff stress, which we defined in an earlier lecture is actually equal to the Cauchy stress under those conditions and is equal to the physical stress that we are talking about here in the materially-nonlinear-only analysis.
In other words, both those stress measures are equal to the physical stress that appears here, which is, of course, the force per unit area. The one that we are so familiar with in infinitesimal displacement analysis.
Let us look further at dynamic analysis. Dynamic analysis is generally performed in nonlinear analysis, using an implicit time integration scheme or an explicit time integration scheme. And in a later lecture, we will discuss such time integration schemes.
In implicit time integration, we look at the equilibrium equation at time t plus theta t to obtain the solution at time t plus theta t. And this means that we will have to evaluate this left-hand side written here as given on the right-hand side.
This part here, this external virtual work, comes from the external loads that are not the mass of the inertia forces. The inertia forces are taken care of via this part, via this integral here, which I discussed already a bit earlier.
In explicit time integration, we are evaluating or we're looking at the equilibrium equation at time t to obtain the solution at time t plus theta t. Quite different from implicit time integration. And the governing equations are in the total Lagrangian formulation right here, in the U.L., the updated Lagrangian formulation given here, and in the materially-nonlinear-only analysis as given here.
Notice, of course, that R will involve the inertia forces evaluated at time t now. And that will, of course, enable us to march forward with a solution as we will discuss later on in another lecture.
The finite element equations corresponding to these continuum mechanics equations look as follows. In materially-nonlinear-only analysis, let's look first at static analysis. We have this basic equation.
Notice a tension stiffness matrix that does not carry any subscript 0 or t because we are talking about the original volume, the displacements being infinitesimally small, the physical stress, no Cauchy stress really, no second Piola-Kirchhoff stress needs to be introduced. We just talk about the physical stress that we are so familiar with in infinitesimal displacement analysis. And that, of course, goes into the evaluation of the K matrix because the material law will appear in here, the incremental displacement vector, and on the right-hand side, the load vector, and the nodal point forces that are equivalent in the sense of the principle of virtual work to the current element stresses. By current, I mean F time t plus theta t at the end of iteration i minus 1.
This equation, of course, looks very much alike of what we have seen in the updated Lagrangian formulation and in the total Lagrangian formulation. In dynamic analysis using implicit time integration, this will be the governing equation. Now, the mass matrix, the acceleration vector with an iteration [? count of ?] i because we are marching forward to a situation, to a configuration which is still unknown, a tangent stiffness matrix, the same tangent stiffness matrix that we see here, by the way, the incremental displacement vector, and on the right-hand side, the same quantities that we have here.
In dynamic analysis using explicit time integration, we have the mass matrix, the same mass matrix, generally, that we have here. Although in implicit time integration, we will sometimes use a lump mass matrix, sometimes a banded mass matrix, a consistent mass matrix. With an explicit time integration, we generally use only the lump mass matrix.
But otherwise, the same kind of matrix here. The acceleration vector. The force vector or the nodal point forces, corresponding to time t that are externally applied to the structure. And the tF vector, which is the force vector corresponding to the stresses in the elements at time t.
Notice, we are looking here at equilibrium at time t to obtain the solution at time t plus theta t. We are looking here at equilibrium, or I should say, we're iterating for equilibrium at time t plus theta t. And thus, we will obtain the solution for time t plus theta t.
In the total Lagrangian formulation, we have very similar equations. In static analysis, a tangent stiffness matrix, and otherwise, the same kind of vectors that I talked about earlier already. Notice now, of course, we have the subscript 0. Notice also that the total tangent stiffness matrix is made up of a part that we might call a linear strain stiffness matrix and a part that we may call nonlinear strain stiffness matrix. This is also called the geometric stiffness matrix.
We will talk about how we construct these matrices just now. In dynamic analysis, we proceed as in the material-nonlinear-only formulation, of course. And in all the other formulations, if we use implicit time integration, we apply the equilibrium equation. We look for the equilibrium at time t plus theta t, as expressed here. And we have vectors, matrices very similar to what we have in the material-nonlinear-only formulation except that once again, of course, we have now introduced here the geometric stiffening affect, the nonlinear strain stiffness matrix.
In dynamic analysis using explicit time integration, we don't use any K matrix. We will discuss that also much more later on. And this is the governing equation. Very much the same as in the material-nonlinear-only formulation.
