Flash and JavaScript are required for this feature.
Download the video from iTunes U or the Internet Archive.
Topics: A demonstrative computer session using ADINA - nonlinear analysis
- Use of ADINA for elastic-plastic analysis of a plate with a hole
- Computer laboratory demonstration - Part II
- Selection of solution parameters and input data preparation
- Study of the effect of using different kinematic assumptions (small or large strains) in the finite element solution
- Effect of a shaft in the plate hole, assuming frictionless contact
- Effect of expanding shaft
- Study and evaluation of solution results
Instructor: Klaus-Jürgen Bathe
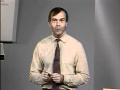
Lecture 22: Demonstration U...
Related Resources
Study Guide (PDF)
References
Bathe, K. J. “Finite Elements in CAD and ADINA.” Nuclear Engineering and Design 98 (December 1986): 57-67.
User Manuals, Verification Manual, and Theory and Modeling Guide for ADINA, see www.adina.com
Bathe, K. J., and A. Chaudhary. “A Solution Method for Planar and Axisymmetric Contact Problems.” International Journal for Numerical Methods in Engineering 21 (January 1985): 65-88.
The following content is provided under a Creative Commons license. Your support will help MIT OpenCourseWare continue to offer high quality educational resources for free. To make a donation or view additional materials from hundreds of MIT courses, visit MIT OpenCourseWare at ocw.mit.edu.
PROFESSOR: Ladies and gentlemen, welcome to this lecture on nonlinear finite element analysis of solids and structures. In this lecture, I would like to continue to consider the plate with a hole that we already considered in the previous lecture. But I now would like to turn our attention to a nonlinear solution.
As we mentioned in previous lectures, a nonlinear analysis should only be performed only once a linear solution has been obtained. The linear solution checks the finite element model and yields valuable insight into what nonlinearities are important. And once again, we considered the linear solution of this plate in the previous lecture. We now want to go on with the nonlinear solution.
Here we have the plate with the hole once again. It's a square plate subjected to the loading shown. Here is the whole. These were the material data that we used in the linear analysis. The thickness of the plate is given here. We consider only one quarter of the plate because of symmetry conditions, we can considering that one quarter, analyze the whole plate, as we have discussed in the previous lecture.
In the previous lecture, we also showed how we use ADINA-IN to generate the data for this mesh. And this input data then is used in ADINA to actually perform the analysis. We did the analysis for linear conditions in the previous lecture.
Some important considerations for the nonlinear analysis are now what material model to select, what displacement strain assumptions to make, what sequence of load application to choose, and what nonlinear equation solution strategy and convergence criteria to select. We will address these issues in this lecture.
We use, once again, the ADINA system. Now, of course, for the elasto-plastic static response. We will also investigate the effect on the response when a shaft is placed into the plate hole.
Some important observations regarding the nonlinear analysis are given on this viewgraph. First of all, we notice that the recommendations that we discussed regarding the linear analysis that we discussed in the previous lecture are also very valid here of course. But for the nonlinear analysis, we need also to consider and be careful with the sequence and incremental magnitudes of load application and the choice of convergence tolerances. We ill address, of course, these issues just now.
The first analysis that I'd like to discuss with you is a limit load calculation of the plate. Here we show the plate and the load, p, will increase continuously up to a maximum value and then decrease to 0. The plate is modelled as an elasto-plastic material. And the material assumption is summarized on this viewgraph here.
Here are the material properties. We assume basically it is a steel. Notice the stress strain law is shown here. We assume isotropic hardening in the analysis. We discussed what this means in an earlier lecture.
The initial Young's modulus is the one that we use for the linear analysis. Nu is equal to 0.3. And the strain hardening modulus is given here.
This idealization is probably only applicable to small strain conditions, strains that are smaller than 2% roughly. The maximum that you would want to allow is probably 4%. And we will actually perform the analysis first using a materially nonlinear only formulation. This means, as we discussed in the early lectures, that we neglect all kinematic nonlinearities, that we only include the material nonlinearities in the analysis, these material nonlinearities.
