This page is a guide to preparing and soldering wires to electronic devices. The first step in preparing the wire is cutting the plastic coating off of it, or "stripping" it. You do this with the use of a wire stripper; our class went for the fancy model of wire strippers:
Wire stripper.
You strip a wire by placing it into the slot in the wire stripper that is the appropriate size for the specific wire (too big and you won't cut off any of the plastic, but too small and you will cut the wire in half instead of cutting off just the plastic; finding the right size is largely a matter of experimentation). For our fancy gizmo, run the wire through the gripping section and squeeze the handles together so that it pulls the plastic off; for a more generic wire stripper, just grab the wire and pull it through the device.
Wire in wire stripper.
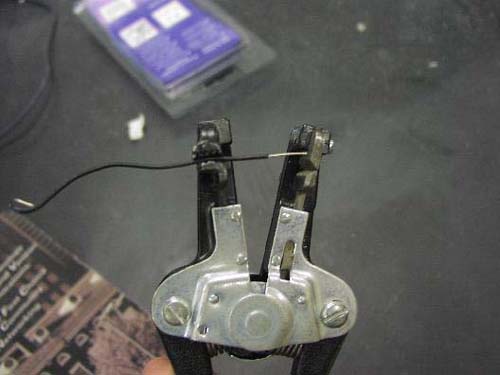
Wire stripper in action.
Now that you have an uninsulated end of wire, you get to start soldering. To solder, you need, of course, solder, as well as a soldering iron. I personally find it very hard to solder without small-diameter solder and a clean soldering iron, so I'll explain how to solder with those things.
First, plug in the soldering iron. While you're waiting for it to warm up, make sure that its sponge is at least slightly damp, so that you can clean the tip of the iron. If you don't have a sponge for the iron, just cut an ordinary kitchen sponge in half and use that; it works fine. After the iron has warmed up for a minute or so, put a little solder on the tip if it is starting to turn odd colors, and you're ready to start soldering.
A tip before soldering: Make sure that at least one, if not both, of the things you are trying to solder together are anchored down; you don't have enough hands to hold two things together and manage a soldering iron at the same time, and wires that are in contact with a soldering iron for an extended period of time can get painfully hot... To solder two things together, arrange them so that they are wrapped around each other, and hold the soldering iron against the back of the joint while you push solder in from the front. This insures that the metal pieces that you are soldering together heat up enough to chemically mix with the solder, so that you get a very strong solder joint that won't break apart over time.
Soldering gun soldering together two wires.
Put on just enough solder so that all attaching surfaces are fully coated; you don't get extra points for making solder blobs, and they are more prone to breaking and short-circuiting. After each soldering job, wipe off any excess solder on the tip of the iron onto the wet sponge; this prevents blobs of solder from forming and helps clean the iron, keeping it as efficient as possible at transferring heat from the tip of the iron to the solder.
Wiping off the soldering gun to clean it.
When you're done, if no one else is going to use the soldering iron, unplug it and let it cool down. These things can take a long time to cool down; wait a good few minutes after it is no longer hot enough to boil steam off of the sponge before you put it away. As a general warning, always beware of the soldering iron sitting out on the table; cold irons look exactly the same as hot irons. I actually discovered this in class, in a vain attempt to scrape some of the encrustations off one of the tips of the irons in class; the iron was actually still on (I wasn't quite awake that morning). Fortunately, there was so much junk built up on the iron that it took me a good half a second to realize that it was hot, and it did little real damage; it still hurt, though. That reminds me: In terms of long-term soldering iron maintenance, there is really only one thing on an iron that can break, and that is the tip. If it gets so coated in junk that it doesn't work, or if it gets chipped or something, just get a new one; it's not worth the effort (and, apparently, risk) of working with a bad tip.