Flash and JavaScript are required for this feature.
Download the video from iTunes U or the Internet Archive.
Description: Crystalline silicon solar cells. Feedstock: silicon refining, Siemens, fluidized bed reactor, metallurgical route, novel concepts. Crystal growth: ingot silicon.
Instructor: Prof. Tonio Buonassisi
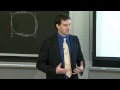
2011 Lecture 10: Wafer Sili...
The following content is provided under a Creative Commons license. Your support will help MIT OpenCourseWare continue to offer high quality educational resources for free. To make a donation or view additional materials from hundreds of MIT courses, visit MIT OpenCourseWare at ocw.mit.edu.
PROFESSOR: But today we're going to be talking about crystalline silicon solar cells. Now, for those of you who do not work in crystalline silicon PV, the reason this topic is important is because crystalline silicon comprises about 90% of all solar cells manufactured today. It's the dominant technology, and the technologies that you're working on are going to displace, or are aiming to displace crystalline silicon, so it's good to know your enemy.
For those who are working on crystalline silicon, this is meant to be a background of all of the different aspects-- the entire supply chain of crystalline silicon-- so that you gain insight into the areas that you're not currently focused on. You're getting a perspective of the bigger picture. Crystalline silicon PV has been around since 1954. The original-- well, in its current incarnation. That was when Bell Laboratories announced the development of the modern crystalline silicon PV cell, and that was 6% efficiency in 1954, published in general applied physics, and the cell architecture, it's obviously evolved over the years but it's not entirely dissimilar from what we have today as a cell architecture for our modern PV cells.
So, over the course of-- it's almost been 60 years of development of crystalline silicon photovoltaic technology. That means both the cell itself, the materials that go into it, and also the manufacturing, or the methods to produce said materials and device, over the course of those, almost, 60 years much innovation has happened both in terms of manufacturing and technology. So today, we'll be going over kind of a status quo snapshot of where crystalline silicon stands and we brought in a number of show and tell items so that you can see as we talk.
So just for the show and tell, we're going to be moving from the feedstock materials over here finally into wafers and cells on that side. All right. So, these lecture notes are going to be valid for both 10 and 11. We're going to split this up over two classes to really dive into some of the details. The first question is why silicon? Why did silicon evolve as what is currently the dominant technology, which is currently 90 percent of the PV market, and I think it boils down to a couple of reasons. One is scalability. If you look at the elemental abundance, on the vertical axis it's abundance, atoms of the element per 10 to the 16 atoms of silicon. The reason that everything is normalized to silicon is because there is, well, quite a lot of it in the earth's crust. As you can see, it's the second most abundant element on the Earth's crust.
It just so happens that, out of all the stardust that is here on the planet, we have a high percentage of silicon like the moon and like many other planets in our solar system-- at least the hard ones. You can see oxygen is probably the, well, oxygen is the only element with higher natural abundance in the earth's crust, the upper crust, than silicon and we go down as we go to higher and higher atomic number. The probability of formation due to subsequent fusion reactions in stars decreases and, hence, it follows this almost a power law distribution as you can see there. So it's scalable.
It is present in the Earth in high enough capacity to reach terawatt scales. It's nontoxic and, as Don Sadoway likes to say, if you want batteries dirt-cheap, you have to make them out of dirt. A similar expression is used in the crystalline silicon community. I believe the quote in 1366 is, "It's not only good for the planet, it is the planet." A variety of riffs off of this particular chart right here, but from a technological point of view, why did silicon evolve to the point where it is today?
It forms a very tenacious surface oxide. So, if you were to expose a piece of pure silicon to air, the surface oxide that forms is very, very strong and very resistant, and very dense. So, unlike some materials that corrode when exposed to atmosphere, silicon oxidizes maybe the first few 10s of angstroms, 100 of angstroms, and then it peters out so it's diffusion-limited oxide growth mechanism that eventually stabilizes at a very thin but very dense and very protective oxide layer. So the risk of having a silicon wafer degrade inside of a solar module is very low. Furthermore, that oxide layer from an electrical point of view it's very passivating.
So as we studied on, as we solved in the exam, those interface states or those surface states, the surface of semiconductor, those can be reduced or minimized by the presence of certain passivating layers, and it just so happens that by the benevolence of nature, the silicon oxide, which is shown in these red triangles right here, has a very low surface recombination velocity, passivates a surface very well, and results in high-performing devices. In this particular case, they're plotting emitter saturation current density in femtoamps per centimeter squared-- this is very, very low-- versus sheet resistance.
This is essentially the dopant concentration in the emitter, so they're looking at how the passivation quality changes as a function of dopant density and silicon oxide works pretty well, and it's an effective diffusion barrier. And, probably most significantly, those are maybe one looking forward rationale one technological or scientific rationale and as far as the field is concerned, as far as engineering community is concerned, silicon has a lot of momentum. It's the most common semiconductor material, silicon and germanium were both purified, more or less, around the same decades but, because silicon has a wider band gap, you have a lower thermal carrier concentration, lower intrinsic carrier concentration, folks were able to make transistors and devices with lower noise out of silicon as opposed to germanium and silicon technology really took off in terms of the PV industry benefited a lot by that cross-pollination.
Many technologies came in from the integrated circuits industry to assist or give a boost to the PV industry. This number is a little outdated, it's now about $100 billion. Hard to keep up with things growing at 68% a year. Technology acceptance results in lower interest rates. So if you have a technology that is well-accepted by the market then you go to a bank and say, hey, I want to install some of those things and the bank says what are those things you say oh, hundreds of thousands of them have been installed already. It's OK. It's a proven technology. The bank says OK, I'll lower your interest rates. That means you pay less money on interest. Your capital is more cheap. It works better in your favor, and the opposite is true with an entirely new technology that's unproven.
So that's really summing up why silicon. Momentum, forward motion if you will, some inherent intrinsic technological advantages, some of which are listed here, and I'll get to that in a second, scalability. To get back to the technological advantages, I think it's important to recognize what they are so that when you're thinking of a new material, you can cross check and say, gee, do I have these or do I not have these. If I don't have them, it's not the end of the world. You might have other advantages that overcome the ones that silicon doesn't have. Let's add some more into this list. Just stream of consciousness. Silicon has a very high refractive index near the band gap edge. So, near the band gap edge, it's absorbing light less efficiently. Right? It has a larger attenuation length of the light, a smaller optical absorption coefficient right as you approach the band gap.
So silicon absorbs poorly in the infrared because it's an indirect band gap semiconductor, but it also has a very large optical, sorry, a very large real component of the refractive index. Does anybody remember what that refers to? Real component of refractive index. Lesson number two. What does that dictate?
AUDIENCE: Reflection.
PROFESSOR: Reflection, exactly. So, if I were to tailor and index of refraction grading on the front side of my device, so I allow the light to be absorbed efficiently, on the backside I can put a very large index of refraction mismatch so that the light bounces back. In other words, the light trapping silicon is benefited by the fact that you have this awesome reflection capability. The refractive index is around 3.6, the real component of the refractive index, in the infrared at around 1070 nanometers. Which means that if you design your cell right, you can get an extension of the optical path length by a factor of 50 over the thickness. So if your thickness of the device is d, the optical path length can be increased up to about [? 51d. ?] That's as a result of this great reflectance.