Later on, we however want to also perform in this lecture an analysis that includes the displacement large quotations and in fact even large strain conditions. And we will study those analysis results in comparison to the material nonlinear only analysis results.
The load history used for the analysis is shown on this viewgraph. You can see that we are increasingly linearly the load up to a maximum value of 650 MPa, megapascals, and then suddenly decrease the load to 0. Notice we are using altogether 14 steps, 13 to increase the load and just one step to decrease the load. Of course, we are having here a time axis. But the load step or time step that we used was delta t equal to 1.
Well we performed this analysis a few weeks ago in my laboratory at MIT. And we brought in a video crew to video record our actions. I'd like to now share with you what we have recorded and also narrate to you what actually is happening in the computer run as we prepare the computer run, as we run it, and also interprets the resides.
Our first step is to modify the input data that we prepared in the previous lecture for the linear analysis of the plate. We now have to, of course, modify this input data. First of all, to introduce the load curve, this load history curve that we just discussed. And then we also have to modify the material data to correspond to the elasto-plastic material data that we now want to associate with a plate. So let us look now at the video record of what we did some weeks ago in my laboratory at MIT regarding the change of these input data.
Here we see once more the mesh that we're using to analyze the plate. And now we prepare input data for ADINA-IN. Here we input the time function that we employ. You recognize the function points for time 0, 13, and 14 with the values 0, 6.5, 0.
We also input that 14 steps are used in the analysis, that time step delta t is 1. Next we input the material definition. And note that there is a typographical error. We typed plestic instead of plastic. We try to do the typing fast and did not notice the error. Notice the Young's module E, Poisson's ratio nu, the strain hardening modulus ET, and the yield stress [? sigma ?] yield are defined.
Because of the typographical error, the program prints out an error message, namely the plestic material is not found in the library. Here we see the library of material models available in ADINA. The library consists of the material models elastic, orthotropic, thermo-elastic, and so on and so on. We know retype the material data definition.
We also do not want to use equilibrium iterations. The default in ADINA is to use equilibrium iterations. Actually, the BFGS method we discussed earlier because large errors of solution can accumulate when iterations are not used. We discussed all of this earlier.
Let's see what happens when we do not iterate in the solution of this problem, just as a point of study. We now finally by the command ADINA generate the ADINA data input. Note that in this input preparation we only change the data from the linear analysis data used in the previous lecture to the data for the nonlinear analysis we want to perform now.
Having set up the proper input data for ADINA-IN and having used ADINA-IN to generate the input data for ADINA, we can now execute that input data with ADINA obtain our first analysis results. We evaluate these analysis results by plotting the force applied here as a function of the displacements corresponding to this motion as well. And we will see that the force displacement curve looks rather unphysical. In other words, the results don't make much physical sense.
So we search for an explanation. Why is that so? And we will find that the reason is that we did not use equilibrium iterations in the analysis. In fact, if you go back, you will see that we deliberately did not want to use equilibrium iterations in this first analysis, although in ADINA the default is to use equipment directions.
But I wanted to once show you what kind of results you must expect if you don't use equilibrium iterations. So we realized that we should really use equilibrium iterations and that we will, of course, have to change our input a little bit through ADINA-IN in order to perform equilibrium iterations.
The load history that we will still be using is the same. Here it is shown once again. But now we will use the default method of equilibrium iterations, the BFGS method. And this one will be applied, this method of equilibrium iteration will be used for each load step. Once again, 13 load steps up and one load step down.
The convergence criteria that we using in the analysis are show here, the convergence criteria on energy. And we talked about this one quite extensively in a previous lecture. And the convergence criteria on the force, again, I'd like to refer you to our previous lecture.
When we apply equilibrium iterations in each step, we will see that our results look good. They make physical sense. In fact, they look quite appealing. So let us look now at these solution results. Let us go, in other words, to what has happened in the laboratory the way we have been video recording it earlier.