Finally, in the updated Lagrangian formulation, we also obtain similar equations and static analysis. These are the equations that we want to solve. Notice also, the nonlinear strain to them there or the nonlinear strain stiffness matrix.
Otherwise, the matrices and vectors are very much alike what we have seen before. Dynamic analysis implicit time integration and in dynamic analysis using explicit time integration. Notice that in each of these, we are always cutting out the subscript t or t plus theta t the way I have been talking about earlier already.
We have seen this equation, of course, before in our earlier lectures. What we now do is we introduce the mass terms. And we are talking about implicit time integration and explicit time integration. We should note that these equations are valid for single finite element as well as for an assemblage of finite elements.
If we have a large number of elements, then, of course, we would assemble these as we do it in linear elastic analysis using the direct stiffness method. Considering an assemblage of elements, we will see that different formulations may be used in different regions of the structure. In other words, schematically here we may have some elements that are governed by the T.L., the total Lagrangian formulation, some others by the updated Lagrangian formulation, and some others by the material-nonlinear-only formulation.
Notice that compatibility between these elements is, of course, perfectly preserved if these are compatible elements as shown here. Then, there is nothing wrong with using the U.L. formulation for certain elements that are bordering elements with another formulation such as this.
It is not true, for example, that due to the fact that you're using here different kinds of formulations, you are getting an incompatibility introduced here. I've heard that sometimes. That is certainly not my understanding of the subject matter. It does not matter whether you have the same kind of formulations or two different kind of formulations. That will not effect the compatibility between two elements.
Let us now concentrate on the derivation or on the formulation of a single element matrix. To obtain a single element matrices, we have to introduce, of course, an interpolation matrix. And this matrix interpolates the internal element displacements via the nodal point displacements.
Here, I'm showing a full node element with these nodal point displacements. Notice these are measured in the Cartesian coordinate directions. Notice however, that these nodal point displacements are measured into a skewed direction, an a b coordinate system.
There's nothing wrong with introducing different systems because this is Q system at the different nodal points. The nodal point vector, the vector of nodal point degrees of freedom is listed here. Notice that vector carries a hat to denote the fact that it contains this great nodal point displacements.
Notice also, that the subscripts 1, 2 refer to the Cartesian coordinate directions for the superscripts referred to the nodal point. Here 1, 2 again. 3 denoting the nodal point.
Notice up here, a b, of course refer to the skewed directions. And the 1 refers to the nodal point 1. We want to interpolate the internal displacements in terms of the nodal point displacements.
And that is being achieved by this relationship here. U, the internal particle displacements are given via H, the displacement interpolation matrix times U hat. U hat being this vector, the one we just discussed. U being a vector of these two displacements. Now, notice that these two displacements, of course, depend on which particle you are looking at.
Here, a particular particle. This would be the displacement you want. That's the displacement U2. And these displacements vary over the element, which would be expressed by this H matrix. These are the nodal point displacements.
These are the varying, continuously varying displacements of the particles within the element. We will, of course, use this kind of relationship now quite extensively. We have, of course, also already encountered this relationship in linear elastic analysis.
Let us now see how we are formulating the different matrices. For all analysis types, in which we want to include inertia forces, we evaluate this integral as shown here. Notice the displacements and accelerations are interpolated via this relationship here.
For the accelerations, of course, we would have dots here, dots there denoting second time derivatives. And we would have t plus theta t as a superscript on each of these variables. Notice that we also use this interpolation here for the virtual displacements. And the result is given right here just like in linear elastic analysis.
The right inside load vector as evaluated is shown here. Once again, we introduce interpolation for U or for the virtual displacements and the virtual surface displacements. This interpolation here gives us this H matrix, H transpose matrix. This here interpolated gives us the HST matrix.
Notice that HS is the interpolation matrix for the surface displacements as a function of-- or rather it gives the surface displacements I should say as a function of the nodal point displacements. So HS is really evaluated by using H, the H matrix I just talked about, and evaluating that H matrix on the surface of the element. That is how you get HS.
And all of this expression together gives us the load vector. As a matter of fact it is really the same process followed that we are using in linear infinitesimally displacement analysis. In material-nonlinear-only analysis, considering an incremental displacement UI, we evaluate this integral here as shown here. Notice here the virtual displacements that are coming in because we have the virtual strains there.