Many other materials that are being explored as PV materials have refractive indices around two, which would mean that your optical path length extension is around 16. So that's one thing to keep in mind. even though it doesn't absorb light quite as well, it traps light fairly well. Another advantage of silicon is that it forms sp3 hybridized orbitals, for chemists, it forms-- it's tetrahedrally coordinated, in other words bond to four other neighbors, and most 3D transition metals don't do that. They don't bond in that configuration. Some do but many don't and, as a result, the solid's solubility in other words, the ability to incorporate impurities into a growing silicon crystal is low. It rejects the impurities from the solid into the melt, and you're able to purify the material very efficiently.
That's not always the case with most materials. Sometimes they incorporate impurities very readily, up to a few atomic percents. The typical impurity concentration of silicon is in the order of parts per million, parts per billion, parts per trillion. Still can be enough, as you learned during your homework assignments, still could be enough to affect device performance but is very low. It would be a lot worse if silicon were able to absorb more impurities and so forth. So, there are a number of reasons why the silicon PV technology has gained the foothold that it has so to bump it out of its leadership position, one really has to be clever and the parameter of merit is performance per unit cost. Kilowatt hours per dollar, if you will.
So, we're going to talk about the current manufacturing methods and materials because this will give you an insight into the dollars per kilowatt hour, the kilowatt hours per dollar. Essentially, the cost per unit energy produced. You can begin to seize opportunities within the crystal silicon world to improve the manufacturing process or you can begin to say OK, you know what, this is way too complicated. Let me take a completely different route. I'm going to develop a new technology instead that will overcome these manufacturing difficulties. So let's explore them in detail.
First, the market. This is the evolution of market share from 1980 to mid 2000s. After mid 2000s, the market just continues growing at 68% a year and you really lose resolution to this portion down here so it's to 2006 so that we can actually see what's going on in the earlier days. In the earlier days, 1980, let's pick 1985, the market was split about a third-third-third between thin films, amorphous silicon namely, monocrystalline silicon, and a material called multicrystalline silicon. Now let's go piece by piece. What is monocrystalline silicon, multicrystalline silicon and thin films?
Well thin films are materials that are usually between a few hundred nanometers up to about three, maybe five microns thick. To give you size perspective, your hair is about 50 microns in diameter, so we're talking about 1/50 the width of your hair. That's the active absorber layer and of course the plastics and encapsulates and everything else that go around them make it a bit thicker, but the absorber layer is very thin and so you're not spending much on your absorber layer. It absorbs light very efficiently, has a very large absorption coefficient, and is able to absorb photons efficiently.
Crystalline silicon, on the other hand, does not absorb light as well as many thin film materials so we need about an order of magnitude to two orders of magnitude thicker substrates, and the crystalline silicon substrates today in commercial manufacturing are typically between 160 to 190 microns, with an average around 170, 180. So about four times the thickness of your hair. Monocrystalline silicon and multi. Let's talk about the difference there. So, monocrystalline silicon, folks are probably familiar seeing pictures, at least something like this. Right? So this right here is an example of a Cherkofsky silicon wafer. Appropriate for integrated circuit work. I'll pass this around so folks can get a sense.
So this is an example of a monocrystalline silicon wafer for the integrated circuits industry. Let's analyze it in a little bit more detail. So, the front surface is polished, nicely polished. Polished to, I think, somewhere in the order of a few nanometers mean surface roughness. Using a chemical mechanical polishing mechanism. The thickness is around 700-- or 675 microns. Somewhere in that range. So very, very thick wafer. The objective is not to break. Right? If you're making integrated circuit, this entire wafer that I'm holding right here could be worth a few 10s or 100s thousands of dollars by the end of the processing sequence, so if one of these breaks, that's an awful lot of revenue that the company's losing. So the substrate is thick because they don't want it to break. Silicon is brittle at room temperature.
If you were to manufacture solar cell out of this, you could but it would be very expensive. The chemical mechanical polishing that they use to flatten the surface out costs a lot of money, it's very time intensive, and the thickness of the silicon is above and beyond what is necessary to absorb light well. If anything, increasing the thickness is just increasing your emitter saturation current, since you have a higher recombination current being driven by bulk recombination. You have more recombination centers because you have a greater thickness, and it's driving a larger diffusion current from the emitter into the base. So making it this thick really doesn't make sense. So I'll pass this around so folks can kind of get a sense.
Make sure this gets the entire round. I'll be recycling those platens. Please hold, if you're going to take it out, which you're welcome to do, please hold it like a photograph. What I don't want to have happen is folks put their fingerprints all over it. The wafers that are used in the PV industry are cut from the same ingot like that one, except that the ingots, essentially, if you were to pack circular wafers into a module, it would look something like this. Here's your module and, mind you, you're spending a lot of money on the glass and the encapsulates and the aluminum framing and so forth, and now your solar cells look like that. There's probably more of them that you can put in here, but what do you notice about this? What is the packing density, or packing fraction. It's very low, right? You're losing all of this material in between. All that space is just going to be blank space.
Some of the earliest PV modules actually use circular wafers, but the more modern ones, what they do is a very complicated cost analysis where they say, OK, if I were to chop off the edges of my wafer and completely remove them, I'd be losing a lot of silicon but I'd be increasing the packing fraction. So in the limit that my module materials, the glass, the encapsulant, the framing materials are infinitely expensive and my silicon costs nothing, I want to do this. In the limit that my module materials are free and installation is free but the silicon is super expensive, I want to keep full round wafers, and the reality is that we're somewhere in between. And so, instead of making one or the other extreme, typically what you'll see is something like this chopped off, like that, where you have a pseudo-square. The wafer itself has flat edges on the sides but it also has kind of pseudo-rounded corners here, and Joe did we bring any of those in? The psuedo-squares, the monocrystalline psuedo-squares. These ones. OK. All right. No worries. I'll show them to you next class.
So, the idea is to make-- cut it out of the same ingot as that one right there, but make it thinner, on the order of 170 microns thick, and to chop off part of the edge, and how much you chop off depends on the dynamic pricing of silicon versus module materials and installation and whether or not you can sell the module, if there's a certain threshold of performance that it needs to reach because obviously, if you have a bunch of dead space in here, you're losing that to-- you're not producing power out of that. So if somebody wants a module that's yay efficient, you might want to increase the packing density. So that's monocrystalline silicon. Multicrystalline silicon. Let's put it this way for now. We'll describe how multicrystalline silicon is made, but for now I'm going to say that multicrystalline silicon is a crystalline silicon variety that is comprised of many small grains.
So if you look at a multicrystalline silicon wafer, something like, let's say, oh this is a perfect example right in here. If you look at a multicrystalline silicon wafer, you can see that it looks nice and-- here maybe, that's probably an OK view of it. You can see individual grains. Right? If you look closely at it. And those are grains of crystalline material that are joined by grain boundaries. So the grain orientation in one region might be pointing in this direction, the grain orientation in the neighboring region like that, and they come together at a grain boundary and, when we have polycrystalline materials like this, it's generally indicative of some faster growth that didn't allow for a nice homogeneous single crystal material to evolve, and that's indeed what happens during the multicrystalline silicon ingot growth. It's occurring under a slightly modified growth condition then, say, that beautiful single crystalline piece over there, and we'll explain how they're made in a second.