Here we see the solution results, the load applied as a function of the displacement, the extension of the quarter plate. On the horizontal axis, we measure the displacement. On the vertical axis, we measures of value of the load, actually the pressure applied.
So far the curve looks OK. But we show here only the responsible for the first 13 steps for which the load has increased monotonically. here we see now the load displacement response for all 14 steps. Notice that the scale on the horizontal axis measuring displacement is different from what we used before.
Note that the 13 first steps bring us to the maximum load and maximum positive displacement and that the predicted unloading response in step 14 is quite unrealistic. We obtain a large negative displacement. As we will see, this is due to not having used equilibrium iterations.
Next, we look at the mesh and study the plastic zones as they develop with increasing load. A time code is given about the mesh. This time code gives the step number. It increases until time is equal to 14.
The plastic zones are shown by shading the area that is plastic. For the first steps, there's no plasticity. Then the plastic zone is small, it develops around the hole and it grows rapidly as the larger load levels are reached.
Note also how the plastic zone spreads through the elements. We used 3 by 3 Gauss numerical integration and test whether an integration point has gone plastic. If so, we shade the contributory area of the integration point. As an average for each integration point, the contributory area is 1/9 ninth of the element area.
Here at step 12, you can very nicely see how the plastic zones have progressed through the elements. The elastic plastic interface boundary goes through the elements. Note that at step 14, after unloading much off the plate is still plastic. This is quite unphysical.
We now rerun the analysis with equilibrium iterations and here is the load displacement response we now obtain. First we look at the scales on the axes.
We note that the loading response is similar to what we had before. Although a much larger displacement is reached in steps 13. The unloading response in step 14 is now quite realistic, with a permanent positive displacement at zero load.
Finally, we show the plastic zones for this analysis. Note that we show the initial mesh time 0 and then immediately the time equals 6 results. Initially, the plasticity progresses as much as in the analysis without equilibrium iterations, but the final spread of plasticity reached in step 13 is larger. And after unloading of the load at the end of the analysis, the complete plate is elastic. However, clearly permanent deformations have occurred as can be seen by looking at the default mesh at time 14.
As we discussed already, our analysis results now look quite good. They look quite reasonable. But one additional way to evaluate the analysis results is to plot stress vectors. We did so in the linear analysis of the previous lecture when we also looked at the analysis results obtained from this mesh, but of course, in linear analysis.
We want to do now the same for the nonlinear analysis results that we obtained. And let us just quickly look at what we're doing in the stress vector output. We plot at each integration point two lines as shown here. If they are carrying an arrow, then it is tensile stress. No arrow means compressive stress. And notice these two lines correspond to the principal stresses. Notice that the lengths of these lines are proportional to the magnitudes of the stresses.
So let's now do a stress vector plot for the mesh at time 13 and at time 14, in other words, at maximum load application and after removal of the total load, four the results that we just have obtained.
Here we see the stress vectors plotted onto the total mesh for the stress state at time 13, that is at total load. We note of course, that there is very much information, there are many stress vectors. To see any detail we have to focus our attention onto certain elements.
Here we now look closer at the elements adjacent to the horizontal symmetry line. We note that the stress vectors correspond to vertical tensile stresses as expected. At a top edge of the plate we see tensile vertical stresses and tensile horizontal stresses. The maximum stress at any integration point is 1100 megapascals and occurs near the hole.
Here we now see the stress vector plot at time 14, that is after load removal. It is most interesting to study the stress flow in the mesh. Note that the stresses flow along and parallel to the free surface of the plate. This must be so because there are no externally applied tractions anymore.
Here we see the detail of the stress flow in the corner of the plate. The stress vectors are parallel to the free surface. And here is the stress flow in the elements around the hole. The same observations apply.
The maximum stress is 880.3 megapascals. This completes what I wanted to show you in this phase of the analysis.