Notice here the real displacements, which are coming in from these real strains. Of course, these are strain increments and, correspondingly, displacement increments. Nodal point displacement increments always. These B matrices, BL matrices, are obtained by evaluating the strains from the nodal point displacements.
And, of course, the interpolation that is used for the element goes in here. The B matrix, of course, contains derivatives of the elements of the H matrix. A vector containing components of eIj is this one here.
For example, in two dimensional plane stress analysis, the entries in this vector are listed right here. Notice that there is a 2 here because e12 is equal to e21. And the sum of these two, of course, gives us a total sheer strain. And therefore, we simply put a 2 times e12 here.
This evaluation is performed much in the same way as in linear infinitesimal displacement analysis. Except that we have to remember this stress tensor, this stress strain tensor, this considerative tensor varies in the incremental solution because we have materially nonlinear conditions. So the K matrix here will change. And that is indicated, of course, by the t up there.
Notice the B matrix, in this incremental analysis, using the material-nonlinear-only formulations is constant. For the material-nonlinear-only formulation, we also want to evaluate the F vector. And that F vector is a result of this integral here.
We take this integral, interpolate the virtual strains. And that is this part here, in terms of the virtual nodal point displacements. And we assemble in this vector here capital sigma at time t, the stresses t sigma ij. We assemble those in this vector.
Notice, in two dimensions analysis, this vector is given down here as these components. By the way, no two here. You should think about that. There should be no two here.
Total Lagrangian formulation. We have similarly an integral as in the material-nonlinear-only formulation. We interpolate, once again, these real incremental strains, the virtual strains. And the result is directly given here. With the B matrix, now, defined via this equation down here. And, of course, this vector here contains the components of the incremental strain tensor.
However, in the total Lagrangian formulation, we know also have an additional integral. And that integral is coming in because of the geometric stiffening effect of the nonlinear strain term effect. Here we have the integral. And the discretization is given on the right-hand side here.
Notice this is a BNL matrix, nonlinear strain matrix, we call it. This here is a matrix of the second Piola-Kirchhoff stresses at time t. And here we have, again, the BNL matrix. This product together gives us the KNL matrix.
One might ask how do you get these quantities? Well, actually we construct this S matrix and the BNL matrix such that when you take the product of this whole right-hand side, you get that. So these matrices are really constructed such as to obtain what we need to get. And that is this part here. I will show you later on specific examples in another lecture.
Here we have the S matrix containing components as I've mentioned. And this matrix here times this vector contains the components of this displacement derivative.
The right-hand side, of course, for the total Lagrangian formulation has the evaluation of the F vector. And that one is obtained from this integral. Notice we go over. We evaluate this integral by this relationship here. The linear strain displacement matrix goes in here. And a vector of the second Piola-Kirchhoff stresses goes in here. Once again, this vector is constructed in such a way that this right-hand side here is equal to that integral.
In the updated Lagrangian formulation, we proceed much in the same way. Considering incremental displacement UI, we have this integral to evaluate. We interpolate the strains via the strain-displacement [? interpolation ?] matrix, and the result is this here. This is here the linear strain stiffness matrix. Here we have a relation very much alike of what we have in the total Lagrangian formulation for the incremental strains.
The nonlinear strain stiffness matrix in the updated Lagrangian formulation is also very much evaluated like in the total Lagrangian formulation. It is this integral that we now have to capture. And we do so by constructing a BNL matrix, a tall matrix, such that this total product here is equal to this integral. And what's underlined here in blue is the matrix that we're looking for.
We should, of course, also evaluate in the updated Lagrangian formulation the F vector. And that F vector, which appears on the right-hand side of the equation in the updated Lagrangian formulation, is evaluated by calculating this integral. Notice that this is obtained by this right-hand side. The BL, of course, is the linear strain displacement matrix. And here we have a vector, tall hat, which contains the stresses, Cauchy the stresses at time t. It's constructed such that this integral here, with this part in front of it, gives us exactly that integral. And what is underlined here in blue is the actual F vector that we're looking for.
So what we have seen then, is that the finite element matrices for the material-nonlinear-only, the total Lagrangian, and the updated Lagrangian formulation are formulated by looking at the individual volume integrals in these continuum mechanics formulations. And by interpolating the displacements and strains much in the same way as we are used to in linear analysis.