So those are the technologies in general, the base absorber materials, and then there's ribbon silicon which is a really, really small fraction of the total production in decreasing, but at one time, ribbon silicon was viewed as the up and coming technology. Still today, there are about 20 startup companies around the United States working on some aspect of this and probably about a dozen more around the world. Yeah.
AUDIENCE: I had a question about the multi.
PROFESSOR: Yeah.
AUDIENCE: So for the multi and micro and poly, is that different grain sizes?
PROFESSOR: Sort of. So, multicrystalline silicon is a polycrystalline silicon material. The definition of multicrystalline silicon is that the average grain size is about a centimeter squared, or larger, and that's where multicrystalline came about. Polycrystalline silicon, in the silicon community, has a very specific meaning. It means, usually a plasma-enhanced chemical vapor deposited layer, so PCVD-deposited layer of silicon, that has on the order of one to five micron diameter grains. So very, very small grain material. About 1/50 the width of your hair. Maybe 1/10 the width of your hair and, to distinguish it from that really small grain material that will perform very poorly, one calls this multicrystalline silicon.
AUDIENCE: And is there microcrystalline silicon?
PROFESSOR: There is also microcrystalline silicon and microcrystalline silicon is actually at the phase transition between amorphous and polycrystalline silicon. So as you're going from an amorphous material increasing the temperature, let's say, of growth or increasing other parameters during the deposition process, as you begin to evolve from an amorphous material into a crystalline material, you transition through this microcrystalline regime which is a bit of a hybrid. It has some regions that are amorphous and other regions that are crystalline. In your assigned readings, this book was assigned, and I believe in the syllabus it says read chapter X.
Unfortunately, there is no chapter X. I guess you could interpret it as 10, but the essence was that there are two versions of the book. One is version three, which was published about seven years ago, and the newest version just came out last year. The newest addition is addition three. So the chapters have rearranged slightly, but what I'll do is I'll highlight crystalline silicon solar cells and modules in here so that you can get a sense of what is in the chapter and you're welcome to go back and have a look. So I'll go ahead and highlight this chapter right here and pass it around. Feel free to glance through the book as well. It's a great read. It dives into great detail into each of the different technologies.
OK. So, let's talk about feedstock refining. We're going to start the silicon value chain from the raw materials and work our way all the way to the final module at the end. So we'll start with the feedstocks themselves. Down here is a rough cost breakdown. Kind of think of it as wafer, cell, module being like a third-third-third of the total module cost and then balance the system components beyond that. So we'll start from our feedstocks and the raw materials in the ground, we'll wind up with systems on the roof, and we'll walk through each of the different steps of current manufacturing process.
So raw materials. Shown here is quartz and coal, for a very good reason. The way feedstock refining occurs at the very first stage is to take oxidized silicon, silicon dioxide, quartz and to reduce it to silicon, say, silicon zero. Unoxidized silicon, which is also called silicon metal. It's called a metal because it is very low resistivity. It's very low resistivity because there's a very high impurity content still. The purity of this material coming out here is around 99, 99.9% here. So, it sounds like a high purity but, if we're talking about parts per million of impurities, we have some further refining steps to do after this. So let's walk through this.
We start with the raw materials in the upper left. It says raw material inputs. Carbon and SiO2. The SiO2 forms, usually, quartz. That can be some of high purity pegmatite, it could be, for example, a hydrothermal quartz, higher purity varieties of quartz. You could even use, maybe, a metamorphic quartzite material.
Let me explain. So, some of the highest purity materials are coming from these veins of magma that float up and then phase separated during millennia. Some of the lowest purity quartz is coming from sand, essentially crushed rock that made its way into, say, a beach-like environment and then rock was deposited on top of that, pressure was increased, and this whole mixture of mica, feldspar, and of quartz got pushed together and formed a solid block. That would be your metamorphic quartz materials, and so you'd have a much higher impurity content in the metamorphic quartz than you would in, say, a high purity pegmatite or hydrothermal quartz.
Regardless, depending on the feedstock source of the quartz, and there are people who study this. Believe it or not, there are entire departments dedicated to mining quartz and figuring out where the different veins of the highest purity quartz are, where you get them from. That's the SiO2 input and the C input over here on the left hand side, Carbon.
So, typically what is used in the PV industry is either a fast-growing wood source like eucalyptus or southern pine, right? Northern pine tends to be slower growing, but eucalyptus and southern pine both tend to be fairly fast-growing. You can tell by the spacing in the rings, if you chop the tree down and do a cross section, or coal. So carbon, essentially. And the two react inside of this furnace right here and this furnace, just to give you a sense of scale, here's a human being.
This is the furnace. So it's about five stories tall, 12 meters in diameter. It's a big, big, big creature. This furnace right here is what is producing the reduced silicon and what's happening is these feedstock chunks are being thrown in at the top and there's an arc going between the electrodes, usually some carbon-bearing material, and a base contact, and so that arc creates a very high temperature. Something in the order of up to 2000 degrees Celsius, near the arc, and the temperature decreases as you go further and further away, so up near the top here it might be even below the melting temperature of silicon, somewhere around 1,200 degrees. So this is an extremely inhomogeneous, messy system.
This metallurgical grade silicon refining furnace right here, this arc furnace, also called a carbothermic reduction furnace, a very busy place. Lots going on. Extremely inhomogeneous if you were to take a cross section also in terms of temperature and in terms of the chemical states of the different constituents species, but the general reaction that happens is the carbon would much rather bond to the oxygen than silicon, and so the carbon steals the oxygen from the silicon reduces the silicon to silicon metal and CO2 is released. We'll get to that in a second. Flag that. Put an asterisk next to it. We'll come back to that in a second.
Other byproducts of this reaction, so this is the liquid silicon metal coming out here at the bottom. It's essentially liquid molten silicon reduced, so silicon zero, not a silicon oxide, reduced silicon metal, and then finally it's poured into these buckets, also called ladles and solidified, crushed up to size, and then distributed at the end. Other byproducts coming out of this reaction include-- this is liquid silicon up hear. It's very high temperature and there are gases and a lot of oxygen because of the reduction process, and so silica, or SiO gas, can be produced and silica gas can begin aggravating and forming very small particles, almost like shards, of silicon oxide material, and these can be on the order of one to five microns and very rough and jaggedy around the edges. Now, who here has studied public health and knows anything about PM1 or PM1.5 denominations. Do they ring a bell? What are those Ashley?
AUDIENCE: It's the size of particles that can get stuck in your lungs.
PROFESSOR: Exactly! Right? So PM1 or PM1.5 would refer to the micron diameter, 1 or 1.5 micron diameter particle that would get stuck in the [INAUDIBLE] and result, eventually, in edema or, probably, more of water filling up in the lungs as a result of the body trying to expunge these, and because they're jaggedy and pointy, they get stuck in there and they don't come out and eventually the people can even affixate as a result.
So, before in the past, when we had these big smokestacks sitting on the top of these metallurgical grade silicon refineries that would just spew the silica dust into the air, the folks downstream would be affected and this actually did happen, to some degree, in, for, example, Kristiansand in Norway and, as a result, the refineries began putting in filters over here to prevent the silica dust from getting thrown and spewed out into the atmosphere and the filters are a very interesting contraption. A lot of work went into designing them just right to allow the air to go out but the particulate matter to stay behind and once every delta t, maybe in the order of an hour so, the airflow direction inverse and all the dust comes crashing down to the bottom and then gets collected inside of here. It's kind of like pushing air through the different direction through a sock, and all the dust comes out to the bottom, you collect it, and it's sold to the--?