This completes our materially nonlinear only analysis of the plate. However, if we look at the solution results once more closely, we find that in this element here the magnitude of the strains is about 2% at the end of load step 11, 4% at the end of load step 12, and 14% to 15% at the end of load step 13. In other words, at maximum load application, we have certainly here large strains.
And one might very well ask, what is the effect of this large strain on the analysis results? Of course, in the materially nonlinear only solution, we did not include any kinematic nonlinearities.
So our next objective is then to perform analysis that said include kinematic nonlinearities. And we want to now proceed with a total Lagrangian formulation analysis, which includes large displacements, large rotations, but only small strains.
And I also want to share with you some solution results that we obtained using an updated Lagrangian formulation. We did not talk about this formulation in the earlier lectures. We did talk about this formulation, but not about that formulation. This formulation really is best covered in a separate lecture.
However, it's still very interesting to look at the solution results that we obtain we this formulation. If you want to read up on this formulation, please refer to the study guide in which a reference given. A paper is referred to in which this formulation is described.
So let us now look at the solution results obtained from these three formulations. And the solution results that we want to look at are once again the force displacement curve for each of these formulations. In other words, force applies here, displacement seen here, for these three formulations. Let's turn back to the laboratory and see what are the results.
Here we see the analysis results for the MNO, that is the materially nonlinear only, the TL, that is the total Lagrangian, and to UL, that is the updated Lagrangian formulations. We look first at the horizontal axis scale giving the displacement. And then at the vertical axis scale giving the load that is the pressure applied.
Notice that there are three, in fact we will we later four distinct curves. However, under this much plasticity, the curves are almost the same. The TL analysis results corresponds to the smallest displacements. The MNO solution gives larger displacements. And the UL solution gives the largest displacements.
For the UL solution, we actually see two curves when looking closely. These correspond to using once 14 steps as for the TL and MNO analyses and then using once twice the number of load steps. Note that the unloading response in all solutions is quite the same. However, of course, the permanent displacements at 0 applied load are quite different because the maximum displacements corresponding to peak load were different.
These analysis results underline the importance of choosing the appropriate kinematic formation for the analysis. Here, large strain effects are quite significant at the very high load levels.
In the next analysis we now consider the effect of a shaft in the hole. Notice, we look at the same plate as before except that we know first consider elastic condition only. And the shaft is shown here. The shaft has this Young's modulus and Poisson ratio, same as the plate. But it is 5 times thicker than the plate and for the shaft we also consider plane strength conditions.
What we want to do is place a shaft in there, the shaft being initially flush with the hole, assuming no friction between the shaft and the hole. And then we pull on the plate and want to investigate what is the effect of having that shaft there. The analysis input data have to now be modified because we have to put the shaft in there using finite elements as shown here in red. We used collapsed 8-node elements to represent the shaft. In other words, these collapsed 8-node isoparametric elements become, of course, triangular elements as shown here.
Notice we now have a contact surface here. And that contact surface is modeled using a contact algorithm, which we did not talk about in this series of lectures. This again, would be best covered in another lecture. I'd like to refer you here to another paper, the reference of which is also given in the study guide, if you're interested in reading about the contact algorithm. The contact algorithm can take into account friction conditions as well, but in this particular analysis, we assume 0 friction along the contact surface.
The solution procedure that we are using is it the full Newton method without line searches. And the convergence criteria that we are using are listed here. These we have been talking about earlier already. Here we now because of the contact conditions have to introduce also this convergence criterion, which is really a convergence criterion on the incremental contact force.
So let us now proceed with this analysis. And once again, we perform the analysis and of course, we're looking at solution results.
Here we see the mesh of the plate once more, the mesh we used in the previous analyses. We now need to change the input data for the analysis to also define the shaft. This is done using ADINA-IN. We need to define the addition nodal points and elements for the shaft in the same way as we input earlier the nodal points and elements of the plate.