Once we have formulated these matrices, we, of course, have to evaluate them. And that is done using numerical integration, once again, just very similar to what we're doing in linear analysis. We're using, primarily, Gauss integration or Newton-Cotes integration. Schematically, in two-dimensional analysis, the K matrix would be evaluated as shown here.
Notice that in isoparametric finite element analysis, we are integrating from minus 1 to plus 1 over the domain. Two-dimensional analysis, of course, two integrations involved. That we have a B matrix transposed, C matrix, B here, a determinant of a Jacobian matrix, which comes in because we are transforming from the x1, x2 space to the RS space. And we call that the G matrix's total product. And the numerical integrations then really involves nothing else but summing a product of alpha ij, Gij over all numerical integration points. Notice the ij here now refers to the ij's integration point.
This is what we are doing also in linear analysis and in nonlinear analysis as well. Similarly, we would evaluate the F vector, which, of course, we have in the material-nonlinear-only, total Lagrangian, or updated Lagrangian formulation as shown here. Notice, once again, integration from minus 1 to plus 1. And this part here is what we might call G again. F then, is obtained as shown here.
Of course these are the integration point weights that are given to us, which we simply use in the finite element solution. The mass matrix is evaluated as shown here. Mass density goes in there. H transpose H. H, of course, being the displacement interpolation matrix. And this is our G here. With that G, we should put a bar under that G here because it's a matrix. You put it in. And if we use that G here in this formula, we get the M matrix.
So the numerical integration is really performed much in the way as we're doing it in linear analysis. Frequently, we use Gauss integration, as I mentioned earlier. And, as a typical example, 3x3 into Gauss integration is schematically shown here. Here is our element. Here is the R coordinate axes. Here is the s coordinate axes.
This would be the integration point stations that we are using for 3x3 integration. The r and s values are given as shown here. Same r and s values as in linear analysis. And we notice that these integration point stations are all within the element. That is, of course, one feature off the Gauss integration.
As I mentioned earlier they use also Newton-Cotes integration, for example for the integration through the shell's thickness. Here is the r direction, which is a coordinate axis in the mid-surface of the shell. And s goes through the thickness.
Notice here we have five point Newton-Cotes integration. And that some integration points, as a matter of fact two here, are actually on the surface of the element. Because we are including the surface of the element, we use Newton-Cotes integration quite frequently in nonlinear analysis. The reason being that if we do an elasto-plastic analysis, we find that the larger stresses, of course, are generally generated on the surfaces of the element.
And these are then also the areas where plasticity sets in earliest, which means that we want to pick up this elasto-plastic response as quickly as possible. And integration point stations on the surface of the element can be of benefit.
If you compare Gauss with Newton-Cotes integration, we recognize that with n Gauss points, we integrate a polynomial of order 2n minus 1 exactly, meaning, for example, with two Gauss points, you integrate a cubic exactly and everything below it, of course. Whereas with n Newton-Cotes points, we integrate only a polynomial of n minus 1 exactly. So we need really many more Newton-Cotes integration points to pick up the same accuracy in the integration as you do with the Gauss point integration.
For this reason, we use, primarily really, the Gauss integration, particularly in the analysis of solids. Maybe a big, chunky bodies where there is no need, really, to pick up the plastic response say on the surface directly of the solid.
Newton-Cotes integration involves points on the boundaries. I mentioned that already. And therefore, this integration scheme is effective for structural elements for the reasons that I just gave.
In principle, the integration schemes I employed as in linear analysis. The integration order must be high enough not to have any spurious energy modes in the elements. We will get back to that in later lectures, particularly when we talk about structural elements, beam elements, and shell elements. This is a very important point.
The appropriate integration order in nonlinear analysis can sometimes be higher than in linear analysis, for example, to model the plasticity accurately, once again, in a shell solution or such type of analysis. On the other hand, a too high integration order is also not of value because remember, that the maximum displacement variation, therefore, the maximum strain variation you can pick up, is of course, given by the interpolation you're using.
So it doesn't make much sense to go up in very high integration order in order to try to pick up a high variation in strains, plastic strains, and the corresponding stresses, of course. It doesn't make sense to do that when you are limited by the actual strain variation anyway due to the interpolations on the displacements that you're using.