AUDIENCE: The footwear industry for absorbing--
PROFESSOR: It might be. I don't know, but I know that the majority of it goes to the cement industry and so, depending on the market rates of silicon, here at the bottom metallurgical grade silicon, versus what the cement industry is willing to pay, you might tune your process to optimize for one industry or another. So, this is to say that early on in refining processes, you're serving multiple industries with one plant and volatility of pricing is affected, in part, by what those other industries are doing. What the demand there is. It's something to be aware of.
Let's go back to the CO2 real quick that's being emitted. So that is one of the byproducts of the reaction. In terms of total CO2 content from the production of solar cells, the CO2 produced during the reduction process is a small percentage, I think something under 5% or 10% is the number I pulled out of my head, it's a small percentage of the total CO2 emitted during solar cell manufacturing because the electricity that goes into producing the rest of the solar cells coming from fossil fuel based sources comprises the majority of CO2 emissions during fabrication of these devices. The electricity used to run these electrodes, for instance, the electricity used to melt this silicon byproduct here, or to gasify it in the subsequent reactions, that is the majority of the CO2 coming out of the process.
Any questions so far about this? They're fun plants to see. We don't have too many of them in the US. Majority of these carbothermic reduction furnaces are either in China, Norway. Norway has a lot of cheap hydropower so the hydroplant is usually only a few 10s of kilometers away from the refinery and if you go to, say, [INAUDIBLE] in Norway, where they have a number of these plants, you'll see not only silicon being refined there but also magnesium, other elements, aluminum being smelted in the same peninsula-- the same industrial park.
AUDIENCE: When general mining of silicon happens or silica, the Chinese have--
PROFESSOR: The reduction process, this carbothermic reduction process here, the majority of it happens at the same places like Norway or China-- places that have cheap electricity. There's also a feedstock refinery. I don't know if it extends all the way back to the metallurgical grade silicon refining, but there's a feedstock refining facility going up in the Middle East right now in Qatar, as a result of the cheap natural gas. So, wherever you have cheap access to energy, you can set one of these plants up and get off and running and your CO2 intensity will be dictated by the fuel source that you're using. Hydro, in that case, it might be low unless you take methane into account that might be emitted in the reservoir, if you have decaying biomass underneath the water, but if you would exclude that and if you look at the CO2 intensity of the fossil fuels that are being burned, it might be better to do it in, say, Norway, from an environmental point of view, than to, say, manufacture this stuff in China. Yeah.
AUDIENCE: How many kilowatt hours are we talking [INAUDIBLE]?
PROFESSOR: Okay, so what is the energy intensity of this process right here, in other words. Well, why don't I put a flag on that. Why don't we put a flag on that and come back with specific numbers for this process right here. I don't want to say something and regret it later.
AUDIENCE: Well, we know the energy intensity of the solar panel itself.
PROFESSOR: Yeah.
AUDIENCE: But the energy--
PROFESSOR: But specifically what fraction comes from the MGSi refining, I'd rather not pull something out of my head. Any other questions? OK. So somewhere in the order of two million metric tons of metallurgical grade silicon are produced annually. Probably somewhere in the order of 10% of that is destined for the PV industry. The remainder gets split among a variety of different industries. So what I'm talking about here when I say metallurgical silicon, I'm referring to this right here. This stuff coming out. It has about 99% or 99.9% purity and it gets used in a variety of industries. So those industries are: the PV industry, and we'll explain how the rest of the refining happens, the integrated circuits industry, that's the wafer that just went around that's made its way back up here, and silicones those are-- so, a pet peeve of mine is hearing the word silicon and silicone used interchangeably. Silicon is this element-- is an element on the periodic table and it's the element that comprises this wafer right here.
Silicone, on the other hand, is an organelle, I guess you could say, it's not exactly organelle metallic, silicon isn't a metal, but it would be a molecule that is comprised of carbon atoms and silicon-- silicon being in the middle and the carbon being on the sides-- and that is used as caulking or sealing agent in your showers, for instance, or in plumbing, round windows. It tends to be very flexible, compliant but yet impermeable, preventing the inflow of gases. So silicones, they're metal alloys including steel and aluminum. Why would you silicon there? What does it have to do with steel or aluminum? Let me ask this. Has anyone ever played with pure aluminum? Highly refined, ultra high purity aluminum. Say five nines or six nines. Yes! What happens to ultra-pure aluminum?
AUDIENCE: It's really flexible.
PROFESSOR: It's really flexible, you can dent it with your fingernail, and it wouldn't make very great boxes. Right? So we need it to be stronger and scratch-resistant and so we have these additives into the aluminum, silicon being one of them, that increases the strength of the aluminum, essentially preventing plasticity or preventing a dislocation flow into the material. So that's more or less how silicon-- metallurgical grade silicon, also called MGSi as shown up here at the very top-- that's how MGSi gs is distributed worldwide and that's the current production. Now let me ask another question. Steel and aluminum, where are those used the most? What industry uses steel, aluminum the most?
AUDIENCE: Construction.
PROFESSOR: Constructive industry, automotive industry. How fast are those growing annually? Let's estimate it from GDP. Annual-- worldwide GDP. What's the worldwide GDP growth look like. US is around 1%. China 8%. Let's pick a number somewhere in between. Four, right? All right. So, let's say 4%, 5% worldwide. Silicone's probably on that order. How about the PV industry. How fast is it going right now? Somewhere in the order of, it's a volatile year right now, this one year, but in the past, historically, it's been around 40% to 60% a year.
So, where do you think the price pressure for metallurgical grade silicon is going to come from? What industry? It's going to come from PV. It's a small fraction of the pie right now but it's growing fast. Something to keep in mind. So that's why, if you look at pricing of metallurgical grade silicon, yes. Superimposed upon pricing is a function of time. You have the global macroeconomic situation. Right? So that's kind of the dampening function on top of it all, but there's just this general trend toward rising prices as you put increasing price pressure on metallurgical grade silicon. So additional refining capacity will be needed if the current growth keeps up in this industry.
So let me talk about going from metallurgical grade silicon about two nines to three nines pure. What I mean two nines means 99%, three nines would be 99.9% pure, to silicon that we can use for solar cells, which typically has to be about six nines pure. And so this is called the Siemens process which is purification through gaseous distillation, and that's the method that is currently used to make most of our silicon. So the way this process works is we start with metallurgical grade silicon at the top, represented by a little sack of metallurgical grade silicon chunks. We produce silane gas out of that metallurgical grade silicon. We essentially- silane gas is SiH4. So it would essentially be this right here.
So you'd have a silicon atom here, tetrahedrally coordinated with-- tetrahedrally meaning four bonds with hydrogen atoms on the side-- and this is silane gas-- well, silane-- which, at room temperature, is a gas and that's what happens in this step right here. We're forming-- we're gasifying the silicon. This process is the distillation process. To extract the pure silane gas, it's the distillation process that's used in large towers similar to fractional distillation where we might heat up the material and then, depending on its mass, it settles down to a certain height in that tower and we're able to extract it. The silane gas here has been sold to the photovoltaics industry. LCD. Liquid crystal display. Right? Thin film industries as well, they use silane. If you're depositing the polycrystalline and silicon for your LCDs or if you're making amorphous silicon solar cells, they use silane as well. So this little truck here might go to three different companies, depending on who's willing to pay more.