Let's look at the information that defines the content condition between the plate and the shaft. And here we see the input for ADINA-IN. There are two contact surfaces. The one is the plate hole surface and the other is the shaft surface. We denote these two to be a contact surface pair.
Here you now see the mesh of the shaft and the plate. The shaft is defined by triangular elements. Here we see the default mesh at maximum load. Note that the plate has been extended vertically and has shrunk horizontally. The shaft has prevented the hole to shrink much horizontally. And on top off the shaft, a gap has opened. All of these deformations are quite realistic.
Here, we see just the shaft and the ring of elements of the plate around it. Once again, the calculated deformations make sense. If you look closely at the shaft by itself, you observe that it has been compressed horizontally by the plate.
Let's look next at some stress vector plots. These also show that a physically realistic solution has been obtained. Here we see the stress vectors in the element layer of the plate around the shaft. Note that the stress vectors are plotted onto the original mesh. For the element adjacent to the horizontal symmetry axis off the plate, we see a vertical tensile stress and a horizontal compressive stress. Such stresses are to be expected. The horizontal compressive stress is, of course, due to the contact with the shaft.
Note that going around the shaft, the stresses in the plate align to be parallel to the free surface of the hole, since there is only contact near the horizontal symmetry axis of the plate. This completes what I wanted to discuss with you for this phase of the analysis.
Finally, I would like to look with you at the analysis results we obtained when we apply to this plate with the shaft 100 MPa up there and down here. We assume that they plate is made of an elasto-plastic material. In fact, we model that material as shown in our early analysis.
And in addition to this loading here shown, also the shaft expands. It expands uniformly. And in fact, it expands 0.05% based on the initial dimensions of the shaft during each load step and we apply 10 load steps. So the loading then all together is in the first load step, 100 MPa applied here. And from the second to 11th load step, we expand the shaft by 0.05% in diameter, so to say, based on the initial dimensions.
We use the updated Lagrangian formulation to model the response of the plate. Let's look now at these analysis results.
Here we see just as a reminder once more the mesh we are using. Also, here is once more the detail of the mesh around the shaft. This is the default mesh at step 1. The deformations are due to the tensile load of the 100 megapascals on the plate.
Next we plot the plastic zones in the plate as they develop when the shaft expands. Notice again the time code above the mesh giving the step number since delta t equals 1. There are all together 11 steps. The shaft expands from step 2 step to step 11.
We see the time code running and at time 7 we see the first plasticity. This plasticity spreads as the shaft further expands. The maximum plastic zone is, of course, reached at the maximum expansion of the shaft, that is at time 11. This completes what I wanted to say about this analysis. Note that after each analysis step we looked at the calculated deformations and stresses is to identify whether these make sense.
This brings us to the end of this lecture and to the end of this course. I'd like to now just take a few minutes for some closing remarks regarding the course. I mentioned already in the first lecture that nonlinear finite element analysis is a very large field. There are continuum mechanics principles, numerical algorithms, and software considerations.
We could not cover in detail many aspects of all of these fields in these 22 lectures. However, I do believe that the 22 lectures provide a good introduction and a good foundation for further study. I would hope that you would listen to these lectures with your colleagues, that these lectures would initiate discussions, stimulations for your work in nonlinear analysis and, of course, also questions.
We at MIT continue to work in nonlinear finite element analysis. And we also offer from time to time weekly courses. I would be glad to see some off you at these weekly courses to share some of the experiences that you have had listening to these video lectures and also regarding your work in practice.
Finally, I'd like to mention that a video course of this nature can only be produced through the concerted effort of a number of very devoted people. I'd like to thank for their collaboration and support Dick Norris, Elizabeth DeRienzo, Pat [? Regan ?] of the Center of Advanced Engineering Study at MIT, and Ted Sussman, my student. And very finally, thanks also for the crew around here. Thank you for your attention.
Free Downloads
Video
- iTunes U (MP4 - 69MB)
- Internet Archive (MP4 - 69MB)
Subtitle
- English - US (SRT)