Let me show you an example here that demonstrates some of the points that I'm trying to make. Here we have an eight node element that models the response of a cantilever and the bending moment. We measure the rotation phi here. We have here the material data. Notice we are talking about an elasto-plastic material with yield stress. And we apply a bending moment as shown here.
In linear elastic analysis, you would get the exact response to this problem using one eight node element. You might have tried it already. You may know that. The reason, of course, being that this element contains a parabolic displacement interpolation, which is the analytical solution to this problem. And therefore, you get the exact solution.
In elasto-plastic analysis, however, the solution depends on the integration order we are using. And this is demonstrated on this view graph. Here we show on the vertical axis, the moment normalized to the moment at first yield. And on the horizontal axis, the rotation of the beam normalized to the rotation at first yield, respectively.
Now, notice that the linear elastic response, of course, would be simply this line here going up vertically. In elasto-plastic analysis, however, the element starts yielding. And the yield is picked up, depending on the integration order you're using.
With 2 by 2 integration, we get this solution here. And this would be the limit load. With 3 by 3 integration, we get this solution for the limit load. And with 4 by 4 integration, we get this solution as a limit load.
So this solution very much depends on the integration order that you're using. And it shows here that we need enough integration point stations through the thickness of the beam in order to approximate, appropriately, the limit load that we want to calculate.
Let me show you another problem. And this is an interesting problem in which we want to design a numerical experiment to test whether an element can undergo properly large, rigid body motions. Here we consider a single two-dimensional four node element. It could be plain stress or plain strain. And we want to test by a numerical experiment that you can perform on a computer program, whether this element can actually perform large, rigid body motions, of course, properly. And by properly, I mean there should be no stresses generated in the element when it is subjected to these rigid body motions.
Well, there are for this element three rigid body motions of interest. Two translations and one rotation. It's a two-dimensional element, so these two translations, of course, refer to the horizontal translation and the vertical translation. The rotation, of course, refers to the rotation in the two-dimensional plane.
To test whether the element can undergo properly the horizontal rigid body motion, we designed this numerical experiment. We put here to truss elements. We call them M.N.O. trusses because they do not include then any geometric nonlinearalities. They are really just springs. And we put this element on a roller here. Keep it otherwise free. And we put onto this degree of freedom a load, R. And on that degree of freedom a load, R, as well.
The load is very large. So the element should move over stress free by a very large amount. This is one rigid body movement that the fall out element must, of course, be able to undergo. And this test is passed for the T.L., U.L., and the M.N.O, or linear analysis, of course.
Similarly, we could perform this test for the vertical direction. And we would find that, once again, the T.L., U.L. formulation, and M.N.O. formulation will pass a test for the vertical direction as well.
The interesting test is the one for the rotation. Here we have our fall out element supported at the left-hand side by a pin, and on the right-hand side by an M.N.O. truss. Once again, a truss element that does not model any geometric nonlinearalities. We are applying to this node here a force, R, that would, of course, make this element here go through the rotation.
Since the force should be taken in the spring, the element should rotate stress free. Note that because this spring is and M.N.O. spring, the force acting onto this node here must always work vertically only. After the load is applied, the element, originally here, must have rotated by a very large amount. The area must have not changed. In other words, the element size must remain constant. And the element must be stress free.
This test is passed by the by the U.L., and the T.L., the total Lagrangian formulations, by the updated Lagrangian, and the total Lagrangian formations properly. But if you were to use the material-nonlinear-only formulation, you would see that this element does not remain or keep its original size. The reason being that this node here will move up on this side here because of the M.N.O. truss there. We move up here. And all of the element remain stress free, the element actually grows in size.
It's an interesting test that you can actually perform on a computer program. Once again, the total Lagrangian and the updated Lagrangian formulations, which, of course, are designed to more large quotations and large strains pass this test properly, whereas the M.N.O. Formulation, which is not designed to model large quotations, would not pass this test property.
Well, in this lecture, I've been trying to give you an overview of the general element matrices that we need in the U.L., T.L., and M.N.O. formulations. In the next lectures, we will derive these element matrices in detail for different types of elements. Thank you very much for your attention.
Free Downloads
Video
- iTunes U (MP4 - 97MB)
- Internet Archive (MP4 - 97MB)
Subtitle
- English - US (SRT)