Most of the silane is used for polysilicon. The gas has to be converted back into a solid, and that's where this particular process here, the Siemens process is used. Again, you have a current passing through some seed material and the gas is being cracked onto that seed. You form these rods. The rods are then cracked into chunks and then the chunks are loaded into ingot crucibles. Yes.
AUDIENCE: So the silane gas is shipped as a gas in the trucks.
PROFESSOR: Sure.
AUDIENCE: Or on rails?
PROFESSOR: Well it's pyrophoric, as you can guess from just glancing at this chemical structure right here. It's highly reactive. Pyrophoric means that it can combust at room temperature. It can catch on fire, meaning there are more stable compounds than this that can form when you react this gas with air and, during the early days of silane development, folks really didn't know much about it and there's some early research-- some of the earliest research done here at MIT, in fact. They would fill up an evacuated chamber with silane gas and spark and nothing would happen. Spark a second time, nothing would happen. Spark a third time, boom. OK. That's critical limit. Such and such amount. You know, they'd keep increasing the amount and finally it would go boom.
Tell you what, lets repeat the experiment since we're good scientists. They'd repeat it and, at low concentrations, click. Boom. That's strange. That was much lower this time. Let's repeat the experiment one more time. Click. Click. Click. Click. Click. Click. Click. Click. Click. Boom. All right. I don't really understand this gas, but I'm going to say it's really dangerous so I'm going to have little warning bells that will detect the silane gas if it's leaking and tell people to get the heck out of the building if it starts being leaked. It's also toxic for humans, by the way. Very small dilute concentrations can kill you and so three buildings on campus, only three to my knowledge, are set up with the proper safety equipment to use silane gas in the laboratory.
Building 13, which is the material science building, and then-- MTL and related. So we have this gas right here. Extremely powerful. There are variants thereof. You can replace some of the hydrogens with chlorine, like this and now you have trichlorosilane. It's all one word. So tricholorsilane, I've just replaced three of my silanes-- my hydrogens with chlorine and now I have a different molecule, still silicon bearing, still very reactive, but now reactive at different temperatures and I can modify my process by substituting out some of the hydrogens for chlorines.
So we have the silane gas or trichlorosilane or the variants thereof, loaded into some transportation vehicle that is very safe, leak-proof and preventing accidents on the road, to deliver it to where it is going to be consumed, which are these so-called polysilicon, or Siemens reactor as shown here. Excuse me. What happens, or how the process actually flows, let me go back one step. We're going to start from up at the very top of the process and move all the way down, showing you what the manufacturing equipment looks like at each step. So, this is the distillation process used to create the silane and when you see one of these factories just think of a refinery. In fact, the people who don't like this particular process who aren't a fan of the silane refining process and opt for other ways of purifying their silicon, liken this to an oil refinery. The imagery is very stark there.
The polysilicon production, this is the Siemens reactor, it's much smaller in comparison to the metallurgical grade silicon furnace. Much smaller than the carbothermic reduction furnace. Here, we have a small human or human next to the small contraption. Here are a series of them lined, almost like little pods and, out of this material, actually inside of the furnace, you have these rods that are passing current and heating up and the silicon is cracking onto the rods. So we wind up with six nines, usually called 6N solar grade silicon as a result of this process. We could also go up to, even, nine nines using the Siemens process. It could be very, very pure depending on how fast you grow, what the purity of your silane gas is.
AUDIENCE: Yeah. What is cracking. What does that mean?
PROFESSOR: Sure. So what it means is this gas molecule comes in, sees a solid surface, the central atom right here, the silicon atom, gets deposited onto the surface, becomes an adatom, which means it's a surface atom, it's scuttling around and the remaining elements within this molecule are then free to move away as a gas.
AUDIENCE: So you've broken those bonds.
PROFESSOR: Yes. Effectively, you've added the core constituent of this molecule onto the surface. It's joined the collective if you will and, in this matter, the diameter of those rods grows with time. So what I'm going to do is pass around an example of a chunk coming from this Siemens rod. Be very gentle with it please. On the outside you can see a corrugated, rough, cauliflower-like structure. That's because you're optimizing for deposition speed, not for beauty of the surface. You don't really care how flat it is, unless you're trying to grow a very specific type of material called flotsam, which we get to the second, but in general, if you're trying to crack it up and break it into a smaller piece and into a chunk like this and throw it into a big ingot furnace, it doesn't really matter what the surface looks like.
On the inside, it's pretty dense silicon and, if look very carefully, right in the middle there you can see the rod. The initial seeding rod. It's a slightly different color. So I'll pass these around and please be gentle.
AUDIENCE: Is the seeding rod just silicon?
PROFESSOR: It's actually doped silicon, so it's lower resistivity so you can pass more current through it. This here is chunks, or smaller chunks of the polysilicon so, essentially, just crushed polysilicon and if you're trying to load a crucible with big chunks like this you'll leave a lot of empty space unless you crush some of this up and make finer grains out of it and fill in the gaps. So I'll pass these around right here so you can have a look at them. Those are examples of the Siemens grade polysilicon. This is a bigger rod. Here is the seed coming right through the middle. Here's the surface where you can see it's kind of rough and corrugated and one of the biggest issues with this feedstock refining process is that there are very large plants and long lead times.
This is a plant construction going on right now, you can see. Typical lead times are between 18 and 24 months. That's a long time between when the board says yes, we will create new silicon refining capacity and product starts to roll off the production line and into customers' hands. It's a long time and what this results in are drastic oversupply and undersupply conditions in the market. So the silicon feedstock price goes very high during periods of undersupply and very low in periods of oversupply and we're in an oversupply condition right now. Five years ago, let me quantify this. Five years ago if you went to the spot market-- maybe four years ago-- if you went to the spot market, you could pay $100 to $500 per kilogram of silicon. That material that was just right there I bet one you would put it into your bag and run away out the door right now and be able to go to Mexico. Now the polysilicon prices are much, much lower on the spot market. Somewhere in the order of $30 to $50 per kilogram. About an order of magnitude lower.
AUDIENCE: Isn't lower cost silicon better for the PV industry, though?
PROFESSOR: Is it better for the PV industry? As a customer most definitely, it is good for you. As an installer, it is most definitely good for you. As a polysilicon producer who wants to be a sustained industry presence, it's not good for you. So this wide oscillation between fat cat and scrawny is not very good for any industry. It's unpredictable and it causes some players to drop out.
AUDIENCE: OK.
PROFESSOR: And the investments are very large as well. As you go from the early stage portions of the value chain toward the module, the investments generally decrease and so this is an outlook coming from last year-- the numbers are still a little bit outdated-- polysilicon production is buttressing up against 200,000 metric tons per year at this point in about 3/4 to the PV industry. The cost of manufacturing is between $20 and $25 per kilogram and 2010 prices were around $50 to $70. Now they're on $30 to $50 in 2011 and the 2008 prices were around $500 per kilogram in the spot market and it really boils down to the inability to adapt to demand.
If you have a very large contraption that produces the feedstock materials and it takes a long time to build the factories, you're just not going to be able to adjust fast enough. Here's supply and demand, demand being the red and supply being the blue. You can see how the oversupply-- the undersupply condition of the mid 2000s really led to our current condition. So, alternatives to solar grade silicon feedstock refining. What are some people thinking in terms of other processes that they can use? These are two processes right here and, mind you, when we were in this situation with this price for the silicon, everybody and anybody was coming up with new ideas of how to manufacture the silicon. Now that we're barely selling at cost and in an oversupply condition, many of these ideas are having a struggle-- a hard time in the market. They're struggling right now. So fluidized bed reactor and upgraded metallurgical grade silicon.
Let's talk about each of those in turn. So what the fluidized bed reactor folks realized was, gee, if we're depositing on a rod, our surface area to volume ratio is really large-- sorry, is really small. Our surface area to volume ratio is going to be very small. So think of it this way. If we have a sphere, a sphere would be the quintessential example where we'd have a very large surface area to volume ratio. If we had a plate, we would have, as well, a very large surface area to volume ratio and in the case of the condition prior, where you have this rod, you really can't deposit that quickly and so what these folks decided was, what we're going to do is introduce small silicon granules into this vessel, into this evacuated chamber, and-- here's the evacuated chamber right here-- and we're going to flow silane gas into the system right here and the smaller particles are going to go higher up because of this flow of gas coming in the bottom and those will grow and eventually settle down down here where we can extract the bottom.
So we'll wind up with these beautiful little silicon granules. These ones shown right here, which I'll pass around as well, those are coming from a fluidized bed reactor, and they're nice beautiful, spherical granules that are grown a lot faster, I mean, a lot more silicon is deposited per unit time than through the Siemens process as shown there in the back. As a result, the energy intensity is lower, the cost is lower, there's a very tricky process to nail to get just right, because you have to get the gas flows right, you have to design the chamber well, redo some purity contents. It's a tricky process, and so this is being produced right now, I believe, by only a few companies. REC has a capability of doing it. MEMC, as well, has the capability of doing this process. By and large, most silicon is coming from the Siemens process. Yup.
AUDIENCE: Sorry, both of those companies have the normal refining process?
PROFESSOR: They have the normal refining process.
AUDIENCE: The [INAUDIBLE]
PROFESSOR: Yup, and that's why they developed this new one. They had these smaller, internal projects that we're able to develop. So, yeah. I was just mentioning the energy intensity. This is the kilowatt hours per kilogram, going back to your question about energy intensity. This is trichlorosilane based Siemens process, silane based Siemens process. They're more ore less comparable in terms of energy intensity. And the silance based fluidized bed reactor process. According to internal REC numbers, which are little rosy, but never the less, the trend is correct here. It is lower somewhere in the order of an order of magnitude energy intensity, and cost is lower as well.
So let's move away from the silicon refining by distillation process entirely. Let's leave gaseous distillation aside and say, what if we were to take this metallurgical-grade silicon and, through liquid purification routes, result in high purity silicon. How would we do that?
Well, if we turn to other industries, the ones that smelter aluminum or refine manganese and so forth, we would see a multitude of different options that we could borrow. Slag refining, bleaching, leaching solidification. Let me walk through them one by one. Leaching-- that's fairly straightforward. So if we put in some acid, for instance, that dissolves the metals but doesn't dissolve the silicon we could leach the metals out of the material, and so that's the essence of leaching. You might crush up your material, in other ways other ways expose the metals, or impurities, to the acids inside of your system.
Slag refining says, gee, what if we were to introduce some material that could absorb the metals into it? The solubility of the metals would be higher inside of the slag agent than inside of the liquid. Maybe we throw in calcium oxide or yttrium oxide or some, usually it's a metal oxide that has a very high melting temperature that remains a solid or, at least a glassy solid, and we pour it on top of our silicon and it's able to absorb, say, the phosphorus or the boron that's inside of our silicon so that we reduce impurity content and then we can add the phosphorous and boron later intentionally, but to the concentrations we want not to exuberantly high concentrations that might be found in nature. Solidification-- during this solidification process you're taking your molten silicon and you're solidifying it directionally from the bottom up and, because the solubility of impurities tends to be larger in the liquid than it is in the solid, it's like dragging a comb through the entire material dragging out the impurities. Concentrating them in the liquid and leaving a more pure silicon behind. Obviously, at the very, very end you have this highly concentrated region of impurities which then you have to slice off and remove, so the solicitation process doesn't come without a yield penalty. You still throw away some of your material. So you can't repeat the solidification over and over and over again, I guess you could, but you'd be losing material every step. So some combination of these processes here, and others. Other trickery. Low temperature eutectic formation with other elements, for example. Some combination of this is used to refine the silicon without creating a gas out of it.
So wafer fabrication. We're now going from feedstock, we're leaving feedstocking behind, and we're going to be talking about how do you go from the feedstock materials that are being passed around the room right now into a wafer that you can then manufacture a solar cell device out of? One of these for instance. So let's talk about wafer fabrication right here. So again, just to situate ourselves, we've gone from raw materials to silicon feedstock and now we're going to feedstocks to wafers. Any questions right now before we dive into that? Yeah.
AUDIENCE: Question about supply. So silicon is very abundant but the high purity silica deposits-- are they really abundant too?
PROFESSOR: Great question. So the question was are the high purity silica deposits as abundant as, say, silicon. Certainly. If you bend over and rub your fingers against the ground you're probably going to come up with, probably, millions of trillions of silicon atoms in your fingernails. Those are not very purity. So the highest security quartz deposits are more rare and they are sought after, and so they're are known. Their locations are known. There's one specific one in Norway, one specific one in North Carolina, and so forth around the world and there-- in a sense, they go to places. People have adjusted their metallurgical-grade silicon refineries and their subsequent down process for that particular ore. Once you run out of it, it's not that the world ends, we just have to adjust for the next feedstock source.
So, in principle, there are people looking at a variety of silicon inputs. Anything from the dirtier, compressed, metamorphic quartz that I mentioned. Some people looking at rice husks, which are silica rich as well. Other people looking at seashells which, mostly calcium carbonate, but other things as well. I mean, there was a wide range. When the price of silicon was $500 per kilogram, you got a multitude of ideas. When the price comes back down, people tend to be more conservative.
AUDIENCE: Is silicon considered a renewable resource?
PROFESSOR: Is silicon considered a renewable resource. It is not a renewable resource in the sense that, once you mine it from the ground, you've mined it from the ground and you used in some way. The reason it's considered not an issue is because there's so much of it. Not all of it, though, is in the easy to access form. Right? Some of the silicon might be bound up within heavily contaminated sources and that's where the refining ingenuity comes into play. As long as prices remain low, there's not too much interest, say, for example, that mine in Peru that has titanium oxide needles throughout their silicon because why would you want heavily titanium contaminated silicon? But as the price of silicon, it probably will, rise again then people might take another look at that mine and say gee, how can we phase separate the rutile and anatase from the quartz early on in the process by crushing and etching or something so we can access this feedstock material. We'll see.
It really depends on how the market evolves, where people go looking for their silicon, but there's a lot of it in the earth's crust.
AUDIENCE: You're not concerned about silicon?
PROFESSOR: No. Nope. What is a bigger bottleneck are are the refining steps in between. First it was the reactors and soon it's probably going to be the metallurgical-grade silicon reactors as well. All right. Wafers. How do we get to these from the raw feedstock materials that are being passed around the room right now? So single crystalline silicon ingot growth. Let's walk through that first. How do we get these beautiful ingots? They're about half of all silicon market right now.
The biggest growth method, by far, is called Czochralski growth and, named after the Polish physicist there Jan Czochralski. What you do is you have a bath of molten silicon. A crucible, if you will. This tends to be a circular crucible, rounded at the bottom, usually made of quartz with heaters on the outside to heat up the molten silicon. To heat up the silicon chunks in here. Once everything is molten, looking like a big bathtub of silicon, you introduce a small crystalline silicon seed into that molten silicon and then you begin pulling while rotating that seed.
So the seed is a single crystal material and what ends up happening is, as you introduce the seed into the material and begin pulling, you start pulling out this crystal. Single crystalline crystal. It's a thing of beauty and this seed is actually very, very narrow in diameter. It might be about that big around so pretty narrow in diameter and it's being able to support this ingot of a few, usually a few, tens to hundreds of kilograms of mass underneath it and that's because silicon is very strong even though it's brittle. So if you weren't to apply, say, for example, a shear force on your silicon but just to apply an axial load, you could support a very, large weight underneath it.
So the [INAUDIBLE] of silicon is grown from the bottom and eventually you wind up with this nice ingot, as shown right there. The art that goes into growing this properly is amazing. I'll highlight it with one small little example just to illustrate the bigger picture that a lot of effort goes into making these defect-free, quote unquote, defect-free crystals.
They're called defect-free because they contain no grain boundaries and no dislocations. They have impurities, they have intrinsic point defects, meaning vacancies or interstitial atoms, but they don't have grain boundaries or dislocations and so they're called defect-free silicon. You introduce that seed down into the liquid melt. Thermal stress happens. Right? Because you have the shock between the solid silicon seed encountering the liquid for the first time.
So this locations [? form ?]. And you have to pull the seed out in such a way, you slowly rotate and make this shoulder. The shoulder has to be as quick as possible because you don't want to waste material. Everything inside this shoulder right here gets thrown away. So that little piece of material right there gets tossed out. So you want to make the shoulders as narrow and as quick as possible so you can utilize the majority of your ingot but, at the same time, you have to make it thick enough so that the dislocations can move all the way and propagate all the way to the outside and end and terminate in the shoulder before propagating into the crystal.
So that's just one example of the technology that goes in the growing these. Another might be, gee, we're PV industry, we want to make the stuff fast whereas, in the IC industry you can invest up to a few of dollars per gram of silicon and still make a profit because you're selling a computer at 1,000 bucks. In the PV industry, we can invest, at most, a few tens of cents per gram of silicon. So we have to make this stuff fast. We can't dilly dally. You might want to crank up the growth speed, then you run into issues with defect concentrations, intrinsic point defect concentrations, during the growth. I'm illustrating this just to highlight the complexity of the growth process of making these ingots, and the latter example was one that the PV industry is facing today. It's actually a hot research topic.
Yeah. And then Ashley.
AUDIENCE: The rotation speed does that just affect time, or does it affect other things?
PROFESSOR: So it affects a multitude of things. One of the things that it affects is the flow of, the convective flow, of the melt. So the liquid flow inside of the melt is, in part, determining how much oxygen gets transported from this crucible here into the growing crystal. If you manage to suppress that convective flow in the melt, you will also suppress oxygen transport since the fusion is going to be a lot slower than turbulent transport or [INAUDIBLE] transport or convective transport. Yeah. Question?
AUDIENCE: I just have two questions so one is how fast do you rotate it and the other is what that does control-- the diameter because I've heard of 12 inch wafers versus like 18 inch wafers.
PROFESSOR: Sure. So one of the things that controls diameter is the balance of heat extraction. So if you cool something down, especially molten silicon, it will freeze, it will grow. If you heat it up, it will shrink. So that's one of the components that controls the diameter.
The pull speed and how you grow that shoulder, essentially how you heat up the material and how fast you pull at those initial stages, also dictates the diameter and you can see in the ingots themselves, they're not perfect. They have a little bit of corregation and that's the fluctuations of the temperature of the melt, fluctuations of the heater output, fluctuations of pull speed, maybe what's pulling this entire contraption is kind of a stepper motor that has a certain granularity to it. Results in corregated edges. It's not perfect and so there will be some adjustment made to the form factor of the edge to get this nice round wafer at the end of the day.
AUDIENCE: Does the seed rod [INAUDIBLE] all the way to the ingot or just near the top?
PROFESSOR: All right. So the entire ingot becomes pattern or templated by the seed rod. So this entire ingot has the same crystalline orientation as a seed.
AUDIENCE: And is the seed doped differently than the silicon?
PROFESSOR: It might be but I'm not aware that that affects the overall process. It could be that it's one of the critical pieces of the magic sauce that makes it work but I'm not aware. Rotation speed. It's not rotating like this it's a slow rotation so I would-- let's see. How many radians per second--
AUDIENCE: Can you see it?
PROFESSOR: You can visually see it if you looked at it long enough. Yeah. Yeah. So one modification, one variant, of the single crystalline growth method is called float-zone growth. You take a rod of poly, much like that right over there that's inside of here, and you pass an RF coil, radio frequency coil, next to the rod and what that does is, essentially, heats up the silicon, if it's doped highly enough. It will melt the silicon locally. Folks have probably heard of fancy high-end stoves that we can only probably hope to afford in 10 or 15 years, but these stoves that are inductive heaters. Right? They're not resistive heating elements, they're inductive heating elements and the way that works is you have a radio frequency source that then is absorbed by, in the case of the RF heater, I believe it's a specific type of iron that the inductive heating ovens need.
And so this RF coil here is emitting energy, which is absorbed by the silicon and melting it, and you start with the polycrystalline rod coming from the Siemens process and in that case, this rough, corrugated material right here won't do. Right? This is too rough for that RF coil to pass over and be a consistent distance away.
In the case of float-zone growth, you actually have to modify your polysilicon production process. You have to modify the Siemens process so that you get a nice smooth rod, which you can then pass the RF coil next to and melt and you again start with a seed at the bottom, your RF coil starts down here and then the RF coil moves through the material, almost like a comb from the bottom to the top, converting the polysilicon into nice single crystalline material and, in the process, it concentrates impurities in this liquid region. Since the liquids have a higher solubility in the liquid than they do in the solid, the impurities are then aggregated inside of the liquid region and, again, like a comb, they just get swept out of the material. Not all of them, but a large percentage of them, and so you can make multiple passes with this RF coil to further concentrate the impurities and the extremities and remove them from the material.
So that's a float-zone method. Very expensive material, very high purity. One of the reasons it has high purity is because you don't have this quartz crucible nearby, you don't have this molten silicon that's absorbing or dissolving the quartz and transporting the oxygen into your crystal. You have much lower carbon and oxygen concentrations to [INAUDIBLE] float-zone material. So if anybody is doing experiments with silicon, for whatever reason, using it as a substrate material, you want to think carefully about what type of silicon you source and from where you source it. You can find some very poor quality silicon out there in the market, especially if you going into the aftersale market, and we know this from some--
AUDIENCE: [INAUDIBLE].
PROFESSOR: --very painful experiences. And so there are some better sources from which to get your wafers and we're happy to talk about that offline. So, again, single crystalline silicon. We're going to venture into the world of multicrystalline silicon ever so briefly here. First, we'll start about cast material and, just to emphasize here, we have regions of crystalline material that have grain boundaries separating the adjacent grains and the reason we go into multicrystalline silicon is really oftentimes, it is a lower cost method of producing a silicon wafer although you have the grain boundaries. So, again, single crystalline, Czochralski and float-zone, you wind up with round wafers, typically single crystalline variety, and multicrystalline silicon wafers tend to be more square-like and more visibly multi-grained, if you will.
So let's talk about those for a minute. How do you make a multicrystalline silicon wafer? Again, you would start with the solar-grade silicon that could either be coming from the Siemens process, it could be coming from the fluidized bed reactor, it could be coming from an upgraded metallurgical-grade silicon, the liquid purification route but, somehow, some way, you get chunks of silicon, or granules of silicon, that have a high enough purity for you to make solar cells out of, and high enough purity is typically in the order of one part per million impurity content. So you put your solar-grade silicon into a crucible and then you melt the silicon inside of it. Silicon melts at 1,414 degrees Celsius. It's a very high temperature. So 1,414 degrees Celsius is the melting temperature of silicon.
And then it's cooled. Not just randomly, but from the bottom up and the reason it's cooled from the bottom up is because, and here I guess you'll actually have to come up and see this after class, it's rather difficult to see from here, but this is a cross section of a small ingot. This is the outside of the ingot where it was contacting the wall, these little pieces of white stuff that are flaking off, this is the fused quartz silica that forms the crucible wall, and the silicon nitride coating that form the anti-stick coating that prevented the silicon from sticking to the crucible, and so it's kind of rough and corrugated but, if we were to rotate this around and look at the inside, this here is a cross section of the actual ingot from the inside and, if you look carefully, you'll see grains growing from the bottom to the top. You probably can't see them from here, you'll have to come up after class and take a look, but the grains are growing from the bottom to the top and that is called directional solidification, or the result of directional solidification.
Directional solidification is when you solidify from the bottom to the top and, typically, your grain boundaries are going to be running perpendicular to the solid-liquid interface, so your grain boundaries will be running up like this as you grow your material from the bottom to the top. If you were to do uncontrolled solidification and all walls would freeze the same time, you'd have grains growing in from the sides, you'd have grains growing in through the bottom and then, when you slice your wafer out horizontally, the grain boundaries wouldn't be running perpendicular to the surface. They might be running parallel to the surface, in which case they could wreck havoc on your minority care diffusion length. Imagine you being an electron having to travel across that grain boundary that's between you and the P-N junction. Whereas, if the grain boundaries are running perpendicular to the surfaces, now they're only affecting very small areas of the entire solar cell wafer.
So when I pick up a wafer like this, this wafer was chopped from the ingot this way or, to put it into perspective here, this wafer was sliced out like that from this. So the grain boundaries were running perpendicular to the surfaces and that way they don't impede as much with electron transport. So the multicrystalline silicon ingot is formed. The ingot is then chopped into these blocks, usually between 16 and 24, that means four bricks to an edge or five bricks to an edge. Some folks are exploring six by six, so 36 bricks, and then the bricks are rotated on their side and then sliced into wafers and individual wafers come out. So you can see the wafers I've sliced from the bricks as I showed you right here.
Is this diagram clear to folks? In general since-- any confusions? Any questions? No.
AUDIENCE: How do they cut the wafers?
PROFESSOR: How do they cut wafers! So this is a process called wire sawing sign and this is one of the most beautiful technologies because it was invented in the PV industry and transported back, adopted by the IC industry. So it's one of the few examples of technology that went the other way. Let me get to that point.
AUDIENCE: How was it done before?
PROFESSOR: It was done by ID saws, for instance, inner diameter saws, that would slice off wafers like a wafer off of a salami.
AUDIENCE: So not a wire but like a disk?
PROFESSOR: Like a disk saw. Yeah. Exactly. Like the inner diameter meaning your saw is like a rotating blade and you're just using, you know-- Yeah. OK. So directional solidification of multicrystalline silicon. This is a cross section of a furnace that is solidifying an ingot right here. Here's your ingot. This is a liquid silicon and, essentially, it's solidifying from the bottom to the top and, hopefully, we'll have a tour of one of the world's largest ingot solidification furnace manufacturing companies in the world. So, they don't manufacture the silicon, they manufacture the furnace that manufactures the silicon. If that makes sense.
AUDIENCE: Do they also make the crucible?
PROFESSOR: No. That would be Vesuvius. Yeah. It would be other companies that make the crucibles. And these are some of the furnaces right here. The keyboard and monitor. For size comparison, stairs. So they're about two stories tall. You can go up here to the top and look down into them. It's pretty cool. Using a little infrared lens to block out the heat so you don't get blinded and the furnace itself-- all the action happens inside of here. The top can lift-- typically, they're the bottom loaded. You'll see this little seal right here. So this bottom part typically comes down because you want to trap the heat inside of it so you're not losing all that and the bottom is removed, the forklift comes in, picks up this ingot and crucible which could be a few of kilograms in mass-- up to about 600, maybe even a ton-- and removes it and places in the proper location.
It's a pretty dirty environment. The operator will typically take a garden hose and hose it down inside afterward. It's really an antithesis of an IC fab at this stage right here. These are graphite insulation materials on the sides of the crucible and this yellowish dust that you see everywhere is silica, again. That nice fine grained dust that's bad for you lungs.
The directional solidification process can be, to some degrees, used interchangeably with the so-called Bridgeman process. It's also a name for a specific type of directional solidification. This is your ingot, this is the ingot chopped into bricks, and then the bricks-- here's an ingot coming out of a furnace. Those are the bricks over here. This is a really tiny one. It's like lab scale. The big ones are about over a meter along the long edge.
And then, to saw them into wafers, we use what's called wire sawing. These are several kilometers of wires-- of wire. One continuous wire, several kilometers long, typically of a steel-based composite. Running in these bricks right here, in the presence of a glycol-based slurry, typically, and silicon carbide or diamond grit, and the grit is being pressured by the wire against the silicon.
The grit is very small in size-- micron size-- and it's, essentially, chipping out small pieces of silicon as this wire is progressing through and, over a period of around 6 to 8 hours, you saw through the entire brick and you use, maybe, four or eight of them at a time. So if that wire were to snap about halfway through the process, all those bricks are gone. So it's very important that the wire be very robust and able to support the sawing process and, as I said, it's several kilometers long and moving at a speed of a few meters per second. So this is zinging along through your material in the presence of very small grit and slurry, and so the consumables that are used in the wire sawing process are enormous, and you lose about half of your silicon due to sawdust in this process right here.
So this is a prime candidate for replacement of the manufacturing process, even though it's so commonly used today. What I'm going to do is give a quick pause right here until our next class, where we'll pick up and talk about ribbon growth, which seeks to get around all the complexities of multicrystalline silicon ingot growth while still keeping the cost advantage. So with that, thank you.
This file contains slides used in both Lectures 10 and 11.
Free Downloads
Video
- iTunes U (MP4 - 247MB)
- Internet Archive (MP4 - 247MB)
Subtitle
- English - US (SRT)